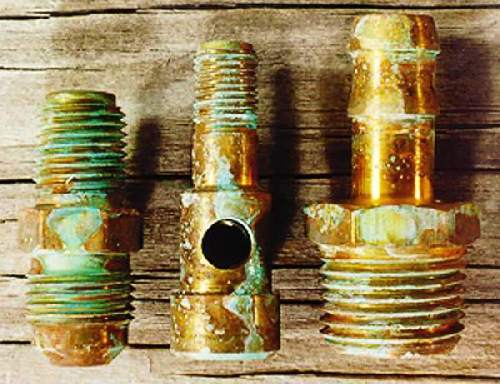
How do you put thread in a sewing machine?
Using a cup
- Put the cone thread in the cup or glass.
- Thread the machine with the cone generally as you would with a thread spool.
- Place the cup anywhere where you find it comfortable, and you have to ensure that the cup or glass does not fall and the cone does not roll ...
- You can start sewing. ...
How do I thread my Machine?
Upper threading
- Turn off the machine.
- Raise the presser foot lever. ...
- Raise the needle by turning the handwheel toward you (counterclockwise) so that the mark on the wheel points up. ...
- Pull up the spool pin completely.
- Put a spool of thread on this pin. ...
How to thread a sewing machine and wind a bobbin?
Winding the Bobbin
- Set the thread on the spool pin and place the spool cap on top. Most machines come with a plastic wheel called a spool cap. ...
- Unwind about 18″ or so of thread and bring it around the backside of the bobbin winder tension disc, wind it around the tension disc one time. ...
- Select a bobbin that works specifically with your machine. ...
What is the best quality thread for sewing?
Top 10 Sewing Thread Reviews
- NEX 60 Piece Sewing Thread Kit. This sewing thread kit doesn’t sit at the top of our picks for no reason. ...
- Candora Sewing Thread Assortment. Being made from polyester, this thread is very much suggested for the projects where you need the tensile strength to be very high.
- Gutermann Multi-Color Thread Set. ...
- Coats XP All Purpose Thread Kit. ...

What do you need to machining an internal thread?
For machining an internal thread, you need twist drill, 90°countersink, internal hand or machine tap, adjustable tap wrench (for hand) or hand drill (for machine), and safety goggles. Before threading, you need to know which tap to choose and what diameter of the hole needs. Internal taps are designated according to nominal size. The diameter or the twist drill for tapping can be calculated using the formula: Core hole diameter = Tap diameter – Thread pitch. In our chart, you can find the standard Metric and English drill bit and tap size for your thread holes.
How to cut threads on a CNC machine?
1. Centering with a punch and then drill a core hole with the twist drill. 2. Use the 90°countersink to countersink into the core hole and make a chamfer. 3. Put the tap into a tap wrench and turn it into the core hole to cut the thread. Internal threads are also available on CNC turning parts, lots of rules of cutting a thread on ...
What is a tap in machining?
In daily life, the nut is a type of typical internal thread. A tap is a metal threading tool used to cut the internal threads on a CNC machining part, thrilling is the process of threading and drilling internal threads using a specialized cutting tool on a CNC mill.
What is the chamfer on a threaded product?
The external thread end of all threaded products should have chamfer. The external thread is cut with a round die which is fixed in a die stock, the round die has three or more cutting edges which are are serrated and represent the nut thread.
What tools do you need to thread a lathe?
If you have a turning lathe, turn the diameter about 0.1 times the pitch smaller than the thread outer diameter. You need the threading tools for external threads are file, round rod, vise for clamping, round die, die stock, flat-tip screwdriver and cutting spray.
How to cut a round rod?
2. Clamp the round die into a die stock and fix it firmly, turn the round die clockwise onto the round rod with sufficient pressure to cut the thread. Make sure to cut straight thread.
What is the profile of a thread?
The profile of the thread is composed of the crest (the top of threads), root (the bottom of threads), and flanks (joining crests and roots). Thread pitch is the distance measured parallel to the thread axis, between corresponding points on adjacent threads.
What is a thread in engineering manufacturing?
