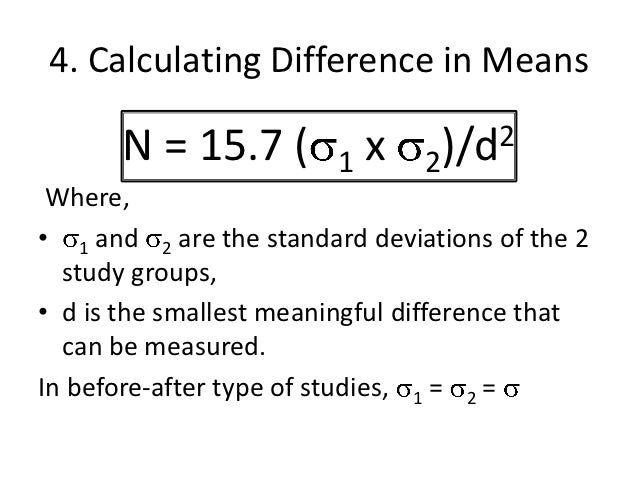
The Average Order Size Formula is: Dollar Amount Spent By Customers ÷ Number of Tickets = Average Order Size As an example, if you wanted to calculate your average order size for the past seven days, where you made $150,000 on 1,000 tickets, your average order size would be $15. $150,000 Weekly Sales ÷ 1,000 Tickets = $15 Average Order Size
Full Answer
How do you calculate optimum order quantity?
Order Quantity Formula To calculate the optimum order quantity "Q," take the square root of the following: "2N" multiplied by "P" and divided by "H." "N" is the number of units sold per year, "P" is the cost to place one order and "H" is the cost of holding one unit of inventory for one year.
What is the ideal order size for an economic order?
Economic Order Quantity is Calculated as: EOQ = 2.2360 Hence the ideal order size is 2.2360 to meet customer demands and minimize costs. It is also the reordering point at which new inventory should be ordered.
How does the size of an order affect the cost?
As explained by the economic concept known as economies of scale, the cost per unit of ordering a product falls, the larger the total quantity of the order. However, the larger the total quantity of an order, the higher the cost to hold and carry your inventory. Determine the order cost (incremental cost to process and order)
What is the ideal order size for inventory management?
Hence the ideal order size is 14.142 to meet customer demands and minimize costs. It is also the reordering point at which new inventory should be ordered. Let’s say for Maruti Suzuki Limited, it wants to determine the economic order quantity for its operations to minimize inventory costs and better cash flow management.
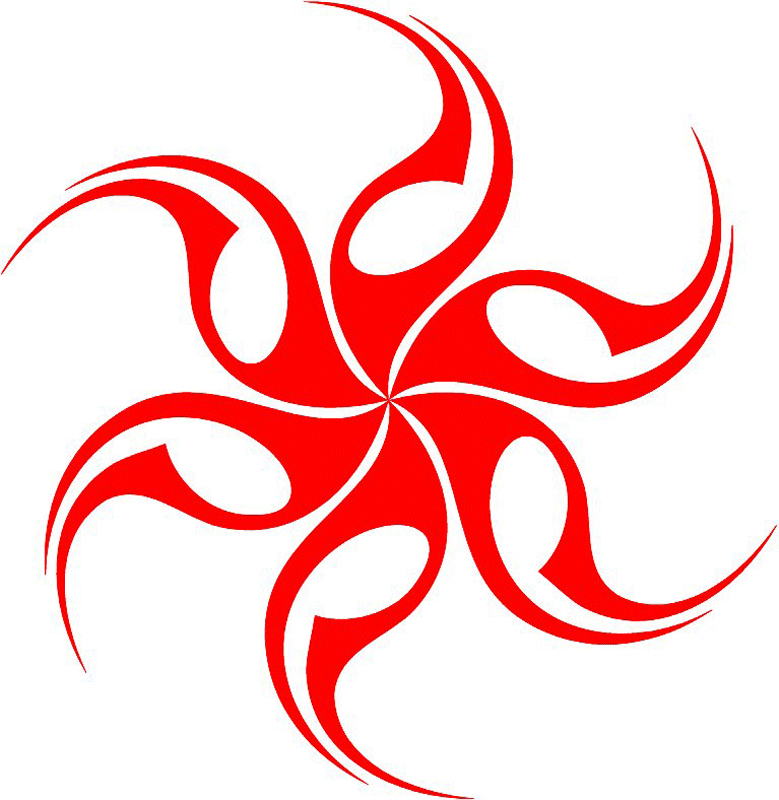
What is order size?
