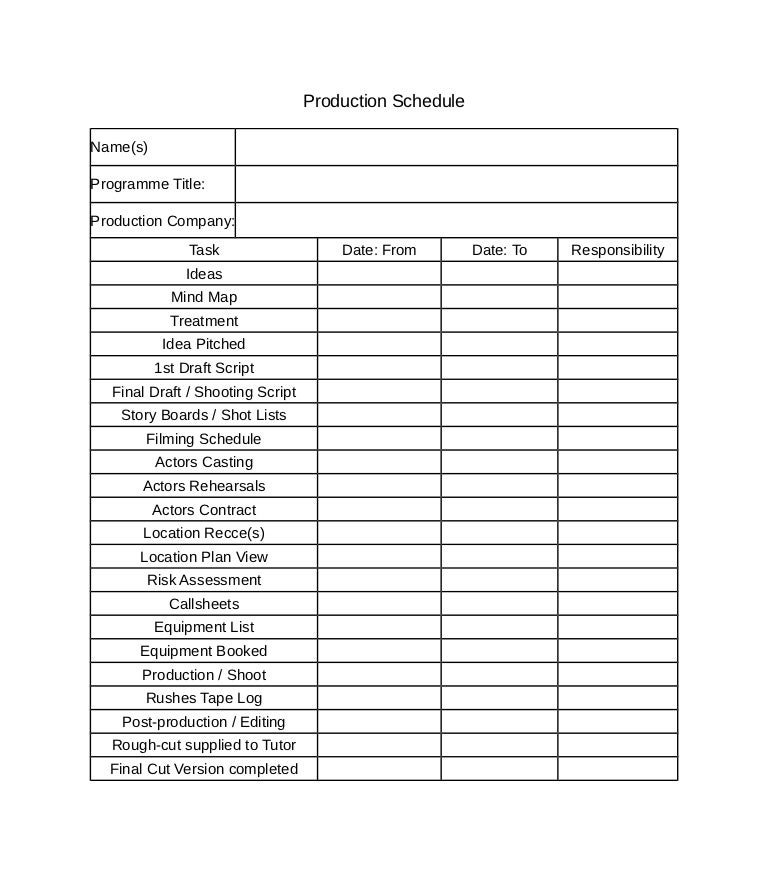
You can divide the total number of units produced by plant operating time to calculate the average production rate. Use this value to multiply by total downtime and find the total number of units you failed to produce during planned production hours. Plant Uptime = plant run time (production) / Total available time to run or produce
How do you calculate production time calculator?
Production Time Calculator. The production time for a manufacturing process is primarily determined from the cycle time, but must also account for the defect rate, machine uptime, and machines used. Using these parameters, the run quantity, run time, down time, total production time, and production rate (parts/hr) will be calculated.
How do you calculate the cost of production?
Such costs typically comprise of costs that can’t be attributed to the production process but indirectly impacts the production. Such costs can be bifurcated into indirect labor costs, indirect material costs, and variable costs on overhead. Next, add the resulting value in step 1, step 2, and step 3 to arrive at the cost of production.
What are the parameters used to calculate the production time?
Using these parameters, the run quantity, run time, down time, total production time, and production rate (parts/hr) will be calculated. The production time does not include the time for any initial setup or post-processing operations.
What are the different types of production scheduling?
Scheduling can fall into three types: Master production schedule: A master schedule is a plan for manufacturing a product within a specific time frame. It includes elements such as personnel, budget, routing processes and resources.
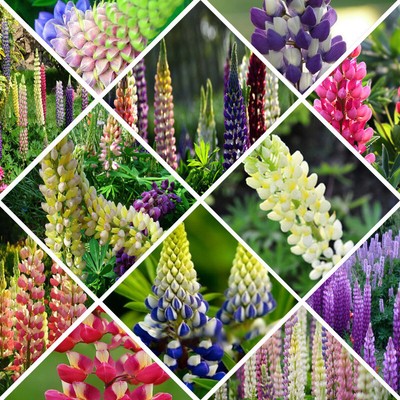
How do you make a production schedule?
Creating a Production ScheduleRead Over the Script. ... Use Breakdown Sheets. ... Estimate the Length of Production. ... Under-Schedule Each Day. ... Keep Your Cast and Crew in Mind. ... Schedule Difficult Scenes First in Production. ... Avoid Abruptly Shifting Emotional Gears. ... Shoot Chronologically Whenever Possible.More items...•
What is production schedule example?
An example of a master production schedule (MPS) for manufacturing is usually a spreadsheet that contains a production plan consisting list of sales orders, from purchase orders and sales forecasts, and specific time periods that they will be produced within a 3 to 12-month time horizon.
How do you calculate the production?
Cost of production or cost price or production costs can be calculated by adding all direct and indirect costs of a manufacturing unit. Here is the formula of calculating cost of production. Total cost of production= Cost of labor Cost of raw materials ie Overhead costs on manufacturing.
How is master production schedule calculated?