A thread is a continuous spiral ridge with a uniform cross section formed on the inner or outer surface of a cylinder or cone. The thread profile consists of a peak, a root and a flank. The thread pitch is the distance between corresponding points of adjacent threads measured parallel to the thread axis. The pitch diameter is the diameter of the theoretical cylinder. When the theoretical cylinder passes through the thread, the distance between the thread crest and the thread root is equal. In an ideal product, these widths are equal to half of the pitch.
What tools do you need for thread machining?
The tools you will need for external thread machining are: a file, a round bar, a vise for clamping, a round die, a die head, a flat head screwdriver, and a cutting spray. 1.
What is a tap thread?
In everyday life, a nut is a typical internal thread. A tap is a metal threading tool used to cut internal threads on CNC machined parts. The thrill is the process of machining and drilling internal threads on a CNC machine using a specialized cutting tool. Products with threads should have a countersunk hole at the end of the internal thread.
How to make a chamfer for internal threads?
1. center the hole with a punch, then drill the core hole with a twist drill. 2. Sink the core hole with a 90° countersink and make a chamfer. 3.
What are the different types of threads?
Types of threads: There are many types of threads, depending on the classification criteria. Machine threads and spacer threads are commonly used in fasteners. unf threads and unc threads are the standard series in the unified thread system. Here we come to the issue of external and Internal Threads.
What are external threads?
Common external threads include screws, bolts, studs or plug gauges. When designing external threads, try not to terminate at a large diameter near or adjacent to the shoulder. The width of this camber depends on the size of the thread, whether the thread is coarse or fine, and the throat angle of the Thread Cutter.
Where should a countersunk hole be on a thread?
Products with threads should have a countersunk hole at the end of the internal thread.
How do threads work?
Thread Rolling. Threads may be applied to a bolt or other cylindrical object by rotating the part between two opposing dies. As pressure is applied to the workpiece by the dies, the part is deformed, and the material is displaced and flowed with the resulting shape being a thread.
What are the different threads?
Regardless of the method used, threads have certain nomenclatures that must be considered when preparing for production. They are: 1 Thread angle 2 Major diameter 3 Minor diameter 4 Pitch diameter 5 Helix angle 6 Lead 7 Pitch
Why are threads rolled?
Threads which are rolled are often tougher due to work hardening than threads that are cut by dies or by a threading insert . Thread rolling also has the advantages of being a must faster production process. Thread rolling is also referred to as a cold-forming process.
What is the most commonly used method for producing or cutting threads?
Another one of the most commonly used methods for producing or cutting threads is with the use of a die. Dies can be used in lathes, screw machines and CNC lathes to produce both internal and external threads by cutting or by rolling.
Why use thread chasers on dies?
When using a die, there are several thread chasers that cut the thread then back away from the work to permit fast removal of the tool. Each set of thread chasers is designed to cut a different thread. One set of chasers would be used at a time, but each, in turn, to ensure that the new threads are cut to the tolerance depth.
How many degrees to turn a thread?
Therefore, in manual thread cutting, normal wrench usage is to cut the threads 1/2 to 2/3 of a turn (180 to 240 degree rotation), then reverse the tap for about 1/6 of a turn (60 degrees) until the chips are broken by the back edges of the cutters.
What is rolled thread?
Threads of metal fasteners are usually created on a thread rolling machine. They may also be cut with a lathe, tap or die. Rolled threads are stronger than cut threads, with increases of 10% to 20% in tensile strength and possibly more in fatigue resistance and wear resistance.
What is the difference between indexable and solid thread milling tools?
The tooling used for thread milling can be solid or indexable. For internal threads, solid cutters are generally limited to holes larger than 6 mm (0.24 in), and indexable internal thread cutting tools are limited to holes larger than 12 mm (0.47 in). The advantage is that when the insert wears out it is easily and more cost effectively replaced. The disadvantage is the cycle time is generally longer than solid tools. Note that solid multiple-form thread cutting tools look similar to taps, but they differ in that the cutting tool does not have a backtaper and there is not a lead-in chamfer. This lack of a lead-in chamfer allows the threads to be formed within one pitch length of the bottom of a blind hole.
Why do you thread lapping?
Rarely, thread cutting or grinding (usually the latter) will be followed by thread lapping in order to achieve the highest precision and surface finish achievable. This is a toolroom practice when the highest precision is required, rarely employed except for the leadscrews or ballscrews of high-end machine tools.
What is the difference between tapping and milling?
