
What is a phosphate coating?
It combines with or causes a chemical conversion that transforms the surface of the metal part into a protective layer, which is uniform and inert to the environment. Phosphate coating combinations include zinc phosphate, iron phosphate, chromate, or manganese phosphate.
What are the disadvantages of phosphate coatings?
Although phosphate coatings provide good adhesion and some barrier protection, when the coating becomes damaged the corrosion progresses rapidly starts on the open metal surface because low solubility phosphates do not possess enough inhibiting power compared with chromates and thus cannot provide self-healing of the damaged zone.
Why is my Zinc phosphate rusting?
A. Depending on your bath chemistry you may be running out of accelerator. If your Zinc Phosphate appears OK but rusts when drying you should check your free/total acid ratio. Be sure to limit drying of parts between phosphate and rinse. Q.
What is the difference between zinc phosphate and iron phosphate coating?
Zinc phosphate is a non-metallic, crystalline coating that is extremely adherent to materials. It is important to note that the zinc phosphate coating results from the solution itself, not from the part surface like an iron phosphate coating.
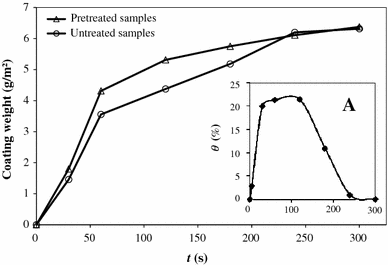
Does phosphate coating prevent rust?
Phosphate coatings are often used to protect steel parts against rusting and other types of corrosion. However, they are somewhat porous, so this use requires impregnating the coating with oil, paint, or some other sealing substance.
Is black phosphate rust proof?
Black Phosphate This coating normally is gray to black in appearance and provides mild corrosion resistance.
Does black phosphate coating rust?
Black Oxide adds a mild layer of corrosion and abrasion resistance to fasteners. Like any material, black oxide treated fasteners can rust in the right environments.
Does phosphate cause corrosion?
Acid Phosphate Corrosion occurs where high levels of deposits are present and an acidic phosphate compound is used as part of the boiler water or evaporator water treatment program. Poor feedwater treatment often results in high corrosion product levels.
Can phosphate coating be removed?
Industrial laser cleaning can remove all types of phosphate coatings, including iron phosphate coatings, manganese phosphate coatings, and zinc phosphate coatings.
Is phosphate coating same as galvanized?
Phosphatizing is usually a pretreatment for paint or powder coating, whereas galvanizing is a heavy coating of hot-dipped zinc. A galvanized surface is far more corrosion resistant than an unpainted phosphatized surface, but can be difficult to paint.
Which is better black nitride or phosphate?
A nitride exterior will protect the barrel longer than a phosphate exterior finish. However, a chrome-lined, or phosphate, barrel will hold up better to sustained fire than a nitride interior. Nitride has a slight edge in accuracy and price. However, phosphate coated/chrome lined barrels are more common.
Can you paint over phosphate coating?
Ideally, you would paint the parts right after applying the phosphate coating. If the parts are not going to be painted, then you can apply some kind of rust inhibitor that can act as a barrier to corrosion.
Are phosphate screws rust proof?
Black drywall screws have a phosphate coating that is supposed to keep the wet drywall compound from causing the screw head to rust.
What are the negative effects of phosphate?
Phosphate toxicity can exert cytotoxic effects to compromise the functional ability of various organ systems. Phosphate toxicity can induce an increased rate of apoptosis in various tissues that can be suppressed by reducing the phosphate burden [40].
Why is phosphate banned?
While phosphates are low toxicity, they instead cause nutrient pollution and feed the algae. This leads to eutrophication and harmful algal bloom. Many countries have banned the use of phosphates in detergent, including the European Union and the United States.
Why do we no longer use phosphates?
Phosphate has been essential to feeding the world since the Green Revolution, but its excessive use as a fertilizer has led to widespread pollution and eutrophication. Now, many of the world's remaining reserves are starting to be depleted.
Does chemical blacking prevent rust?
Red oxidation is commonly known as rust, and black oxide can keep it at bay. The process doesn't actually oxidize the metal; the cold black oxide “coating” comprises a very thin layer of copper selenium. This compound prevents rust from forming on the steel and also gives the part some resistance to mild abrasion.
