
How Optical Coatings Work Whenever light passes from one medium into another medium with different optical properties, part of the light is reflected and part transmitted. The intensity ratio of the reflected and refracted components is a function mainly of the difference in refractive index among the materials, the polarization of the incident light, and the angle of incidence.
What is optical coating?
An optical coating is one or more thin layers of material deposited on an optical component such as a lens or mirror, which alters the way in which the optic reflects and transmits light. One type of optical coating is an anti-reflective coating, which reduces unwanted reflections from surfaces, and is commonly used on spectacle and camera lenses.
What is the difference between optical coating and anti-reflection coating?
An anti-reflection coating could be applied to reduce the reflection at each surface to less than 0.1% and a highly reflective dielectric coating could also be applied to increase reflectivity to more than 99.99%. An optical coating is composed of a combination of thin layers of materials such as oxides, metals, or rare earth materials.
What factors affect the performance of an optical coating?
The performance of an optical coating is dependent on the number of layers, their thickness, and the refractive index difference between them. This application note discusses optical coating theory, different types of common coatings, and coating manufacturing methods.
What are the optical coatings of a mirror?
The simplest optical coatings are thin layers of metals, such as aluminium, which are deposited on glass substrates to make mirror surfaces, a process known as silvering. The metal used determines the reflection characteristics of the mirror; aluminium is the cheapest and most common coating,...
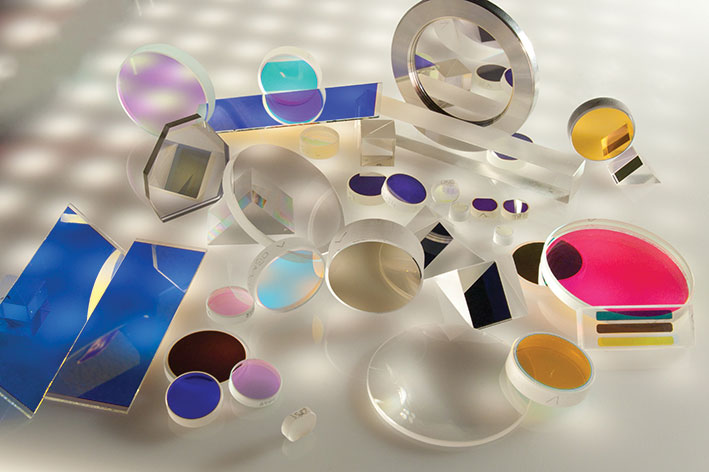
How are optical coatings applied?
Optical coatings can be applied directly to the surface of an optical component to tailor its reflectivity, as in the case of an optical mirror or beamsplitter. For other components, such as lenses, the applied coatings may simply improve their overall transmission properties by reducing surface reflectivity.
Why do we need optical coating?
The prime uses of optical coating are to block certain wavelengths of light or to provide a highly reflective surface. In some cases, they provide both functions, reflecting specific wavelengths, while allowing others to pass through unobstructed.
How do reflective coatings work?
AG and AR coatings are made of multiple layers of metal oxides, and they are applied to the surfaces of the lens. These layers effectively reduce the amount of light reflected onto your lenses, allowing more light to be transmitted through the lens without the glare.
How are lenses coated?
Protecting your lenses Scratch-resistance lens coatings work by a nano millimetre layer be applied to your lenses, often behind the anti-reflection layer. This is designed to gradually increase hardness, in order to protect your lenses from scratches.
Which coating is best for eyeglasses?
AR coating is highly recommended for all eyeglass lenses, but especially for polycarbonate, high-index and aspheric lenses, which all reflect more light than regular lenses.
What are lens coatings made of?
These are constructed from thin layers of materials such as magnesium fluoride, calcium fluoride, and various metal oxides, which are deposited onto the optical substrate.
How do you remove coating from glasses?
