
What is the formula for job order costing?
Job costing, also known as project-based accounting, is calculated by adding together costs for all the individual items categorized under three major areas of a project: labor, materials and overhead. The overall formula for calculating the cost of a job is: Total job cost = Materials + labor + overhead.
Which would cost systems companies use, job order or process?
Key Takeaway. A process costing system is used by companies that produce similar or identical units of product in batches employing a consistent process. A job costing system is used by companies that produce unique products or jobs. Process costing systems track costs by processing department, whereas job costing systems track costs by job.
What are steps in job-order costing process?
7 Steps in Job Costing Identify Job. The first step in the job-costing process is to identify the scope of the project or job. ... Identify Costs. Step two is to identify the direct costs associated with the job. ... Select Allocation Base. ... Indirect Costs. ... Compute Rate. ... Compute Indirect Costs. ... Compute Total Costs. ...
What are the main features of job order costing?
There are many similarities between job costing and contract costing, which are:
- (1) Both job costing and contract costing are specific order costing.
- (2) In the case of both job costing and contract costing, each job or contract constitutes a cost unit.
- (3) Both methods have the same object to find out cost and profit.
- (4) Under both the methods a separate account is opened. ...

Can a business use both a job order cost system and a process cost system?
Work in process inventory is the cost per unit and the equivalent units remaining to be completed. Process costing and job order costing are both acceptable methods for tracking costs and production levels. Some companies use a single method, while some companies use both, which creates a hybrid costing system.
Can a company use both types of cost accounting systems?
Can a company use both types of cost accounting systems? A company can use both types of systems. For example, General Motors uses process costing for standard model cars and job order costing for custom-made vehicles.
What companies use job order costing and process costing?
Below are examples of different types of companies using job order costing systems to track inventory and how the process differs.Retail companies.Law firms and accounting businesses.Medical services.Film studios.Construction companies.
Is process costing the same as job order costing?
Job order costing tracks prime costs to assign direct material and direct labor to individual products (jobs). Process costing also tracks prime costs to assign direct material and direct labor to each production department (batch).
Which type of costing system combines characteristics from both job order and process systems?
A hybrid costing system is a cost accounting system that includes features of both a job costing and process costing system.
Why would a company use multiple cost accounting systems?
Why would a company use multiple cost accounting systems? 1- Provide employees with information useful in managing activities that consume resources. 2-Furnish managers with information to evaluate and reward performance.
Which type of business would most likely to use a job order costing system?
Companies in the white collar sector of business, including law firms, accounting businesses and private investment companies, can utilize job order costing to manage individual client accounts. For example, accounting firms can consider each individual client a job.
Which of the following product situations is better suited to job order costing than to process costing?
Explanation for correct answer: Job order costing is better for the situation when the Costs are easily traced to a specific product.
Does Coca Cola use process costing?
No matter who the customer is, they all end up receiving the same product. For example, Coca-Cola may use process costing to track its costs to produce its beverages.
Would a pharmaceutical manufacturer use process or job order costing?
Mass production of identical units such as beverages, pharmaceuticals, cereal, utilize process costing to determine the cost of each unit.
What is one main difference between a process cost system and a job order cost system?
One main difference between job order costing and process costing is the product type and the uniqueness of the product evaluated.
What type of companies use process costing?
Process costing is generally used by manufacturers that produce a large volume of identical items, such as companies involved in oil refining, food production, chemical processing, textiles, glass, cement and paint.
What is job order costing?
As you’ve learned, job order costing is the optimal accounting method when costs and production specifications are not identical for each product or customer but the direct material and direct labor costs can easily be traced to the final product . Job order costing is often a more complex system and is appropriate when the level of detail is necessary, as discussed in Job Order Costing. Examples of products manufactured using the job order costing method include tax returns or audits conducted by a public accounting firm, custom furniture, or, in a comprehensive example, semitrucks. At the Peterbilt factory in Denton, Texas, the company can build over 100,000 unique versions of their semitrucks without making the same truck twice.
When to use a job order cost system?
