
Here's the formula:
- The number of partially completed units x percentage of completion = equivalent units of production.
- 300 x .5 = equivalent units of production.
- equivalent units of production = 150.
- 500 + 150 = 650 equivalent units of production.
- Total equivalent units for a cost component = A + B × C.
- Where.
How do I find equivalent units?
How do you find equivalent units? Equivalent units. are calculated by multiplying the number of physical (or actual) units on hand by the percentage of completion of the units. If the physical units are 100 percent complete, equivalent units will be the same as the physical units.
How to compute equivalent units in cost accounting?
- Beginning inventory of 750 units is 100% complete with regard to materials and 30% complete with regard to conversion.
- 9,500 units were started during the period.
- 8,900 units were completed and transferred.
- Ending inventory is 100% complete with regard to materials and 68% complete with regard to conversion.
How do you calculate equivalent units of production?
Calculate Equivalent Units of Production. Here’s the formula: The number of partially completed units x percentage of completion = equivalent units of production. Plugging in the information that you have from the parts maker, there are 300 partially completed units. These 300 units are 50 percent completed.
How do you calculate cost per equivalent unit?
Key Concepts and Summary
- costs added during the period
- costs of the units in ending inventory
- costs started and transferred during the period
- costs in the beginning inventory and costs added during the period
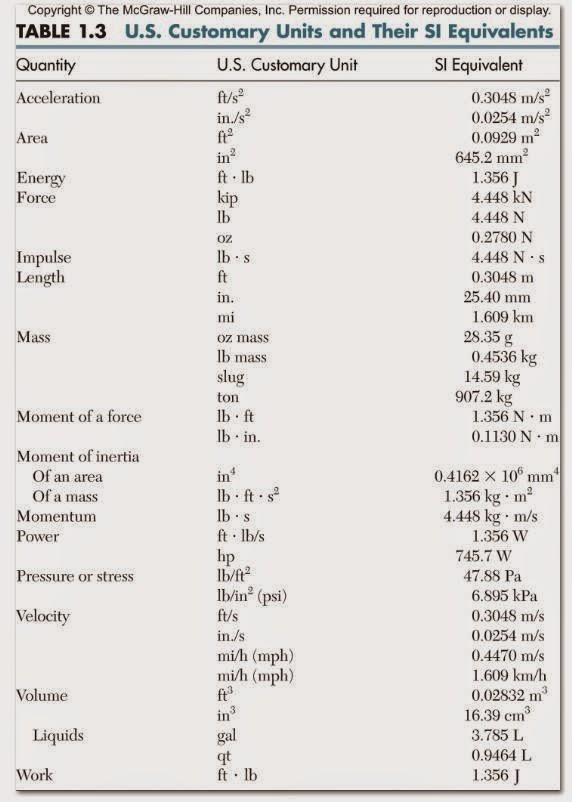
What is equivalent units in accounting?
An equivalent unit of production is an expression of the amount of work done by a manufacturer on units of output that are partially completed at the end of an accounting period. Basically the fully completed units and the partially completed units are expressed in terms of fully completed units.
How is the cost per equivalent unit calculated?
The cost per equivalent units for materials is the total of the material costs for the beginning work in process inventory plus the cost of material transferred in to the department plus the total of material costs incurred during the period.
How do you calculate equivalent units using weighted average?
Equivalent units = Number of physical units × Percentage of completion. For direct materials, 3,000 equivalent units = 5,000 physical units × 60 percent complete; for direct labor and overhead, 1,500 equivalent units = 5,000 physical units × 30 percent complete.
How do you prepare an equivalent unit statement?
For example – in a process 1,000 units were introduced out of which till the accounting period 600 units are completed and out of 400 units 60% are completed, i.e. (400 × 60)/100 = 240 units will be considered as equivalent units and total completed units will be 840 units (i.e., 600 + 240).
How do you find the equivalent units of production using FIFO?
5:547:52Cost Per Equivalent Unit, FIFO Method, Part 1 - YouTubeYouTubeStart of suggested clipEnd of suggested clipSo we've got two thousand three hundred and twenty-four direct materials in 2255 for conversionMoreSo we've got two thousand three hundred and twenty-four direct materials in 2255 for conversion costs now we just divide in order to get the cost per equivalent unit.
How is the cost per equivalent unit calculated quizlet?
We calculate the cost per equivalent unit by adding together the cost of beginning Work in Process Inventory and the cost added during the period. We divide the total dollar amount by the number of equivalent units we previously calculated.
What do you mean by equivalent units of production?
It is the number of completed units of an item that a company could theoretically have produced, given the amount of direct materials, direct labor, and manufacturing overhead costs incurred during that period for the items not yet completed.
What is equivalent production how it is computed?
The formula of equivalent production is : Equivalent units of work-in-progress = Actual no. of units in progress of manufacture x Percentage of work completed. For example, if 70% work has been done on the average on 200 units still in process, then 200 such units will be equal to 140 completed units.
