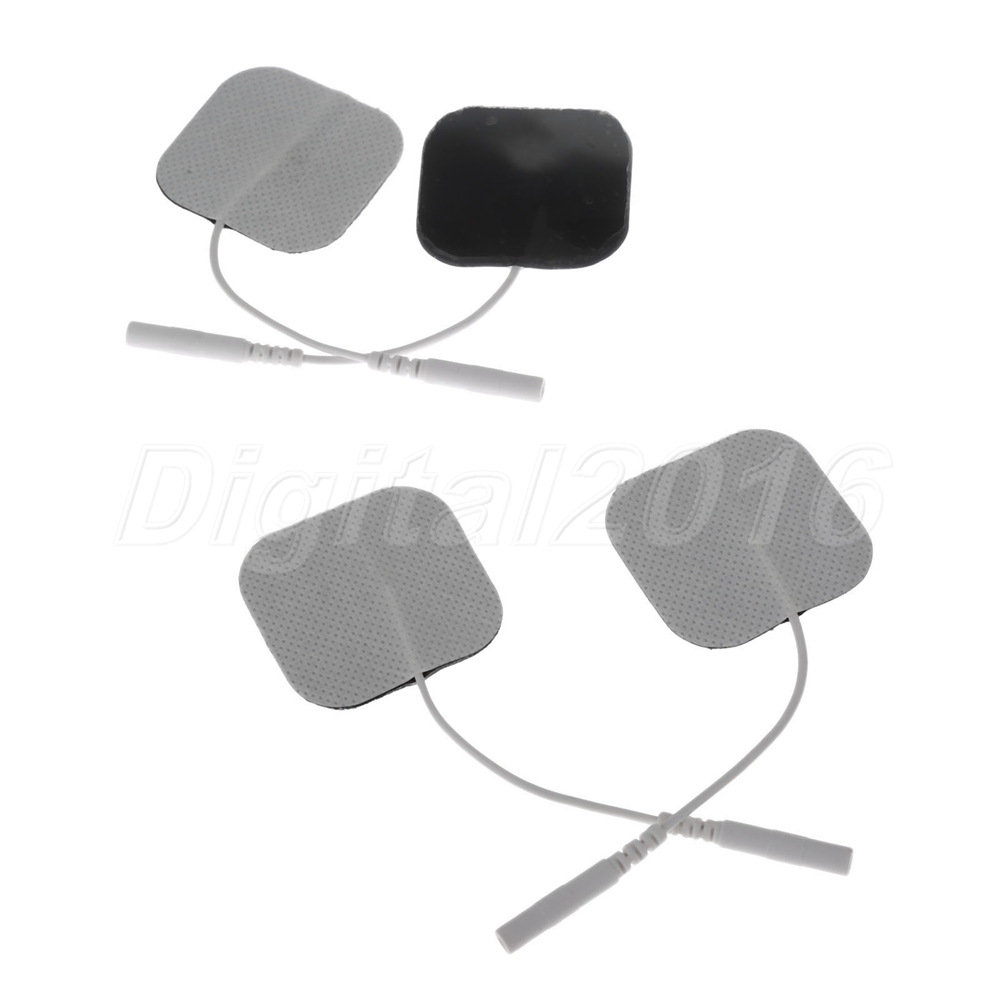
The impulse responses h (x, z) and the spatial transfer functions H (fx, fz) on the (x, z) plane, due to the physical size of a rectangular or circular electrode, are as follows: hsize (x, z) = 1 / S under the electrode area S and hsize (x, z) = 0 elsewhere (2) for a rectangular electrode of width a and height b and
How do you determine the welding current for a specific electrode?
To determine the correct current type for a particular electrode, refer to the fourth digit of the AWS classification, which represents the type of coating and type of compatible welding current (see Figure 1). Refer to the fourth digit of the AWS classification to determine the compatible welding current.
What size welding electrode do I need for 275 amps?
You can also use the specifications to determine the size that will provide the welding current that you require for the job. The higher the current, the bigger size of the electrode you need. For a 275 amps of current, you should use an electrode with 5/16 inches in diameter. A 1/16 inch diameter electrode will not be sufficient for the job.
What factors should you consider when selecting a stick electrode?