Mix 5 parts of isopropyl alcohol with one part of saltwater. Place your glasses onto a plate and pour out the prepared solution just enough so the lenses are entirely submerged. Let it sit in the solution for an hour to soften the anti-reflective coating. Scrape off the anti-reflective coating using a plastic scraper.
What are the disadvantages of anti-reflective coating?
Disadvantages of Anti-Glare Coating Dirt is very visible: Though they stay cleaner for longer than standard lenses, when they are dirty, it's very evident because there's no glare to hide any particles or grime. Cannot be repaired: Once damaged, the lenses will need to be replaced.
Does anti-glare coating wear off?
The average life of an anti glare coating is two years, and after that, you have to change it with the new one. The anti glare coating starts to wear off under various conditions, including scratches from keys, using lousy quality cleaning solutions, and microfiber cloths.
How long do lens coatings last?
between one and two yearsOn average, lens enhancements last between one and two years depending on how well you care for your glasses. One lens coating that can increase the life of your lenses is scratch resistant coatings. Use these if you tend to handle your glasses roughly or use them in rough environments.
What is an advanced coating on glasses?
Anti-reflection coatings are also known as AR, or MAR, and comprise many different thin layers of coating to greatly reduce glare from different wavelengths of light. By reducing unwanted reflections from the lens surfaces, more light is transmitted through the lens, making vision clearer.
Do glasses coatings work?
A good quality anti-reflective coating can reduce almost all light reflections from a pair of spectacles. That leads to 99.5% of available light passing through to the eye, offering better overall vision. Anti-reflective coating makes the lenses look within your spectacles virtually invisible.
Why are lenses coated with thin film?
Lenses are often coated with a thin film to reduce the intesntiy of reflected light.
What are mirror coatings used for?
Mirror coatings decrease the light transmission thereby minimizing certain harmful wavelengths from reaching the eyes. They optimize the usable light that passes through the lens for specific light conditions helping guard against harmful high energy visible light.
What is BBAR coating?
Broadband antireflective (BBAR) coatings consist of multiple layers, alternating between a high index material and a low index material. The layers are deposited on the substrate via electron-beam deposition.
What is thin film optical coatings?
Thin film optical coatings are applied to optical substrates such as glass to alter or change its optical properties. The coating is applied in extremely thin layers to the surface and the number of coatings and the thickness of the coating is done to effect a specific wavelength of the light.
What is optical coating?
An optical coating is one or more thin layers of material deposited on an optical component such as a lens or mirror, which alters the way in which the optic reflects and transmits light. One type of optical coating is an anti-reflective coating, which reduces unwanted reflections from surfaces, ...
How does high reflection coating work?
High-reflection (HR) coatings work the opposite way to antireflection coatings. The general idea is usually based on the periodic layer system composed from two materials, one with a high index, such as zinc sulfide ( n =2.32) or titanium dioxide ( n =2.4), and one with a low index, such as magnesium fluoride ( n =1.38) or silicon dioxide ( n =1.49). This periodic system significantly enhances the reflectivity of the surface in the certain wavelength range called band-stop, whose width is determined by the ratio of the two used indices only (for quarter-wave systems), while the maximum reflectivity increases up to almost 100% with a number of layers in the stack. The thicknesses of the layers are generally quarter-wave (then they yield to the broadest high reflection band in comparison to the non-quarter-wave systems composed from the same materials), this time designed such that reflected beams constructively interfere with one another to maximize reflection and minimize transmission. The best of these coatings built-up from deposited dielectric lossless materials on perfectly smooth surfaces can reach reflectivities greater than 99.999% (over a fairly narrow range of wavelengths). Common HR coatings can achieve 99.9% reflectivity over a broad wavelength range (tens of nanometers in the visible spectrum range).
What is dielectric coating?
