
Can carbon steel be welded?
Most of the other alloying elements in steel are not conducive to welding, but their content of influence is generally much smaller than that of carbon. Generally, low-carbon steel has good weldability and does not require special process measures.
What are the rules for welding high carbon steels?
Rule 1 – Avoid excessive penetration. When we weld high carbon steels we almost always will be using an undermatching filler metal, that is a filler metal with lower tensile strength than the base metal. We do this in order to have a ductile weld that will not be stressed to the point of fracture.
Which type of steel has the worst weldability?
At the same time, the welds are also more prone to hot cracks and high-carbon steels are more prone to hot cracks than medium-carbon steels. Therefore, this type of steel has the worst weldability, so it is not used in general welding structures and is only used for repair welding or surfacing of castings.
Can You weld with different kinds of steel?
When welding with different kinds of steel, it can be tricky to get the metals to work well together and also avoid rusting in your final product. Welding dissimilar metals can be tricky in many situations, however, some can be welded successfully. So, how do you weld stainless steel to carbon steel?

What happens to high carbon steel when welded?
Medium carbon steel such as C1045 typically requires preheat and post-heat treatment to avoid weld cracking. High carbon steel is even more prone to weld cracking than the other two groups of carbon steel.
Is high carbon steel harder to weld?
The high carbon steels are difficult to weld because of the hardening effect of heat at the welded joint. Because of the high carbon content and the heat treatment usually given to these steels, their basic properties are impaired by arc welding.
Can you weld on carbon steel?
Steel consists of iron and carbon with small amounts of miscellaneous metals, such as manganese, chromium, silicon, vanadium, and nickel. Low carbon steel contains only 0.3 percent carbon, making it incredibly easy to weld.
Can you weld on high strength steel?
Because of their unique properties, high strength steels can be more challenging to weld than mild steels. The material is stronger, but often used in thinner cross sections to decrease the overall weight of the structure.
What steel Cannot weld?
Some examples of material combinations that cannot be fusion welded successfully are aluminum and steel (carbon or stainless steel), aluminum and copper, and titanium and steel. Nothing can be done to alter their metallurgical properties. That leaves changing your process.
Which type of steel is not weldable?
Ferrite and martensitic stainless steel Other types of stainless steels, such as ferritic and martensitic stainless steels, are not as easily welded, and must often be preheated and welded with special electrodes.
Why welding is a poor joining method for high carbon steels?
The high-carbon steels contain carbon from 0.60% to 2.00%. This group of steel is very difficult to weld because they readily form the hard and brittle martensite phase as steel cools from welding.
What is the hardest metal to weld?
Some of the harder metals to weld include aluminum, nickel, and titanium.
Can you weld hardened steel?
By using suitablepost-welding heat ways and picking weld joints that equitably circulate weight on the metal, one can effectively weld hardened steel. One can preheat it or use a low hydrogen bar whenwelding. However, you have to preheat it and, at that pointre-temper in the wake of welding, If it's devicesteel.
Can high strength steel be welded to mild steel?
Yes, provided that the welding procedure, particularly any preheat, is designed for the high yield steel. This may mean using basic low hydrogen MMA (SMA) consumables. It is also a convention that the weld metal matches the strength of the weaker of the two components although this is not invariably the case.
Can you repair high strength steel?
Repair of this type of steel is not recommended. This type of steel should be replaced only, at factory joints. Sectioning or partial replacement is not recommended. The use of heat to repair damage is not recommended for this type of steel.
Can you mig weld ultra high strength steel?
When GMA (MIG) welding ultra-high-strength steel (UHSS), like boron-alloyed steel, there are a few additional things to consider. Most UHSS parts are typically replaced using squeeze-type resistance spot welds (STRSW) at a factory seam and GMA (MIG) plug welds used to attach the part where a spot welder cannot reach.
What is high carbon steel?
High carbon steel refers to the carbon content of more than 0.6% of the steel, it is mainly used to require high hardness and wear resistance of machine parts, such as rotating shaft, gear, bearing and coupling. It has a greater tendency to harden than medium carbon steel, and forms high carbon martensite, which is more sensitive to the formation of cold crack. At the same time, the martensite structure formed in the welding heat affected zone has a high hardenability, which leads to the decrease of the plasticity and toughness of the joint and poor weldability. Therefore, special welding technology must be adopted to ensure joint performance. When making the welding process of high carbon steel welding parts, all possible welding defects should be taken into full consideration and the corresponding welding process should be adopted.
What is the effect of preheating before welding and slow cooling after welding?
1) Preheating before welding and slow cooling after welding can not only reduce the hardness and brittleness of the heat-affected zone but also accelerate the hydrogen diffusion in the weld.
Why should stress relief annealing treatment be carried out immediately after welding?
5) Stress relief annealing treatment should be carried out immediately after welding to promote the outward diffusion of hydrogen in the weld.
Why is stainless steel electrode used in welding?
If the base metal is not allowed to preheat during welding, in order to prevent cold cracks in the heat-affected zone, Austenitic stainless steel electrode can be selected to obtain good plasticity and strong anti-crack Austenitic organization.
Why do we use grooves in welding?
Groove: In order to limit the carbon content in the weld metal , the fusion ratio should be reduced. U-shaped or V-shaped grooves are generally adopted, and the oil and rust in the range of 20mm on both sides of the groove and the groove are cleaned.
Does carbon steel crack?
High carbon steel has a great tendency to harden, and it is easy to appear hot crack and cold crack during welding. How do you prevent thermal cracking?
Does high carbon steel welding require joint strength?
