
A failure mode is defined as the manner in which a component, subsystem, process, etc. could potentially fail. Failure modes can be identified through existing data, or by brainstorming possible instances when the process, product, or service may fail.
- Step 1: Identify potential failures and effects. The first FMEA step is to analyze functional requirements and their effects to identify all failure modes. ...
- Step 2: Determine severity. Severity is the seriousness of failure consequences of failure. ...
- Step 3: Gauge likelihood of occurrence. ...
- Step 4: Failure detection.
How do you identify potential failure modes in software testing?
Step 3: Identify potential failure modes. A failure mode is defined as the manner in which a component, subsystem, process, etc. could potentially fail. Failure modes can be identified through existing data, or by brainstorming possible instances when the process, product, or service may fail.
What is failure modes and effects analysis?
Failure modes and effects analysis ( FMEA) is a step-by-step approach for identifying all possible failures in a design, a manufacturing or assembly process, or a product or service. “Failure modes” means the ways, or modes, in which something might fail.
What is potential failure mode in FMEA?
I use the AIAG FMEA manual as my reference here... Definition: Potential failure mode is defined as the manner in which the process could potentially fail to meet the process requirements and/or design intent as decribed in the process function/requirements column. (Page 39)
Can a failure mode be both process and product?
That's fine. I stand by my (and AIAG's FMEA) opinion that a failure mode can be both process and product at that step of the operation.
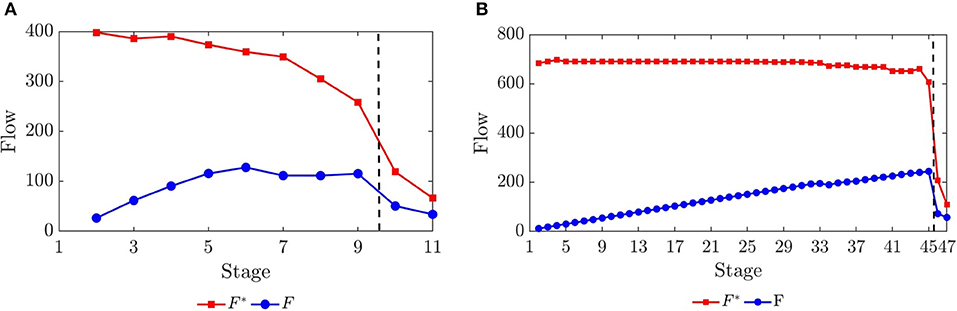
What is a potential failure mode?
Potential Failure Mode is defined as the manner in which a component, subsystem, or system could potentially fail to meet the design intent. The potential failure mode may also be the cause of a potential failure mode in a higher level subsystem, or system, or be the effect of one in a lower level component.
What are examples of failure modes?
Examples of failure conditions include: premature operation, failure to operate at a prescribed time (complete loss of function), intermittent operation, failure to cease operation at a prescribed time, loss of output during operation (reduced performance), degraded operation (loss of performance over time), and/or ...
What are the four types of failure modes?
Examples of failure modes are: Ductile fracture. Brittle fracture. Fatigue fracture.
What are the five types of causes for failure modes?
Failure Modes: Understand the 5 most common failure typesBeam failure (not intended to be realistic ;-) )Ductile fracture with characteristic distortion and shear lip.Part which failed due to fatigue.Creep failure of a pipe.
What are the different types of failure?
4 Types of Failure We Have all Experienced and Will AgainAbject Failure.Glorious Failure.Common Failure.Predicted failure.
What are the 3 types of FMEA?
Types of FMEA: Process FMEA (PFMEA) Functional FMEA (FFMEA) / System FMEA (SFMEA) Software FMEA.
What is the most common failure mode?
Fatigue failure In materials science, fatigue – the weakening of a material caused by cyclic loading resulting in progressive, brittle, localized structural damage – is the most common failure mode and the one that generally produces other types of failure.
How does FMEA is is used to forecast & identify potential failure modes state give 3 simple steps?
An FMEA uses three criteria to assess a problem: 1) the severity of the effect on the customer, 2) how frequently the problem is likely to occur and 3) how easily the problem can be detected.
What are the 5 steps of the FMEA process?
Here's an overview of the 10 steps to a Process FMEA.STEP 1: Review the process. ... STEP 2: Brainstorm potential failure modes. ... STEP 3: List potential effects of each failure. ... STEP 4: Assign Severity rankings. ... STEP 5: Assign Occurrence rankings. ... STEP 6: Assign Detection rankings. ... STEP 7: Calculate the RPN.More items...•
What is the main cause of failure?
