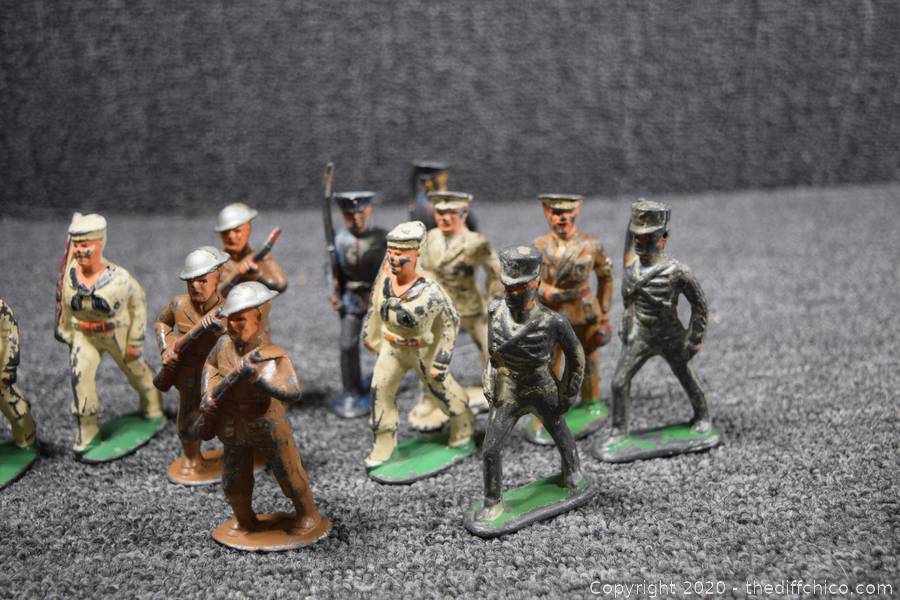
Can you solder diecast metal? Depends on the die-cast metal grade and type, but assuming Mazak, or Zamak Zamak (formerly trademarked as ZAMAK and also known as Zamac) is a family of alloys with a base metal of zinc and alloying elements of aluminium, magnesium, and copper. Zamak alloys are part of the zinc aluminium alloy family; they are distinguished from the other ZA alloys because o…Zamak
What metals can be soldered?
As such, soft soldering is ideal for a range of metals, including brass, lead, copper, tin, cast iron, and aluminum. For this text, we look at how to solder cast iron parts.
How to solder cast iron parts?
For this text, we look at how to solder cast iron parts. Tools Required Use the isopropyl solvent to clean the cast iron workpiece. If the component has oil or grease, use a rag to wipe it clean. It is essential to clean the component before soldering to prevent the metal from forming an extra coat of oxide.
Can You solder cast iron with a propane torch?
Light up the propane torch to heat the cast-iron piece directing the flame’s blue cone toward the metallic part. Be sure to move the iron around the area surrounding the seam until the solder has changed color and filled the seam. You should, however, avoid heating the solder directly.
How do you fix a broken soldering tip?
You can also coat the tip with flux by dipping it into a can of flux or by spreading the flux on a small brush and applying a little solder on the surface. Wipe excess solder using a rag when the solder is still melting to renew the tinning as the coat wears off fast Avoid melting the solder using direct heat from the soldering iron or torch.

How do you fix a die cast metal?
3:4510:05How to Solder and Repair Die-cast Cars. (Redline Restoration - YouTubeYouTubeStart of suggested clipEnd of suggested clipThis flux will help the solder flow into and around the broken diecast. Now comes the somewhatMoreThis flux will help the solder flow into and around the broken diecast. Now comes the somewhat dangerous part I'll be using a gas-powered soldering iron these get really hot really fast.
How do I join diecast metal?
0:164:24Pot Metal and Zinc Die Cast Repairs Made Easy With Super ... - YouTubeYouTubeStart of suggested clipEnd of suggested clipAfter drilling or drem bling the pits just heat with a soft flame add your flux and solder sand. NoMoreAfter drilling or drem bling the pits just heat with a soft flame add your flux and solder sand. No more pits. When the flux turns brown you add your solder. And you're done.
Can you weld die cast steel?
Die cast parts made from the alloy AlSi9MgMn (Silafont-36) are particularly well suited for welding, both the standard MIG and TIG methods (see Gas-shielded welding processes) and laser beam welding.
Can you solder cast iron?