The other major type of optical coa ting is the dielectric coating (i.e. using materials with a different refractive index to the substrate). These are constructed from thin layers of materials such as magnesium fluoride, calcium fluoride, and various metal oxides, which are deposited onto the optical substrate. By careful choice of the exact composition, thickness, and number of these layers, it is possible to tailor the reflectivity and transmitivity of the coating to produce almost any desired characteristic. Reflection coefficients of surfaces can be reduced to less than 0.2%, producing an antireflection (AR) coating. Conversely, the reflectivity can be increased to greater than 99.99%, producing a high-reflector (HR) coating. The level of reflectivity can also be tuned to any particular value, for instance to produce a mirror that reflects 90% and transmits 10% of the light that falls on it, over some range of wavelengths. Such mirrors are often used as beamsplitters, and as output couplers in lasers. Alternatively, the coating can be designed such that the mirror reflects light only in a narrow band of wavelengths, producing an optical filter .
How to reduce reflections from surfaces?
Further reduction is possible by using multiple coating layers, designed such that reflections from the surfaces undergo maximum destructive interference. By using two or more layers, broadband antireflection coatings which cover the visible range (400-700 nm) with maximum reflectivities of less than 0.5% are commonly achievable. Reflection in narrower wavelength bands can be as low as 0.1%. Alternatively, a series of layers with small differences in refractive index can be used to create a broadband antireflective coating by means of a refractive index gradient .
How much does antireflection coating reduce reflection?
Such coatings can reduce the reflection for ordinary glass from about 4% per surface to around 2%. These were the first type of antireflection coating known, having been discovered by Lord Rayleigh in 1886.
What is transparent conductive coating?
Transparent conductive coatings are used in applications where it is important that the coating conduct electricity or dissipate static charge. Conductive coatings are used to protect the aperture from electromagnetic Interference, while dissipative coatings are used to prevent the build-up of static electricity.
Why do we use dielectric layers?
Dielectric layers are sometimes applied over top of metal films, either to provide a protective layer (as in silicon dioxide over aluminium), or to enhance the reflectivity of the metal film. Metal and dielectric combinations are also used to make advanced coatings that cannot be made any other way.
What is optical coating?
In simple terms, an optical coating is one or more thin layers of material that affect how light interacts with a certain optical component. In order to understand how optical coatings work, it is important to know how light interacts with transparent media. The index of refraction (n) of a medium describes how light behaves when travelling within ...
How does optical thickness relate to the distance traveled by light?
The optical thickness that light travels within a medium is thus equal to the real distance travelled by light in vacuum. The wave nature of light allows for two or more light waves add their intensities together when they interact.
What is it called when waves cancel each other out?
The waves are then said to be “out of phase” and when this occurs, adding the intensities of the waves cancel each other out in a phenomenon called “destructive interference”. Destructive interference can happen with other types of waves, such as sound waves.
What is the index of refraction?
The index of refraction (n) of a medium describes how light behaves when travelling within it, with vacuum having an index equal to 1 and all other media having an index greater than 1.
What happens when a wavelength is half a wavelength?
On the other hand, if the phase difference between the waves is half a wavelength, the peak of one wave lines up with the valley of the other wave, as shown in the figure below.
What is the purpose of coating optical fiber?
The main job of coatings is to protect the glass fiber , but there are many intricacies to this objective. Coating materials are carefully formulated and tested to optimize this protective role as well as the glass fiber performance.
Why is the low index coating important for fiber lasers?
The low index coating gives the fiber a higher numerical aperture (NA), which means the fiber can accept more of the pump power.
How thick is a coating on fiber?
Some coatings may be as thin as 10 µm, and others are several hundred microns thick. Some specialty fibers use the same acrylate coatings as communication fibers.
What percentage of fiber is polymer?
For a standard-size fiber with a 125-µm cladding diameter and a 250-µm coating diameter, 75% of the fiber’s three-dimensional volume is the polymer coating. The core and cladding glass account for the remaining 25% of the coated fiber’s total volume. Coatings play a key role in helping the fiber meet environmental and mechanical specifications as well as some optical performance requirements.