1:1812:32What is Master Production Schedule MPS ? [MPS Calculation ... - YouTubeYouTubeStart of suggested clipEnd of suggested clipWe also need the inventory levels how much inventory. We have on hand we also need the customersMoreWe also need the inventory levels how much inventory. We have on hand we also need the customers order and we should also know the trucks and capacity. Which would be away of the inventory.
How do I create a production schedule in Excel?
1:313:07Master Production Schedule Excel Template Step-by-Step Video ...YouTubeStart of suggested clipEnd of suggested clipIn the initial inventory column input the projected amount of inventory that you'll be entering theMoreIn the initial inventory column input the projected amount of inventory that you'll be entering the period with in the week rows simply input your mps in the yellow. Row.
What are the 4 components of production scheduling?
Five Components of Production Scheduling1) Planning2) Routing.3) Scheduling4) Dispatching5) Execution
How do you calculate production productivity?
The basic calculation for productivity is simple: Productivity = total output / total input.
How do you calculate production capacity?
How to measure manufacturing production capacityMachine hour capacity = number of usable machines x hours employees can use machines.Hours to produce one product = number of products produced in a day / hours of operation.Production capacity = machine hour capacity / hours to produce one product.More items...•
How do you calculate productivity man hours?
Multiply the number of workers by the number of hours each one worked to calculate the number of man-hours your business used during that time period. In this example, multiply 10 workers by 160 hours per worker to get 1,600 man-hours. This means that you produced 50,000 pieces using 1,600 man-hours.
What are the 5 steps to production planning?
Production Planning in 5 StepsStep 1: forecast the demand of your product.Step 2: determine potential options for production.Step 3: choose the option for production that use the combination of resources more effectively.Step 4: monitor and control.Step 5: Adjust.
What is a production schedule in accounting?
What is a Master Production Schedule? The master production schedule (MPS) is a production plan that states which products will be manufactured, as well as their amounts and start dates.
What is production schedule in Business plan?
Production scheduling is the allocation of available resources to production processes and events. It is essentially the mapping of actual resources to the production plan built for them. Scheduling is used to plan use of factory equipment and resources, human resources, and to plan processes and material purchasing.
What does production schedule mean?
The production schedule is a project plan of how the production budget will be spent over a given timescale, for every phase of a business project.
What is an example of a production process?
This process is a production activity that processes raw materials by combining them into a finished product. An example is the car production process, where car parts are made separately, starting from the steering wheel, frame, engine, tires, and so on.
What is production schedule in business plan?
Production scheduling is the allocation of available resources to production processes and events. It is essentially the mapping of actual resources to the production plan built for them. Scheduling is used to plan use of factory equipment and resources, human resources, and to plan processes and material purchasing.
What is a production schedule for an event?
What is a Production Schedule? The Production Schedule is the master timeline for coordinating live event production teams. It details what the various productions teams including audio, video, lights will be doing over the course of an event onsite.
What is a production schedule in manufacturing?
In manufacturing, a production schedule is a timeline set up to create the right amount of products to meet the demand within a timeframe. It helps you keep your costs low and avoid overproduction while still meeting your deadlines.
What is a solid production schedule?
For a manufacturer, a solid production schedule is the foundation of a healthy customer relationship.
What happens if you miscalculate when you need some materials in the production process?
If you miscalculate when you need some materials in the production process, that’s it. Production has to pause or pivot to another product until it arrives.
What is assembly to order?
Assemble-to-order: you only make the exact amount of production orders from your customers. Very common with perishable products, like finished food dishes. But it’s growing in popularity as a part of the Lean manufacturing movement, too.
Why do you need a reliable production schedule?
But to maintain steady production and good relationships with your customers , you need a reliable production schedule.
What are the most common strategies for a company?
Some of the most common strategies are level production, make-to-stock, and assemble-to-order. (There’s also the chase strategy, but we don’t recommend it.)
What is master production schedule?
Master production schedule (MPS) is a term used to describe a centralized document telling you what you need to produce, how much you need to produce, and when you need to produce it.
What is production planning?
Production planning, on the other hand, is the early stages of your manufacturing process where you’ll define the production levels, with limited and fewer details. The purpose of production planning is to determine the production of items, in terms of families or groups.
What is master schedule?
The master schedule helps you set your reorder points to make deliveries that need to be placed. You can do this by coordinating different management information systems such as marketing, finance, etc.
What is rough cut capacity planning?
Rough cut capacity planning with your master production schedule helps you figure out the realistic capacity you need to meet demand, increase profits, and minimize your costs.
Can you use ERP software to manage master production schedule?
Why not try out an automated master production schedule within your business with a 14-day free trial to see how much it can improve your production lines efficiency.
Does Katana have a master schedule?
However, Katana has been built with a master production schedule, which automates the tasks associated with your master schedule and streamlines the entire process. Katana’s MPS system is a steady flow, not a fire hydrant of data. It prioritizes your schedule, so you see what’s important, and of course, you can see everything at once too.
How to determine your Production Capacity?
There are several different ways for determining your production capacity.
What is Production Capacity?
