
How to Perform a Life Cycle Cost Analysis
- Develop Design Alternatives. Identify and develop a minimum of two mutually exclusive options that serve the same purpose, with the assumption the only economic difference between alternatives is total cost.
- Determine Activity Timing. ...
- Estimate Costs. ...
- Compute Life Cycle Costs. ...
- Analysis. ...
- References. ...
When is the best time to reduce life cycle cost?
The best time to reduce life-cycle costs is early in the acquisition process. ... The cost of the full-rate production item constitutes a significant portion of the life-cycle cost of the DOGWOOD program, which is in the later portion of the Technology Maturation and Risk Reduction phase. One of the alternatives being explored is an aircraft ...
What are the stages of the life cycle?
- INFANCY: Basic Trust vs. ...
- EARLY CHILDHOOD: Autonomy vs. ...
- PLAY AGE: Initiative vs. ...
- SCHOOL AGE: Industry vs. ...
- ADOLESCENCE: Identity vs. ...
- YOUNG ADULTHOOD: Intimacy vs. ...
- ADULTHOOD: Generativity vs. ...
- OLD AGE: Integrity vs. ...
What is the concept of "life cycle costing"?
In essence, therefore, the lifecycle cost of an asset comprises the sum of: initial construction cost on-going maintenance and other operating costs, eg, cleaning and utilities occupancy costs, eg, reprographics, catering and the like (BS ISO 15686, Part 5 includes these as part of 'non-construction costs' but it is usual in the UK to include them ... More items...
What is an asset life cycle?
What Is the Asset Life Cycle? An asset life cycle is a strategic and analytical approach to the management of a business’s assets. Most commonly performed with an accurate data collection system, such as Asset Management Software, an asset life cycle is broken down into multiple stages.
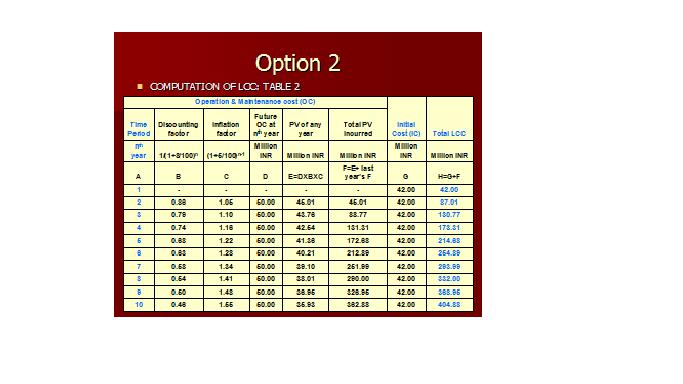
How life cycle cost analysis is prepared?
8.3. 2 Life-Cycle Cost AnalysisEstablish objectives.Identify constraints and specify assumptions.Define base case and identify alternatives.Set analysis period.Define level of effort for screening alternatives.Analyze traffic effects.Estimate benefits and costs relative to base case.Evaluate risk.More items...
What is included in a life cycle cost analysis?
What is Life Cycle Cost Analysis? Life cycle cost analysis (LCCA) is an approach used to assess the total cost of owning a facility or running a project. LCCA considers all the costs associated with obtaining, owning, and disposing of an investment.
How do you calculate life cycle cost?
Aggregate all the costs associated with a particular asset for each year of its usable life and add them all up (before adjusting for residual value) to work out the total life cycle cost.
What six things are accounted for in a life cycle cost analysis?
Life cycle costing provides an estimate of the cost that an asset will incur in its lifetime. Life cycle costing calculation generally involves adding six types of costs; purchase costs, maintenance costs, operational costs, financing costs, depreciation costs, and end-of-life costs.
Why is it important perform a LCC analysis?
The purpose of an LCCA is to estimate the overall costs of project alternatives and to select the design that ensures the facility will provide the lowest overall cost of ownership consistent with its quality and function.
What is the formula and why we require life cycle costing?
This calculation is as follows: Life-cycle costing (LCC) = capital cost + lifetime operations cost + lifetime maintenance costs + disposal costs - residual value. Perform a risk analysis for potential purchase - Each potential plane should be evaluated for risks like reliability and maintainability for its lifetime.
