
Impurities are removed from bauxite by leaching a bauxite ore using a leach solution to dissolve impurities from the bauxite ore and form a pregnant leach solution containing the impurities in...
What are the impurities of bauxite?
Bauxite deposits invariably contain a range of impurities, ranging from organic material to trace elements such as Ga, Zn, Pb, P and Be. Table 2.1 shows typical compositions of a range of smelter aluminas.
How is bauxite purified by Bayer process?
The bauxite is purified by Bayer process. first the ore is mixed with hot concentrated solution of sodium hydroxide. the NaOH will dissolve the oxides of aluminium and silicon but not other impurities such as iron oxide which remain unsoluble. the unsoluble materials are removed by filtration. How is silica removed from bauxite?
What liquid is added to the bauxite in the size reduction process?
In the embodiment illustrated in Figure 2, the purified regenerated leach solution 62 is used as the liquid which is added to the bauxite in the size reduction process 12.
What is the washing process of bauxite?
As part of the beneficiation process, the bauxite may be subjected to washing with water. This washing process leads to the removal of water-soluble impurities from the bauxite and removal of impurities which are bound loosely to the bauxite and are thus readily liberated from the surface of the bauxite.
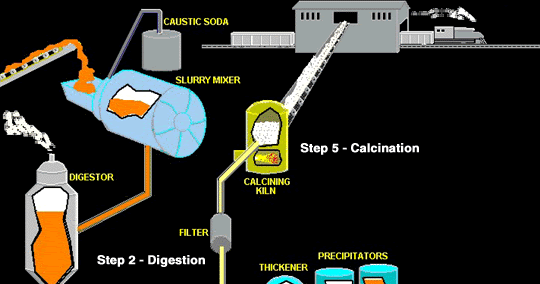
How is bauxite purification done?
The bauxite is purified by the Bayer Process. First the ore is mixed with a hot concentrated solution of sodium hydroxide. The NaOH will dissolve the oxides of aluminum and silicon but not other impurities such as iron oxides, which remains insoluble. The insoluble materials are removed by filtration.
How bauxite ore is purified?
Bauxite, the ore of aluminium, is purified by either Hall's process or Baeyer's process or Serperck's process. Mond's process is used for refining nickel. Liquation process is used for refining Bi, Sn, Pb and Hg.
Which compound is used to remove impurities from bauxite?
aqueous sodium hydroxideIn the Bayer process, bauxite is typically crushed, washed, dried and ground before being treated with aqueous sodium hydroxide at an elevated temperature. The sodium hydroxide dissolves the alumina to form a solution from which insoluble impurities (“red muds”) are removed.
What is the process of removing impurities?
The osmosis is the process of movement of a solute from the region of its higher concentration to a region of lower concentration through a semipermeable membrane. The dialysis is the process of removal of dissolved impurities from the colloidal system by means of diffusion through a suitable membrane.
How is alumina extracted and purified from bauxite?
Extracting aluminium The bauxite is purified to yield a white powder – aluminium oxide (also known as alumina) – from which aluminium can be extracted. The extraction is done by electrolysis , but first the aluminium oxide must be melted so that electricity can pass through it.
Which is the process used for purification of bauxite are containing silicate as impurity?
Baeyer's process is used for the purification of bauxite containing as chief impurity .
What are bauxite impurities?
The major impurities in Bauxite are iron oxides (goethite & hematite), silicon dioxide, the clay mineral kaolinite as well as small amounts of anatase (TiO2). Consequently, its composition varies considerably with alumina constituting from about 50% to about 70%.
Which of the following is used to remove impurities?
Decantation is the process used to remove impurities from dispersion medium in Ultracentrifugation.
Which method is used to concentrate bauxite?
The Bayer process is the principal industrial means of refining bauxite to produce alumina (aluminium oxide) and was developed by Carl Josef Bayer.
How are impurities from the ore removed?
∗ Hydraulic Washing: This technique concentrates the ore by going it through an upward stream of water whereby all the lighter particles of impurities are isolated or separated from the heavier metal ore.
Which method is used to remove impurities from water?
In distillation, there is a change of state from liquid to gas and then again to liquid. Reverse osmosis can also be used as one way to remove the impurities but the most effective way is distillation. Some impurities are insoluble; they are removed by the process of filtration and sedimentation.
How do you remove impurities from metals?
These methods include:Distillation, which involves vaporizing the metal and then allowing it to solidify outside of the impurities.Liquation, which involves melting the metal, and allowing it to run out of the solid impurities.Poling uses a green log of wood to reduce oxidized metals.More items...•
What are the impurities in a bauxite smelter?
Bauxite deposits invariably contain a range of impurities, ranging from organic material to trace elements such as Ga, Zn, Pb, P and Be. Table 2.1 shows typical compositions of a range of smelter aluminas. In the Bayer process, many impurities are at least partially soluble in the caustic digestion liquor and may be carried over into precipitation if they are not removed in the desilication product. The addition of lime is widely used to control some of these impurities, particularly phosphorus, by precipitation as their calcium salts. Certain impurities are of concern to the smelter, especially if high-purity grades of metal are being produced. Bath accumulation is also observed for some elements, calcium, phosphorus and occasionally beryllium being of ongoing interest. Phosphorus has been associated with losses in current efficiency ( Haugland et al., 2001 ). Sturm and Wedde (1998) suggest a one per cent reduction in current efficiency in the reduction cell, per 100 ppm increase of P 2 O 5 in the electrolyte. Surveys of aluminium smelter perceptions of alumina quality inevitably rank impurity content, along with particle size distribution, as of particular importance ( Chandrashakar et al. 2005 ).