What are the total equivalent units for direct materials?
Calculating Equivalent Units of ProductionTotal equivalent units (direct materials) = 190,000 + 5,000 * 100%= 195,000 unitsTotal equivalent units (conversion costs) = 190,000 + 5,000 * 60%= 193,000 unitsMay 20, 2022
Why is the calculation of equivalent units necessary?
What are equivalent units? Why do we need to calculate equivalent units? Equivalent units must be calculated in order to allocate manufacturing costs to both the completed units and the units still in inventory.
How do you calculate units start and completed?
Therefore, the started and completed unit of 75,000 units was computed by deducting the ending WIP (5,000 units) and beginning WIP (10,000 units) from the total units to account for of 90,000 units....1-on-1 CMA Coaching Support.Beginning WIP10,000Started units this period80,000Total units to account for90,0001 more row
How are equivalent units for transferred in calculated under the first in first out FIFO?
Under the FIFO cost flow assumption, it is assumed that the costs that enter first in the department exit first. The consequence of this assumption is that the cost of units transferred out first includes the cost of opening WIP and then the cost of units added during the period.
How to find equivalent units?
To simply calculate equivalent units, you can multiply the number of physical items by the percentage of the work done on them. For two items that are 50% done, you would have one equivalent unit (2 x 50% = 1). When the items are completely finished, the number of equivalent units is equal to the physical items.
What is equivalent unit of production?
Equivalent units of production are a concept used to understand how much money partially completed products are worth to a company. They are useful for process costing, which is the analysis of money flow within the manufacturing process. Equivalent units describe how much work has been done on a certain number of physical items.
Factors Of Production
Equivalent units must be considered relative to each of the factors of production. In other words, 80% of necessary direct material may be in process but only 60% of the direct labor and factory overhead.
Example
To better understand equivalent units, focus on an example for Navarro Steel. To begin, one needs to identify the total units that are to be considered, no matter their stage of completion at the beginning and end of the month.
Cost Per Equivalent Unit
The equivalent unit calculations are carried forward into the “cost per equivalent unit” schedule. This shows how the combined costs from beginning work in process (assumed at $2,122,500) and current period production (assumed at $7,365,000) are divided by the equivalent units.
What is equivalent unit?
An equivalent unit is a term used to describe work-in-progress inventory units at the end of a specific time period. It defines the number of completed units of a particular item that the company could have produced, given the amount of costs that were incurred during that time period for all items not yet completed.
Why are equivalent units of production recorded separately?
Equivalent units of production are recorded separately for the three categories of manufacturing costs because direct materials are added to the beginning of the manufacturing process, while labor and manufacturing overhead are added throughout the process. As a result, the equivalent units of direct materials will always be higher ...
Is the equivalent unit of direct materials higher than other units of production?
As a result, the equivalent units of direct materials will always be higher than other manufacturing costs. When a company assigns costs to an equivalent unit of production, the simplest method is by using the weighted-average cost of beginning inventory and adding new cost in additional purchases of direct materials.
What are equivalent units in work in process?
Answer: Equivalent units in work in process are often different for direct materials, direct labor, and manufacturing overhead because these three components of production may enter the process at varying stages. For example, in the Assembly department at Desk Products, Inc., direct materials enter production early in the process ...
What happens if a unit is 100 percent complete?
If the physical units are 100 percent complete, equivalent units will be the same as the physical units. However, if the physical units are not 100 percent complete, the equivalent units will be less than the physical units.
What is the second method of calculating equivalent units of production?
The second method of calculating equivalent units of production uses a FIFO method or First-in First-out. Businesses will first sell the finished inventory that they first receive, followed by any inventory they receive later, hence first in, first out.
Why do accountants use equivalent units?
Accountants use the term equivalent units to explain how costs are segmented between items that are still in production versus items that are in completed form. Many items are in continuous production, so without some way to calculate equivalent units, it would be difficult to determine how much money was tied up in production costs.
What is equivalent unit?
Equivalent units is a cost accounting concept that is used in process costing for cost calculations. It has no relevance from an operational perspective, nor is it useful for any other type of cost derivation other than process costing. Equivalent units of production are usually stated separately for direct materials and all other manufacturing ...
What is equivalent units of production?
Equivalent units of production is a term applied to the work-in-process inventory at the end of an accounting period. It is the number of completed units of an item that a company could theoretically have produced, given the amount of direct materials, direct labor, and manufacturing overhead costs incurred during that period for ...
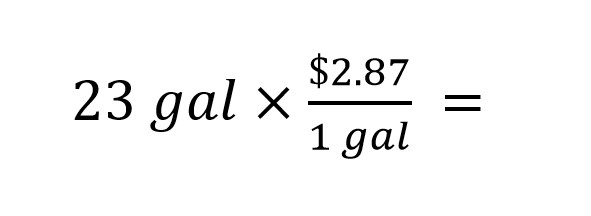