/sleeve_puller-56a73bbf5f9b58b7d0e811c8.jpg)
Compression fittings work by the compression of an ‘olive’ between two tapered surfaces and the pipe itself. The two surfaces are the body of the fitting (be it a valve, connector or any other type) and the nut. Using a spanner and a pair of grips the nut is tightened.
Full Answer
How tight do you make a compresion Fitti?
A lot depends on the friction of the fittings. I don't bother counting how many turns, because each one is different. Really you should only tighten a compression fitting about 1.25 turns, but I like to do turns in small increments and check for leaks after each turn.
What do you need to know about compression fittings?
The Basics of Compression Fittings
- Introduction to Compression Fittings. Compression fittings are one of the most common and versatile methods of connecting metal or hard plastic tubing.
- Ferrules. ...
- Tubing. ...
- Installation. ...
- Application Considerations. ...
- Conclusion. ...
Are compression fittings reliable?
How reliable are compression fittings? Compression fittings are more reliable than threaded fittings. They are easier and faster to install than soldering. And they are safer because no torch is needed. However, compression fittings can be prone to issues from vibration and repeated bending.
What is the proper way to do a compression test?
Part 2 Part 2 of 3: Performing the Test
- Put the compression test adapter into the engine's first cylinder. Look down on the engine to figure out which cylinder is closest to the front of the engine.
- Connect the compression gauge to the opposite end of the hose. ...
- Crank the engine at least 4 times to complete the test. ...
- Move the compression gauge to repeat the test on the other cylinders. ...
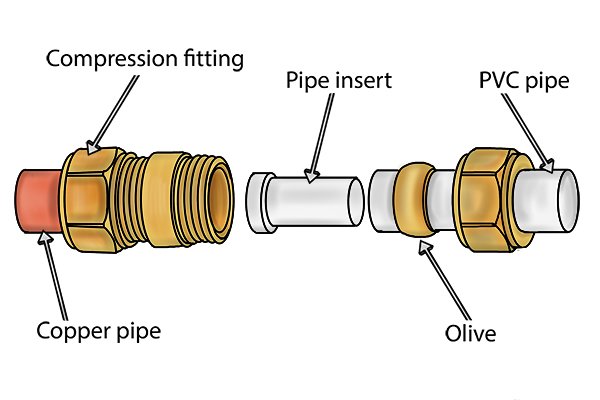
How do pipe compression fittings work?
Compression fittings work by the compression of an 'olive' between two tapered surfaces and the pipe itself. The two surfaces are the body of the fitting (be it a valve, connector or any other type) and the nut. Using a spanner and a pair of grips the nut is tightened.
Are compression fittings reliable?
The answer is very simple; compression fittings are extremely reliable! These fittings are a safe choice because they are leakproof and can be used in many types of high-pressure situations.
What are the disadvantages of using compression fittings?
Disadvantages: Compression fittings are bulkier and can be considered less aesthetically pleasing compared to the soldered joint. Compression fittings are not nearly as robust as soldered fittings making them much more sensitive to powerful stresses.
How well do compression fittings work?
0:556:10How compression fittings work - YouTubeYouTubeStart of suggested clipEnd of suggested clipOnce you tighten the actual compression knots up it actually squeezes out olive so the olive gripsMoreOnce you tighten the actual compression knots up it actually squeezes out olive so the olive grips the pipe. And it also is forced into the fitting. Creating a watertight seal.
Do professional plumbers use compression fittings?
Compression fittings are required in both plumbing and electrical conduit systems to join pipework or tubing together. They are also used in toilet stop valves and hot and cold water taps in domestic and industrial settings.
Will compression fittings leak over time?
They are often used to connect fixtures and appliances that will eventually need to be replaced. While compression fittings are convenient, they may leak if not installed correctly. If a leak does develop, there are steps you can take to fix it.
Should you use Teflon tape on a compression fitting?