Order Size means the total Purchase value per Order.
How do you calculate suggested order quantity?
InformationSOQ (Suggested Order Quantity) = Order Up to Level - Balance.OUTL (Order Up To Level) = Safety Stock/Presentation Stock + Lead Time + (Greater of) Source Order Cycle or Item/SKU Order Cycle.Available Balance = On Hand + On Order - Back Order - Quantities Reserved or Held.
What are ordering costs How are they calculated?
Ordering cost formula example Since the annual demand is 10,000 units, the business needs to place 10 orders throughout the year. With this information, business executives determine the total order cost for the year is $10,000, since 1,000 x $10 in the formula results in $10,000.
How do you calculate the number of orders in a year?
The number of orders in a year = Expected annual demand/EOQ. Total annual holding cost = Average inventory (EOQ/2) x holding cost per unit of inventory. Total annual ordering cost = Number of orders x cost of placing an order.
What is the optimal order size?
Optimal order quantity is a calculation that determines the most cost-effective amount of inventory for your company to purchase. Essentially, this calculation represents your ideal order size to meet demand without overspending on excess stock.
How do you calculate reorder point?
In order to calculate reorder point, a business has to know the average unit sales per day, the average lead time and the amount of safety stock they have on hand. Multiply the average unit sales by the average lead time, then add the safety stock quantity to calculate your reorder point for a specific item.
What are the 3 types of ordering costs?
Ordering, holding, and shortage costs make up the three main categories of inventory-related costs. These groupings broadly separate the many different inventory costs that exist, and below we will identify and describe some examples of the different types of cost in each category.
What is the example of ordering cost?
Examples of order costs include the costs of preparing a requisition, a purchase order, and a receiving ticket, stocking the items when they arrive, processing the supplier's invoice, and remitting the payment to the supplier.
What is the formula of total cost?
Consequently, total cost is fixed cost (FC) plus variable cost (VC), or TC = FC + VC = Kr+Lw.
How do you calculate the time gap between two orders?
Order cycles per year are calculated by dividing the annual demand D by the order quantity Qo. An order cycle is the amount of time between when an order is placed and when the next order after it is placed. The cycles per year are simply the total number of order cycles completed in one year.
How do you calculate the average inventory?
To calculate the average inventory over a year, add the inventory counts at the end of each month and then divide that by the number of months. Remember to also include the base month in fiscal year average inventory calculations which also means you would divide that sum by 13 months rather than 12.
How do we calculate the quantity when purchasing a product locally?
The quantity might be per item or per unit of measurement, such as ounces, grams, gallons, or liters. To calculate the unit price, simply divide the cost of the product by the quantity you're receiving or check the store's shelf label.
How do you calculate optimal order quantity in Excel?
Economic Order Quantity or EOQ can be defined as the optimum level of quantity and frequency of orders for a particular level of demand....Economic Order Quantity = √(2SD/H)Economic Order Quantity = √(2SD/H)EOQ = √2(10000)(2000)/5000.EOQ = √8000.EOQ = 89.44.
What is a suggested order?
The Suggested Order is the total amount of the item to be placed on a purchase order to a vendor or on a transfer requisition to an Asset Location. This value is calculated by the Response Formula based on the information maintained for the item in the inventory at a particular Asset Location.
What is the formula for quantities of materials for concrete?
