
How often should I recalibrate my torque wrench?
How often should I calibrate my Torque Wrench? Recalibration should be 5000 cycles or every 12 months. However, the standard recognises that many businesses will have their own procedures for the control of test devices and, as a torque wrench can be considered a test device, a company’s own procedures must take precedence over the default 5000 cycles/12 months.
How often do torque tools require calibration?
Some professionals believe that the performance of the tool is affected between 2,500-3,000 repetitions. Therefore, it is generally recommended to calibrate the torque wrench after 2,500 repetitions have been made.
How often does a torque wrench need recalibrated/?
Nearly all torque wrenches will need to be recalibrated approximately once each year, or about every 5,000 uses. Since you most likely are not keeping track of how often you use your torque wrench, once a year is a good rule of thumb. How you calibrate a torque wrench will depend on the type you purchase or own.
How to measure a torque wrench?
Measure from the center of the fastener to the center of the square drive tang on the torque wrench. Measure in a line parallel to the body of the wrench. If the position of the crowfoot wrench decreases the effective length of the torque wrench, creating a negative change, then input this amount into the equation as a negative number.
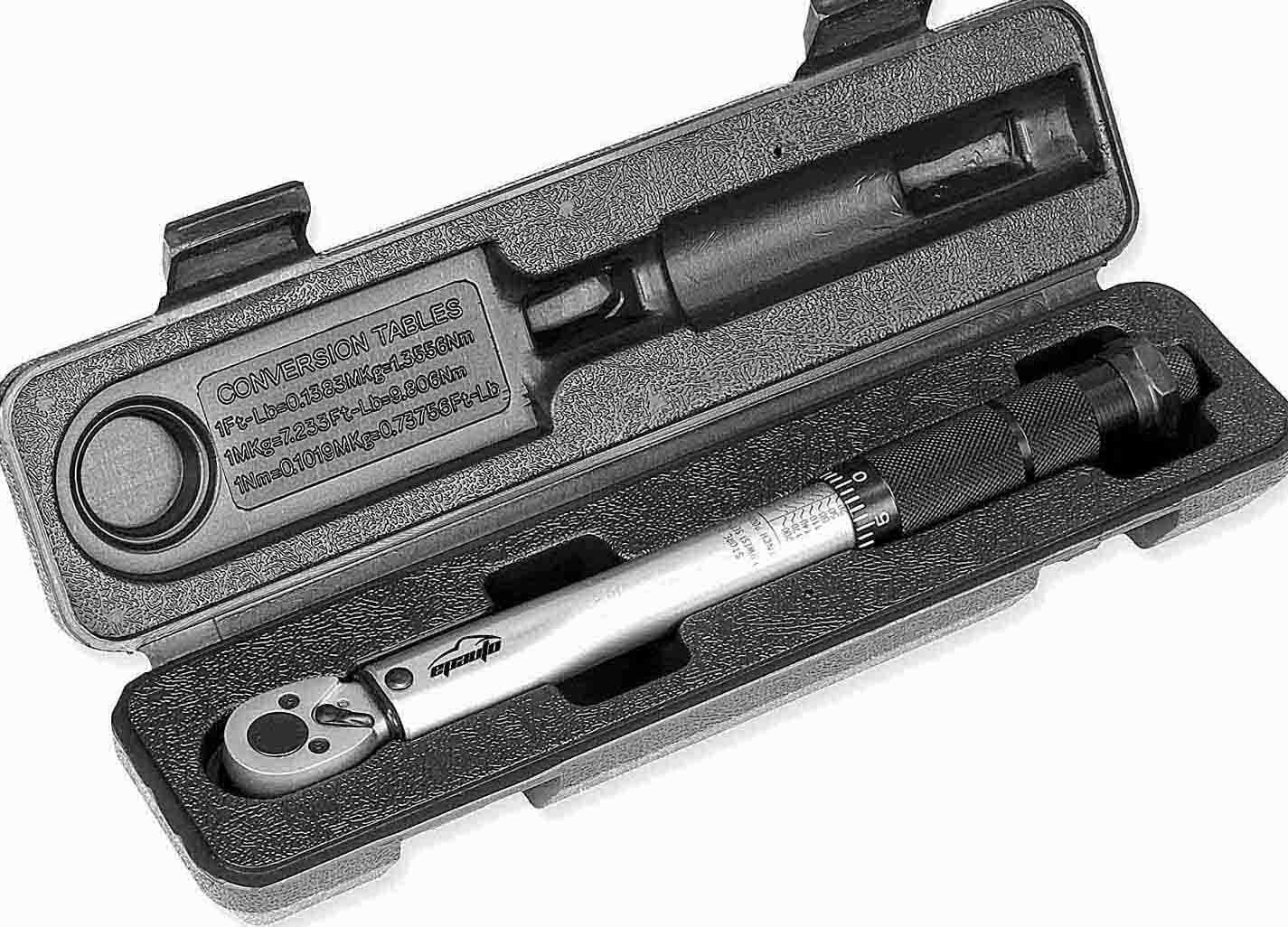
How often should a torque wrench be calibrated?
