
Manufacturing process of calcium silicate bricks:
- Within the first stage, an appropriate ratio of sand, lime, and pigment is mixed well with 3 to 5% water; the paste is obtained with a moldable density.
- The mixture is moulded into bricks using a rotary tablet that uses the mechanical pressure to pressurize the bricks.
- The pressing pressure varies from 31.5 to 63 N / mm2.
How do you make calcium silicate bricks?
Calcium silicate (sand lime and flint lime) bricks are manufactured by mixing lime, sand and/or crushed silicaceous or flint stone together, with enough water to allow the mixture to be moulded under high pressure. The bricks are then steam autoclaved so that the lime reacts with the silica to form hydrated calcium silicates.
What is calcium silicate made of?
Calcium silicate units are manufactured from fine siliceous aggregate (and sometimes silica flour) and 10–20% ground quicklime or well hydrated lime. Inert pigments may be included to influence the final brick colour. The units are shaped into moulds under pressure and cured by autoclaving at around 170°C for between 4 and 16 hours.
What is calcium Hypo silicate brick?
The amount of calcium within the compound such as silica content and lime crystals in the sand is called calcium hypo silicate, this process is carried out for 6 to 12 hours. Finally, the bricks obtained are transported to the site. The mortar required to provide plaster on calcium silicate bricks is very low.
What is the difference between calcium silicate and mortar bricks?
Calcium silicate bricks have a propensity for all colour variants to darken quite noticeably when wet. The wetter bricks below DPC level and just above dpc level (where the dpc has been bridged) is noticeably darker. Mortar considerably harder than the masonry units.
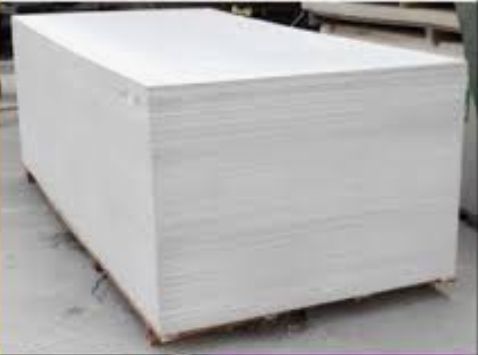
How are calcium silicate bricks made?
Calcium Silicate Masonry / Brick is manufactured by mixing high calcium lime with a very fine siliceous aggregate, & water, which is then moulded at high pressure, followed by high-pressure steam curing.
What do you mean by calcium silicate bricks?
Calcium silicate (sand lime and flint lime) bricks are manufactured by mixing lime, sand and/or crushed silicaceous or flint stone together, with enough water to allow the mixture to be moulded under high pressure.
How do you make lime bricks?
Insert nine parts of sand into the mixing bucket.Insert one part of lime into the mixing bucket. ... Stir the ingredients until they are evenly mixed.Pour the mixture into the brick mold.Press the mixture, using a hard surface to increase pressure. ... Expose the mixture to air.More items...
Where are calcium silicate bricks used?
Calcium silicate bricks are made of sand and lime and popularly known as sand lime bricks. These bricks are used for several purposes in construction industries such as ornamental works in buildings, masonry works etc. Sand lime bricks are popularly used in European countries, Australia and African countries.
What is the strongest brick?
Class A engineering bricks are the strongest, but Class B are the more commonly used. Engineering bricks vary in colour from red to blue.
What temperature is needed for calcium silicate bricks?
In fact, the baking curve of this brick is at a temperature of 1420 to 1480 degrees Celsius, and the linear expansion during baking is equal to 4-5%. In industrial and factory conditions, this brick withstands temperatures up to 1700 degrees Celsius, which is due to the presence of liquid phase in its main ingredients.
Can you make bricks out of any soil?
All soils contain sand, clay and some organic matter. The best soils for mud bricks would be those classed as 'clays', 'clay loams', 'silty clay loams', or 'silty clays'. A 'sandy clay loam' would require additional clay or organic matter added (e.g. straw) to make an effective brick mixture.