Calculation Of Materials For Different Mix Ratio:Volume of dry concrete = 1 × 1.54 = 1.54 m3.Formula, Cement = (Volume of dry concrete/a+b+c) × a.Formula, Sand = (Volume of dry concrete/a+b+c) × b.Formula, Aggregatess = (Volume of dry concrete/a+b+c) × c.Required water for 1 bag cement=0.0159 × 1000 = 15.9 Litre.More items...
How do I calculate quantity in Excel?
Use the COUNT function to get the number of entries in a number field that is in a range or array of numbers. For example, you can enter the following formula to count the numbers in the range A1:A20: =COUNT(A1:A20). In this example, if five of the cells in the range contain numbers, the result is 5.
What is upselling in a restaurant?
Upselling is when your servers guide guests towards purchasing a more expensive version of an item. This includes things like subbing regular fries for sweet potato fries for a dollar more, or upgrading their cocktail from well liquor to its top-shelf counterpart.
What does "make it easy for guests to customize items" mean?
Make it easy for guests to customize items: This includes all possible substitutions, additions, sides, and allergy restrictions. Your servers have the greatest knowledge of what most people ask for in terms of customization, so make sure to get their input when building your online ordering menu.
How to increase average order size?
Another key component of successfully increasing average order size by upselling and cross-selling is ensuring that your servers know the ins and outs of your menu, as well as some general food and alcohol knowledge.
How much does upselling increase revenue?
According to Sumo, upselling and cross-selling can increase revenue by 10-30% on average. Upselling and cross-selling are similar – they are both ways to encourage customers to order more than they initially intended – but there are two distinct differences.
What is cross selling?
Cross-selling is when a server suggests an additional item that pairs well with what the guest has already ordered, like suggesting a wine to pair with their dish or recommending a dessert when the guest has just ordered a coffee after their meal.
What is average order size?
Your restaurant’s average order size, sometimes also called “average order value,” is the dollar amount spent by your customers, divided by the number of tickets in a given time period.
Can servers cross sell desserts?
Alternately, if a guest seems in a hurry, your servers won’t want to waste their time cross-selling them on desserts or apps , but this does provide an opportunity to recommend a dish that comes out of the oven quickly (and has a higher profit margin than most other dishes.)
Why is the EOQ important?
The EOQ helps companies minimize the cost of ordering and holding inventory. As explained by the economic concept known as economies of scale, the cost per unit of ordering a product falls, the larger the total quantity of the order. However, the larger the total quantity of an order, the higher the cost to hold and carry your inventory.
What is EOQ in inventory?
The EOQ is usually used to set the reorder point within your inventory management workflows. Together, these metrics tell you when to place an order (reorder point) and how much order to place (EOQ formula). This prevents you from carrying too much deadstock or facing stockouts.
What is economic order quantity?
The economic order quantity (EOQ) is the order quantity that helps minimize holding costs and order costs for your business. Use the EOQ formula to start optimizing your inventory costs.
What does D mean in a product?
D represents demand, or how many units of product you need to buy.
What is fixed cost?
Also known as fixed cost. This is the amount you have to spend on setup, process, and so on.
Why is economic order quantity important?
Economic Order Quantity is one of the important tools used by companies in cash flow planning for minimizing the cost of inventory or decreasing the amount of cash held up in inventory. This is because for some companies such as FMCG companies have inventory as their largest asset and they need to be properly planned such that sufficient inventory is present for catering to customers but at the same time, it should be minimized so that cost savings can happen for the company. The Economic Order Quantity helps in estimating that level of inventory.
Why does Unilever want to determine economic order quantity?
Let’s say for Hindustan Unilever Ltd. it wants to determine economic order quantity for its operations to minimize inventory costs and better cash flow management.
What is economic order quantity?
Economic Order Quantity is used to determine the optimum level of quantity and frequency of orders for a given level of demand. The optimum level is determined while minimizing the cost per order. The key components of the Economic Order Quantity formula are: –
What is the ideal order size?
Hence the ideal order size is 2.2360 to meet customer demands and minimize costs. It is also the reordering point at which new inventory should be ordered.
How to determine number of orders?
Number of orders – Number of orders is determined by dividing annual quantity demanded with a volume per order.