Will black chromate rust?
1) Black Chromates give Corrosion Protection to your Parts / Components (and to the Zinc Deposit / Coating). The Black Chromate Layer protects the Zinc Coating against the Formation of White Rust.
Is black zinc rust proof?
Black Zinc Provides mild corrosion resistance and a black finish. It is thicker than a Black Oxide finish, so on tight fitting parts be wary of this finish. If a stylish finish is required as well as corrosion protection this is a good option.
Does black zinc coating rust?
Zinc plating offers sacrificial protection against corrosion and black oxide does not. Black oxide has no rust resistance except its wax or oil.
What is phosphate coating?
Phospate Coating- What Is It? Phosphate coating is a crystalline coating applied on the outside of ferrous metals to inhibit corrosion. The phosphate coating is usually gray to black color on the surface.
How is phosphate coating weight measured?
Choose a phosphated item (about 5 cm x 10 cm), then degrease in trichloroethylene or clean mineral spirits. Dry the item and cool to room temperature.
What is meant by phosphating or iron phospate coating?
Phosphating is the process of covering a surface with iron phosphate coating. It's defined as a pretreatment method for corrosion protection. Meaning phos phating on metal reacts chemically to provide an insoluble crstalline layer.
What causes phosphate crystals to grow?
The temperature of the phosphate solution, insufficient accelerator, poor pre-cleaning, and insufficient processing time in the hot phosphate bath is most likely to effect phosphate crystal growth. Be sure to measure the coating weight, see MIL-DTL-16232G PDF.
What is phosphate conversion coating?
Phosphate conversion coatings are used on steel parts for corrosion resistance, lubricity, or as a foundation for future coatings. If not done properly the base layer will not chemically bond with the protective coating.
Why do immersion heaters shut off?
All the immersion heater systems have a liquid level safety to shut the heaters off in the event of evaporation, tank leakage, or chemical hose failure. There are no right answers, only intelligent choices.
What is double boiler tank?
Double boiler tanks. This is a tank in a tank. Outer tank made of steel or stainless and the inner tank is 300 series stainless. The heating system is flanged heaters mounted on the outer tank. The design is critical because the inner tank wants to buoy out of the outer tank. So, tank structure is to be considered carefully. Use inhibited ethylene glycol if you use steel. You can also use heat transfer oil like Mobil 1.
How are Mg coatings prepared?
Conversion coatings have been prepared by a variety of processes on Mg and its alloys. The natural oxide layer on Mg-based materials is vulnerable and provides very limited protection. This layer can be thickened by using thermal, hydrothermal, or alkali treatment ( Lorenz et al., 2009 ). CaP coatings are commonly prepared on Mg and its alloys by immersion in solutions containing calcium and phosphate ions such as simulated body fluid (SBF) ( Gray-Munro and Strong, 2009 ). However, satisfactory results have yet to be obtained due to crack formation and poor coating adhesion. Similar immersion procedures can also be used to fabricate fluoride-containing thin films.
How is manganese phosphate used in gearboxes?
Manganese phosphate coatings are used for reducing wear and for improvement in the running-in of a gearbox. In the phosphating process, phosphoric acid pickles the surface and forms with Mn-ions a layer of phosphate crystals with high oil affinity. The dissolution of metal leads to pits in the surface, referred to as surface porosity. Surface porosity influences both gear noise and friction. In this paper, the phosphating process parameters are studied, both in the activation immersion step and the consecutive phosphating immersion step. The purpose of this study has been threefold. Firstly, to characterise the surface porosity with one measurement parameter. Secondly, to identify the parameters with the greatest influence on crystal sizes and surface porosity underneath the phosphate layer. Thirdly, to obtain a mathematical model which will predict coating thickness and surface porosity.
What is phosphate coating?