Can you make your own bricks?
The easiest to make are sun-dried adobe bricks. Whether you use naturally-occurring clay or buy clay from a distributor, it is always recommendable to test your clay recipe. Clay for bricks usually contains soil mixed with plastic clay and sand. You can form bricks manually using molds, or with mechanical presses.
How do you make cement bricks?
0:000:41How to Make Bricks from Concrete - YouTubeYouTubeStart of suggested clipEnd of suggested clipTo make bricks from concrete form a mold for the bricks using strips of plywood and lumber. Once youMoreTo make bricks from concrete form a mold for the bricks using strips of plywood and lumber. Once you've built the mold spray form release oil on the inside so the concrete doesn't stick to the wood.
How are bricks made?
Essentially, brick are produced by mixing ground clay with water, forming the clay into the desired shape, and drying and firing. In ancient times, all molding was performed by hand.
Is calcium silicate vegan?
Calcium Silicate is vegan.
Can calcium silicate board get wet?
2, excellent waterproof performance: calcium silicate board has excellent waterproof performance, in the bathroom, bathroom and other places of high humidity, can still maintain the performance of stability, will not expand or deformation.
What is calcium silicate used for?
Calcium silicate is used as an anticaking agent in food preparation, including table salt and as an antacid. It is approved by the United Nations' FAO and WHO bodies as a safe food additive in a large variety of products.
Do bricks contain calcium?
Fly ash clay bricks are manufactured with clay and fly ash—a byproduct of coal burning—fired at about 1,832°F. This type of brick is sometimes described as self-cementing, since it contains a high volume of calcium oxide and therefore expands when exposed to moisture.
What is calcium silicate insulation?
Calcium silicate (CalSil) insulation is a high-temperature, high-strength thermal insulation characterized by its crystalline formation. This crystalline structure is what gives calcium silicate its insulating properties.
What is calcium silicate ceiling?
Calcium Silicate Ceiling is also called as calcium silicate false ceiling or calcium silicate ceiling board, which is classified as fiber cement reinforced calcium silicate products made up of portland cement, fine silica, special cellulose fibers and selected fillers to offers amazing features in impact resistance, ...
What is calcium silicate brick made of?
Join now! Calcium silicate bricks are made of sand and lime and popularly known as sand lime bricks. These bricks are used for several purposes in construction industries such as ornamental works in buildings, masonry works etc. Sand lime bricks are popularly used in European countries, Australia and African countries.
What is the sand content of calcium silicate bricks?
Calcium silicate bricks contains high amount of sand is about 88 – 92%. It means the properties of these bricks depends upon the characteristics of sand used. So, the sand used shall be well graded and should not contain any impurities like organic matter, soluble slats etc. the finely divided clay may be present but it is up to 4% only which helps the brick in pressing and provides smoother texture.
How to make bricks from sand?
In the first step, suitable proportions of sand, lime and pigment are taken and mixed thoroughly with 3 to 5 % of water. Then paste with moldable density obtains . The mixture is molded into bricks using rotary table press which uses mechanical pressure to press the bricks. The pressure of pressing varies from 31.5 to 63 N/mm 2 . In the final stage, bricks are placed in autoclave. Autoclave is nothing but a steel cylinder with tightly sealed ends. The diameter of autoclave is bout 2m and length is about 20m. After placing bricks in this closed chamber saturated steam pressure is released which is about 0.85 to 1.6 N/mm 2. The temperature inside the chamber is raised and the reaction process begins. Silica content in sand and calcium content in lime reacts and forms crystal like compound called calcium hypo silicate. This process is done for 6 to 12 hours. Finally, the obtained bricks are transported to work place.
How long does it take for a lime to react with calcium?
Silica content in sand and calcium content in lime reacts and forms crystal like compound called calcium hypo silicate. This process is done for 6 to 12 hours. Finally, the obtained bricks are transported to work place.
Why use sand lime brick?
Sand lime bricks provides more comfort and accessibility for architects to attain desired shape and designs.