1. Inadequate training. Enabling employees to complete tasks properly, and with minimal mistakes, requires time and effort. When people do not understand what they are doing or how to do it optimally, there is a higher chance of making mistakes or failing to complete tasks altogether.
What is the most common failure mode?
Fatigue failure In materials science, fatigue – the weakening of a material caused by cyclic loading resulting in progressive, brittle, localized structural damage – is the most common failure mode and the one that generally produces other types of failure.
What is the difference between failure and failure mode?
A failure may originate from an error. When the failure occurs, the item enters a fault state. A failure mode is the way in which an item could fail to perform its required function.
What is failure mode observation?
A failure mode is defined as the manner in which a component, subsystem, process, etc. could potentially fail. Failure modes can be identified through existing data, or by brainstorming possible instances when the process, product, or service may fail.
What are failure mechanisms?
"Failure mechanisms are the physical, chemical, thermodynamic or other processes that result in failure. Failure mechanisms are categorized as either overstress or wear-out mechanisms. Overstress failure arises because of a single load (stress) condition, which exceeds a fundamental strength property.
What is potential failure mode?
Definition: Potential failure mode is defined as the manner in which the process could potentially fail to meet the process requirements and/or design intent as decribed in the process function/requirements column. (Page 39)
What is failure mode and effects analysis?
Failure modes and effects analysis ( FMEA) is a step-by-step approach for identifying all possible failures in a design, a manufacturing or assembly process, or a product or service.
Why keep FMEA to 3?
The reason I try to keep the causes to no more than 3 is the fact that your FMEA can become really large. Let's say someone stated a potential cause was "Martians did it". The occurence rating would be say a 1. Would I keep this in my process FMEA? No, I would discard it. The number keeping no more than 3 is not solid but not too many have more than 3 potential causes with occurence rating over 5 or 6.
What is process FMEA?
Process FMEA focuses on manufacturing and assembly processes. Refer to this website for more info - http://www.npd-solutions.com/fmea.html
What is failure mode in FMEA?
So, when performing a Process FMEA, a failure mode can be a process failure and/or a product failure.
Is there confusion over failure modes in a Process FMEA mixing a potential cause with a potential failure?
There is a lot of confusion over failure modes in a Process FMEA mixing a potential cause with a potential failure mode.
Can failure mode be both process and product?
That's fine. I stand by my (and AIAG's FMEA) opinion that a failure mode can be both process and product at that step of the operation.
What is failure mode and effect analysis?
What is a Failure Mode and Effect Analysis (FMEA)? Failure Mode and Effect Analysis (FMEA), also known as “Potential Failure Modes and Effects Analysis” as well as “Failure Modes, Effects and Criticality Analysis (FMECA)” is a systematic method for identifying possible failures that pose the greatest overall risk for a process, product, ...
Why is failure mode important?
In the following example, Failure Mode A is important because it is likely to escape to the customer. Failure Modes B and C, are critical because they could be costly. Failure Modes.
How Does FMEA Work?
Once each failure mode is identified , the data is analyzed, and three factors are quantified:
What is the RPN of failure mode?
The failure mode “data entered incorrectly” with a potential cause of “data entry error within a single field” has the highest RPN, and warrants further review since it has been identified that there are no controls in place, and a detectability score of 10 has been assigned. The failure mode for “application filled out incorrectly” has a lower RPN of 96 , but may also deserve further investigation since the severity rating is high at 8.
What are the two types of FMEA?
There are currently two types of FMEA: Design FMEA (DFMEA) and Process FMEA (PFMEA).
Why is FMEA important?
It is important to document and assess all changes that occur which affect quality or reliability.
What is FMEA in process control?
FMEA provides a structured approach to identifying and prioritizing potential failure modes, taking action to prevent and detect failure modes and making sure mechanisms are in place to ensure ongoing process control.
What is failure mode?
Failure Mode – The specific manner or mode in which the failure occurs.
What is failure mode and effect analysis?
In the product design world, it’s common to use a tool called a Failure Modes and Effects Analysis (FMEA) to improve a design or process. FMEAs are commonly separated into two different categories, depending on their application: A Design FMEA (D-FMEA) is used in product design to identify possible design weaknesses and failure modes. ...
How to reduce RPN?