How do you calculate life cycle cost in Excel?
1:0724:41Life Cycle Costing (LCC) in Excel 1 - YouTubeYouTubeStart of suggested clipEnd of suggested clipSo we can do it a number of different ways um in excel we can use the calculation that we looked atMoreSo we can do it a number of different ways um in excel we can use the calculation that we looked at in class which is one over the power of one plus.
What is life cycle cost in project management?
Life Cycle Costing Method (LCC) LCC also known as total life-cycle costing (TLCC) is the sum of all types of costs: acquisition (ICC), O&M, and decomposition incurred over the lifetime of a project discounted to the present [34].
What cost estimating technique would be?
The four major analytical methods or cost estimation techniques used to develop cost estimates for acquisition programs are Analogy, Parametric (Statistical), Engineering (Bottoms Up), and Actual Costs.
How life cost analysis is implemented?
Life-cycle cost analysis (LCCA) is a tool to determine the most cost-effective option among different competing alternatives to purchase, own, operate, maintain and, finally, dispose of an object or process, when each is equally appropriate to be implemented on technical grounds.
What is conventional LCC?
The conventional LCC is, to a large extent, the historic and current practice in many governments and firms, and is based on purely economic evaluation, considering various costs associated with a product that is born directly by a given actor; it is usually determined by the perspective of a single actor, often the ...
What is meant by life cycle cost?
Lifecycle costing is the maintenance of physical asset cost records over entire asset lives. This means decisions around the acquisition, use or disposal of assets can be made in a way that achieves the optimum asset usage at the lowest possible cost to the entity.
What is a life cycle cost quizlet?
Life Cycle Costing is the sum of all costs incurred during its life span of an item or system.
What are the objectives of life cycle costing?
The objective of life cycle costing is to minimise life cycle cost by optimizing reliability, maintainability and supportability. Figure 4 illustrates the relationship between the system operational effectiveness and other design parameters. Life cycle cost will decrease as the reliability increases.
What is life cycle cost analysis?
Life cycle cost analysis offers a general framework that can be used to assess the need for additional costs during a project’s useful life. With such knowledge in mind, it is possible to regulate cash outflows by forecasting requirements of a project.
Why is life cycle cost analysis important?
Life cycle cost analysis is especially useful where a project comes with multiple alternatives and all of them meet performance necessities, but they differ with regards to the initial , as well as the operating , cost . In this case, the alternatives are compared to find one that can maximize savings.
How does LCCA work?
All the costs involved are treated as base year values equivalent to present-day dollar amounts; LCCA transforms all dollar values into future year occurrence equivalents and then discounts all the values to their base dates. In such a way, it’s easy to find their present value.
What is rigorous modeling based on LCCA?
Rigorous modeling based on LCCA incorporates value engineering so that a project’s cost outline can lower expenditures by a huge margin. The procedures are done through a series of tests on the cost of operation.
What is due diligence in project finance?
Due Diligence in Project Finance Due diligence in project finance involves managing and reviewing the aspects related to a deal. Proper due diligence ensures no surprises arise in regard to a financial transaction. The process involves a comprehensive examination of the transaction and preparation of a credit appraisal note.
What is project related cost?
Project-related costs can be classified into initial costs, fuel costs, replacement costs, operation and maintenance costs, finance charges#N#Service Charge A service charge, also called a service fee, refers to a fee collected to pay for services that relate to a product or service that is being purchased .#N#, and residual values.
What is capital budgeting?
Capital Budgeting Best Practices Capital budgeting refers to the decision-making process that companies follow with regard to which capital-intensive projects they should pursue. Such capital-intensive projects could be anything from opening a new factory to a significant workforce expansion, entering a new market, or the research and development of new products.
What is life cycle costing?
Life cycle costing (LCC) is the process by which the owners of an asset compile all the costs that this asset will incur over the course of its lifetime. When it comes down to it, life cycle costing isn’t an especially obscure concept, because on some level, everyone does it every time they make a purchase. When you’re thinking about investing in ...