Also, do not use too much Teflon tape as this could be counterproductive and prevent the joint from sealing properly and/or causing the tape to gum up. DO NOT use Teflon tape under the compression nut or on flare threads of brass compression fittings (or a compression fitting of any other material)!
Why do compression fittings fail?
Unlike threaded fittings, compression fittings can seal properly but nevertheless slip out of position as a result of forces on a pipe. In this case, the plumbers failed to properly restrain the repaired pipe when using compression fittings.
How much pressure will a compression fitting hold?
Compression fittings are the perfect choice for high pressure applications. In combination with a high pressure tubing material like steel, large compression fittings can often be used at pressures in excess of 10,000 psig.
How do I stop my compression fitting from leaking?
Tighten compression fittings firmly with two wrenches to crimp the ferrule onto the pipe (Photo 3). Also make sure the pipe or tube goes straight into the fitting. Misalignment will cause a leak. If the fitting leaks after you turn on the water, try tightening the nut an additional one-quarter turn.
Do you need jointing compound on compression fittings?
Thread sealants such as joint compound (pipe dope or thread seal tape such as PTFE tape) are unnecessary on compression fitting threads, as it is not the thread that seals the joint but rather the compression of the ferrule between the nut and pipe.
What are the two types of compression fittings?
There are two basic types of compression fitting:Type-A or non-manipulative fitting: These fittings are easy to install and do not require any modifications to the tubing. ... Type-B or manipulative fittings: Installation of Type-B fittings require flaring or belling the tubing.
Do compression fittings fail?
Unlike threaded fittings, compression fittings can seal properly but nevertheless slip out of position as a result of forces on a pipe. In this case, the plumbers failed to properly restrain the repaired pipe when using compression fittings.
Are compression fittings better than push fit?
Solder fittings are the gold standard in copper, however compression fittings are generally the next level down and very reliable. I would stick with those over push fit as these can pop off.
How much pressure will a compression fitting hold?
Compression fittings are the perfect choice for high pressure applications. In combination with a high pressure tubing material like steel, large compression fittings can often be used at pressures in excess of 10,000 psig.
How long will a PVC compression fitting last?
As one of the most-used plumbing materials, PVC pipe is known for being very durable and long-lasting. In fact, PVC pipes last approximately 100 years.
What are compression fittings?
Plumbing compression fittings are designed to connect two pipes; a fixture and a pipe or a fixture and a valve together.
Can you recycle compression fittings?
When using compression fittings, please ensure that you won’t recycle its parts. For instance,yYou just can’t use the old ring and the old seat and then afterwards just replace the nut. That’s a big no-no. If you need to replace the fitting, you must ensure that all the components of the replacement are new.
Do you have to be a master plumber to install compression fittings?
Compression fittings are pretty easy to install. You don’t have to be a master plumb er to be able to create connections with the help of these plumbing parts. However, there are some things that you should remember. 1. These fittings are designed to keep the pipes, fixtures and valves in place.
Can compression fittings be used to lengthen pipes?
Another thing that you have to take note of is that compression fittings are not meant to lengthen pipes. That’s definitely not their job. If you’ll use a double compression type, you’ll have to anticipate that it won’t last very long. Every rotational movement or impact on the fitting will result to its wear and tear.
What is compression fitting?
Compression fittings are one of the most common and versatile methods of connecting metal or hard plastic tubing. Particularly useful for their extreme temperature and pressure capabilities, and their compatibility with aggressive fluids, compression fittings can be seen in systems varying from gas lines in refineries, ...
What are the factors that determine the success of compression fittings?
Chief among these are fitting and ferrule design, tubing selection, and installation procedure.
What is the importance of the shape of the ferrule and the mating angle of the fitting body?
The shape of both the ferrule and the mating angle of the fitting body are critical factors in the reliability of a compression seal. Both components must be tapered in a manner that allows the ferrule to compress properly as the nut is tightened, while maintaining axial alignment with the tubing.
How does metal tubing affect compression?
