
Calculate an employee’s labor cost per hour by adding their gross wages to the total cost of related expenses (including annual payroll taxes and annual overhead), then dividing by the number of hours the employee works each year. This will help determine how much an employee costs their employer per hour.
How to calculate the total hourly cost of Operation?
Conversely, you can calculate the total hourly cost of operation by dividing the annual fixed costs by the number of annual operation hours and adding it to the variable hourly cost.
How to calculate operating expenses?
Thus, operating expenses include: To calculate the operating cost, you first need to determine the Cost of Goods Sold (COGS). COGS = Opening Stock + Purchases + Direct Expenses – Closing Stock. Then, calculate the total operating expenses, as mentioned above.
How to calculate labor cost?
How Is Labor Cost Calculated? 1 #1. Calculate the Gross Pay. The first thing you want figure out is the gross pay of an employee. 2 #2. Figure Out the Actual Worked Hours. 3 #3. Determine All Annual Costs Per Employee. 4 #4. Calculate the Total Annual Payroll Cost. 5 #5. Calculate the Hourly Labor Cost.
How to figure out the actual worked hours per year?
Figure Out the Actual Worked Hours The total work hours per year are 2080. However, every employee needs to take days off. Let’s say that Maria did not work 12 days in that year. Here is how to calculate hours not worked: The actual hours that Maria has worked for a year are 1984 hours. #3. Determine All Annual Costs Per Employee

Is it dangerous to know your hourly cost?
Without knowing this cost, it’s impossible for any business to be able to understand their true operating costs, which is an extremely dangerous practice. Determining your Actual Hourly Cost can be a massive headache at times.
Can owners and managers take full control of employee expenses?
Well it turns out that owners and managers today can take full control of their Employee Expenses, without the need to know a single formula or require any spreadsheet experience. I’m going to share this with you today.
Is a spreadsheet necessary to calculate hourly cost?
While a spreadsheet is still a great idea to be able to list, display and filter employees when we have this cost, it’s not necessarily needed to grasp the main concept of just a regular hourly cost.
How Is Labor Cost Calculated?
In order to calculate the labor cost of an employee per hour, you need to go through a simple process of factoring in all expenses related to their employment.
What percentage of labor cost should be in a company?
The average labor cost percentage should typically be in the range of 20% to 35% of a company’s gross sales. However, there are variations, depending on your field.
What is equal labor cost?
The expenses that you pay for each employee equal your labor cost for that particular staff member.
What does labor cost mean?
Labor cost does not only mean the hourly rate that you pay a member of your staff. It spans a number of other expenses that you need to account for. Only after factoring them in you can get the actual labor expenses for your company.
How to reduce labor expenses?
One of the most important tips for decreasing your labor expenses is to accurately track employee hours. Mistakes in time tracking can have serious and costly consequences for your business.
What are the biggest expenses you need to cover?
Whether you’re running a restaurant, a construction company, or another small business with employees, labor costs are some of the biggest expenses you'll need to cover.
How many hours does a worker work in a year?
The total work hours per year are 2080. However, every employee needs to take days off.
How are production and machinery costs related?
Companies then must evaluate their total expenses with a degree of accuracy and confidence to achieve profitability. Machine vs. production costs factor into the overall expenses of running a company. Neither cost should be calculated in isolation but considered as a part of a larger equation. Production costs represent the total expenses related to the operational costs of doing business as a company, while industrial machinery costs are those expenses related to the means of making the product. The operating costs of each are determined by combining fixed and variable costs that are calculated at yearly and hourly rates.
What are some examples of unexpected costs?
Unexpected costs are those unplanned or hidden costs that can lead to a setback or delays in production that affects a company’s bottom line. Downtime due to a machine breaking down is a good example of an unexpected cost. Reliability of industrial machinery is a must. Another example is during machinery changeovers. More a hidden cost than unplanned, when the same machine is used to produce different parts or components it may require a changeover, i.e., refitting the machine with different attachments to accommodate given production. Either of these unplanned or hidden operational costs are difficult to calculate. Keeping detailed records of unplanned downtime, predictive maintenance, and effective planning of changeovers can help offset and factor in unexpected costs.
Is annual operating cost fixed or variable?
The annual operating cost of industrial machinery is part of a broader equation that is affected by two distinct types of costs, fixed and variable. Where one cost is a certain amount, the other can fluctuate. Fixed costs remain the same even as the volume of production rises or falls. Variable costs do not. Such costs increase or drop with the volume of production. A good example of each—when companies acquire industrial equipment that machinery is considered an investment, i.e., an asset, not a cost. However, its annual depreciation is certain and unaffected by the volume of production. Therefore, it is a fixed cost. The cost of repairing that machinery each year can vary in direct proportion to the volume of production. Therefore, those costs are variable.
How are operating costs reflected in income statement?
Operating costs are reflected in the income statement after calculating the gross income. These are deducted from your gross income to calculate your business’s net income. Net income is the last item appearing on your company’s income statement.
What is the purpose of operating costs?
Operating costs form a substantial portion of the total production expenses. So, to manage such costs, manufacturing units have to adopt operational cost reduction strategies. These include putting specialized machinery and equipment and evaluating alternatives to machinery. Thus, as a manufacturer, you need to manage operating expenses.