You can solder a number of types of metals, including cast iron, which we'll look at in this post. Because soldering requires temperatures between two hundred fifty and six hundred fifty degrees Fahrenheit, you should use a propane torch rather than the more powerful, albeit more dangerous, oxygen-acetylene torch.
What is the best glue for diecast metal?
Epoxy Glues Mix the adhesive epoxy on a piece of old newspaper or printer paper and keep it close to the diecast. Apply the adhesive with a small brush or toothpick, which keeps you from using too much adhesive on the piece.
Will JB Weld work on diecast?
The best glue for diecast metal, bar none, is JB Weld. If you're not familiar with it, it's a super-strong epoxy that sets up harder than steel. It's more brittle than steel, but it still makes an exceptionally durable bond.
What's the best way to weld cast steel?
MIG welding can weld cast steels with great success, especially if you weld long joints or thin castings. In addition, it is the easiest process to use. The common ER70S-6 wire is more than enough to weld most cast steels with great results.
How can you tell the difference between cast iron and cast steel?
Cast Iron vs Cast SteelCast IronCast SteelCast iron have very good vibration damping properties.In terms of vibration damping, cast steel is inferrior to cast iron.More of Brittle Nature.Ductile nature.Machinability lower.Good machinability.Weldability is lower as compared to cast steelGood Weldability5 more rows
What is the best way to weld cast steel?
Welding Cast Steel Step By StepStep 1 – Grind surfaces flat enough for good fusion between parts. ... Step 2 – Use a filler material with a low-hydrogen content. ... Step 3 – Preheat if necessary. ... Step 4 – Position filler material correctly. ... Step 5 – Take slow, steady welds with short arc lengths.More items...•
What metal Cannot be soldered?
Of metalsSolderabilityMetalFairCarbon steel Low alloy steel Zinc NickelPoorAluminium Aluminium bronzeDifficultHigh alloy steel Stainless steelsVery DifficultCast iron Chromium Titanium Tantalum Magnesium2 more rows
Is it better to braze or weld cast iron?
Generally, welding two pieces of iron together is a bad idea, you'll be better off with brazing. More on brazing later. Welding cast iron works much better with repair jobs, like cracked parts or when you drilled a hole in the wrong place and you need to fill it in.
Does silver solder work on cast iron?
Silver Solder can be used to join most common metals, including Mild Steel, Stainless Steel, Copper, Brass, Cast Iron and Dissimilar Metals.
How to repair cracks in pot metal?
The first step for any pot metal cracks repair is cleaning the pot metal. We recommend using a Dremel as shown to prepare the cracks before beginning torch work. Note the technique: it’s vitally important to remove all oxidation or impurities from the pot metal cracks prior to soldering. Be sure to strip all pot metal surfaces before you begin ...
What is the #2 problem with pot metal?
Cracks or gouges in zinc die cast/pot metal is the #2 pot metal restoration problem, second only to pot metal pitting. For this instructional video, we simulate cracks in pot metal by using a Dremel tool to create a groove in a pot metal part.
Can you use heat freeze to repair pot metal?
We were demonstrating this pot metal cracks repair using a pot metal piece previously featured in our “pot metal pits” repair video. We were aware that the previous solder could loosen if we didn’t stop the heat from spreading, so we used Heat Freeze Heat Paste to stop heat transfer and to protect an existing solder repair in the adjacent area.
Can you remove excess flux from pot metal?
Excess flux can be removed with warm water and a wire brush. Super Alloy 1 is a perfect match for pot metal, so no one will ever notice the cracks you’ve repaired with Super Alloy 1 pot metal solder and flux kit.
What temperature to solder zinc die cast?
While zinc die cast can be difficult to solder due to its low melting temperature of 786°F, Super Alloy 1 has a working temperature of 350°F, making it the ideal solution for soldering or brazing zinc die cast parts–with any torch: propane, MAPP gas, butane, acetylene, oxyacetylene, or even a heat gun. And Super Alloy 1’s unique liquid flux acts ...
What is zinc die cast?
Zinc die cast is an inexpensive alloy used in many manufacturing applications, due to its corrosion resistance, high strength, electrical conductivity, and thermal conductivity. Zinc die cast is also sometimes referred to as Zamak.
What metals are super alloys?
Super Alloy 1 also bonds pewter, pot metal, white metal, monkey metal, stainless, bronze, steel, aluminum, brass, and copper–individually or together in any combination. This one rod is a must have for every toolbox. A few things to remember:
What metals are used in pot metal casting?