The way in which metal tubing is produced can have a significant effect on its performance with compression fittings. Tubing should be smooth and free of roughness or extrusion lines that can create a leak path past the ferrule. Furthermore, tubing that has been stored in coils can often have an asymetrical diameter, preventing even compression. While an elastomeric seal can deform to match these slight variations, the metal-to-metal seal of a compression fitting is less forgiving. It is also important that the end of each section be squarely cut, to allow the tubing to sit symmetrically in the fitting body.
Why use softer tubing?
The use of softer tubing (such as polyurethane or vinyl) is not normally recommended with compression style fittings because the tubing wall is likely to collapse, or move away from the ferrule. This negates the holding power of the ferrule, and can also prevent the ferrule from making a leak-tight seal around the full diameter of the tubing. If there is a particular design issue (for example, a tight bend radius) that necessitates softer tubing, it is important to reinforce the tubing wall. Some manufacturers offer tubing inserts for this purpose. The tubing insert, usually made of metal, is pressed into the soft tubing, and supports the tubing wall so that it will not collapse as the ferrule is compressed.
What is the radial compression of a ferrule?
It is this radial compression that creates the leak tight seal between the fitting, ferrule, and tubing, and gives the compression fitting its name. ...
Why is PTFE tubing used?
PTFE tubing is a popular material choice for tubing because it is resistant to most chemicals, handles relatively high pressure, is low out-gassing, and is more flexible than metallic tubing. One key design factor when using this kind of tubing is its tendency to “cold flow”, or deform away from a compressive load. This can cause leaks to develop over time, as the tubing wall begins to creep (cold flow) away from the ferrule. The cold flow issue is exacerbated when the tubing is exposed to high temperatures, and can occur even when fittings are properly installed and initially leak free.
How To Install A Compression Fitting On Plumbing Pipes?
It shouldn’t be that difficult to install a compression fitting into your DIY plumbing. In fact, there are only three simple steps to follow. Here is a step-by-step guide to doing the installation. Read to learn more!
How To Select Compression Fitting?
Therefore, you need to choose a compression fitting that is strong enough to allow only the necessary amount of water to pass through without undue pressure drop. Here are a few important factors you might want to look out for before purchasing a compression fitting:
What To Do If Compression Fitting Is Leaking?
Water leakage is not an uncommon case, but it is quite easy to solve. Yet, you might need to spend time finding out the reason and try different solutions!
How to install a compression fitting on a pipe?
Slip the compression nut from the compression fitting onto the pipe, then slip on the compression ring. Slide both pieces down so they are 1 inch or so from the end of the pipe. Fit the compression fitting onto the pipe (or fit the pipe into the fitting, as applicable) until the pipe stops inside the fitting.
What is compression fitting?
A compression fitting is not a specific plumbing part but rather a type of fastening system for valves, water supply tubes and other plumbing fittings. The valve (or other part) has a port where the pipe slips in, and the port has male threads on the outside. Before you fit the parts together, you slide a compression nut ...
How to check if a compression fitting is leaking?
Check the compression fitting for leaks after you've completed all of the other plumbing connections and turned on the water supply to the pipe. If the compression fitting leaks, use both wrenches to tighten the compression nut gently until the leak stops.
How to cut a pipe?
Cut the end of the pipe, if necessary, using a tubing cutter. Open the jaws of the tubing cutter and fit it onto the pipe so the pipe rests squarely against the two flat rollers of the cutter. Tighten the cutter so the cutting wheel is snug against the pipe.
How to seal a pipe with a nut?
Once the pipe and fitting are together, you slide the ring against the fitting, then thread the nut onto the fitting. The nut compresses the ring between itself and the fitting, and the tapered edges of the ring are wedged tight inside the fitting and the nut, creating a watertight seal.
How to tighten compression nut?
Slide the nut over the ring and thread it onto the fitting until it is hand-tight. Be careful not to cross-thread the nut. Fit one wrench onto the body of the fitting and hold it so that the fitting doesn't move. Use another wrench to tighten the compression nut about one-half to three-quarters of a turn.