Why is life cycle costing important?
For a start, it gives you an excellent analytical framework for choosing between two or more assets when you’re making purchasing decisions.
What is purchase cost?
Purchase costs – This is the amount of your initial investment.
Do you need to include life cycle costs in your calculation?
It’s worth noting that depending on the asset, some of these costs may not apply , and therefore you don’t need to include them in your calculation. For example, if you’re doing life cycle costing for an item that you purchased outright without any outside financing, then you won’t need to calculate the amount of interest you incurred on the purchase. Of course, you’ll also need to minus any salvage or residual value that the asset ends up having.
Can you calculate life cycle cost in Excel?
Of course, you don’t have to calculate life cycle cost manually, as it’s very easy to complete this analysis on Excel, or indeed any other spreadsheet software. Aggregate all the costs associated with a particular asset for each year of its usable life and add them all up (before adjusting for residual value) to work out the total life cycle cost. But don’t just take our word for it – there are plenty of online templates and YouTube tutorials that you can use to learn how to calculate life cycle cost in Excel.
Is there a universally agreed-upon formula for life cycle costing?
Now that you know a little more about the life cycle cost analysis definition, it’s time to get to grips with life cycle costing yourself. There’s no universally agreed-upon formula for working out life cycle costing, as the specific costs are likely to vary depending on the asset.
Are there any limitations of life cycle costing?
However, there are a couple of limitations of life cycle costing that you should be aware of. Firstly, it’s time consuming . There’s a large amount of data that you’ll need to aggregate throughout the life cycle costing process, and with the need to work out depreciation as well, calculating life cycle cost can become a fairly complex undertaking. It’s also worth noting that in some cases, you’ll need to estimate particular costs and adjust them as you move forward. This may introduce an additional level of uncertainty into your analysis.
What is a Life Cycle Cost Analysis?
A life cycle cost analysis (LCCA) is an evaluation tool or method used to determine the expenditure required to purchase, own, operate, and maintain an item or service. This analysis is a very critical and intricate part of your purchasing process and future financial forecast.
Why is life cycle cost analysis important?
Simply because many businesses equate extending a device’s life cycle as the equivalent of saving money.
What is LCCA analysis?
An LCCA is also a subset of a cost-benefit analysis or CBA. As a whole, a CBA analyzes the various benefits and the related cost for various alternatives. As a result, you may initially need to do a CBA, but it is the LCCA that should be used to make the final purchasing decision.
What is asset in the life cycle?
The Life Cycle of Electronic Devices. An asset is defined as an item, device, thing or entity that has potential or actual value to an organization or business. Furthermore, asset management and life cycle cost analysis go hand-in-hand.
What is the first stage of the asset life cycle?
1. Planning: This, of course, is the first stage of the asset’s life cycle. This is also where you assess your company’s needs as they pertain to the number of devices required to meet your needs. This stage establishes and verifies asset requirements. 2.
How many stages are there in the life cycle of an electronic device?
The life cycle of an electronic device or any device or service consists of four key stages or phases. They are as follows:
Why do we need LCCA model?
For example, if you apply a CBA to justify the purchase of a particular CPU to build your computer around, you would still need to develop an LCCA model to evaluate life cycle costs. As you may know, today’s CPUs are more powerful and efficient than ever before. The need for more cores and higher processing speeds is a necessity to keep up with the ever-changing technological landscape.
What is the purpose of life cycle cost analysis?
The purpose of life cycle cost analysis is to identify all types of costs that a business may not think of in the initial stages. Businesses might be tempted with a lucrative offer without realizing that over time the costs surpass the offer pretty quickly. Life cycle cost analysis throws light on whether profits can recover the costs incurred at different stages of a product’s life cycle. Rather than compare individual costs, a cumulative comparison of the options is possible by first identifying all the costs related to the asset or product.
What is life cycle costing?