Factors you should consider when selecting a stick electrode include base metal type, joint fit-up and welding positions. Before you power up your machine and pick up your electrode holder, consider these basic guidelines. The first step in choosing an electrode is to determine your base metal composition.
How do I identify a stick electrode’s tensile strength?
You can identify a stick electrode’s tensile strength by referring to the first two digits of the AWS classification printed on the side of the electrode.

How do you select electrodes for welding?
Factors for Selecting the Right Stick ElectrodeBase metal properties.Tensile strength.Welding current.Base metal thickness, shape and joint fit-up.Welding position.Specification and service conditions.Environmental job conditions.
How do I know what size welding rod to get?
As a general rule, for single-side single-pass butt welds, up to 3/16″ metal thickness, you choose a welding rod that is a step thinner than the base metal. For example, if the base metal is 1/8″, you select a 3/32″ rod.
What are the common electrode sizes?
Common electrodes used in Stick welding are 6010, 6011, 6013, 7018 and 7024 with the most common diameters ranging from 1/8- to 5/32-in.
What are three common electrodes sizes?
Size: common sizes are 1⁄16, 5⁄64, 3⁄32 (most common), 1⁄8, 3⁄16, 7⁄32, 1⁄4, and 5⁄16 inches. Core wire used with electrodes needs to be narrower than the materials that are welded. Material: stick welding electrodes come in cast iron, high carbon steel, mild steel, iron-free (nonferrous), and special alloys.)
What size is a 7018 welding rod?
3/32"Product Description. AWS Classification: E7018 | Rod Diameter: 3/32" and 1/8" | Electrode Length: 12" and 14" | Polarity: DCEP and AC.
What do the 4 numbers on a welding rod mean?
The first two digits of a 4-digit number and the first three digits of a 5-digit number stand for tensile strength. For example, E6010 means 60,000 pounds per square inch (PSI) tensile strength and E10018 means 100,000 psi tensile strength. The next to last digit indicates position.
What determines the size of the stick electrode?
The diameter of the wire, less the coating, determines the size of the welding rod. This is expressed in fractions of an inch such as 3/32", 1/8", or 5/32." The smaller the diameter means it requires less current and it deposits a smaller amount of filler metal.
What is the meaning of E6013 in welding electrode?
Thus the number E6013 written on an electrode indicates that it is a rutile potassium based flux coated mild steel electrode with 62,000 psi minimum tensile strength having light penetration which can be used in all positions of welding except vertically down.
What do the numbers on electrodes mean?
The first two digits represent the resulting weld's minimum tensile strength, measured in pounds per square inch (psi). For example, the number 70 in a E7018 electrode indicates that the electrode will produce a weld bead with a minimum tensile strength of 70,000 psi.
What size is 6013 welding rod?
Compare with similar itemsThis item E6013 - General Purpose/Mild Steel - Welding Electrode/Rod - 12" x 3/32" (PACK: 5.5 LB)Blue Demon 6013 X 3/32" X 14" X 5LB Plastic General Purpose Carbon Steel ElectrodePrice$2440$1876Sold ByMUNDAKA TECHNOLOGIES, INC.Amazon.comAre batteries included?No—Item Weight5.70 lbs5.21 lbs3 more rows
What are the 3 types of electrode?
Science > Chemistry > Electrochemistry > Types of ElectrodesGas electrodes.Metal–sparingly soluble metal salt electrodes.Metal – metal ion electrodes.Redox Electrodes.
When to use 6010 or 7018?
E 6010 electrode can be used on painted, galvanized, and unclean surfaces, while E 7018 is used on clean or new sheet metal. E6010 is used for deep penetration welding, while E 7018 is used for welding metal that tends to crack, producing quality welds with excellent toughness and high ductility.
What is a 7018 welding rod used for?
Premium 7018 welding rods are designed for welding low, medium and high carbon steels and higher strength low alloy steels. This rod will give you reasonable control over the arc and minimize the post-weld mess.
When would you use a 6013 welding rod?
6013 welding rod has its applications in:General purpose fabrication.Shipbuilding and repair.Metal buildings and structures.Machine parts.Thin sheet metal welding.Shaft buildup.Welding of vehicles.Excessively machined and damaged mild steel.