One main advantage against tapping, is that tapping only starts making a complete thread profile on the third thread, whereas thread milling will produce a complete thread profile from the top to the bottom.
When to use thread cutting?
Thread cutting, as compared to thread forming and rolling, is used when full thread depth is required, when the quantity is small, when the blank is not very accurate, when threading up to a shoulder is required, when threading a tapered thread, or when the material is brittle.
Which is better, tapping or thread milling?
Thread Milling has a better thread quality than tapping as it offers better chip evacuation. Tapping uses a tool the same size as the thread, forcing the chip through the thread for evacuation.
What are the 3 methods of thread machining?
There are 3 methods for thread machining by CNC machining center: thread milling, tap machining, and picking machining.
What is thread milling?
Thread milling is the use of thread milling tools for the processing of large-hole threads, as well as the processing of threaded holes of difficult-to-machine materials. It has the following characteristics:
How to choose taps?
Everyone should choose the appropriate tap according to the material to be processed. Compared with the milling cutter and boring cutter, the tap is very sensitive to the processed material. Taps are divided into through-hole taps and blind-hole taps. The leading end of the through-hole tap is long, which is the front chip removal. When the blind hole is processed, the processing depth of the thread cannot be guaranteed. Pay attention to the difference between the two. When using a flexible tapping chuck, note that the diameter of the tap shank and the width of the square should be the same as that of the tapping chuck. The diameter of the shank of the tap for rigid tapping should be the same as the diameter of the spring collet.
What is buckle machining?
The buckle machining method of the CNC machining center is only a temporary emergency method. It is recommended that you use the thread machining method to process the tool to effectively improve the efficiency and quality of thread machining, reduce the processing cost and improve the efficiency of the machining center.
What path does a thread cutter use?
The tool generally uses a 1/2 circle arc path to cut in and out to ensure the thread shape, and the tool radius compensation value should be brought in at this time.
Can you use one tool for a left handed thread?
With the same pitch, no matter whether it is a left-handed thread or a right-handed thread, one tool can be used, which reduces the cost of the tool.
Can you use multiple tool holders for machining?
The tool holder must be accurate and consistent with the position of the tool slot, otherwise multiple tool holders cannot be used for machining, which will cause random snapping.
What are threads used for?
The above threads are used for the following purpose: 1 To join two parts of a machine like nut-bolt and stud. 2 To get mechanical livers for lifting weights, such as chain pulleys, jacks etc. 3 For accuracy in precision instruments like micrometres. 4 In jobs of power transfer. 5 To control or reduce speed.
Which direction do threads go?
These threads are inclined towards the right-hand side. These are tightened in a clockwise movement. These are known as right-hand threads.
What is taper thread?
Taper Threads. Threads cut on around but taper surface is called taper threads. These are sued for shafts like buffing spindles. These threads can be right hand or left hand. The above threads are used for the following purpose: To join two parts of a machine like nut-bolt and stud.
What is the angle of a B.S.W. thread?
In shape, this thread is similar to B.S.W. thread. The angle of this thread is also 55° but the number of thread per inch is more i.e the thickness of threads is less. This makes the grip more strong. Nut bolts having this thread are used where is more vibration.
What is a three start thread?
In the case of a three-start thread, for one complete turn, the thread advances three times as far if it were a single thread. Multi-start threads are used in those cases where fast movement or motion is needed Fountain where they are widely used.
What is the angle of British Association threads?
It is used in small and tiny electrical and mechanical instruments like radio, television, electrical goods, meters and watches. The angle of these threads is 47 1/2°. These can be used for 1/2″ or 6 mm nut bolts.
What is the angle of the American national thread?
IT has been recognised by the American standards institute. It is a “V” shape thread. Its angle is at 60°. ITs roots and crest are flat. The same standard Insititute has invented national fine thread, This thread is thin. IT is used in motor vehicles and aeroplanes etc.
What is the angle of a thread?
When threads are rolled, the angle on the first and last threads may approximate a 45° angle. Exact angles can not be produced due to the displacement of the metal forming the thread.
How many threads are there in a hole?
External threads can usually be produced within 1-1/2 threads from a shoulder and internal threads tapped to within 2-1/2 threads from a hole bottom. The number varies with the pitch of the thread and by the machinability of the material.