Life cycle costing is a method of adding up all the costs associated with an asset starting from its initial cost to its end of life. It does not take into account the salvage value or residual value of the asset. Life cycle costing provides an estimate of the cost that an asset will incur in its lifetime. Life cycle costing calculation generally involves adding six types of costs; purchase costs, maintenance costs, operational costs, financing costs, depreciation costs, and end-of-life costs. The summation of these costs gives the life cycle costing value. In some cases, the costs won’t apply to the asset in question and so they are not part of the calculation.
Why is life cycle costing important?
It is used by businesses that are involved in long-term planning. Life cycle costing enables businesses to make better decisions with regard to their investments. If there are two assets you are considering, calculating the life cycle costing of the two assets can unveil which asset is more profitable in the long run. In this way, you can spend your money in the right places. Life cycle costing makes budgeting easier. For example, if you do not know the expenses that will be incurred, you won’t be able to make a reliable budget. With life cycle costing budgeting is more precise.
Why is cost comparison important in life cycle costing?
Another major purpose of Life cycle costing is cost comparison to make effective decisions that can prove fruitful in the long term. Businesses can choose to invest as they wish depending on how much they are willing to spend. When they have various options, it makes sense to compare the costs that will be incurred to make smarter decisions. Let us say product A has a lifetime cost of $500 while product B has a lifetime cost of $650 even though they perform the same function. Comparing costs enables businesses to decide which is the more cost-effective option from the options available. This can maximize profits.
How does life cycle costing help a business?
Life cycle costing aids in planning . A business can effectively plan when it is aware of the various costs involved. For example, let us say a product’s initial costs are extremely high, it has a lifetime of 10 years, and the maintenance costs are low. With life cycle costing, a business is aware of all these costs and so it can plan budget allocation accordingly. Additionally, it uncovers when a product needs a higher investment in comparison. For instance, if a product needs higher investment during the operational phase, then a business is better prepared to invest and spend at that time. Without life cycle costing, expenditure planning is tougher although possible.
How business software helps you stay on top of your financials?
When you are running a business, tracking costs and revenue are the core functions. Without a business software such as TallyPrime in place, tracking costs can be challenging and time-consuming. Businesses should get in the habit of using accounting software from the start as it simplifies accounting tasks. TallyPrime empowers businesses to manage cash flow, perform accounting calculations, generate insightful reports, securely access data, and manage inventory effectively. All this is to efficiently organize your business financial data so you can make decisions related to investment and costs.
How is comparative analysis developed?
Each comparative analysis is developed on a project- specific basis. The Project Manager, Technical and Consultant Groups will decide together how to determine the details of each analysis. A “base case” will be established. The Project Team will then draw upon its collective experience to identify alternatives to the base case. For example, in analyzing mechanical distribution systems, the team might decide to consider a base case of overhead air distribution and an alternative underfloor approach. Section IV discusses the format used to record the results of the comparative analyses. While this format is intention- ally generic (to accommodate various types of studies), all Project Managers must use the same format so that the data collected and analyzed are documented consistently. The results of each team’s studies will be incorporated into the Department of Project Management’s LCCA library for future reference. In this way, Stanford will create a database of building studies as both a reference for future projects and a tool for understanding similarities and differences between building systems.
How to do LCCA?
