
How do you calculate production time?
- Available Minutes for Production / Required Units of Production = Takt Time.
- 8 hours x 60 minutes = 480 total minutes.
- 480 – 45 = 435.
- 435 available minutes / 50 required units of production = 8.7 minutes (or 522 seconds)
- 435 minutes x 5 days = 2175 total available minutes.
How do you calculate production?
How do you calculate production quantity in economics? Calculate EPQ In other words, calculate the EPQ by multiplying twice the annual demand by the setup cost per unit; dividing the product by the holding cost per unit multiplied by the inverse of daily demand divided by daily production ; and taking the square root of the result.
How many hours Am I working calculator?
you can use Microsoft Excel to calculate work totals, simplifying your payroll preparation. Especially when you deal with employees who go off the clock for breaks and meal hours, your daily ...
How to calculate takt time in production process?
This means a bulb to be completed every 4.8 minutes.
- In simple terms, it is how fast you need to manufacture products in order to fill your customer demand.
- Takt time calculation=Available time / customer demand. ...
- 8 hrs is the working time in your 9 hours working day (so you need to exclude your breaks, meetings etc) to mention the available time (numerator).
How do you calculate production schedule?
calculate the total production required. (Total Production = total forecast + back orders + ending inventory – opening inventory), calculate the production required each period by dividing the total production by the number of periods, and calculate the ending inventory for each period.
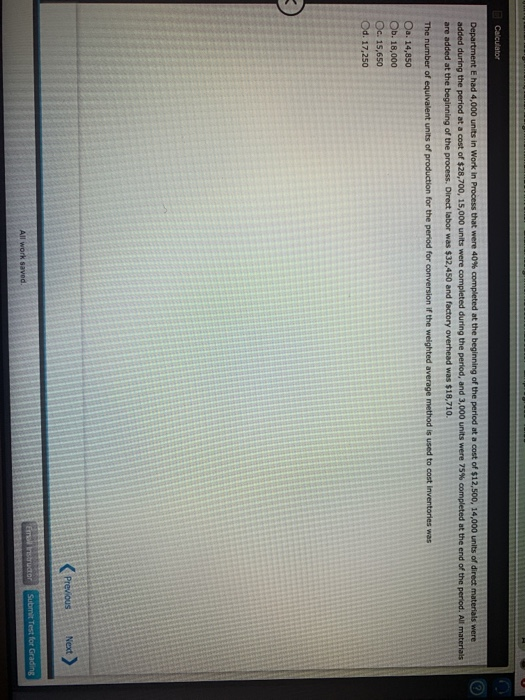
What is formula of average production time?
Calculating Production Rate Production rate is calculated simply by dividing your weekly output by the number of hours used to produce them. If a standard 50-hour week produces 10,000 units, then this would mean your production rate is 200 units per hour (10,000 / 50), including a few faulty units.
How do you calculate production minutes?
Cycle Time ConversionsOften, you will need to convert cycle times into another unit of measure. ... 1 / Minutes per Part = Parts per Minute. ... (1 / Seconds per Part) * 60 = Parts per Minute. ... (1 / Hours per Part) / 60 = Parts per Minute.
What is total production time?
The production time for a component is the total time required to produce a component and is composed of the following: (1) setup time Ts, which is the time it takes to load and unload each component and to return the tool to its starting point; From: Comprehensive Materials Processing, 2014.
What is production calculation?
Here is the formula of calculating cost of production. Total cost of production= Cost of labor Cost of raw materials ie Overhead costs on manufacturing.
How do you calculate production per day?
Determine how long it takes to produce one unit of product, then divide the daily plant capacity in hours by the time it takes to produce a product to arrive at the daily production capacity. For example, say it takes a worker half an hour (0.5 hours) on a machine to make a widget and the capacity is 800 machine hours.
How do you calculate man hours in production?
Multiply the number of workers by the number of hours each one worked to calculate the number of man-hours your business used during that time period. In this example, multiply 10 workers by 160 hours per worker to get 1,600 man-hours. This means that you produced 50,000 pieces using 1,600 man-hours.
How do you calculate productivity per hour in Excel?
Step 1: Locate a blank cell, we will use A2 as an example, and enter in the output value. Step 2: Locate a blank cell, B2, and put in the input value. Step 3: In a different cell, type out =A2/B2. Step 4: Press enter to confirm the calculation and the formula will be replaced with a value in the cell.