When would you use a 6011 welding rod?
The 6011 welding rod is useful for jobs that require deep penetration, no matter the position or welder setup. It is a solid all-around welding rod. Because it is an iron rod, it is useful for most kinds of iron and mild steel. You can handle just about anything with 6011 rods.
What is the difference between 6011 and 7018 welding rods?
The 6011 and 7018 sticks have little in common. E7018 produces stronger joints and can handle high-carbon alloys, unlike the E6011 electrode. E7018 is a fill-freeze rod, so it has medium penetration and fill. The fast-freeze E6011 is well-known only for its deep penetration.
RWMA Class 1 (C15000 & C16200)
Also know as ZIRCONIUM-COPPER. This alloy is suited for high tempature applications such as welding aluminum & magnesium alloys. The Zirconium minimizes eletrode sticking when resistance welding coated materials. C15000 can be harder to find in larger sizes.
RWMA Class 2 (C18200 & C18150)
Also know as CHROMIUM-COPPER or ZIRCONIUM-CHROMIUM-COPPER. This alloy is suited to welding cold- and hot-rolled steels, stainless steel, and low conductivity brasses and bronzes.
RWMA Class 3 (C18000 & C17510)
NICKEL-COPPER (BERYLLIUM FREE) and BERYLLIUM-NICKEL-COPPER are suited to welding steels having high electrical resistance, such as stainless steel.
RWMA Class 20
COPPER-ALUMINUM OXIDE (Glidcop) has exceptional resistance to deformation when welding and it is highly recommended for weld caps when welding coated and galvanized steels. It allows a stable start-up and generally outlasts other cap material when welding parameters are not carefully controlled.
What is Elkonite?
Elkonite is a copper-tungseten ally. Elkonite comes in up to 12 different alloys and many shapes and sizes. Copper and tungesten are not mutially soluable. Each material (tungesten and copper ) is comprised of a distinct metal which is then dispersed in to the matrix of the other through infultration.
How to choose an electrode?
The first step in choosing an electrode is to determine your base metal composition. Your goal is to match (or closely match) the electrode composition to the base metal type, which will help ensure a strong weld. If you’re in doubt about the composition of your base metal, ask yourself these questions: 1 What does the metal look like? If you’re working with a broken part or component, check for a coarse and grainy internal surface, which usually means the base material is a cast metal. 2 Is the metal magnetic? If the base metal is magnetic, chances are good that the base metal is carbon steel or alloy steel. If the base metal is not magnetic, the material could be manganese steel, 300 series austenitic stainless steel or a non-ferrous alloy such as aluminum, brass, copper or titanium. 3 What kind of sparks does the metal give off when touched by a grinder? As a rule of thumb, more flare in the sparks indicates a higher carbon content such as in A-36 grade steel. 4 Does a chisel “bite” into the base metal or bounce off? A chisel will bite into a softer metal, such as mild steel or aluminum, and bounce off of harder metals, such as high carbon steel, chrome-moly or cast iron.
How to determine qualified electrode position?
Here’s how you decipher the qualified electrode position: 1 = flat, horizontal, vertical and overhead. 2 = flat and horizontal only. For example, a 7018 electrode can be used in the flat, horizontal, vertical and overhead positions.
What electrode to use for a groove weld?
You’ll also want to assess the joint design and fit-up. If you’re working on a joint with a tight fit-up or one that is not beveled, use an electrode that provides a digging arc to ensure sufficient penetration, such as an E6010 or E6011. For materials with wide root openings, select an electrode, such as an E6012, that creates a concave weld face suitable for bridging gaps and making groove welds.
What electrodes are used for deep penetration?
The type of current you use also influences the penetration profile of the resulting weld. For example, a DCEP compatible electrode , such as an E6010, delivers deep penetration and produces an extremely tight arc. It also has the ability to “dig” through rust, oil, paint and dirt. A DCEN compatible electrode, such as an E6012, provides mild penetration and works well when bridging two joints or welding high speed, high current fillet welds in the horizontal position.
What does 60 on an E6011 electrode mean?
For example, the number “60” on an E6011 electrode indicates that the filler metal produces a weld bead with a minimum tensile strength of 60,000 psi and, as a result, would work well with a steel of similar tensile strength. If playback doesn't begin shortly, try restarting your device.