Why do we use high index coating?
The high-index outer coating helps the fiber to meet strength and bending requirements. Fibers for power delivery. In addition to rare-earth-doped fibers for lasers, there are other specialty fibers where a low-index coating can serve as a cladding layer and improve optical performance.
Why does fiber break during proof testing?
During proof testing, the fiber may break at a point with a weak area, due to some flaw in the glass. In this case, the fiber that ran through the testing gear prior to the break has passed the proof test. It has the minimum tensile strength. Fiber after the break also is passed through the machine and screened in the same fashion. One problem is that such breaks can affect the continuous length of fiber drawn. This can be a problem for some specialty fiber applications, such as gyroscopes with polarization-maintaining fiber, where splices are not acceptable. Breaks also can lower the fiber manufacturer’s yield. And an excessive number of breaks can indicate other problems in the preform and draw processes 2.
What happens if you don't coat glass?
If a fiber were to be drawn and not coated, the outer surface of the glass cladding would be exposed to air, moisture, other chemical contaminants, nicks, bumps, abrasions, microscopic bends, and other hazards. These phenomena can cause flaws in the glass surface.
What is optical coating?
Optical coatings are deposited as thin-film multilayers of a variety of materials using specific deposition techniques. Coatings are applied to optical components that are intended for use at wavelength regions between UV and far-IR. The materials and processes used to make these coatings are described here and in the attendant materials data tables.
What is surface coating?
Surface coatings used to control optical, mechanical and electrical properties are deposited as nano- and micrometer thicknesses of special materials.
How are fluoride and oxide deposited?
With the exception of the fluoride compounds and lanthanum titanate, these materials are typically deposited by e-beam evaporation or by sputtering from targets . Fluoride compounds and many of the oxide compounds can, alternatively, be evaporated from resistance-heated sources. Because of chemical, stress and process incompatibilities, layers from the oxide and fluoride chemical classes are generally not combined in a coating. The exception is with UV coatings where layers are thin and the material selection of transparent materials is small. Multicomponent materials have been developed to achieve improvements in one or more thin-film layer properties over the single-element precursor. Examples are doped fluorides and oxides and mixtures of two or more similar materials. Mixed and doped starting materials can be obtained, or modifications can be accomplished during evaporation or sputtering from separate sources of materials. Layers of fluorides and sulfides (selenides) are combined in LWIR coatings.
What is PVD in coatings?
Deposition and growth of thin film s of these materials to build optical coatings is accomplished by one of the many variations of two main physical vapor deposition (PVD) processes: evaporation and sputtering. Deposition of films of metal oxide compounds by evaporation or by sputtering can proceed from a preparation of the compound as the starting material or from the base metal and subsequent reactive oxidization to the final desired composition. The nonoxide materials in Table 1 generally start and end with similar compositions. The data tables that follow this article provide suggested deposition parameters.
How to deposit optical film?
Optical films can be deposited from a metal target by oxidizing/nitriding sputtered metal ions to deposit an oxide or nitride film layer of the desired composition. DC magnetron sputtering is the technique used with metal targets that are electrically conducting.
How to reduce coating problems?
A technique that coating technicians apply to reduce these problems is to create a dense melt by repeated charging of the crucible and melting down to a dense mass. This procedure is wasteful of time and resources, and an improved preparation of many oxide compounds has been introduced: premelted cones that fit the e-beam pocket.
What happens when a melt is electrically conducting?
When the melt is electrically conducting, e-beam deflection and defocus due to localized charging are eliminated.
What is the structure of a coating?
The structure of most coatings resembles a series of discrete alternating layers of high index and low index materials. Different arrangements of stack structure result in different types of coatings (e.g., Bandpass vs. Edgepass vs. BBAR). Fine tuning of layer thicknesses and refractive indices is done to optimize performance characteristics in the wavelength range of interest. Thorlabs has a selection of thin film modeling tools to design, characterize, and optimize many aspects of an individual coating's performance.