Many small manufacturers are not aware of what their production capacity is. Often, they can give a rough estimate but cannot back it up with numbers. This is unnerving considering that many important business decisions depend on the company’s production capacity. Decisions based on estimations, however, are never as good as those based on cold, hard data.
What is the Capacity Utilization Rate?
The capacity utilization rate is an important KPI related to production capacity. It shows how much of a company’s production capacity is being used, and how much is left unused. The figure is presented as a percentage.
How to determine capacity for a future period?
To accurately determine your capacity for a future period, detailed planning must be done. Manufacturing of each product must be broken down to a sequence of operations, workstations and their individual availability must be defined, setup times need to be measured, materials’ availability and lead times must be considered, as well as any other details that may affect the schedule.
What is capacity planning?
Capacity planning and scheduling – an approach for accurate shorter-term planning.
Why is it important to know your production capacity?
Knowing your production capacity gives you the chance to improve production planning and production scheduling, give more accurate lead times, and forecast your cash flow. Theoretically, capacity is a certain number that tells you how much your factory could produce. But practically, how much you can output is almost never a fixed number.
When does outsourcing work?
Outsourcing production. This can be done when your machinery is already working in full gear and cannot accommodate a capacity increase.
What is a master production schedule?
The master production schedule (MPS) is one of the most important processes in an enterprise resource planning (ERP) business system and therefore should have robust measurements to drive that performance and improvement. Several metrics can help with this goal.
Is there a separate schedule for each product line?
There is a separate schedule (and metric) for each product line in the business. Each schedule is locked at the end of each week for the following week (for measurement purposes only; schedule will actually be revised as necessary).
What is production rate?
The Production Rate Calculator computes the length, area, volume or generic units that can be processed, produced or consumed over a period of time base on a constant rate. It also computes the amount of time needed to process, produce or consume a total length, area, volume or number of generic unit based on a total number and a constant rate.
What are units and time?
Units and Time. Units can be anything: student papers that are graded, applications that are processed, cars that are assembled, eggs that are laid, virtually anything. For example, a unit could be a box of clothes and the time to process a box of clothes would be the time.
How is concrete produced?
Concrete is produced by the cubic yard. Milk is produced by gallon or liter. Corn is produced by the bushel and oil by the barrel. This calculator handles 23 different units of volume and their interaction with time.
How much corn can you harvest in 12 hours?
Use the Area over Time function with the Unit Area (uA) equal to 3 acres, the Duration of Production (dU) equal to 20 minutes and the Period of Production (P) equal to 12 hours. At a constant rate, your combine will harvest 108 ac res of corn in 12 hours.
How to calculate production cost?
The calculation of Production Cost Equation can be done by using the following steps: 1 Firstly, Determine the costs of direct material. Direct materials usually are composed of costs that are related to the procurement of raw materials and utilizing them to produce finished goods. 2 Next, determine the costs of direct labor. The cost of direct labor is usually composed of costs on labor costs and costs on manpower that are in line with the process of production. Such costs generally consist of wages, salaries, and the benefits the business compensates to the labor for delivering finished goods or services. 3 Next, Determine the costs of manufacturing. Such costs typically comprise of costs that can’t be attributed to the production process but indirectly impacts the production. Such costs can be bifurcated into indirect labor costs, indirect material costs, and variable costs on overhead. 4 Next, add the resulting value in step 1, step 2, and step 3 to arrive at the cost of production.
What is the production cost formula?
The production cost formula is composed of costs that the business or a company incurs in making finished goods or delivering specific services and includes typically direct labor, general overhead expenses, direct material expenses, or expenses on raw materials and supplies expenses.
Why is the determination of production costs important?
The determination of production costs formula is necessary as well as critical for the business to ensure the profitability of the business. Profitability Of The Business Profitability refers to a company's ability to generate revenue and maximize profit above its expenditure and operational costs.
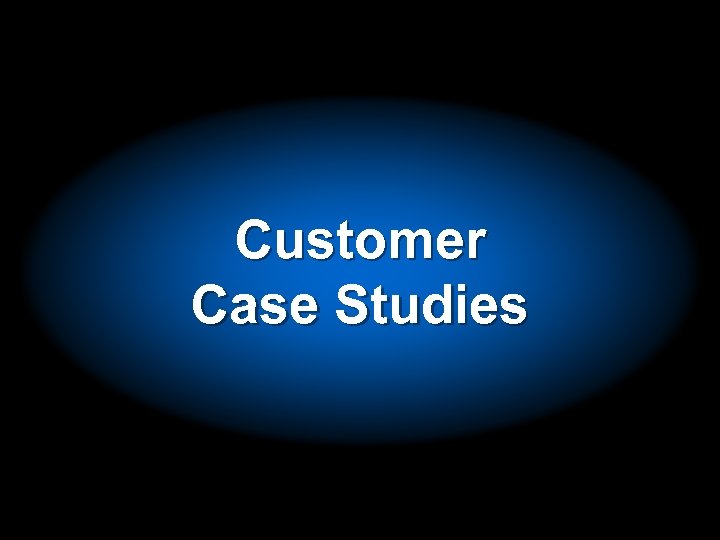