How to determine tensile strength of stick electrode?
You can identify a stick electrode’s tensile strength by referring to the first two digits of the AWS classification printed on the side of the electrode. For example, the number “60” on an E6011 electrode indicates that the filler metal produces a weld bead with a minimum tensile strength of 60,000 psi and, as a result, would work well with a steel of similar tensile strength.
What electrodes are needed for thin materials?
For thin materials, you will need an electrode that produces soft arcs, such as a 6013. Also, smaller diameter electrodes will provide shallow penetration to help prevent burn-through on thinner materials.
Stick Welding Electrodes PDF Chart
In this welding rod chart, you will find over 220 stick electrodes classified according to the American Welding Society (AWS) code.
Welding Rod Sizes and Amperage Chart
We'll cover only mild steel rods for the shielded metal arc welding electrode size and amperage chart. If we covered all 220 electrodes as we did in the PDF above, the chart would have thousands of lines, which wouldn't be practical.
Stick Welding Rods Selection Guide
Choice of a stick welding electrode is often specified in the Welding Procedure Specification (WPS), but if you are new to stick arc welding, or the job doesn't define the electrode, this guide will help you make the right choice.
Commonly Used Shielded Metal Arc Welding Rods
Now let's take a deeper dive into each of the commonly used welding rods.
Conclusion
With over 220 electrodes with official classifications from AWS, it's difficult to digest everything in one take. The point of this article is to get you up to speed and provide the necessary detailed knowledge to understand stick welding electrodes with a focus on selecting the right for your needs.
What is the electrode used to make a weld?
The tungsten electrodes are used to produce the weld and then a filler metal is contributed to make the seal. The external filler metal is often a filler rod but the materials can vary. It is the electrode that produces the arc for the weld and really does the work.
What is a tungsten electrode?
Thoriated tungsten is a red color-coded electrode with a principal oxide of 1.7-2.2% thorium oxide. This has long been one of the universal go-to options for any metal and strength for DC compatibility.
How Do You Choose Tungstens Size?
If you’re a beginner and still working on getting familiar with the different techniques, we recommend that you start out using 3/32, which is 2.4 mm. This is the best option for beginners.
How many packs of tungsten electrodes are there?
When you choose a diameter, the Tungsten electrodes typically come in a 10-pack. You may find that you need several sizes but keep in mind the length is pretty standard while the diameter can vary.
What Lengths Do Tungstens Come In?
There are different lengths available but you will normally see a length of about 7 inches or 175 mm. It is the diameter that really makes the difference.
How to determine which electrode is best for the base metal?
You can determine which electrode is ideal for the base metal you’re using via the end digits on the electrode. For better understanding, use rods that end with 15, 16, or 18.
What happens if your electrodes don't match?
Tensile strength is a big deal when buying electrodes. If your rod’s tensile strength doesn’t match the base metal, you’re going to likely experience cracks , including other inconveniences that come with using rods with low tensile strength.
What type of rods do welders use?
However, consumable electrodes happen to be the most common type of rod out there. SMAW (Shielded Metal ARC Welders) and MIG (Metal Inert Gas) welders use them.
What is consumable electrode?
Consumable electrodes are electrodes that experience significant changes to their structure when used. What this means is that they melt during the welding process. And after melting, the consumable electrode mixes with the weld, making the bond holding both metals in place stronger.
Why is choosing the right welding rod size important?
So, choosing the appropriate welding rod size is crucial. That’s because choosing the wrong welding rod would produce a weaker weld. Consequently, all your efforts would be in vain.
Why should welding electrodes be ductile?
Why? Some may ask this question. Well, the reason is to ensure that the electrode doesn’t end up cracking.
What does 7028 mean on a welding rod?
If the welding rod reads 7028, the first two numbers (70) indicate the rod’s tensile strength. In this case, the rod’s tensile strength is 70,000 pounds per square inch.
Which thickness plate should be used for different thickness plates?
If the plates are different thicknesses, the thinner plate thickness should be used.
Can you double the leg size of a weld?
If a weld can only be made on one side of the plate, then the weld size should be doubled . The following table gives the leg size of fillet welds for various plate thicknesses based on the previous formula.
