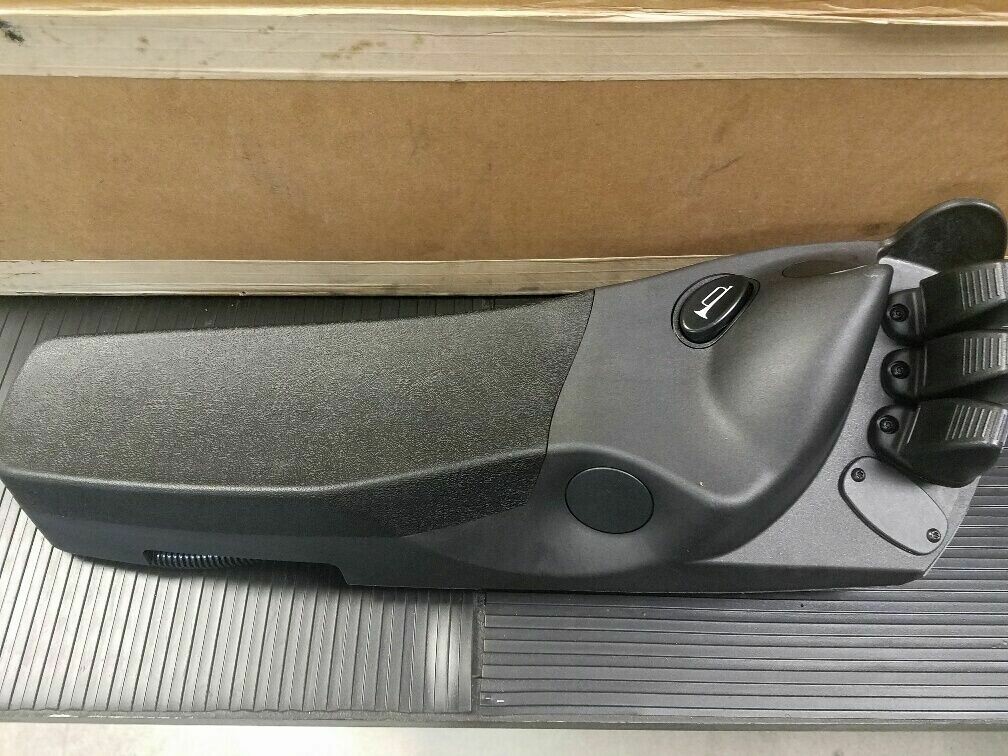
How to identify obsolete inventory
- Monitor Physical Count Tags ...
- Track the Last Usage Date ...
- Compare Withdrawals to On Hand Balance ...
- Review a Where Used Report ...
- Review Engineering Change Orders ...
- Review the Prior Obsolete Inventory Report ...
- The Need for Inventory Reviews ...
When does inventories become obsolete?
Inventory usually becomes obsolete after a certain amount of time passes and it reaches the end of its life cycle. Products that become obsolete or dead go through multiple steps before they become unsellable. It usually starts as slow-moving inventory, then becomes excess inventory and finally turns into obsolete inventory.
How do you determine if a part is obsolete?
This report is most effective if bills of material are removed from the computer system or deactivated as soon as products are withdrawn from the market; this more clearly reveals those inventory items that are no longer needed. An additional approach for determining whether a part is obsolete is reviewing engineering change orders .
What kind of businesses need to track obsolete inventory?
Businesses that sell physical products, as well as those in the maintenance and repair industry, need to track obsolete inventory.

How do you know if inventory is obsolete or excess?
Identify your excess and obsolete inventory Excess inventory: When stock levels for a product plus buffer stock exceed forecasted demand. Obsolete inventory: When stock remains in the warehouse and there is no demand for it over a prolonged period of time (typically for at least 12 months).
How do auditors identify obsolete inventory?
The best way to identify obsolete inventory is by implementing the right tools, technology, and processes to identify slow-moving inventory on hand. For instance, conducting regular inventory audits can quickly identify obsolete inventory before it eats away at your profits.
How do you test provision for obsolete inventory?
The provision for obsolete inventory is based on the book value of the unsold inventory. You can find this amount by running an inventory aging report that identifies stock that has not been sold within a specific time.
What is an example of obsolete inventory?
Obsolete inventory – example In other words, their sell-by date is November 30. John Doe sells 7,500 cookies by November 30. This means that there are 2,500 cookies that it cannot sell. Those 2,500 cookies are 'obsolete inventory.
What causes obsolete inventory?
Inventory obsolescence is often caused by businesses failing to understand the product life cycles of the items they stock and consequently missing the warning signs of those nearing their end.
What do companies do with obsolete inventory?
Obsolete inventory write-offs are a common practice for reducing excess stock. Companies often charge obsolete inventory to their cost of goods sold at the end of the year – taking the loss and moving forward.
Can obsolete inventory be written off?
Key Takeaways. An inventory write-off is the formal recognition of a portion of a company's inventory that no longer has value. Write-offs typically happen when inventory becomes obsolete, spoils, becomes damaged, or is stolen or lost.
What analytical procedures might reveal obsolete or slow moving inventory?