Phosphate coatings are made up of thin crystalline layers of phosphate compounds that adhere to the surface of the metal substrate. The phosphate crystals are porous and can be formed from zinc, manganese or iron phosphate solutions. Each of the three types provides a phosphate coating with slightly different properties, such as crystal size and coating thickness. This allows a more specialized coating to be selected for the particular application required for part of the structure. These coatings are usually applied to carbon steel, low-alloy steel and cast iron. The coating is formed by either spraying or immersing the substrate into a solution of dilute phosphoric acid combined with other chemicals that assist in the coating process. Phosphate coatings can also be applied to zinc, cadmium, aluminium, tin and galvanized steel, but are difficult to apply on material with high alloys, which are often immune to the phosphoric acid. The main components of a phosphating solution are:
How is zinc phosphate formed?
Zinc phosphate coating is formed by crystallization on the surface by a chemical reaction. Zinc phosphating should be applied by spray or immersion, and it can be used for any phosphating application.
What is conversion coating?
Conversion coatings refer to the types of coating which on application convert the substrate into a compound with desirable properties. The surface so prepared provides a high degree of adhesion and corrosion resistance. Some important conversion coatings are described below.
What is manganese phosphate coating?
Manganese phosphate coatings are applied when wear resistance and antigalling properties are required. Manganese phosphate also possesses the ability to retain oil, which further improves anti-friction properties and imparts corrosion resistance to the coated parts.
What is the coating bath made of?
The coating bath consists of an acidic mixture of phosphate, chromate and fluoride. Fluoride acts as an accelerator. It is applied to aluminum. The mechanism is given below:
What is phosphate coating?
Phosphating or phosphate conversion coating is a manufacturing process in which an acidic bath solution reacts with the metal part or weldment and combines with or causes a chemical conversion that transforms the surface of the metal part into a protective layer, which is uniform and inert to the environment.
What is the most important stage of powder coating?
The most important stage of powder coating phosphate wash is properly preparing the parts by cleaning residues left from prior processes like welding, grinding, and drawing residues such as machining oils, grease, dust, and rust and then iron phosphate coa ting. This is commonly achieved in a multistage alkaline cleaning, rinsing, phosphating, and rinsing immersion tanks or spraying system. Iron phosphate can sometimes combine washing/cleaning with phosphating depending on initial part cleanliness.
What is phosphating used for?
The most common use for phosphating is pretreatment of parts before they enter a powder coating system.
What are the benefits of conversion coating?
Benefits of the conversion coating process include: surface that is tightly bonded to the base metal. increased surface area. improved corrosion resistance. better adhesion post processes like powder coating paint. Phosphating can be performed on ferrous (iron, steel based) and non-ferrous surfaces (zinc, chrome, aluminum, and manganese).
What is Chromium Phosphate used for?
Chromium phosphate. Chromium phosphate is most commonly used for aluminum alloy based parts. While this process is effective, like zinc phosphate, it uses heavy metals which need to be recovered for environmentally friendly disposal.
What are the controls for phosphate conversion?
The most important process controls in phosphate conversion coating are: Time – The longer the contact time, the more time to chemically react. The process must be long enough to allow the chemistry to form a uniform coating. Temperature – Chemistries typically become more aggressive at elevated temperatures.
What is the effect of pH on coating?
Concentration and pH – The more acid in concentration accelerates the coating process and can result in a heavier total weight of the coating .
What is phosphate conversion coating?
Phosphate conversion coating is a chemical treatment applied to steel parts that creates a thin adhering layer of iron, zinc, or manganese phosphates, to achieve corrosion resistance, lubrication, or as a foundation for subsequent coatings or painting. It is one of the most common types of conversion coating.
How to make phosphate coating?
A phosphate coating is usually obtained by applying to the steel part a dilute solution of phosphoric acid, possibly with soluble iron, zinc, and/or manganese salts. The solution may be applied by sponging, spraying, or immersion. Phosphate conversion coatings can also be used on aluminium, zinc, cadmium, silver and tin.
What are the different types of phosphate coatings?
Types. The main types of phosphate coatings are manganese, iron, and zinc. Manganese phosphate coatings are used both for corrosion resistance and lubricity and are applied only by immersion. Iron phosphate coatings are typically used as a base for further coatings or painting and are applied by immersion or by spraying.
What happens when a solution is acidic and metal?
The acid and metal reaction also creates iron phosphate locally which may also be deposited. When depositing zinc phosphate or manganese phosphate the additional iron phosphate may be an undesired impurity.
What happens when you put zinc phosphate in a bath?
