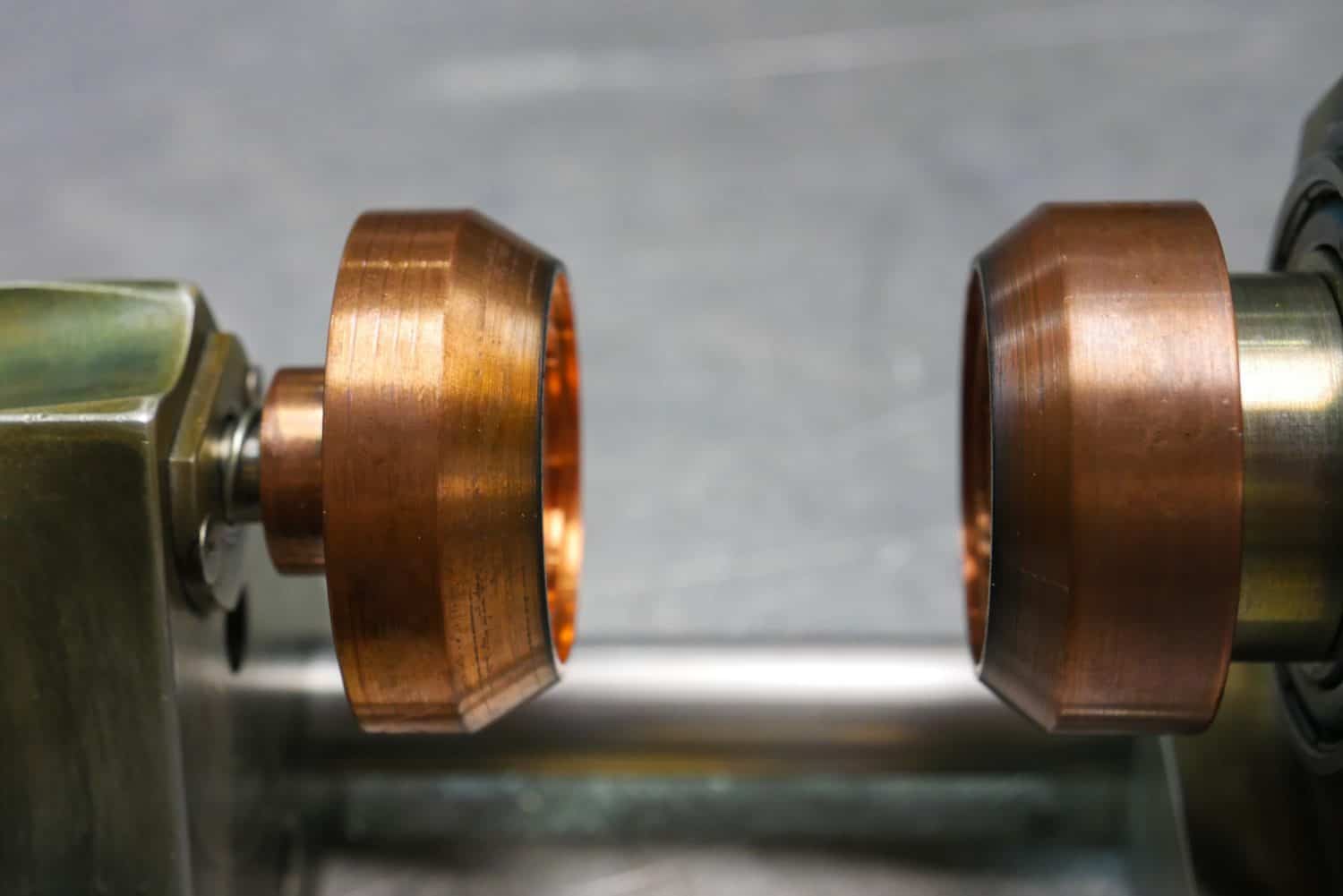
Is it possible to weld finished tool steel?
It is sometimes necessary to weld finished or partly finished tool steel parts. Welding tool steels differs from welding the low carbon machinery steels since tool steels, because of their alloy content and the welding temperatures will actually harden to maximum hardness in and near the area welded.
What type of welding do you use on tool steel?