When a mating part must be seated against a shoulder or hole bottom, should a thread relief be?
When a mating part must be seated against a shoulder or hole bottom, a thread relief (recess or undercut) should be shown on the part. This provides clearance for the threading tools. This is shown in Figures 3 and 4.
Can a thread be made up to a shoulder?
How close to the shoulder or bottom can a full thread be produced? This depends on the size and pitch of the thread and the material threaded.
How does a thread ring work?
A thread ring works on the exact same principle, just in reverse. The rings are manufactured in a set, where the Go ring is machined to a slightly smaller size than the nominal and the No-Go ring is machined to a slightly larger size than the nominal.
What are the two types of threads?
It is important to first understand the two basic types of threaded components out there: Internal threads. External threads. In general, if you are joining two parts via threading, there are going to be two types of threads. The first is the male end which will of course screw into the female end.
What does it mean when a thread plug does not go in?
To inspect an internal thread, both ends of the thread plug are inserted into the threaded component. The Go end of the plug is supposed to thread in; the No-Go end is not. If this test checks out, the part can pass inspection. However, if the Go end does not go in, it can be deduced that the threaded component was machined too small. Subsequently, if the No-Go end does thread into the part, the threaded component was machined too large.
How to fit a bolt and nut together?
Obviously, in order for that nut and bolt to fit together they must be machined to the exact same size. The problem is this is much more complex than just drilling a hole and making sure a rod is small enough to go through it. The overall diameter of the external threads must match the smallest diameter of the internal threads, the quantity of threads in a given length must match, the pitch of the threads must match, and the list goes on and on and on (we will get into a discussion of thread attributes in a later post).
What is thread gage inspection?
All thread gages are classified as an attribute gage, meaning they do not provide feedback on what the exact size of the dimension is. This is in stark contrast to a quantitative measurement that, say, a caliper would give in which it reads out the exact dimension you are measuring.
What is a thread ring?
nuts). Thread Rings. Thread rings are, of course the exact opposite of that. They are the rings that contain internal thread on them and are used for checking external threaded components (i.e. bolts).
How many ends does a thread plug have?
A common thread plug assembly (more on this later) will contain a handle with two ends, one on either side. To inspect an internal thread, both ends of the thread plug are inserted into the threaded component. The Go end of the plug is supposed to thread in; the No-Go end is not.
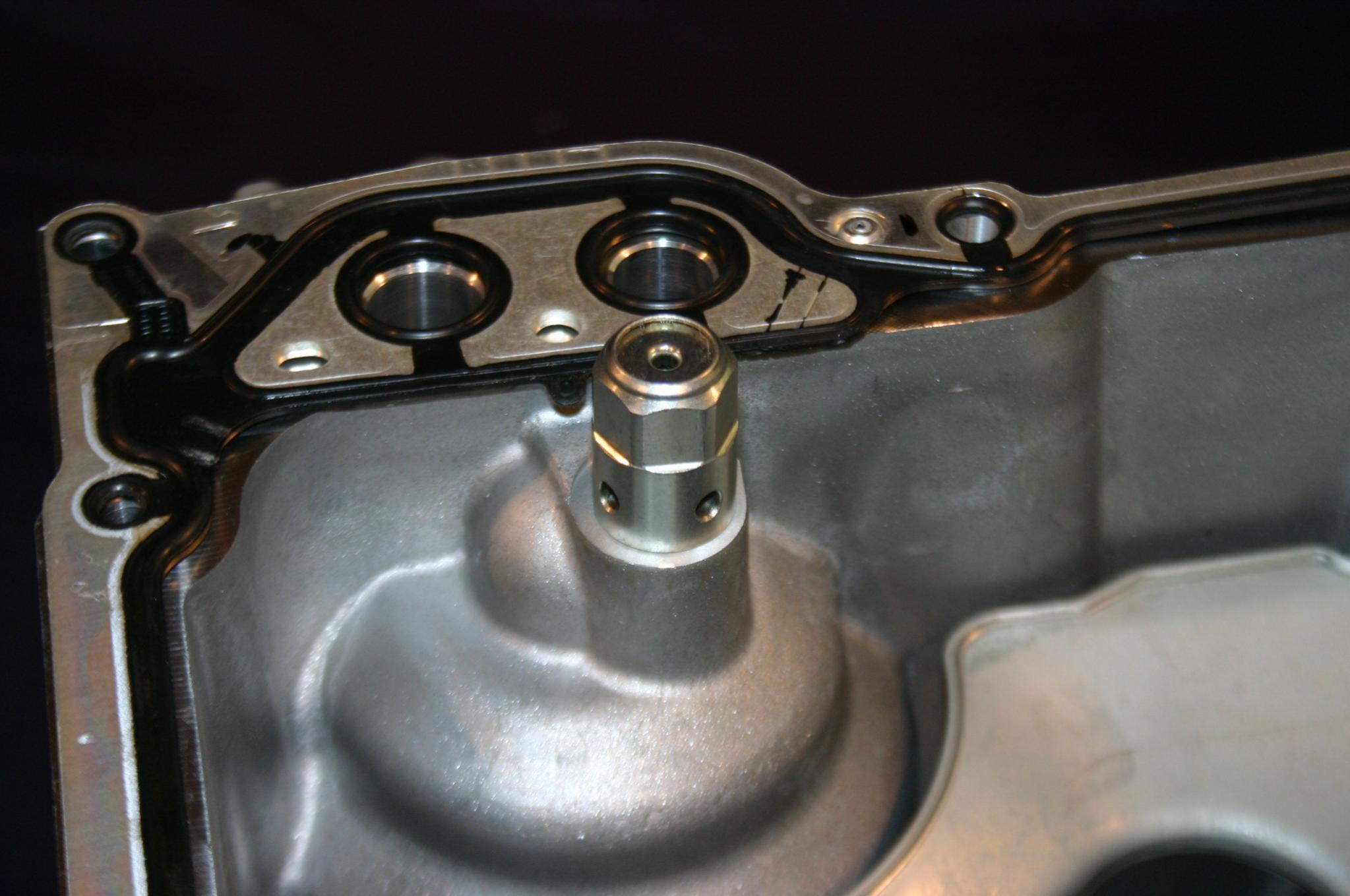