When depositing zinc phosphate or manganese phosphate the additional iron phosphate may be an undesired impurity. The bath often includes an oxidizer, such as sodium nitrite, to consume the hydrogen gas — which otherwise would form a layer of tiny bubbles over the surface, slowing down the reaction.
What is the process of phosphate bath?
Process. The process takes advantage of the low solubility of phosphates at medium or high pH. The bath is a solution of phosphoric acid, containing the desired iron, zinc or manganese cations and other additives. The acid reacts with the iron metal producing hydrogen and iron cations: Fe + 2 H.
What is the best coating for phosphate?
The performance of a phosphate coating depends on its crystal structure as well as its thickness. A microcrystalline structure is usually best for corrosion resistance or subsequent painting. A coarse grain structure impregnated with oil may be best for wear resistance. These factors can be controlled by varying the bath concentration, composition, temperature, and time.
Why does iron phosphate rust?
Your phosphate can be OK and still rust after a few hours because Iron Phosphate coating is not intended to protect the metal without subsequent paint coating. Enough that the humidity in your plant a little bit high, then you will have rust on your Iron Phosphate Coating. My suggestions are as following:
What temperature to use iron phosphate?
Q. We use a "room temperature" iron phosphate product at low concentration for powder coating pre-treatment. We vary the temperature [up to 120 °F] and conveyor line speed [impingement] depending on cleanliness and type of steel. Our customers only require minimal salt spray adhesion. Parts are mostly water-break free. We are seeing some flash rust streaking post dry-off oven. I used a "rust preventative" in the final tank rinse many years ago. The chemical was dyed yellow green and could be seen in the tank. The 1000 gallon tank was dumped and recharged every day. No flash rust. Is such a chemical still available?
Can you use acidic final seal rinse on flash rust?
Acidic final seal rinses are also adequate for some flash rust protection, but are normally less economical to use than the amine based products. I would suggest however, that you make sure the Iron Phosphate solution you are currently using is within it's recommended parameters (pH, temperature, concentration and time) so as to insure a uniform and complete conversion coating on the part surface.
Is phosphatizing better than iron phosphating?
But zinc phosphating or ideally manganese phosphating, would be much better for this than iron phosphating.
Can you leave iron phosphate unpainted?
a. Don't leave the parts unpainted for a long time; plan your work that the paint will be applied immediately after Iron Phosphating .
Can iron phosphate be used on steel?
A. Hello. When using iron phosphate (say 3-in-1, i. e., degreasing, derusting and phosphating), the treated component should be dried, then wiped with a dry cloth, and painted as soon as possible. If left unpainted the component could in the course of hours start getting rusted. Another process called zinc phosphate applied to mild steel components in a seven tank process could help in keeping the components rust free for days without painting. Further details can be furnished.
Should you buy iron phosphate?
You should be buying the iron phosphate from a company that can aid you in your process. The sealer neutralizes the action of iron phosphate.
Does phosphatization rust?
A. Hi Senthil. It's not unusual for phosphatization to rust " some hours" after processing. It depends both on the environment (are they left in a plating shop which uses HCl?) and on the rust preventative compound which they were dipped in. Please tell us something about the parts, the phosphating process, the post-treatment, and the storage conditions for these "some hours". Thanks!
Is zinc phosphate corrosion resistant?
A. Hi Kaushal. We added your inquiry to a thread on the subject where some suggestions are offered. Zinc phosphate is a "pretreatment" for paint or oil, it is not a corrosion resistant finish, but a dip in an appropriate rust preventative oil may give you sufficient life. Good luck.
Is zinc phosphate water soluble?
But, yes, surely they are water-soluble waxes, and dry to the touch oil s that could work. Best of luck.
When you add arbitrary and wrong testing requirements, what happens?
When you add arbitrary and wrong testing requirements, people stop optimizing the coating for the job it's supposed to do, and start optimizing it for the job it's NOT supposed to do, at the expense of de-tuning it for it's rightful job. Your question about increasing the thickness above the correct specification, to try to pass this test, is a good example :-)
Can you run out of accelerator for zinc phosphate?
A. Depending on your bath che mistry you may be running out of accelerator. If your Zinc Phosphate appears OK but rusts when drying you should check your free/total acid ratio. Be sure to limit drying of parts between phosphate and rinse.