What is dielectric coating?
The dielectric coating on dichroic beamsplitters is the source of their functionality. The alternating layers in the coating are designed to cause constructive interference for those wavelengths to be transmitted and destructive interference for those wavelengths to be reflected. The thickness of the coating and the refractive index of the materials in the layers determine the design wavelength for a given beamsplitter.
What is an AR coating?
Antireflective (AR) coatings are hard refractory-oxide coatings that minimize surface reflections within specified wavelength ranges when applied to the surface of optical components. Without AR coating, 4% of the light is lost at each optical surface due to reflections. For example, if three uncoated lenses are being used in series, this 4% loss occurs at each of the six optical surfaces. This results in a total loss of 21.7%. If three AR-coated lenses with a "B" coating (R avg <0.5% per surface) are used instead, the total loss of incident light due to surface reflections is <3%. The use of AR-coated optics improves transmission from 78.3% to greater than 97% in this case. Please note that the 4% loss at the interfaces of uncoated optics is an approximate value that varies greatly with material and angle of incidence (AOI). Please note that the color of the lens does not correlate to the lens’ specifications. The color of each AR coating may vary from batch to batch and is not an indicator of performance.
How many broadband coatings does Thorlabs offer?
Thorlabs currently offers nine different broadband HR coatings optimized for various performance parameters. The graph below shows the specified wavelength range of Thorlabs' in-house broadband HR coatings. Click on the bars in the graph below to view the performance plot for each coating. Click here for a raw data file that compares all of our broadband HR Coatings.
How are vacuum deposition coatings formed?
These coatings are formed by vacuum deposition coating techniques and consist of two reflecting stacks, separated by an even-order spacer layer. These reflecting stacks are constructed from alternating layers of high and low refractive index materials, which can have a reflectance in excess of 99.99%. By varying the thickness of the spacer layer and/or the number of reflecting layers, the central wavelength and bandwidth of the filter can be altered.
What is Thorlabs coating?
Thorlabs' state-of-the-art, in-house, optical coating department provides us with coating capabilities ranging from metal coatings and antireflective coatings to cutting edge Ion Beam Sputtered (IBS) and Plasma Assisted coatings. This full-scale facility not only allows us to produce large numbers of our catalog optics in house but also expands our ability to manufacture custom-coated optics to suit a variety of customer needs.
What is ion beam assisted deposition?
Ion-Beam Assisted Deposition (IAD) uses the same E-beam method to evaporate coating materials but with the addition of an ion source to promote nucleation and growth of materials at lower temperatures (20 - 100 °C). The ion source allows temperature-sensitive substrates to be coated. This process also results in a denser coating that is less sensitive to spectral shifting in both humid and dry environmental conditions.

Overview
Types of coating
The simplest optical coatings are thin layers of metals, such as aluminium, which are deposited on glass substrates to make mirror surfaces, a process known as silvering. The metal used determines the reflection characteristics of the mirror; aluminium is the cheapest and most common coating, and yields a reflectivity of around 88%-92% over the visible spectrum. More expensive is silver, which h…
Current market and forecast
Estimated at US$6.5 billion in 2013, the global demand of optical coatings is forecast to grow 6.5% annually over the next years. The largest application market of optical coatings is electronics and semiconductor combined, while the fastest growing one is fiber optics & telecommunication combined.
Sources
• Hecht, Eugene. Chapter 9, Optics, 2nd ed. (1990), Addison Wesley. ISBN 0-201-11609-X.
• I. Moreno, et al., "Thin-film spatial filters," Optics Letters 30, 914-916 (2005)
• C. Clark, et al., "Two-color Mach 3 IR coating for TAMD systems", Proc. SPIE Vol. 4375, p. 307-314 (2001)
See also
• List of telescope parts and construction