twelve monthsAs a general rule of thumb, it's wise to test the calibration of your torque tools every six months or twelve months. That's rare enough that it doesn't impede productivity and often enough that it doesn't create obscene liabilities.
How long do torque wrenches stay calibrated?
As per the official website of the International Organization of Standardization, ISO 6789 states that a torque wrench should be re-calibrated every 5000 uses or every 12 months.
How do I know if my torque wrench is calibrated?
1:214:48Is your torque wrench accurate? Simple test to check. - YouTubeYouTubeStart of suggested clipEnd of suggested clipSo usually when you see a weight on there you'll see the weight to one side to the other side itMoreSo usually when you see a weight on there you'll see the weight to one side to the other side it could be off just a little bit.
How accurate do torque wrenches need to be?
Every torque wrench operates within a given accuracy range, such as ±2-4% over 20% to 100% of full-scale. Imagine that a beam-type wrench has a 40-250 ft-lb range with an accuracy range of ±2-4% over 20% to 100% of full-scale.
How do they calibrate a torque wrench?
0:532:29How to Calibrate Your Torque Wrench - EASY DIY Tutorial - YouTubeYouTubeStart of suggested clipEnd of suggested clipWe want to start by setting the torque wrench to 40 foot-pounds of torque. Since this is what we'llMoreWe want to start by setting the torque wrench to 40 foot-pounds of torque. Since this is what we'll be testing it against take your torque wrench. And put on a lug nut socket. Put it on your wheel.
Can you over tighten with a torque wrench?
A torque wrench prevents but do not avoid over tightening! The good practice here is to start over : Loosen the bolt first, tighten with an adapted tool and finish with the torque wrench to reach the correct and safe torque.
Do torque wrenches go bad?
A fully loaded torque wrench, left in storage for a long period, can cause a set in the spring, causing it to weaken over time.
Can you calibrate a torque wrench yourself?
You can pay a professional testing lab to do the calibration, or you can assemble a torque wrench calibrator and do the testing yourself. To perform a torque wrench calibration on your own, you need to determine the calibration ratio and multiply that amount by the required bolt torque.
Are digital torque wrenches accurate?
Digital torque wrenches are very accurate instruments. However, their more delicate construction requires extra care while handling. They also require batteries in order to operate.
What range are torque wrenches most accurate?
Bottom line: A wrench is only as accurate as its scale allows. Accuracy Range. Most torque wrenches, regardless of type, state their expected accuracy to be within some range; usually ±2-4% over 20%-100% of full scale for the particular wrench.
Is 4% accuracy for a torque wrench good?
As stated above, most torque wrenches have an accuracy between 3-5%. Let's talk about 100 FT LB torque wrench at 4% accuracy. That would be an accuracy of 4 FT Lb. In this specific case they stated " Every time we get our torque wrenches back from calibration, I get complaints that they are not reading properly."
Do you push or pull a torque wrench?
pullAlways pull, rather than push, a wrench for greater control and balance. That way, if the nut or bolt should suddenly loosen, you're less likely to go flying. Never try to get more torque from a wrench by using a cheater bar or other device to extend the leverage.
Can you use a torque wrench below lowest setting?
Certainly, if a torque wrench is wound back at all it should not be adjusted below the minimum scale marking (usually 20% of maximum) - never to zero as this can adversely affect the calibration of the wrench. Beyond that, it really depends on the application.
How do you maintain a torque wrench?
Store correctly. Always keep your torque wrench dry and store it in an appropriate case to protect it from chemicals, grime and dust. Before storing, make sure to wipe down your wrench with a clean cloth as residue liquid could damage or corrode the wrench over time if left unattended.
Why does my torque wrench not click?