Thus, a job order cost system is used for custom jobs when it is easy to determine the cost of materials and labor used for each job. A process cost system is often less expensive to maintain and works best when items are identical and it is difficult to trace the exact cost of materials and labor to the final product.
Why does the process of production not change?
The process of production does not change because of the costing method. The costing method is chosen based on the production process. In job order cost production, the costs can be directly traced to the job, and the job cost sheet contains the total expenses for that job. Process costing is optimal when the costs cannot be traced directly to ...
Why does Nabisco use process costing?
In order to understand how much each product costs—for example, Oreo cookies— Nabisco uses process costing to track the direct materials, direct labor, and manufacturing overhead used in the manufacturing of its products.
What is the expense recognition principle?
The expense recognition principle is the primary reason to separate the costs of production from the other expenses of the company.
What is conversion cost?
Conversion costs are the costs necessary to convert direct materials into a finished product: direct labor and manufacturing overhead, which includes other costs that are not classified as direct materials or direct labor, such as plant insurance, utilities, or property taxes.
When is process costing used?
Process costing is used most often when manufacturing a product in batches. Each department or production process or batch process tracks its direct material and direct labor costs as well as the number of units in production.
What is job costing?
Job costing is the cost of each job carried during an assignment or project. Whereas, process costing is the total cost of the processes carried out in the entire project.
When is job costing used?
Job costing is used in cases where products produced are unique, and process costing is used for the standardized products produced. In a job, casting losses can be segregated, but in the case of later losses are bifurcated on the bases of processes. Transfer cost is not considered in job costing when the job is shifted from one assignment ...
When is WIP present in costing?
In job costing, WIP may or may not be present, but for process costing, WIP may be present at the beginning and end of the period. Special treatment is required for each job in job costing, whereas in process costing, there is no need for special treatment for each process. Job costing each job is different from another, so it has individuality.
Does job costing have individuality?
But, later, products are produced in large volume, and consequently, therefore, it does not have individuality. In job costing, the time and materials are considered while calculating the cost of the job, so recordkeeping of all these things is an important and tedious task.
Is transfer cost considered in job costing?
Transfer cost is not considered in job costing when the job is shifted from one assignment to another. In the case of process costing, the cost of the previous processing stage is transferred to the next processing stage. There is less scope of reduction of cost in job costing, whereas for the process costing, there is a higher scope ...
Is each job considered an isolated project?
Each job is considered as an isolated project and a distinct entity for. Based on the client’s requirement. No job is the same and is heterogeneous, and each job will have to be done in a manner required to satisfy each job. The difference in work in progress exists in each period.
Can cost be transferred?
The cost cannot be transferred. The cost can be transferred from one process to another. Individuality. Since each job is different from another, all the products have their individuality. Products are produced in large volume, and consequently, therefore, they do not have any individuality.
What is job order costing?
Job order costing is an accounting system that traces the individual costs directly to a final job or service, instead of to the production department. It is used when goods are made to order or when individual costs are easy to trace to individual jobs, assuming that the additional information provides value.
What is process costing?
A process costing system is often used to trace and determine production costs when similar products or services are provided. The concept and mechanics of a process costing system are addressed in Process Costing.
What are the two types of costing systems?
As previously mentioned, the two traditional types of costing systems are job order costing and process costing .
What is the organization of flow of goods through production?
Organization of Flow of Goods through Production. Regardless of the costing method used (job order costing, process costing, or another method), manufacturing companies are generally similar in their organizational structure and have a similar flow of goods through production.
What is prime cost?
Prime costs are costs that include the primary (or direct) product costs: direct materials and direct labor. Conversion costs are costs that include the expenses necessary to convert direct materials into a finished product: direct labor and manufacturing overhead. Their relationship is shown in (Figure).
What are direct material costs?
Direct material costs may include the cost of the protein, grain, and vegetable option, as well as the cost of the packing containers. The direct labor cost is for employees who are directly involved in preparing the meals.
Does one batch lead to a second batch?
However, in mass production, wherein one batch leads to a second batch, stopping the process to properly identify the materials, labor, and overhead costs used for each batch does not provide enough valuable data to justify determining the individual costing of each product.
