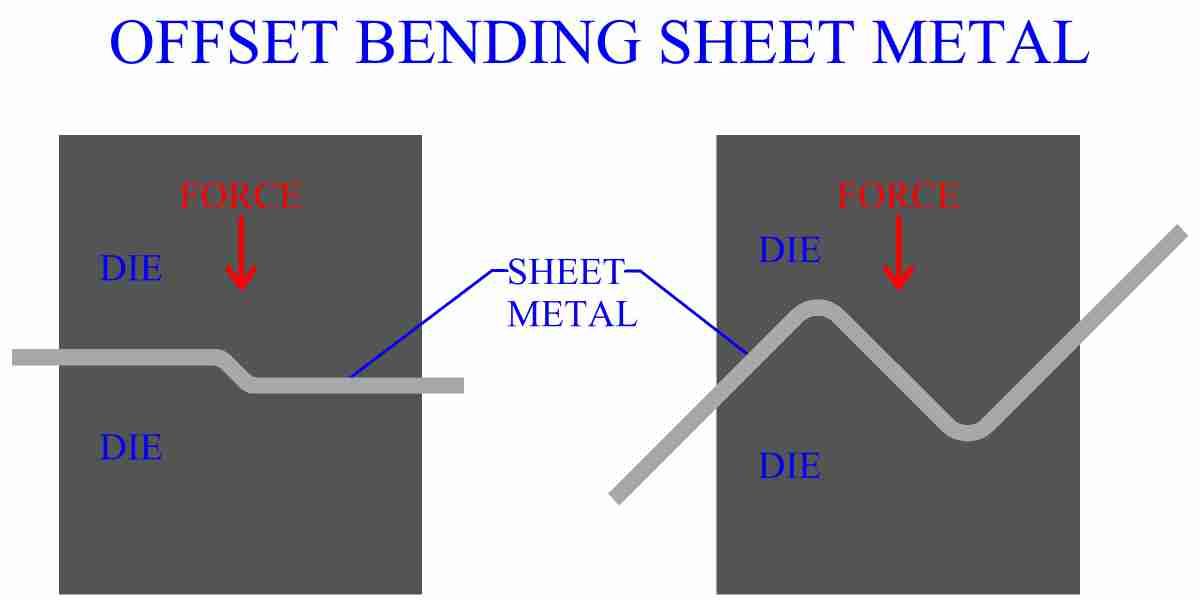
The simple, convenient and rough method is:
- Generally, when the plate thickness is not more than 6mm, the bending radius in the plate can directly take the plate thickness as the radius during bending;
- When the plate thickness is greater than 6mm and less than 12mm, the bending radius in the plate is generally 1.25 to 1.5 times of the plate thickness;
How do you calculate the bend radius of sheet metal?
When the plate thickness is greater than 6mm and less than 12mm, the bending radius in the plate is generally 1.25 to 1.5 times of the plate thickness; When the plate thickness is not less than 12mm, the bending radius in the plate is generally 2 to 3 times the plate thickness.
How do you calculate the length of bending sheet metal?
Sheet Metal Flat Length CalculationStep-1: Calculate the value bend allowance for the required sheet metal bend by using the below formula.Bend Allowance (BA) = (Π/180) × ( R + K×T) × A.Step-2: Calculate the value of bend deduction from the values of bend allowance and outside setback.More items...
How is sheet metal bend deduction calculated?
Here's the formula: Bend deduction = (2 × Outside setback) - Bend allowance. With the bend deduction in hand, you can determine the appropriate flat blank size, and program the press brake so that the backgauge fingers accommodate for material elongation during each bend.
How do you calculate blank bending?
Flat-blank Calculation Calculated flat-blank length = 2.187 in. For overbent angles (see Figure 3), the original formula—OSSB = [Tangent (degree of bend angle complementary/2)] × (Material thickness + Inside radius)—also may be written using the included degree of bend angle.