Once the part is in its final, correct form, you can measure the trim steel and make a new die. In general, gas tungsten arc welding (GTAW) is the best process to use on tool steel based on its amperage and control over feeding and aim. Gas metal arc welding is a better choice for fast filling and joining large pieces.
Does welding Harden tool steels?
Note also that while the heat of welding will harden the higher alloy tool steels, it may actually soften the lower alloy grades to an unacceptable degree and the part may have to be re-heat treated after welding.
What is the consumable used for welding tool steel?
In general, the consumable used for welding tool steel should be simi- lar in composition to the base mate- rial. When welding in the annealed

Are tool steels weldable?
Tool and die steel may be welded in the annealed or hardened condition providing an understanding of the basic characteristics of the steels is known and proper pre- and post-heating and welding techniques are observed.
Can A2 tool steel be welded?
Make sure the A2 is annealed before attemping to weld it. High preheat is required. Weld it with a 100 to 110 ksi filler metal and make sure the weld is of sufficient size to care any loads, including any residual stresses. The part should be stress relieved as soon as the weld is completed.
What metal should not be welded?
Some examples of material combinations that cannot be fusion welded successfully are aluminum and steel (carbon or stainless steel), aluminum and copper, and titanium and steel. Nothing can be done to alter their metallurgical properties. That leaves changing your process.
Is m2 tool steel weldable?
Tool steel cannot be welded at room temperature without considerable risk for cracking and it is generally necessary to pre-heat the mould or die before any welding can be attempted (see later).
What is A2 steel equivalent to?
Equivalent materials to A2 tool steels are: AFNOR Z 100 CDV 5. DIN 1.2363.
How hard is A2 before hardening?
A2 tool steel is typically hardened to 60-62 HRC and then tempered to final hardness. I assume the 50 HRC hardness you mention is the result of this process. A (stress-relief) temper in the range of 1100-1200°F (595-650°C) will lower the hardness, but I suspect only into the range of 44-46 HRC.
What is the hardest metal to weld?
Some of the harder metals to weld include aluminum, nickel, and titanium.
Which steel is difficult to weld?
High Carbon SteelHigh Carbon Steel (Carbon Tool Steel) They are extremely hard and strong, but also have poor weldability and are difficult to weld without cracking. Once heat treated, these are extremely hard and brittle.
Does welding steel make it weaker?
Yes, welding makes steel weak, especially in the HAZ (heat-affected zone) if you weld at high temperatures. Weakening when it comes to welding is usual with chilly-rolled steel. When connecting distinct metals, you can use three main methods: Welding.
How hard is tool steel?
Hardness in tool steel is measured by the Rockwell C test, whereby a standardised load is used to make an indentation. A small indentation indicates high hardness. Hardened cold work tool steels are generally about 58/64 HRC (hardness Rockwell C). Most are circa 60/62 HRC, although some can go up to 66 HRC.
What is Tool Steel made out of?
Tool steels comprise carbide-forming elements such as chromium, vanadium, molybdenum and tungsten in different combinations. They also contain cobalt or nickel which improves their high-temperature performance.
How do you heat treat m2 tool steel?
High Heat: 2100-2225F(1150-1220C), soak 2 to 5 minutes. For vacuum hardening, use the high side of the high heat range and soak times. Quench: Salt or oil to 1000-1100F(540-595C), equalize, then air cool to hand warm, 150F(65C)....Typical ChemistryCarbon0.85%Manganese0.30%Silicon0.30%Chromium4.15%4 more rows
Can you weld all metals?
Every metal is unique. To a certain extent, all metals can be welded, but there are clear advantages and disadvantages to each. Stick welding, also known as shielded metal arc welding (SMAW), is one of the most common welding methods out there.
Can you weld steel to aluminum?
Steel cannot be welded to aluminum by using conventional welding techniques, like SMAW (arc welding), GMAW (MIG) or GTAW (TIG). However, there are some workarounds and alternatives that might provide acceptable results.
Can stainless steel be welded?
Stainless steel can be stick welded, shielded metal arc welded (MIG), or gas tungsten arc welded (TIG). The best choice depends on what you're trying to accomplish since each process yields a different outcome. You can weld stainless steel with a stick, but you probably shouldn't.
Can aluminum be welded?
It's possible to weld aluminum using stick welding methods, but it can be messy. Some of the best methods to use during the process include alternating or direct current TIG welding or MIG welding.