What Is Operating Expense?
Operating expenses refer to the expenses that your business incurs over the normal course of its operations. These include inventory costs, rent, marketing, payroll, research, and development, etc.
What is COGS in sales?
COGS is also known as Cost of Sales. It includes all the expenses that are directly associated with the production of goods or services. Accordingly, COGS includes the following expenses:
Why do non-operating expenses appear on income statement?
Non-operating expenses appear below the operating expenses in your income statement. The very reason is to allow you to assess the core operations of your business. Thus, your company’s revenue is the first item that appears on the income statement. Then, you deduct COGS from revenue to determine your company’s gross income.
How does reducing operating costs affect business?
Reducing your operating costs to a greater extent can negatively impact your business productivity and overall profit. Though, your business profits increase in the short-term if you choose to reduce specific operating costs. However, such a decision can impact your business earnings in the long-run.
Why is it important to keep track of your business's operating costs?
It is important to keep a track of your business’s operating costs and non-operating costs. This helps you in analyzing how each of the costs is linked to your business’s revenue-generating activities. Further, it also helps you to know if you can run your business efficiently or not .
How to calculate total hourly cost?
Conversely, you can calculate the total hourly cost of operation by dividing the annual fixed costs by the number of annual operation hours and adding it to the variable hourly cost.
What are the annual variable costs?
The annual variable costs include: Hourly energy consumption. Consumables lost during use. Maintenance costs. Repair costs. If you multiply the variable costs—which are typically calculated by the hour—by annual hours of operation and add the expenditure to the annual fixed costs, you can calculate the total annual cost of owning the equipment. ...
When buying new equipment, what is the price tag?
When you purchase new equipment, the price tag is just the first expense your business will incur throughout its total service life. Before you purchase a big-ticket item—even when the equipment is meant to last for years—take the time to consider ancillary costs that will follow the purchase.
How does mileage affect the operating cost of a vehicle?
Specific mechanical considerations also influence the total operating cost of a vehicle. Mileage, for example, is an important add-on expense, estimated by dividing the average number of miles driven, by the mean fuel requirements during the evaluation period. The prevailing cost of gas is then used to tabulate dollar-amount totals representing the gasoline costs added by your driving regimen.
What factors influence the cost of buying a car?
Several factors influence the cost of buying cars, including principal and interest. Even if you pay cash for your vehicle, the purchase price must be amortized, to determine monthly operating costs associated with the original purchase.
Is insurance an expense?
Insurance is an oft-forgotten vehicle expense, surprising some car buyers who fail to assess it in advance. Vehicle make and model, as well as the area where it is housed, each impact the total annual insurance payment required. Performance and luxury vehicle owners expect to pay the highest premiums.
Is repair and maintenance an operating burden?
Though they are harder to predict than other automobile operating costs, repair and maintenance expenses place an operating burden on vehicles too. For the most accurate assessment, estimate anticipated costs, to plug-in to operating cost calculator.
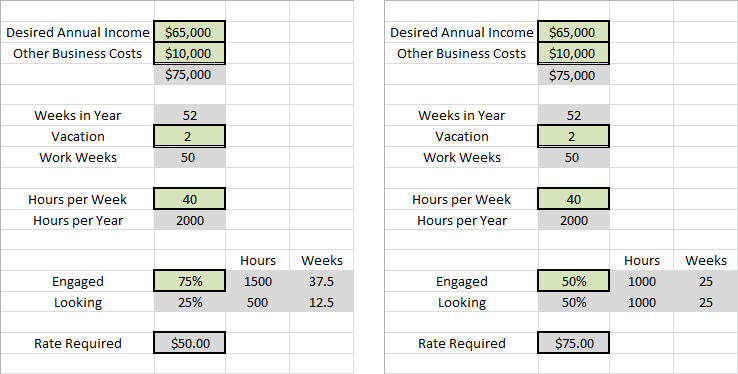
Machine vs Production Costs
- Industrial machinery costs and production costs are figures necessary for the successful operation of a manufacturing business. In order for a company to be profitable, the product it manufactures must generate more revenue than it costs to produce it. Companies then must evaluate their total expenses with a degree of accuracy and confidence to achieve profitability. Machine vs. producti…
Explanation of Fixed and Variable Costs
- The annual operating cost of industrial machinery is part of a broader equation that is affected by two distinct types of costs, fixed and variable. Where one cost is a certain amount, the other can fluctuate. Fixed costs remain the same even as the volume of production rises or falls. Variable costs do not. Such costs increase or drop with the volume of production. A good example of eac…
Calculating Hourly and Annual Costs
- The cost of running a machine per hour factors into its yearly cost. The objective here is to arrive at a figure that represents a reasonable estimate of the cost of operating the machine. Knowing the cost is as much about managing it as it is a primary method of absorbing factory expenses to that of production. The difference between calculating h...
Unexpected Costs
- Unexpected costs are those unplanned or hidden costs that can lead to a setback or delays in production that affects a company’s bottom line. Downtime due to a machine breaking down is a good example of an unexpected cost. Reliability of industrial machinery is a must. Another example is during machinery changeovers. More a hidden cost than unplanned, when the same …