What is job order costing?
Job order costing is an accounting system that traces the individual costs directly to a final job or service, instead of to the production department. It is used when goods are made to order or when individual costs are easy to trace to individual jobs, assuming that the additional information provides value.
What is process costing?
A process costing system is often used to trace and determine production costs when similar products or services are provided. The concept and mechanics of a process costing system are addressed in Process Costing.
Why does the process of production not change?
The process of production does not change because of the costing method: The costing method is chosen based on the process of production and is intended to provide the most accurate representation of the costs incurred in the production process. Maintaining accounting records for each system has its advantages.
Why are bar codes used in costing?
Both job order and process costing are used to track costs with a goal of improved cost measurement efficiency. Bar codes can help with either type of costing. Verified Label, Print & Promotions, Inc. provides a list of how barcodes contribute to efficiency in cost tracking for more information.
What are direct material costs?
Direct material costs may include the cost of the protein, grain, and vegetable option, as well as the cost of the packing containers. The direct labor cost is for employees who are directly involved in preparing the meals.
What is prime cost?
Prime costs are costs that include the primary (or direct) product costs: direct materials and direct labor. Conversion costs are costs that include the expenses necessary to convert direct materials into a finished product: direct labor and manufacturing overhead. Their relationship is shown in Figure 4.4.
What is the difference between job order costing and process costing?
Differences between job order costing and process costing: The main differences between job order costing and process costing are given below: job order costing as per the name, involves costing for individual job orders. This means that for every job completed by a factory direct costs (material, labor) can be directly attributable ...
What is job order costing?
The job order costing system is a costing method that is used to calculate the costs attached to an individual job or order. In a business applying job order costing, each job or order is assigned a job number to distinguish it from the others. Costs related to each job are allocated directly to each specific job.
Why is job order costing aggregated?
While in process costing all the costs are aggregated and compiled, because all the costs relate to a single process of production.
Why is process costing used?
The process costing is used for the costing of more standardized products that are usually produced in large volumes. The job order costing requires more record keeping activities than process costing. This is because in job order costing all the relevant costs are allocated separately to individual jobs and as for every job a separate job card is ...
What is the basic account used in both costing systems?
Both the costing systems use basic accounts like materials, work-in-progress (in the case of job costing; if any) etc. The method for treating over or under absorbed overheads in both costing systems is almost the same. As process costing does not have different batches, the costs are allocated systematically.
Does process costing have different batches?
As process costing does not have different batches, the costs are allocated systematically. The job order costing uses the same approach of assigning overheads to the individual jobs that process costing system uses to assign to a whole production process. The t-accounts also referred as manufacturing accounts that are maintained in both ...
Which hotel uses the job order costing method?
The Sea View Resort Hotel : the hotel is best recommended to use the job order costing because it offers services and the method is designed for such businesses. Willie Wonker’s Chocolate Factory: because the business produces a standard item which units are identical it is best to apply the process costing method.
What is cost accounting?
A cost accounting system is the sum methods and techniques used by businesses allowing them to track resources consumed in production and distribution of services or goods to consumers. These methods and techniques are used by the management in order to evaluate and reward staff performance, by employees in order to manage recourses efficiently ...
What is activity based costing?
The activity based costing procedures are: Only if a cost driver can’t be recognized a cost can be assigned on an allocative basis. Related cost pools are assigned to an overhead rate on costs drivers. Cost pools are used to assign costs; the basis depends on the business and industry.
Why is AVCO used in financial statements?
AVCO is used to establish the value of an inventory by calculating the costs of units.
What is ABC costing?
Activity based costing (ABC) is designed to assign costs to activities. This method has become popular because of the fact that the complexity of businesses keeps growing and so does their need to assign increasingly large indirect costs to the appropriate department or activity. ABC is the process where costing is assigned based on ...
What is manufacturing overhead?
Manufacturing overhead, is the category including all other manufacturing costs like utilities aside for the above mentioned ones. What are the procedures in job order costing, process costing and activity based costing. Job order costing process is a specific set of events which will usually occur with each job.
How are direct labour and materials charged?