How does welding tool steel differ from welding the low carbon machinery steel?
Welding tool steels differs from welding the low carbon machinery steels since tool steels, because of their alloy content and the welding temperatures will actually harden to maximum hardness in and near the area welded.
How long to cool annealed tools?
Postheat hardened tools for 1 hour per inch, 2 hours minimum, at 50F below the original tempering temperature. Annealed tools should be re-annealed.
What temperature should a torch be preheated to?
PROCEDURE. Preheat the part to as high a temperature as is consistent with the final hardness requirements, preferably in the range of 400-1000F (250-538C). The preheat temperature for hardened tools should not exceed the original draw temperature. Furnace preheating is desirable but torch preheat is widely practiced.
Should annealed tools be reannealed?
Annealed tools should be re-annealed. This serves both as a stress relieving operation as well as to minimize the hardness gradient across the weld area. Local conditions may vary the welding methods, but the principle of preheating and slow cooling should be respected to minimize risks.
How to prepare a weld for welding?
All defects of joints to be welded must be prepared by completely removing the defect. This is done by grinding or machining and subsequently removing sufficient materials to allow fusion of the weld deposit in the bottom or root of the preparation. The overall width after material removal will depend on the welding process employed. Gas tungsten arc and manual arc welding generally require wider preparations. In addition, the finished weld metal should be deposited to a minimum depth of three to five millimetres, which must also be accounted for in weld preparation. After machining or grinding the surface must be cleaned of oil or other foreign material.
Why is it important to keep the preheat temperature constant during welding?
The material to be welded must be preheated slowly and uniformly to avoid uneven expansion through localised or partial heating which can Lead to cracking. It is important to maintain the preheat temperature as constant as possible during welding.
What is the hardness of an austenitic welding electrode?
Reputable steel supply houses can recommend specific electrodes of welding wire for each tool steel. Austenitic welding electrodes are frequently used on large repairs as an underlay. This is then overlayed with a hard deposit corresponding to the hardness of the base metal for the working face. The austenitic deposit serves as a cushion because of its excellent shock resistance. The hardness of the austenitic deposit is around 200 BHN and may work harden under impact to 400 BHN equivalent.
When should annealed steel be placed in a furnace?
Annealed tool steel should be placed in a furnace immediately after welding and re-annealed.
What is the problem with welding tool steel?
The main problem in welding tool steel stems from its high hardenability. Welds cool quickly once the heat source is removed and the weld metal and part of the heat-affected zone will harden. This transformation generates stresses because the weld is normally highly constrained, with a concomitant risk for cracking unless great care is exercised. In what follows, a description is given of the welding equipment,
Where to get information concerning heat treatment of the tool subsequent to welding?
Information concerning heat treat- ment of the tool subsequent to welding can be obtained from the brochures for the welding consum- able and/or the tool steel in question.
Why do welders weld at high temperatures?
The basic reason for welding tool steel at elevated temperature derives from the high hardenability and therefore crack sensitivity of tool steel welds and heat-affected zones. Welding of a cold tool will cause rapid cooling of the weld metal and heat-affected zone between passes with resulting transformation to brittle martensite and risk of crack- ing. Cracks formed in the weld could well propagate through the entire tool. Hence, the mould or die should, during welding, be maintained at 50–100°C (90–180°F) above the Ms- temperature (martensite-start tem- perature) for the steel in question. The critical temperature is the Ms of the weld metal, which may not be the same as that of the base metal. In some instances, it may be that the base steel is fully hardened and has been tempered at a temperature below the M s-temperature. Hence, pre-heating the tool for welding will cause a drop in hardness. For exam- ple, most low-temperature tempered cold-work steel will have to be pre- heated to a temperature in excess of the tempering temperature, which is usually ca. 200°C (400°F). The hard- ness drop must be accepted in order to perform a proper preheating and mitigate the risk of cracking during welding. During multi-run welding of a properly pre-heated tool, most of the weld will remain austenitic under the entire welding operation and will transform slowly as the tool cools down. This ensures a uniform hard- ness and microstructure over the whole weld in comparison with the situation where each run transforms to martensite in between passes. It will be clear from this discussion that the entire welding operation should be completed while the tool is hot. Partially welding, letting the tool cool down and then preheating later on to finish the job, is not to be recommended because there is considerable risk that the tool will crack. While it is feasible to pre-heat tools in a furnace, there is the possi- bility that the temperature is uneven (creates stresses) and that it will drop excessively before welding is completed (especially if the tool is small). The best method, of preheating and maintaining the tool at the requested temperature during weld- ing, is to use an insulated box with electrical elements in the walls (see page 6).