How to clean a pipe smooth?
Clean the outside of the pipe with a rag; it must be clean, with no paint or other contaminants. If necessary, apply a cleaner or solvent to the rag to clean the pipe .
How Does a Compression Fitting Work?
Okay, time to get into the nitty gritty of compression fittings. But first, we need to explain how a compression fitting works. While reading this, take a look at the diagram below. It will help you visualize how everything’s put together.
Why use compression fittings?
You’ll want to use compression fittings in a situation where the run of pipe needs to be taken apart or when an area of the pipe will be difficult to solder. One common location in which this occurs is on supply lines to a bathroom, laundry, or kitchen sink because they have compression fittings at both the stop valve and the faucet inlet.
How to tighten a pipe?
Tighten Each Side. Place one crescent wrench on the union. Use your second crescent wrench to tighten each side ( the first wrench is used to keep the pipe stable while you’re tightening with the second wrench). Once snug, tighten about one more half turn.
How to fix a leaky tubing?
Tighten the compression nut with a wrench, forcing the ferrule down into the tubing to secure and seal the connection. If the joint leaks when the water is turned on, tighten the nut a quarter turn at a time until the leak stops. Don’t over-tighten the joint. Too much pressure can crush the tubing or crack the nut.
What is ferrule in plumbing?
A ferrule is a metal band that forms or strengthens a joint. Because copper is a soft metal, the seal can be extremely tight. Use pipe joint compound (or Teflon plumber’s tape) to make sure the seal is watertight. You should also anchor or support the tubing within two feet of either side of the fitting. A side-view showing how the compression nut ...
What happens if you don't bend a pipe?
If you don’t bend the pipe in a gradual, sweeping arc, you’ll be surprised how fast it will kink. And a kink in the pipe is nearly impossible to get back to the right shape. You’ll need to throw the piece away.
How to join a compression joint?
If you don’t need to create a compression joint, but rather need to join a compression union, then follow these steps. 1. Shut Off the Water. I know, it gets annoying having to read this same instruction over and over. But really, it’s that important.
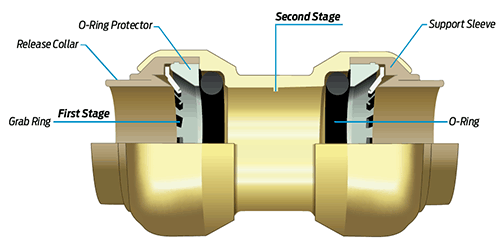
Introduction to Compression Fittings
Ferrules
- The ferrule is the primary sealing component of a compression fitting assembly, and they can be found in a wide variety of materials ranging from stainless steel to graphite. The majority of ferrules in the marketplace however, are manufactured from metals. Metal ferrules are attractive because they are stable over a wide temperature range, and they can bear compressive loads wi…
Tubing
- Compression fittings are most commonly used with hard tubing because the tubing wall must be rigid enough to resist the compression forces applied by the ferrule. Common choices include metallic tubing (such as stainless steel or copper) and stiff plastic tubing (such as PEEK, nylon, Teflon®, Kynar®, or polyethylene). The use of softer tubing (such as polyurethane or vinyl) is no…
Installation
- Installation instructions for compression fittings vary depending on the manufacturer and the specific fitting design. Care should be taken to follow the assembly procedures recommended by the manufacturer. There are however, several common elements to the installation procedure for nearly all compression fittings:
Application Considerations
- Compression fittings are often selected for reasons beyond just leak-free sealing and ease of use. In many applications, high pressures and temperatures necessitate the use of hard tubing, which is incompatible with many other types of fittings. In other applications, such as laboratory instruments, concerns over contamination make the sterility and low out-gassing properties of s…
Conclusion
- Compression fittings are widely used across a number of industries, and can be an asset in almost any fluid power design. Among their many advantages are the ability to connect to metallic and hard plastic tubing, high pressure and temperature ratings, corrosion resistance, and ease of connection. While there are many challenges associated with compression fittings as w…