Step 1. Establish Clear Objectives To be successful, an LCCA study must have clear objectives , and they must be objectives that this type of study is well suited to address. LCCA can capture dollar cost variations between alternatives and show which option will have the lowest overall cost. It can only address values quantifiable in dollars. For example, an LCCA study of high-performance glazing can capture the overall cost-effectiveness of different options as compared to a base case. LCCA is not the right tool to explicitly evaluate improved comfort or occupant satisfaction with the different glazing products. Step 2. Determine LCCA Metrics (total cost and payback) The two primary metrics to be used and calculated in LCCA are the life cycle costs of each alternative and its payback over a certain study life. That is, consideration should be given to total costs and the time it takes to recover an incremental initial investment incorporating the time value of money. When two alternatives have similar O&M costs over the study life, “first” costs (i.e., construction costs) will most likely drive the decision. This approach is further supported by the consideration of uncertainty (see below under Calculating Life Cycle Costs). Step 3. Identify the Base Case and Develop Alternative Designs The Stanford LCCA approach is geared towards evaluat- ing design alternatives. The alternative that captures the “standard” design or minimum requirements for a project is called the “base case.” The design team must develop alternatives to evaluate against the base case. These alternatives must be developed in sufficient detail to derive good cost estimates, which are required to run the life cycle cost calculations and to capture the incremental cost differences of the options. An infinite number of alternatives can be developed for any project. The intent of these guidelines is to capture as much cost benefit as possible given a reasonable amount of effort and investment. The goal should be to develop roughly one to five alternatives for a given building component. The design team should develop the alterna- tives, using its experience and judgment in selecting relevant building and system component options. Analysis of alternatives should consider the effects of diminishing returns. Often, energy efficiency measures look less attractive in combination than when modeled individu- ally. Where possible, effects should be calculated for each measure individually as well as for the measures in combi- nation. For example, shading devices and high-performance glazing could each have a five-year payback, whereas the two in combination may have a seven-year payback if they have a higher combined cost and address the same energy use issues. Step 4. Gather Cost Information Cost information can come from a variety of sources, including cost estimating consultants, contractors, vendors, and designers. For each alternative, gather all of the cost information described below under Cost Components of LCCA (e.g., construction, utility, maintenance, service, and in some cases remodeling costs). Identify additional soft cost requirements for the alternatives as well.
What is LCCA in PDP?
Section III discusses in detail how to address LCCA at each stage. LCCA adds two major activities to the PDP: O&M Cost Benchmarking and Comparative Analysis. Each of these activities occurs at specific phases in the PDP, in conjunction with other Project Team tasks during those phases.
What is LCCA project?
An LCCA may include project, utility, maintenance, service, remodeling, and end-of-life costs, as well as benefits to campus infrastructure. Project Costs Project costs, sometimes referred to as initial or first costs, include both “hard” or construction costs (labor, materials, equipment, furnishings, etc.) and “soft” costs (design fees, permit fees, etc.). Cost estimates and information from contractors, vendors, and design teams can be used to develop project costs for LCCA alternatives. In LCCA studies, the cost differences between alternatives are usually what is important, not the absolute costs. Project costs therefore only need to be developed for the components that vary between alternatives. For example, in comparing two HVAC systems that have the same zonal equipment (e.g., VAV boxes) but varying central equipment (e.g., air handlers), the zonal equipment costs can be ignored and only the costs of the central equipment developed. It is important to be as complete and thorough as possible when considering project cost variations between alternatives; all costs that vary must be captured in order to make a valid comparison. Design and other soft costs should be identified and built into the LCCA calculations. Utility Costs Energy Costs Stanford’s central utilities provide the majority of Stanford facilities with steam, chilled water, and/or electricity, though Pacific Gas & Electric Company is the provider in outlying areas. For each type of utility service there is a cost per unit of energy delivered that will be charged to the building. The rates and units for these utilities are listed below under Life Cycle Cost Parameters. Energy Estimating Methods Typically the mechanical and/or electrical engineers on a design team will estimate the amount and rate of build- ing energy use. The most comprehensive and widely used method of performing these estimates involves detailed hourly computer simulation of building operation with programs like DOE-2. If the level of effort to build a DOE-2 or similar computer model of a building is not appropri- ate for a project, simplified methods exist for estimating energy use. These include: • Equivalent full-load hours • Degree-day methods • Outside temperature bin methods The mechanical and/or electrical engineers can decide which method is most appropriate for a given project, in consultation with the Project Manager. Stanford strongly encourages the use of DOE-2 or similar programs to develop energy estimates. Non-Energy Utility Costs Domestic water and sewer service are two non-energy utility costs that need to be developed when affected by alternatives being modeled. Maintenance Costs Maintenance refers to the costs incurred to keep building systems running properly. The wide array of activities performed by Stanford’s maintenance staff fall into four cost categories: preventive, reactive, planned, and deferred. These data should be based on historical data provided by facilities operations. Preventive Preventive maintenance is routine, scheduled activity intended to keep a system running at its best. This maintenance is performed whether or not there are any problems with a system. It is designed to prevent break- downs. Changing filters and lubricating bearings are examples of preventive maintenance activities. Preventive maintenance costs associated with equipment and systems should be incorporated into LCCA calculations.