What determines the susceptibility of a weld to hydrogen cracking?
The susceptibility of a weld to hydrogen cracking depends on: • the microstructure of the weld metal (different microstructures have different hydrogen sensitivi- ties) • the hardness of the steel ( the greater the hardness, the higher the susceptibility) • the stress level • the amount of diffusible hydrogen introduced in welding
What are the heat treatments after welding?
Depending on the initial condition of the tool, the following heat treat- ments may be performed after welding: • tempering • soft annealing, then hardening and tempering as usual • stress relieving
How is the chemical composition of a weld determined?
The chemical composition of a weld deposit is determined by the compo- sition of the consumable (filler metal), the base steel composition and the extent to which the base material is melted during welding. The consum- able electrode or wire should mix easily with the molten base steel giving a deposit with:
How to prevent cold cracking welding?
As regards the susceptibility of welds to cold cracking, this is the factor that it is easiest to do something about. By adhering to a number of simple precautions, the amount of hydrogen introduced during welding can be reduced appreciably. • Always store coated electrodes in a heated storage cabinet or heated container once the pack has been opened (see earlier). • Contamination on the surfaces of the joint of the surrounding tool surface, e.g. oil, rust or paint, is a source of hydrogen. Hence, the surfaces of the joint and of the tool in the vicinity of the joint should be ground to bare metal immediately prior to starting to weld. • If preheating is performed with a propane burner, it should be remembered that this can cause moisture to form on the tool sur- faces not directly impinged by the flame.
How to prevent steel from cracking?
Follow-Up#N#One more thing -#N#Since you're talking about using air-hardening (as opposed to oil-hardening, water-hardening or brine-hardening) steel, you will probably want to let it cool really SLOWLY after you preheat, weld and postheat it, to prevent it from cracking due to excessive hardening.#N#One way to do that is to drop it into a big metal bucket of dry wood ashes after you weld and postheat it ... and then let it cool down overnight. The slower and more evenly it cools, the less chance there is of cracking, I think.
What temperature should I preheat a joint to weld?
You never mentioned if it was in the annealed or hardened state. If the joint area isn't doing any work (trimming, forming), preheat to 500-600*f, weld with 7018, peen often (best with an air hammer) & let cool in still air. Only if it were a really large weldment would I post heat.
Why is a weld hard when it freezes?
This can be a problem because internal shrinkage stresses can cause cracking in the hard (and not ductile) weldment.
Does water come out of steel?
Water don't come out of steel. If you heat, depending on environmental conditions at the time --- dew point, etc.,,,, you will see water. It's coming out of the air, not the steel. You ever squeeze a piece of steel, get water squirting out???
How does welding tool steel differ from welding the low carbon machinery steel?
Welding tool steels differs from welding the low carbon machinery steels since tool steels, because of their alloy content and the welding temperatures will actually harden to maximum hardness in and near the area welded.
What happens if you let the weld cool?
As you wrote, "Until it cooled", is the key. Without preheat and slow cooling after welding, the metal will become excessively hard. By allowing the weld to cool very slowly, the metal solidifies into metallurgical structures that are less hard. The following links attached below explain it better than me.
How long to cool annealed tools?
Postheat hardened tools for 1 hour per inch, 2 hours minimum, at 50F below the original tempering temperature. Annealed tools should be re-annealed.
What is A2 welding?
A2 is an alloy that was air hardened and probably is being used in cold work operations. To maintain as close as possible the characteristics after your repair welding, it is important to choose a compatible filler metal.
Can you weld tool steel?
We offer the following suggestions for optimum results in the welding of tool steel parts with the warning that as the alloy content and the hardness of the steel to be welded increases the danger of post-weld cracking increases. Note also that while the heat of welding will harden the higher alloy tool steels, it may actually soften the lower alloy grades to an unacceptable degree and the part may have to be re-heat treated after welding. Even in the higher alloys there will be a soft or overtempered zone between the weld and the base metal, but in these grades this soft zone is generally acceptable.