How do you calculate a 90 degree bend?
0:111:24Calculation of compound 90 degree Bends - YouTubeYouTubeStart of suggested clipEnd of suggested clipMake pencil marks on the conduit at the measured distances align the pencil mark on the conduit.MoreMake pencil marks on the conduit at the measured distances align the pencil mark on the conduit. With the center of the bend.
What is the K-factor formula?
Mathematically, K = (180×BA) / (π×θ×T) − (Rᵢ/T) .
What is sheet metal bend allowance?
Bend allowance is defined as the material required to add to the overall length of the sheet metal in order for it to get cut in the right size. Density in metals can be measured in GPa, or gigapascal. The more gigapascal in a material, the stiffer it is.
What is the formula for 135 bend?
For example, if the length of the bar is 12 m (assume), the diameter is 25 mm. So for one bend, it is deducted by 3d as it is 135 degrees bend. i.e. Cutting Length = 12- 3d= 12- 3*0.025= 11.925 m.
Why bend deduction is calculated?
Considering the Bend Deduction and Bend Allowances is a critical first step in designing sheet metal parts as it affects nearly every following step in the fabrication process. More so, it will allow you to achieve the correct size and dimensions needed in the flat pattern.
Why is K factor used in sheet metal?
K- and Y-factors make metal bending more precise without damaging the material. Once you know the K-factor you can identify the location of the neutral axis after bending in addition to how much the material elongates during bending.
How do you calculate development length of a bend sheet?
We go better with a practical example; with a thickness of 1,5 m/m and to calculate the development of the following sheet (see sketch) we will do the next calculation: 70 – (2 x 1,5) + 25 – (2 x 1,5) + 15 = 104 m/m is the length of the piece (before being bended).
How do you calculate development length?
Calculation of Development length: **Note: For bars in compression, 1.25 times the above given values shall be used. Generally, in practice, the development length requirement is expressed as '41 times Ø'or '41 Ø' where 41 is the factor calculated using the above formula& Ø is the dia of the bar.
How do you measure the length of a bent tube?
So, if the hose goes around a 90˚ bend, which is 1/4 of a full circumference, and the radius of the bend is R, then the length of the hose around the bend is = 1/4 x 2πR.
How do you calculate the length of a blank?
0:504:31Calculating Blank Size for Rolled Sheet Metal (Screencast) - YouTubeYouTubeStart of suggested clipEnd of suggested clipMean times pi equals cut length to determine our blank.MoreMean times pi equals cut length to determine our blank.
Instructions
Input material thickness and and inner radius to get the data of K factor, Y factor, neutral layer.
Want to get the price of our press brake?
Our sales team will recommend the most suitable press brake machine for you according to your practical needs. Trust me!
About The Author
Hi, I'm Shane—founder of MachineMfg. I have worked in the metalworking industry for more than 10 years. I do a lot of thinking, reading, and writing around sheet metal fabrication, machining, mechanical engineering, and machine tools for metals.
What is sheet metal bending?
Sheet metal bending is a forming operation where sheets are deformed plastically to change their shape. During sheetmetal bending, the material is stressed beyond its yield strength but below the ultimate tensile strength. After bending a sheet metal part, the total length of sheet metal is more than the flat length.
What is Bend Deduction in Sheet Metal?
During sheet metal bending, the inside surface of the bend is compressed and the outer surface is stretched. Which increases total outer surface area. In other words, after bending, the total sheet-metal part length (A + B) will be greater than the sheet metal Flat Length.
What is K Factor in Sheet Metal?
K Factor in sheet metal bending is a constant that is used to calculate sheet metal flat length. Its value is a constant for a given material, thickness, and machine. The value of K-Factor may vary from machine to machine as well.
What is the mathematical bend deduction?
Mathematically Bend Deduction is equal to the difference between the total sheet metal length after bending and flat length.
How are sheet metal bend allowance and bend deduction related?