What is holding cost?
Holding Costs – Holding costs are the variable costs associated with storing the products in inventory. Holding costs would also be defined as opportunity costs of investing the money somewhere else rather than putting it in buying inventory.
How to calculate your dress size?
Let's find out how to measure dress size... It's really easy! You just need to know three body measurements:
What size dress does Ann wear?
Once she input all necessary information into dress size calculator, she finds out that: Ann wears size 10 in the USA. She should go for a dress size 14 in the UK. In Europe, Ann should choose size 42 when buying a dress. The international symbol for her dress size is M.
Do you need a jacket if it's not warm?
Don't worry if it's not so warm and you need a jacket 🧥. Check the jacket size calculator to find a perfectly fitting jacket; and
Do you have to go from the top to the bottom?
Tip: You don't need to go from the top to the bottom.
Why is the reorder point important?
Reorder points ensure that you don’t fall behind on your next batch of inventory. With an accurate reorder point for each SKU, you’ll always have enough stock on hand to satisfy customer demand — without tying up excess capital in inventory.
What is Shipbob software?
ShipBob is an order fulfillment solution that features built-in inventory management software, giving you precise control over your inventory. You can check inventory counts at each fulfillment center and set automatic reorder levels, so you are notified when stock is running low.
What is a ROP in inventory?
The reorder point (ROP) is the minimum inventory or stock level for a specific product that triggers the reordering of more inventory when reached. When calculating the reorder points for different SKUs, the lead time it will take to replenish inventory is factored in to ensure inventory levels don’t reach zero.
What is Shipbob dashboard?
When you outsource fulfillment to ShipBob, all of your data is centralized in one place: your dashboard. Our software tracks purchasing trends over time to help you with inventory forecasting based on seasonal trends and more.
Why is it important to calculate reorder points?
Establishing reorder points frees up crucial capital and ensures your business is operating at maximum efficiency across inbound and outbound logistics. The most important and sometimes hardest part of calculating reorder points accurately is that you need reliable data for supply chain planning and provide an accurate picture of customer demand. If the data is off, then the calculation will be inaccurate and you may end up with too much or too little stock.
Why is maintaining inventory important?
Maintaining proper inventory levels is an elegant dance that must balance consumer demand and supplier reliability. Storing too much inventory eats up your budget in terms of warehousing costs and available capital, but you also need enough inventory to account for unexpected demand or supply problems.
How to find demand during lead time?
To find demand during lead time, just multiply the lead time (in days) for a product by the average number of units sold daily:
How to calculate sample size?
To calculate sample size, first find the population size, or number of people taking your study, and margin of error, which is the amount of error you'll allow in your results. Then, calculate your confidence level, which is how confident you are in percentage terms that your results will fall within your margin of error, and z-score, a constant value linked to your confidence level. Next, specify your standard of deviation, which is the amount of variation you expect in your results. Finally, plug your variables into the standard formula to figure out the sample size. To learn how to create a formula for unknown populations, read on!
What is the confidence level?
Set your confidence level. Confidence level is closely related to confidence interval (margin of error). This value measures your degree of certainty regarding how well a sample represents the overall population within your chosen margin of error.
What is margin of error?
The margin of error is a percentage the indicates how close your sample results will be to the true value of the overall population discussed in your study.
How to replace variables in a survey?
Plug your values into the equation. Replace each variable placeholder with the numerical values chosen for your survey.
What is the margin of error in polling?
In this example, the margin of error essentially indicates that, if the entire population were asked the same poll question, you are “confident” that somewhere between 30% (35 - 5) and 40% (35 + 5) would agree with option A.
What is wikihow similar to?
wikiHow is a “wiki,” similar to Wikipedia, which means that many of our articles are co-written by multiple authors. To create this article, volunteer authors worked to edit and improve it over time.
How does wikihow mark an article as reader approved?
wikiHow marks an article as reader-approved once it receives enough positive feedback. In this case, 92% of readers who voted found the article helpful, earning it our reader-approved status.