Why can thickness of walls be reduced when constructed using these bricks?
iii. Thickness of wall can be reduced when constructed using these bricks because of high compressive strength.
Which is more economical, clay or silicate?
If clay is available in plenty, clay bricks are more economical than calcium silicate bricks.
How to make calcium silicate bricks?
To make calcium silicate bricks, silica sand is mixed with high calcium lime at a sand–lime ratio of 10 or 20. The mix is then compressed into moulds and “autoclaved” at about 170°C (340°F) for several hours. Some gel, similar to the calcium silicate hydrate gel of the type that is formed by cement, is formed, and this bonds the sand particles together. The main properties of these bricks are:
How is calcium silicate made?
Calcium silicate units are manufactured from fine siliceous aggregate (and sometimes silica flour) and 10–20% ground quicklime or well hydrated lime. Inert pigments may be included to influence the final brick colour. The units are shaped into moulds under pressure and cured by autoclaving at around 170°C for between 4 and 16 hours. During curing some of the lime reacts with the siliceous aggregate to form calcium silicate hydrate, which binds the brick together.
What is the appearance of calcium silicate brick?
Old bricks tend to be partially or fully carbonated with the binder including, or composed of, finely crystalline calcium carbonate. Calcium silicate bricks typically appear fully compacted with no large entrapped air voids present. The appearance of a sandlime brick is illustrated in Figures 246–248, and a flintlime brick is illustrated in Figures 249–251. Both of these examples are old calcium silicate bricks that are fully carbonated.
What are the two types of crystalline modifications of calcium silicate?
Stoichiometric calcium silicate (CaSiO3) has two crystalline modifications: wollastonite (sometimes called wollastonite I or β -CaSiO 3) and pseudo-wollastonite (also called α -CaSiO 3 ). Wollastonite is low-temperature modification exhibiting triclinic structure with a space group of αP 30 while pseudo-wollastonite exhibits monoclinic structure with a space group of C2 / c ( Schmetterer and Masset, 2012 ). Dicalcium silicate (Ca 2 SiO 4) has four different modifications: γ -phase, stable at room temperature, α ′- and α -phases, stable at high temperature and β -phase which is not thermodynamically stable (Schmetterer and Masset). Tricalcium silicate (Ca 3 SiO 5) is a phase stable between 1250 and 1900°C. At or above 1900°C the phase will dissociate into the CaO and Ca 2 SiO 4 ( Welch and Gutt, 1959 ).
What is the name of the sand that binds bricks together?
During curing some of the lime reacts with the siliceous aggregate to form calcium silicate hydrate, which binds the brick together. The term ‘sandlime ’ is used to describe calcium silicate bricks in which only natural quartz sand comprises the siliceous portion of the raw ingredients.
How to make C-S-H?
C-S-H were synthesized by mixing appropriate amounts of SiO 2 (A erogel, A380) and Ca (OH) 2 in pure water (liquid-solid ratio was 5 mL/g) to give a Ca/Si mole ratio of 1.0 and 1.5. The slurries were sealed in polyethylene bottles and stirred continuously using a hot plate at 60 °C. After one week, the gel of C-S-H was separated by filtration using a membrane filter with a pore size of 0.45 μm. After drying under a vacuum, we determined that C-S-H were sufficiently prepared by XRD.
What are the bioactive materials used in bone regeneration?
Ca-Si based bioactive materials can be divided into four groups: bioactive glass, bioactive ceramics, glass-ceramics and cements. The beneficial effects of Ca-Si based materials on inducing bone formation were first found on glass in the system of SiO 2 -CaO-Na 2 O-P 2 O 5 by Hench et al. in the early 1970s ( Hench et al., 1971 ). Glasses with this composition were able to bond to soft and hard tissues forming a carbonated HAp layer when exposed to biological fluid ( Hench 1991 ); hence, it was named bioglass. A number of different types of bioactive glasses have been developed and some have been used in clinic such as 45S5 Bioglass®. Crystallographically, glass is composed of amorphous phase while ceramic consists of crystalline phase. Glass can be partially recrystallized by heat treatment and form glass-ceramics.