The lightweight FMEA is a great start, but in some organizations there are additional details that are filled out. Those details address the actions to be taken and their impact on the failure mode. Specifically, the new columns are as follows: 1 Recommended Actions – These are the actions to be taken in order to reduce the RPN. Often, an RPN above a certain threshold will always require an action to reduce the rating in one or more of the three categories. 2 Owner and Target Date – Each action will have an owner and a target date assigned. 3 Actions Completed – This is where the specific actions are documented that were done in order to reduce the ratings. 4 Updated SEV, OCC, DET – Another round of ratings are assigned to Severity, Occurrence, and Detectability, based on the results of the actions that have been completed. The goal of the actions is to reduce at least one of these categories to bring it within acceptable limits. 5 New RPN – Similar to the prior RPN, this is the product of the updated SEV, OCC, and DET ratings. This should always be lower than the original RPN, or the actions taken provided little to no value.
What is FMEA tool?
As I mentioned earlier, the FMEA is a tool that is intended to identify weaknesses and problems before they occur. The FMEA accomplishes this by breaking an assembly down, often to the component level, and identifying all possible failure modes that we can think of. The image below shows what our lightweight D-FMEA looks like.
What is FMEA in assembly?
As I mentioned earlier, the FMEA is a tool that is intended to identify weaknesses and problems before they occur. The FMEA accomplishes this by breaking an assembly down, often to the component level, and identifying all possible failure modes that we can think of.
What is a FMEA in a process?
A Process FMEA (P-FMEA) is used to identify possible failures in the process that the item must go through to be completed, such as a machining operation, or transportation from one operation to the next.
Why are exclusions added to FMEA?
These exclusions can be added in by the user if they feel they are necessary; for example, if there is a need to track actions to reduce the RPN within the FMEA, if larger teams are using the tool, or if there’s a need for customer reporting requirements and traceability between failure modes and action items. There may be a variety of other reasons to expand on the lightweight FMEA not mentioned here.
What is failure mode analysis?
military, failure modes and effects analysis (FMEA) is a step-by-step approach for identifying all possible failures in a design, a manufacturing or assembly process, or a product or service.
What is failure mode?
It is a common process analysis tool. "Failure modes" means the ways, or modes, in which something might fail. Failures are any errors or defects, especially ones that affect the customer, and can be potential or actual. "Effects analysis" refers to studying the consequences of those failures.
What to know before undertaking an FMEA process?
Before undertaking an FMEA process, learn more about standards and specific methods in your organization and industry through other references and training.
How to calculate risk priority number?
Calculate the risk priority number, or RPN, which equals S × O × D. Also calculate Criticality by multiplying severity by occurrence, S × O . These numbers provide guidance for ranking potential failures in the order they should be addressed.
Why is failure prioritized?
Failures are prioritized according to how serious their consequences are, how frequently they occur, and how easily they can be detected. The purpose of the FMEA is to take actions to eliminate or reduce failures, starting with the highest-priority ones.
What is critical characteristic?
Optional for most industries: Ask, "Is this failure mode associated with a critical characteristic?" (Critical characteristics are measurements or indicators that reflect safety or compliance with government regulations and need special controls.) If so, a column labeled "Classification" receives a Y or N to show whether special controls are needed. Usually, critical characteristics have a severity of 9 or 10 and occurrence and detection ratings above 3.
What are the first and second highest risks of RPN?
Notice that RPN and criticality prioritize causes differently. According to the RPN, "machine jams" and "heavy computer network traffic" are the first and second highest risks.
What is the effect of failure?
The effect is the impact the failure has on the end product or on subsequent steps in the process.
Can a list be paired down?
The list should be exhaustive – it can be paired down and items can be combined after this initial list is generated.

What Is A Failure Mode and Effect Analysis (FMEA)?
When to Use FMEA
FMEA Benefits
FMEA Key Concepts
Tools Used to Plan and Support FMEA
How Does FMEA Work?
FMEA Process Example
Who Should Participate in FMEA?
FMEA Examples & Ground Rules
How to Construct A FMEA: FMEA Procedure
- Step 1: Provide background information on the FMEA:
1. Identify a name or item name for the FMEA 2. Identify the team participating in development of the FMEA 3. Record when the FMEA was first created and subsequent revisions 4. Identify and record the owner or preparer of the FMEA - Step 3: Identify potential failure modes.
1. A failure mode is defined as the manner in which a component, subsystem, process, etc. could potentially fail. Failure modes can be identified through existing data, or by brainstorming possible instances when the process, product, or service may fail.