It could be the fastener is over tightened in the first place and it is clicking away without you noticing it at the beginning of the swing. If it still doesn't click, you'll need a new torque wrench.
Can Craftsman torque wrenches be calibrated?
The torque wrenches can not be re-calibrated.
What range are torque wrenches most accurate?
Bottom line: A wrench is only as accurate as its scale allows. Accuracy Range. Most torque wrenches, regardless of type, state their expected accuracy to be within some range; usually ±2-4% over 20%-100% of full scale for the particular wrench.
Does temperature affect torque wrench?
Temperatures exceeding 120 degrees, meanwhile, will cause the grease inside of the wrench to melt and seep out, affecting performance and accuracy.
Do torque multipliers need to be calibrated?
The torque multiplier shall be re-calibrated if it was exposed to an overload larger than 20% of the rated capacity, after a repair has been carried out or after an improper use which can influence the measurement uncertainty and/or the multiplication ratio.
Is A Digital Torque Wrench Reliable Tool To Use?
Check the manual guide if you are thinking about checking torque wrench accuracy. The best thing to find is how accurate and reliable a tool is depends on how accurately a wrench measures the required torque.
Do A Digital Torque Wrench Needs To Be Calibrated?
A simple, primary reason to calibrate digital torque wrench is that an analogue to digital converters has a voltage reference, and this voltage can drift. This drift in the system can cause an unstable voltage supply, and you can have inaccurate readings.
What is torque wrench calibration?
Torque Wrench Calibration. A torque wrench, as the name suggests, is a wrench used to apply a specific torque to a fastener such as a bolt or a nut. This should be the only thing that a torque wrench is used for.
How to measure torque wrench?
Step 1. Measure and mark the length to your reference point. Your first step is to measure from the center of the torque wrench drive to a point on the handle. Make your measurement in inches and for easy calculations, use a whole number. Use the marker to mark the point where you measured on the handle.
How to hang a torque wrench from a workbench?
Lock the drive of the torque wrench in the vice so that the handle of the wrench is in a horizontal position and hanging away from your workbench. There should be enough clearance to the sides and below the wrench handle so that you can freely hang the weight from it.
What is the most common torque wrench measurement?
The most popular torque wrench measurements are Newton-meter (Nm) and foot-pound (ft-lb).
What to do if your torque wrench doesn't click?
If it didn’t click, move the weight slightly toward your marked point until it clicks. Depending on the precision requirements of your job, you may be able to work with a torque wrench with a couple of millimeters tolerance and can, therefore, consider you torque wrench to be calibrated.
Can you damage a torque wrench drive?
Be careful not to damage your torque wrench drive when locking it in the vice. If necessary, use a soft metal such as aluminum between the vice jaws and the drive so as not to cause any damage.
Can you calibrate a torque wrench yourself?
You can always take your torque wrench to a reputable calibration technician but if you are the adventurous do-it-yourself type, you can calibrate it yourself. In this article, I will explain the procedures for calibrating your torque wrench at home or in your shop.
Why is Torque Wrench Calibration Necessary?
Getting a torque wrench calibrated is essential in order to gets its accuracy verified. Apart from accuracy, calibration also measures the reliability of the jobs performed by the wrench from day-to-day working. The permissible window of calibration error is set at 5% and any error beyond that may seriously affect the performance of the tool.
What happens if torque errors exceed the permissible limit?
If the errors on torque reach beyond the permissible limit, recalibration needs to be considered.
Do torque wrenches need to be calibrated?
A torque wrench requires regular calibration, depending upon the frequency, degree, and kind of usage over a period of time. By learning about when to calibrate the torque wrenches, one would easily be able to correct the performance every time and attain reliable final results.
What is Torque Wrench Calibration and Why Is It Important?
Calibration of a regular torque wrench is vital to the proper application of the tool. It ensures that the wrench can provide proper, accurate readings in relation to industry standards. As such, having a torque wrench properly calibrated is not only vital for proper application, it also ensures its efficacy. Simply put, there is no use in having a tool that isn’t properly calibrated.
How Often Should Digital Torque Wrenches Be Calibrated?
There is no set time frame for how long digital torque wrench calibration should last. In general, the factory calibration of your torque wrench should endure past several uses from your initial purchase, but it does depend somewhat on the type of torque wrench you use. (Again, make sure that yours comes with a torque wrench calibration certificate).
How Do Torque Wrenches Work?