What is the objective of the construction phase?
The objective of the Construction phase is to safely build the project as represented in the contract documents within the parameters approved by senior management and/or the Board of Trustees. There are no specific LCCA tasks or deliverables during this phase.
What is cost effectiveness in Stanford?
Cost-effectiveness is a key component of design at Stanford, and initial project costs are the focus of many activities in the PDP. The long-term cost implications of building projects, however, range far beyond initial design and construction expenses. As the campus grows and ages, the cumulative cost of operating and maintaining facilities significantly impacts the overall institutional budget. To improve the cost-effectiveness of its building and renovation programs, Stanford must invest in designs and systems with improved long-term performance. The Guide- lines for Life Cycle Cost Analysis (LCCA) instruct Project Teams to consider not only the “first costs” of a building (design and construction expenses) but also long-term costs, including utilities, operations, and maintenance. The Vice Provost for Land and Buildings convened a team of staff from departments within Land and Buildings, along with consultants from the design and construction fields, to develop the Guidelines for LCCA. These guidelines have been implemented as part of the broader PDP for all new building and renovation projects. These guidelines define LCCA, explain their relevance to Stanford projects, instruct Project Teams on their implementation, and provide techni- cal specifications for preparing LCCA studies. They also establish standards and metrics to ensure accurate and consistent life cycle data collection and evaluation across projects. These guidelines, like the PDP, are based on the principle of making informed decisions at the project level. They have been designed to dovetail with the existing PDP and to clarify decision making without adding unwieldy require- ments. As the guidelines are repeatedly implemented, the data generated should result in increasingly accurate analyses for future projects.
What is sustainability in LCCA?
At the heart of “sustainability” is a balance between human concerns (e.g., cost, health, comfort) and environmental concerns (e.g., resource use, ecological degradation).

Understanding Life Cycle Cost Analysis
- Life cycle cost analysis is ideal for estimating the overall cost of a project’s alternatives. It is also used to choose the right design to ensure that the chosen alternative will offer a lower overall ownership cost that is consistent with function and quality. LCCA needs to be performed during the initial stages of the design process, as there i...
Costs
- Various costs arise when procuring, operating, or disposing of a project. Project-related costs can be classified into initial costs, fuel costs, replacement costs, operation and maintenance costs, finance charges, and residual values. Only relevant and significant costs in each of the categories above can be used to make investment-related decisions. Costs are considered significant whe…
Life Cycle Cost Analysis For Infrastructure
- Life cycle cost analysis can be used to assess different infrastructural sectors such as rail and urban transport, airports, highways, and ITS, as well as ports and industrial infrastructure. Such kinds of projects make use of capital expenditure, which is the initial cost involved when constructing or delivering an infrastructural asset. Simply put, it is the cost of construction for th…
LCCA and Value Engineering
- Rigorous modeling based on LCCA incorporates value engineeringso that a project’s cost outline can lower expenditures by a huge margin. The procedures are done through a series of tests on the cost of operation. Modeling using LCCA requires a lot of flexibility when adjusting the types of costs associated with materials and assets used in a project over its lifetime. That way, a develo…
LCCA and The Choice of Materials Or Assets
- Value engineering offers the potential to assist developers in choosing the right material and assets. Since a material or asset may come with a unique specification with regards to maintenance and the cost of acquisition, their overall characteristics will not be the same. For example, the most expensive asset may provide superior performance and quality but will requir…
Final Word
- Life cycle cost analysis offers a general framework that can be used to assess the need for additional costs during a project’s useful life. With such knowledge in mind, it is possible to regulate cash outflows by forecasting the requirements of a project.
Related Readings
- Thank you for reading CFI’s guide to Life Cycle Cost Analysis. To keep learning and advancing your career, the following CFI resources will be helpful: 1. Capital Budgeting Best Practices 2. Due Diligence in Project Finance 3. Fixed and Variable Costs 4. Project Management