Sheet Metal Bend allowance and bend deduction are directly related to each other. Mathematically the sum of bend allowance and bend deduction is equal to two times of outside setback.
What happens to the inside of a sheet metal bend?
During sheet metal bending, the inside bend surface is compressed whereas the outer bend surface is stretched. Somewhere in between the thickness of material lies a neutral axis where the material is neither compressed or stretched.
What is the value of the inside bend radius?
The value of the inside bend radius depends on the bending tool and die. Generally, it is considered equal to sheet thickness.
Bend allowance and bend allowance charts
Sheet metal is one of the most commonly used materials in many industries, such as aircraft parts, construction, and automotive, to name a few. So, in order to accurately work with this material, we need to know how it behaves in different scenarios.
Bend deduction calculator
This calculator works as a bend deduction calculator as well! Below you will find its definition and formula.
Sheet metal bending calculation using the bend allowance calculator
Using the two formulas we have explained, the sheet metal bending calculation is simple. So far, in this text, we've covered:
What happens when you bend metal?
When the sheet metal is put through the process of bending the metal around the bend is deformed and stretched. As this happens you gain a small amount of total length in your part. Likewise when you are trying to develop a flat pattern you will have to make a deduction from your desired part size to get the correct flat size.
What is bend allowance?
The Bend Allowance is defined as the material you will add to the actual leg lengths of the part in order to develop a flat pattern. The leg lengths are the part of the flange which is outside of the bend radius.
Is sheet metal bending the same?
Unfortunately sheet metal bending is not always going to be the same in every shop. The largest variations come from the materials themselves. Protective coatings, variations in the alloy and thickness as well as many other small factors all add up to give you Bend Allowances unique to your operation. This chart will get you close enough for most applications and may not require fine tuning on your part, however if you are truly dedicated to precise bending, download the excel sheet and begin plugging in your own values.
What do you need to bend sheet metal?
If your sheet metal is too thick, you may need special machinery, like a brake or a torch, to bend your sheet into the desired shape.
How many inches to bend 24 gauge sheet metal?
As an example, if you want to bend 24 gauge sheet metal at a 90° angle, the calculation would be: 0.017453 x 90 x (0.020 + 0.33 x 0.024) = 0.0438558984 inch bend allowance
What happens if you solve the bend allowance equation incorrectly?
If the equation is solved incorrectly, your sheet metal bend will be incorrect and your sheet metal could be ruined. Thanks! Helpful 1 Not Helpful 1.
How to find bend allowance?
To calculate the expansion that will take place on the outside of your bend angle, you will need to know your bend allowance. You can find your bend allowance with the following formula: (π/180) x B x (IR + K x MT) = bend allowance (BA), where B is the angle complementary to your desired bend angle (1 to 180 degrees), MT is the thickness of the material, IR is the inside radius, and K is the K-factor.
How to make a crease in sheet metal?
Apply an equal amount of force used to create the crease in the opposite direction of the crease. Yup, easier said than done. Once a piece of sheet metal is creased, its well neigh impossible to take the crease completely back out of it. In smaller pieces, I've had success tinkering out a crease with a hammer and a dolly, or on a hydraulic bench press sandwiched between two pieces of flat bar. In a large sheet, a long piece of flat bar could be used as a dolly and some careful tinkering, but the crease will almost always be noticeable. I used a forklift once to flatten out a piece of sheet with mixed results. Next time I'd want to sandwich the sheet between some flat bar first.
How to bend metal with a vise?
1. Gather your materials. Having the right tools on hand will help this process go smoothly and quickly. To bend your sheet metal with a vise and hammer, you will need: 2 wooden or metal form blocks. Block of hardwood and heavy- duty hammer or mallet (optional) Calculator or online bend calculator.
What happens if you bend a sheet of metal 90 degrees?
Did you size the sheet of metal to take into consideration the stretching of the metal at the bend? If you do a 90-degree bend, the metal will stretch and shrink the thickness of the metal.