What are some examples of electrolytes that deposit aluminum?
32 Another example is the Real process that works with an electrolyte of aluminum chloride and aluminum hydride in tetrahydrofuran. A third example is the Natal process which deposits aluminum from an electrolyte of aluminum chloride and aluminum hydride in toluene.
What is the raw material of aluminium?
The raw material for aluminium and alumina is bauxite (named after Les Baux-en-Provence in France), a mixture of the oxide hydrates and clays (aluminosilicates) with impurity oxides such as SiO 2 and TiO 2 and small amounts (ppm) of the strategic compound Ga 2 O 3 and iron oxides that occur as a weathering product of low iron and silica bedrock in tropical climatic conditions. The most common mineral constituent of bauxite is gibbsite. A description of bauxite mineralogy can be found in a number of textbooks (e.g., Wells, 1984 ), and summaries are found in several revisions ( Doremus, 1984 ). Evolution of gibbsite with temperature has been recently studied by neutron thermodiffractometry ( Rivas Mercury, Pena, de Aza, Sheptyakov, & Turrillas, 2006). Deposits of bauxite exist around the world, the largest bauxite deposits being found in Guinea, Australia, Brazil, and Jamaica.
What is the name of the bacteria that is found in ground mines?
Paenibacillus polymyxa, a neutrophilic, organic-acid producing bacterium, was found to be natively present in ground mine waters and many bauxite deposits. When grown in Bromfield medium containing sucrose, ammonium sulfate, magnesium sulfate, and yeast in the presence of calcium carbonate, they undergo calcium-dependent metabolism utilizing calcium to produce polysaccharides and organic acids. The use of the above mine-isolated bacteria in the removal of iron oxides and calcite from low-grade bauxites was investigated to establish an environmentally benign and cost-effective biobeneficiation process. A column- leaching bioreactor which could be operated either in the fluidized bed mode or in a drain mode (depending on particle size) was designed. As mined ground bauxite ore could be fed to the column reactor as a total recycle slurry. Air vents were provided for efficient aeration. Based on bacterial growth cycles, either “cascade” or “uncascade” operation can be performed. The slurry was drained off to a storage tank after bacterial interaction. The leach liquor after filtration of the leached residues was again pumped back to the reactor, and the leaching cycles repeated 4–5 times in the cascade operation sequence. In the uncascade mode, reinoculation or recycle of the slurry was not performed. Higher calcium removal could be observed when the reactor was operated in the cascade mode because continuous bacterial growth and contacts with mineral particles could be ensured. More than 90% of calcium solubilization could be achieved through the cascade mode of bioleaching [85–88].
What are the interactions between clay and microorganisms?
Interlayers can permit ion exchange. They are the products of rock weathering at low temperatures and neutral pH. Microbe–clay interactions are important for a number of interfacial processes. Microorganisms can solubilize, precipitate, and convert clay minerals changing their physicochemical characteristics. Microbes accelerate clay mineral solubilization through excretion of metabolic products and redox reactions involving iron. Many siderophores may be involved in the weathering of iron oxides and silicates, besides the roles played by organic acids, complexing agents, and extracellular polymeric substances. Selective mineral dissolution could occur often resulting in nonstoichiometric altered clay minerals. A common dissolution product is silica. Microbiological weathering of silicates and basalts can result in the production of different clay minerals such as smectite and zeolite. Poorly crystalline clay minerals can often be observed as cell surface coatings. The primary precipitates on bacterial cell walls can be altered to yield crystalline clay minerals upon aging. Extracellular polymeric substances play significant roles in the biosynthesis of several clay minerals [42].
Is bauxite a fluoride?
The recently patented bauxite-based defluoridation method proposes the use of mildly processed (powdered) bauxite ore as a single-use dispersive batch media in a community-scale system [24]. Bauxite, a globally abundant ore of aluminum, is a viable, effective, and low-cost fluoride adsorbent alternative to AA. Raw bauxite ore is comprised of a primary aluminum oxide mineral known as gibbsite [Al (OH) 3] [25–27] and its material cost ($30/tonne) [28] is 50 × lower than the heavily processed and purified end product, AA ($1500/tonne) [29]. Earlier researchers have reported bauxite’s ability to adsorb fluoride [30–32] but many of them did not explore the specific dose of bauxite needed to remediate high fluoride concentrations in contaminated groundwater down to the WHO MCL (1.5 ppm F −). Bauxite deposits are present worldwide, including in countries with fluoride-contaminated regions (e.g., India, Ghana, Tanzania, and China). In particular, one-third of the affected population at risk of developing fluorosis worldwide (66 million people) [1] live in India, which is also home to the fifth largest bauxite deposit (3037 million tonnes) globally [33].
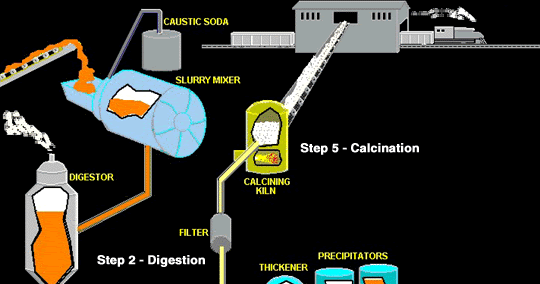