Welding material: High carbon steel welding generally does not require joint and base metal strength. Electrode arc welding is generally used to have a strong ability to remove sulfur, low hydrogen content of the deposited metal diffusion, good toughness of low hydrogen electrode, rather than the strength level is higher than the base metal electrode. When the strength of weld metal and base metal is required, the corresponding low hydrogen electrode should be selected;
1. Weldability of high carbon steel
High carbon steel is mainly used for structures with high hardness and high wear resistance, so the main welding methods are electrode arc welding, brazing and submerged arc welding.
2. Welding defects of high carbon steel and preventive measures
Due to the great hardening tendency of high carbon steel, hot cracks and cold cracks are easy to appear during welding.
Want to buy a laser welding machine?
Contact us right now to receive expert suggest and professional quotation sheet within 24 hours.
What happens when you weld high carbon steel?
When welding high-carbon steel, due to the high carbon content of this steel, the welding will produce a large welding stress, the hardening and cold cracking tendency of the welded heat-affected zone is greater .
What is high carbon steel?
High Carbon Steel is often called tool steel and its carbon content is from 0.60% to 1.70%. It can be quenched and tempered and welding performance is very poor. Hammers and crowbars etc. are made of 0.75% carbon steel; cutting tools such as drills, screws and reamers etc. are made of 0.90% to 1.00% carbon steel.
Why is mild steel called mild steel?
Because of its low strength, low hardness and softness, it is also called mild steel. It includes most of the ordinary carbon structural steel and part of the high-quality carbon structural steel, which is mostly used for engineering structural parts without heat treatment and mechanical parts that require wear resistance by carburizing ...
What determines the weldability of steel?
The weldability of steel depends mainly on its chemical composition. The most influential factor is the carbon, which means that the carbon content of the metal determines its weldability. Most of the other alloying elements in steel are not conducive to welding, but their content of influence is generally much smaller than that of carbon. ...
What are the two main categories of steel?
According to the chemical composition of steel, it can be divided into two main categories: carbon steel and alloy steel. Carbon steels are subdivided into: (i) Low carbon steel with a carbon content of less than 0.25%; (ii) Medium carbon steel with a carbon content of 0.25 – 0.6%; (iii) High-carbon steel with carbon content larger than 0.6%.
When the carbon and sulfur content of low-carbon steel is above the upper limit, in addition to the use of answer?
When the carbon and sulfur content of low-carbon steel is above the upper limit, in addition to the use of high-quality low-hydrogen welding rods, preheating and post-heating and other measures, the groove form should be selected reasonably and the fusion ratio should be reduced to prevent thermal cracks.
Why should welded parts be tempered?
After welding, the welded parts should be tempered to eliminate stress, then to fix the organization to prevent cracks and improve the performance of the weld.
What Welding Rod Do I Use to Weld Stainless to Carbon Steel?
It is recommended to use a 309L when you are joining stainless steel with a more milk steel, which includes carbon steel. You can also use CG-12 which is the cast equivalent to using a 309. The benefit of using 309L is that it contains no molybdenum.
Why is stainless steel so hard to weld?
Welding stainless steel can be difficult because it retains heat very efficiently. Due to this heat efficiency, the steel can warp very easily in high temperatures and distort while it is left to cool. This makes it very difficult to work with as you may find your results vary after you are finished with the welding and you have left the steel to cool. This article on American Torch Tip gives a great overview. So does this video via weld.com.
What is Galvanic Corrosion?
Simply put, galvanic corrosion is when one metal causes another to corrode and break down. This can be a huge issue and can occur frequently with connecting stainless steel with carbon steel due to the ability for it to rust and get weaker over time.
How Can We Prevent Galvanic Corrosion Between Carbon Steel and Stainless Steel?
One of the main reasons many welders avoid mixing stainless steel and carbon steel is due to galvanic corrosion. Even though these two metals do not get along well, they are both strong and useful metals and therefore many welders like to use them together. Luckily, there are ways to combat galvanic corrosion so that the metals will work well together.
What is a tig welder?
The TIG welder uses a tungsten electrode as well as a gas nozzle to weld two pieces of metal together. The tools required are an electric torch and filler rod, a gas welding tank ( read about what gas is best for TIG welding here ), and your standard welding PPE.
Why do welders use MIG welding?
However, MIG welding is recommended due to the different melting temperatures of the different steels because it uses a filler material to connect the different steels. carbon steel pipes. Although many welders choose not to weld dissimilar metals together due to the challenge this can present, it can be done!
Why is welding strength compromised?
This compromised strength is generally due to the differences in melting points and welding temperatures in addition to the operational tolerance of each metal. Projects that mix metal types simply will not result in as strong of a weld as those that use a consistent metal throughout the project.
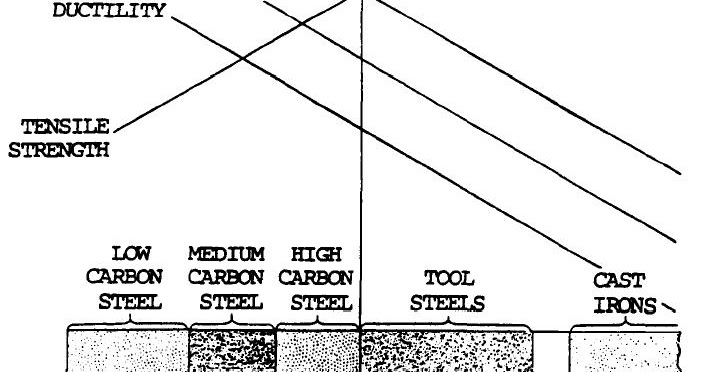