How do you calculate production hourly rate?
For example, let's say that workers at a manufacturing plant can produce 5,000 units per week using 50 hours of labor. As a result, the production rate per hour would be 100 units (5,000 / 50 hours) minus any defective units.
How do you calculate total production?
It is defined as the output per unit of factor inputs or the average of the total product per unit of input and can be calculated by dividing the Total Product by the inputs (variable factors).
How do you calculate production units?
The Formula for the Unit of Production Method Is Depreciation expense for a given year is calculated by dividing the original cost of the equipment less its salvage value, by the expected number of units the asset should produce given its useful life.
How do you calculate production capacity?
Production capacity can be calculated based on a single type of product or a mix of products....The formula used to calculate production capacity is:Factory machine capacity in hours divided by.Product SAM (how long it takes to produce one unit of product)Line efficiency (Average)
How do you calculate production in agriculture?
Total harvest of the plot is obtained by multiplying total number of units harvested by the average unit weight. Crop productivity can then be calculated by dividing total production by the area from where the production came from.
What is the meaning of production cost?
Definition of production cost : the combined total of raw material and direct labor costs and burden incurred in production.
Why is it important to calculate the cost of production?
The cost of production is an important factor for businesses to consider when assessing their financial health. If a product's cost of production is consistently higher than the profits it earns, the company may need to cease production to stay within budget.
Which is the basic production function?
A production function relates the input of factors of production to the output of goods. In the basic production function inputs are typically capital and labor, though more expansive and complex production functions may include other variables such as land or natural resources.
What are units and time?
Units and Time. Units can be anything: student papers that are graded, applications that are processed, cars that are assembled, eggs that are laid, virtually anything. For example, a unit could be a box of clothes and the time to process a box of clothes would be the time.
How is concrete produced?
Concrete is produced by the cubic yard. Milk is produced by gallon or liter. Corn is produced by the bushel and oil by the barrel. This calculator handles 23 different units of volume and their interaction with time.
What is productivity in manufacturing?
In its most basic form, productivity is the measure of output versus input. In manufacturing, this relationship often takes the form of units produced compared to the number of man-hours required. The resulting ratio offers a measure of productivity, but it's only useful when you have a comparison or an expected value.
What is the number of pieces produced?
The number of pieces produced is simply a total in the period of time you wish to evaluate, such as an annual, monthly, weekly or daily period. If you wish to establish an average number of units produced per man-hour for comparison purposes, count all units produced by all employees. If you need to evaluate a single employee, only count the pieces produced by that employee.
What is normal costing?
Normal Costing. In its most basic form, productivity is the measure of output versus input. In manufacturing, this relationship often takes the form of units produced compared to the number of man-hours required.
How to calculate production cost?
The calculation of Production Cost Equation can be done by using the following steps: 1 Firstly, Determine the costs of direct material. Direct materials usually are composed of costs that are related to the procurement of raw materials and utilizing them to produce finished goods. 2 Next, determine the costs of direct labor. The cost of direct labor is usually composed of costs on labor costs and costs on manpower that are in line with the process of production. Such costs generally consist of wages, salaries, and the benefits the business compensates to the labor for delivering finished goods or services. 3 Next, Determine the costs of manufacturing. Such costs typically comprise of costs that can’t be attributed to the production process but indirectly impacts the production. Such costs can be bifurcated into indirect labor costs, indirect material costs, and variable costs on overhead. 4 Next, add the resulting value in step 1, step 2, and step 3 to arrive at the cost of production.
Why is the determination of production costs important?
The determination of production costs formula is necessary as well as critical for the business to ensure the profitability of the business. Profitability Of The Business Profitability refers to a company's ability to generate revenue and maximize profit above its expenditure and operational costs.
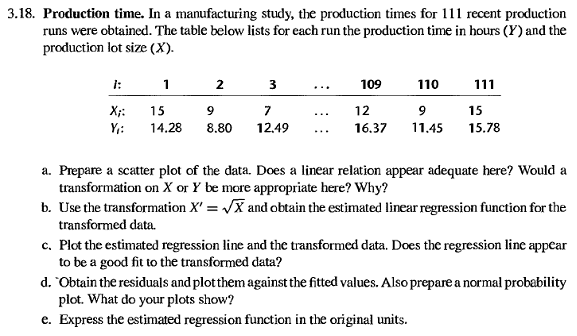