There is no metallurgical standard for pot metal but the blends generally include zinc, aluminum, magnesium, cadmium, copper, and tin in varying degrees. While the low melting points are great for casting, pot metal also has a low boiling point, which can lead to air bubbles in the casting that show up later as pitting.
How many bolts to install a die cast bracket?
After drilling the three 1/8-inch holes in the backing plate we bolted it to the back side of the bracket using three 10-24 bolts. Gently tighten bolts, being careful not to break the die-cast piece in the process.
How many bolts did JB weld remove?
After allowing the JB Weld to cure overnight we removed the three bolts. Greasing the bolts made removal easy as the epoxy did not stick to the threads. At this point the bracket is strong.
What kind of gloves do you use to flatten a JB weld?
On the back side of the bracket we flattened the JB Weld with our finger for a smoother seam. We always wear Nitrile gloves when working with adhesives.
What is structural integrity of pot metal?
The structural integrity of pot metal means it is generally used for parts not subjected to high stress. Like most things, age is not pot metal's friend. As pot metal ages it is prone to oxidation and corrosion both from external contaminates and from internal corrosion.
Why are ferrous metals not used in pot metal?
The reason ferrous metals are not used in pot metal relates to the desire to keep the melting temperature low. Zinc melts at 786 degrees F, which also minimizes energy costs in the casting process. There is no metallurgical standard for pot metal but the blends generally include zinc, aluminum, magnesium, cadmium, copper, and tin in varying degrees. While the low melting points are great for casting, pot metal also has a low boiling point, which can lead to air bubbles in the casting that show up later as pitting.
Why is pot metal not used in automotive?
The reason ferrous metals are not used in pot metal relates to the desire to keep the melting temperature low.
What is special solder?
Specialty Solder. The most common solders are alloys of lead and tin, which are very difficult to use with oxidized metals; others are formulated specifically for use with these metals (i.e. steel and aluminum). Advertisement.
What prevents base metals from oxidizing during the soldering process?
Flux prevents the base metals from oxidizing during the soldering process.
What is the difference between soft solder and hard solder?
Hard Solder. Soft solder uses a low-melting point metal (most often lead or tin) to make it more manageable at the expense of a weaker bond; Hard solder requires flux but forms a much stronger bond because of its higher melting point. Advertisement.
Which metals have a higher melting point?
While silver, bronze, copper, brass and some steels form strong chemical and physical bonds on their own, metals such as high-alloy steels, cast iron, aluminum and titanium often require an alloy with a higher melting point.
What is soldering metal?
Soldering is the process of securing metal joints and electrical components to create stable joints. There are two methods of soldering items: soft and hard soldering. Soft soldering involves joining metal pieces using filler material called Eutectic Tin/Lead Alloy. It is ideal for joining delicate parts that get damaged at high temperatures.
How to melt solder?
Avoid melting the solder using direct heat from the soldering iron or torch. Instead, use the torch or iron to heat the pieces forming the joint until the component is hot enough to melt the solder upon contact. The heated metal part is what melts the solder once fed into the joint. Concentrate on the heavier and thicker parts pulling the soldering iron away momentarily while touching the solder to the joint. The solder should be sucked into the joint fast if the metal is hot enough and if you have applied enough flux to the joint
What is soft soldering?
Hard soldering, however, uses a different alloy that melts at a high temperature and uses a torch that generates more heat than the ordinary propane torch. As such, soft soldering is ideal for a range of metals, including brass, lead, copper, tin, cast iron, and aluminum. For this text, we look at how to solder cast iron parts.
What temperature does hard solder melt?
Tools Required. This type of solder is used because it melts at a relatively low temperature, i.e., 250-650 degrees Fahrenheit. Hard soldering, however, uses a different alloy that melts at a high temperature and uses a torch that generates more heat than the ordinary propane torch.
How to heat flux cast iron?
Then, heat the fluxed cast iron pieces using a propane torch until it gets heated up. Then scrub the component again and apply another layer of flux.
How to put cast iron together?
Place the cast-iron workpiece in the desired position and clamp the pieces together. Then, heat a small amount of solder at the tip and apply it to the seam running it between the metal pieces once it starts melting.
How to keep soldering iron hot?
Be sure to keep the soldering iron in contact with the metal to ensure it is hot enough to melt the solder. Also, keep the iron on the opposite side of the metal or a few inches away from where you are feeding the solder.