(For reference, the formula for torque is: force x length = torque).
How accurate is a torque wrench?
Torque wrench accuracy specifications can range anywhere from 6% to 1% and the purchase price usually scales along with it. When required to maintain a very tight torque specification, it is recommended that you purchase a higher-quality torque wrench.
How much does dropping a torque wrench affect accuracy?
Accidental drops are especially important to avoid. Dropping a torque wrench just once may affect the accuracy by as much as 30 percent ! Determining the frequency of calibration for your torque wrench may be mandated by your specific industry or it could be a personal decision based on one or many of the factors above.
What happens if you store a torque wrench?
If you store your torque wrench at any torque value greater than its lowest setting (usually 20% of maximum), the tension spring will remain under load and weaken over time. This will cause your torque wrench to produce less torque across the range and ultimately lose accuracy.
What causes a torque wrench to rust?
If you frequently use or your torque wrench in below freezing or extremely high temperatures (above 120 degrees Fahrenheit) you run the risk of your tool developing condensation that can cause internal rusting. Premature rusting can also be caused by operating or leaving your torque wrench out in the elements (rain, sleet, or snow).
Can a torque wrench be adjusted back?
Unfortunately, in some cases, your torque wrench may not be able to be adjusted back within manufacturer’s specifications and will need to be replaced.
Can you use a torque wrench as a breaker bar?
Do not use pipes or cheater bars and never use the wrench as a breaker bar.
How to test torque wrench?
It consisted of a device with a certified weight hung from a bar that had a known distance from the center of rotation attached to a pivot. A torque wrench under test was connected and turn until the weight was lifted. From this you could calculate the torque applied with great accuracy.
What torque wrench do I need for lug nuts?
You don’t need a great torque wrench for lug nuts. The precise torque isn’t as important as making sure that all the nuts for a wheel are tightened to the same degree so the load is evenly applied. For larger cars, I use 90 lbs.-feet, and 100 or more on light trucks using slightly larger diameter studs. On a smaller car I might use as low as sixty pounds feet. Check your manuals for the correct specification! That 90 lbs.-ft. figure is assuming your lug nuts and wrench are 19mm or 3/4″. A 1/2″ drive torque wrench from Harbor Freight or a discount store should be fine for wheel studs, though I’d suggest getting a higher quality one for most anything else. A ‘click’ type would be best, since it can be hard to read the scale on one that isn’t when doing lug nuts. Just be sure that you STOP applying pressure when you hear one click. If you hear two clicks before you stop pushing or pulling, you’ve overshot your desired torque. Do be sure to reset your torque wrench to either ‘STOP’ or a low setting before you put it away in order to maintain some semblance of calibration.
What is calibration in metrology?
In measurement technology and metrology, calibration is the comparison of measurement values delivered by a device under test with those of a calibration standard of known accuracy. Wikipedia
Can you tighten a bolt without a torque wrench?
You may not guess at torque! Even the most experienced technicians use a torque wrench. Master technicians can do some tightening without a wrench because after hundred maybe thousands of tightening certain bolts/plugs they know not to over tighten. One example is drain plugs. Many amateur mechanics over tighten and strip drain plugs when changing oil. There is a torque setting for drain plugs, but after doing it repeatedly its a feeling one gets with the wrench.
Is a torque wrench accurate?
A good quality torque wrench is most likely accurate but it is really not calibrated unless it has documentation showing that it’s reading were within some agreed upon tolerance. By their nature, they are unlikely to have this accuracy change over time unless grossly abused or used so much that the wrench is worn out.
Do torque wrenches need calibration?
So yes a tor que wrench needs calibration if you want to be able to claim that a known torque has been applied.
Do caliper brackets fall out?
Yes you do. The caliper bracket bolts many times are torqued to ABOUT 90 ftlp while the guide pins are much less about 45 or so. What happens is that many time the small bolts are over-tightened and the either get the head rounded off or the threads strip out. The caliper bracket bolts are too loose and they fall out since most people do not use thread locker.
How to get a torque wrench to work?
Move the weights up the handle if you hear a click. Listen for a click from the torque wrench as you hang the weight from the marked point on the handle. If you hear one, lift the weight off the handle and set it down again further up the neck, moving toward the head of the wrench.
How to determine torque wrench setting?