Direct labour and materials are charged by the accountant to the work in process accounts using the actual quantity acquired. These quantities are all tracked using a job costing sheet which will likely be already a computerized ledger and use used for each job.
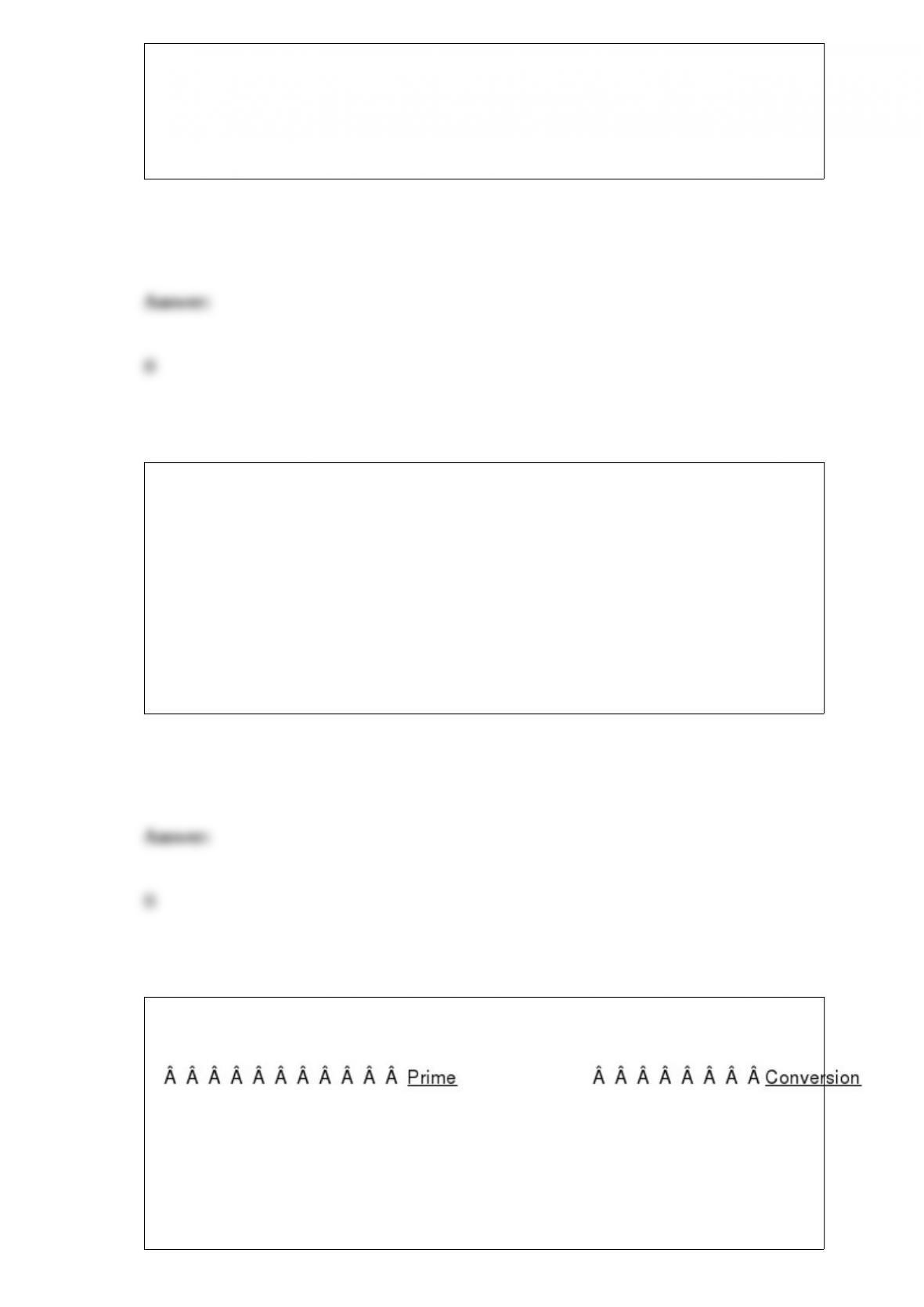