Overview
Subtractive methods
Thread cutting, as compared to thread forming and rolling, is used when full thread depth is required, when the quantity is small, when the blank is not very accurate, when threading up to a shoulder is required, when threading a tapered thread, or when the material is brittle.
A common method of threading is cutting with taps and dies. Unlike drill bits, h…
Overview of methods (comparison, selection, etc.)
There are various methods for generating screw threads. The method for any one application is chosen based on constraints—time, money, degree of precision needed (or not needed), what equipment is already available, what equipment purchases could be justified based on resulting unit price of the threaded part (which depends on how many parts are planned), etc.
In general, certain thread-generating processes tend to fall along certain portions of the spectru…
Deformative or transformative methods
Thread forming and thread rolling are processes for forming, rather than cutting, screw threads, with the former referring to creating internal threads and the latter external threads. In both of these processes threads are formed into a blank by pressing a shaped tool, commonly called a 'thread rolling die' against the blank, in a process similar to knurling. These processes are used for large …
Additive methods
Many, perhaps most, threaded parts have potential to be generated via additive manufacturing (3D printing), of which there are many variants, including fused deposition modeling, selective laser sintering, direct metal laser sintering, selective laser melting, electron beam melting, layered object manufacturing, and stereolithography. For most additive technologies, it has not been long since they emerged from the laboratory end of their historical development, but further commercializat…
Combinations of subtractive, additive, deformative, or transformative methods
Often subtractive, additive, deformative, or transformative methods are combined in whatever ways are advantageous. Such multidisciplinary manufacturing falls under classifications including rapid prototyping, desktop manufacturing, direct manufacturing, direct digital manufacturing, digital fabrication, instant manufacturing, or on-demand manufacturing.
Inspection
Inspection of the finished screw threads can be achieved in various ways, with the expense of the method tailored to the requirements of the product application. Shop-floor inspection of a thread is often as simple as running a nut onto it (for male threads) or a bolt into it (for female threads). This is plenty good enough for many applications (e.g., MRO or hobbyist work), although it is not good enough for most commercial manufacturing. Higher-precision methods are discussed bel…
History
Each method of thread generation has its own detailed history. Therefore, a comprehensive discussion is beyond the scope of this article; but much historical information is available in related articles, including:
• Screw > History
• Screw-cutting lathe > History