The equation is: handle distance times weight divided by 12. In order to determine the right setting for the torque wrench, multiply the distance you measured in step 2 by the 20 pounds you will be using for your weight. That comes out to 480 inch-pounds (24 inches times 20 pounds) which equates to 40 foot-pounds (480 inch-pounds divided by 12).
How to prolong life of torque wrench?
While all torque wrenches will need to be calibrated regularly, you can prolong the life of each calibration by returning the setting of the torque wrench to zero after each time you use it.
How to measure torque wrench?
1. Measure from the square drive to the handle. The square drive is the end of the torque wrench you’d attach a socket to. For the sake of simplicity, use whole inches rather than using any fractions. Mark the point you measured to on the handle and record the distance on a piece of paper for you to come back to later.
What to do if torque wrench falls?
Store the torque wrench low, so if it does fall, it won’t be far enough to cause any significant damage to the calibration.
How to hang a weight from a torque wrench?
Hang the weights from the handle of the wrench. Tie the rope to the weight and make a loop that you can hang from the handle of the torque wrench where you made your mark in step 1. Make sure the length of rope is short enough that the weight won’t touch the ground once you hang it.
Why does my calibration drift?
The strain on the internal spring can cause the calibration to drift if not left on zero.
Where to get a professional calibration for any torque wrench?
The best place to have a torque wrench equipped is a special torque testing laboratory capable of managing any form of torque device, including a torque multiplier, of up to 35.000 pounds per foot of applied force and a torque transducer that can weigh up to 20.000 pounds per foot.
What is calibration in torque wrenches?
Calibration is a measure that defines the accuracy of precise tools like torque wrenches. This parameter is typically checked in torque wrenches and similar tools where accuracy is the most essential factor. The calculation of the physical force applied by the torque wrench is calculated and compared to its fixed torque value. In such a way, you may define the accuracy of a certain torque wrench range permitted by the International Organization for Standardization (the short is ISO).
What to check before buying a torque wrench?
As you might have guessed, calibration is one of the most important factors to check before buying a torque wrench. Consider choosing the wrenches with pre-calibration at the manufacturer’s factory, according to ISO standards. Only these top-notch tools won’t let you down when fastening or loosening the bolts/screws/nuts.
Why do mechanics use torque wrenches?
Mechanics depend on torque wrenches to have precise and consistent torque measurements such that the correct amount of force can be applied to the nuts and bolts in the vehicle. Nonetheless, torque wrenches need to be adjusted periodically to ensure correct readings are given. Although it might be better to take your torque wrench ...
How much torque is required for a torque wrench?
For general, the ISO standard requires 4 to 6 percent above or below the torque range shown by the setting of the torque wrench while measuring. Although everything above such limits is deemed to be non-compliant. To test if a torque tool is not calibrated, you may need the help of professional and special equipment.
How to calibrate a tool when there is no lock?
If there is no lock, place the socket on the wrench and put the socket and then the tool on the lug nut of your vehicle part. Leave some vertical room to add the rope and the weight to do the calibration check properly.
What is a square drive torque wrench?
The square drive is the ending point of any wrench to which you can mount the plug. Using entire inches instead of using the percentages for convenience. Label the stage you calculated to the handle and document the distance on a sheet of paper to bring you back to later. Set the document aside in a quiet position before you use it. Because 24 inches is a typical length for most torque wrenches, it will serve as a guide for further moves.
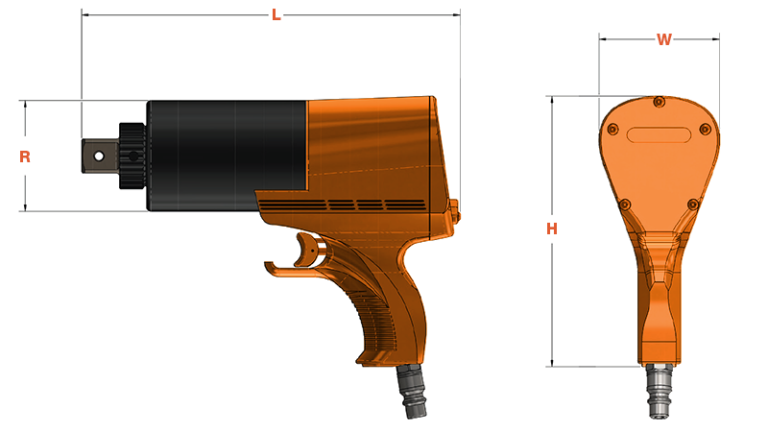