What is arriscraft stone?
As a manufactured product, Arriscraft Building Stone is designed for installation using standard masonry techniques, regardless of the stone style. However, while some Building Stone styles require that a bond pattern be followed, Arriscraft has introduced new options designed for more rapid installation.
How many building stone styles does Arriscraft have?
Currently, Arriscraft offers 10 Building Stone styles, in addition to Renaissance® Masonry Units and a series of Thin-Clad products.
Where is arriscraft manufactured?
Arriscraft in Ontario, Canada, has manufactured calcium silicate building stone for over 60 years. This type of manufactured stone is distinct from both clay bricks and concrete masonry products.
Can arriscraft stone be used on old buildings?
Because calcium silicate masonry units have an authentic, natural grain appearance, they are also a top candidate for use on historical projects, either for repairs and renovations or for new structures being integrated with old buildings . With the added advantage of color matching, Arriscraft Building Stone can come incredibly close to a perfect match.
Is calcium silicate stone natural?
Although this manufacturing process has changed very little over the decades, the demand for this naturally based, calcium silicate stone continues to grow. These “green” units are entirely natural except for the pigments that are added as the raw materials combine. This mixing creates masonry units with through-body color, so stones can be cut, shaped, hand-chiseled or dressed on-site while maintaining the fine-grained texture and color.
What is calcium silicate?
Calcium silicate is a white free-flowing powder. It can be derived from naturally occurring limestone and diatomaceous earth, a siliceous sedimentary rock. It is one of a group of compounds that can be produced by reacting calcium oxide and silica in various ratios e.g. 3CaO·SiO 2, Ca 3 SiO 5; 2CaO·SiO 2, Ca 2 SiO 4; 3CaO·2SiO 2, Ca 3 Si 2 O 7 and CaO·SiO 2, CaSiO 3. It has a low bulk density and high physical water absorption.
What is the chemical name for calcium silicate?
Calcium silicate is the chemical compound Ca 2 SiO 4 , also known as calcium orthosilicate and is sometimes formulated as 2CaO·SiO 2. It is also referred to by the shortened trade name Cal-Sil or Calsil. It occurs naturally as the mineral larnite .
What is the best material for fireproofing electrical circuits?
It is used in passive fire protection and fireproofing as calcium silicate brick or in roof tiles. It is one of the most successful materials in fireproofing in ...
What is monosilicic acid?
Monosilicic acid remains in the bulk solution to play other important roles in correcting the adverse effects of acidic conditions. As opposed to limestone (a popular remediation material), calcium silicate effectively precipitates heavy metals and does not armor over, prolonging its effectiveness in AMD systems.
What is sodium silicate used for?
It is used as a sealant in roads or on the shells of fresh eggs: when sodium silicate is applied as a sealant to cured concrete or egg shells, it chemically reacts with calcium hydroxide or calcium carbonate to form calcium silicate hydrate, sealing micropores with a relatively impermeable material.
What is the fire classification of calcium silicate board?
While the best possible reaction to fire classifications are A1 (construction applications) and A1Fl (flooring applications) respectively, both of which mean "non-combustible" according to EN 13501-1: 2007, as classified by a notified laboratory in Europe, some calcium-silicate boards only come with fire classification of A2 (limited combustibility) or even lower classifications (or no classification), if they are tested at all.
Why use silicone sheets?
For sub-standard products, silicone -treated sheets are available to fabricators to mitigate potential harm from high humidity or general presence of water. Fabricators and installers of calcium silicate in passive fire protection often also install firestops.
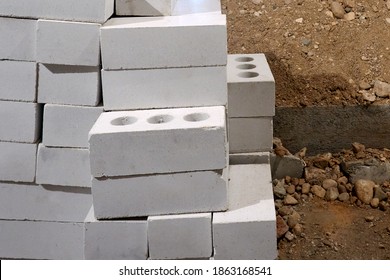