What analytical procedures might reveal obsolete or slow-moving inventory? Inventory turnover ratios. Trend analysis of inventory levels. Days sales in inventory ratio.
How can you reduce obsolescence?
Avoiding obsolescence or minimizing its costs can be accomplished through actions in planning and programming; design; construction; operations, maintenance, and renewal; and retrofiting or reuse of a facility (throughout the facility life cycle).
What are obsolete products?
Something that is obsolete is no longer needed because something better has been invented.
What is the meaning of obsolete items?
Something that is obsolete is no longer needed because something better has been invented.
What are obsolete materials?
Obsolete Material means non-fungible Material to be used in the Work production of which is or will soon be discontinued.
How do the auditors test for obsolete goods in the client's inventory?
The auditors will determine whether the amounts you have recorded as allowances for obsolete inventory or scrap are adequate, based on your procedures for doing so, historical patterns, "where used" reports, and reports of inventory usage (as well as by physical observation during the physical count).
What analytical procedures might reveal obsolete or slow moving inventory?
What analytical procedures might reveal obsolete or slow-moving inventory? Inventory turnover ratios. Trend analysis of inventory levels. Days sales in inventory ratio.
What are the audit assertions for inventory?
Key Assertions of the Audit of InventoryExistence. ... Completeness.Rights and Obligations. ... Valuation.Cut-Off. ... Presentation and disclosure. ... Audit procedures to Ensure Completeness. ... Audit Procedures for Cut-off Analysis.More items...
How do you test if inventory exists?
For inventory that is in the company's possession, the best way to test the existence assertion is to observe the company's physical inventory observation.
Is obsolete inventory bad?
Accumulating too much obsolete inventory can be bad for business since it cuts into profit margins. Inventory is considered an asset since it’s pur...
How do you identify obsolete inventory?
There are several ways to identify obsolete inventory. One way is to use an inventory management system that helps track inventory throughout its l...
Are damaged goods obsolete inventory?
Damaged goods is a type of dead stock and is sometimes considered obsolete if the product is unfixable and therefore, loses its value.
What do I do with obsolete inventory?
There are several ways to handle obsolete inventory. You can sell them at a discount, bundle them with other products, liquidate them through surpl...
How to identify obsolete inventory?
There are several ways to identify obsolete inventory. One way is to use an inventory management system that helps track inventory throughout its lifecycle. This way, you have data to calculate inventory days on hand and inventory turnover rate, which are key inventory metrics to track. You can also use lot tracking to group different batches of inventory.
Why is inventory obsolete?
Obsolete inventory can also be a result of poor inventory management. Without proper inventory planning — including the tools and technology to help track inventory in real time — optimizing inventory levels can be a challenge.
What is obsolete inventory?
Also known as “ dead stock ,” obsolete inventory refers to product that has reached the end of its lifecycle because it’s no longer sellable and most likely will not sell in the future due to a lack of value and demand.
How can inventory audits help you avoid obsolete inventory?
Consistent and accurate inventory audits can also help you avoid and reduce obsolete inventory by understanding how much you’re paying in holdings costs to store slow-moving items that are at risk of going obsolete .
What is Shipbob's inventory management?
ShipBob’s order fulfillment solution offers built-in inventory management tools, data, and reporting that offers insights into demand forecasting, order management, and more to help you make better decisions on how to manage your inventory.
What happens if you don't have any insight into what items are slow moving and taking up storage space?
For instance, if you don’t have any insight into what items are slow-moving and taking up storage space, then it will be harder to identify how much obsolete inventory you’re accumulating.
Why is inventory important?
Inventory is at the heart of an online business, so it’s important to have access to data that provides insights into how well your supply chain is performing.
How to identify obsolete inventory?
The simplest way to identify obsolete inventory without a computer system is to leave the physical inventory count tags on all inventory items following completion of the annual physical count. The tags taped to any items used during the subsequent year will be thrown away at the time of use, leaving only the oldest unused items still tagged by the end of the year. You can then tour the warehouse to see if an obsolescence reserve should be created for them. However, tags can fall off or be ripped off inventory items, especially if there is a high level of traffic in nearby bins. Though extra taping will reduce this issue, it is likely that some tag loss will occur over time.
Why is obsolete inventory identified?
Obsolete inventory must be identified, so that management understands how much of its inventory investment is worthless. This can result in action to dispose of the obsolete items, perhaps returning a small amount of cash to the business. We note below several methods for identifying obsolete inventory.
What is the last used report?
An advanced version of the “last used” report compares total inventory withdrawals to the amount on hand, which by itself may be sufficient information to conduct an obsolescence review. It also lists planned usage, which calls for information from a material requirements planning system, and which informs you of any upcoming usage requirements. An extended cost for each item is also listed, in order to give report users some idea of the write-off that might occur if an item is declared obsolete.
What is the final source of information?
A final source of information is the preceding period’s obsolete inventory report. The accounting staff should keep track of these items and notify management of those for which there is no disposition activity.
What is obsolete inventory?
Obsolete inventory is a term that refers to inventory that is at the end of its product life cycle. This inventory has not been sold or used for a long period of time and is not expected to be sold in the future. This type of inventory has to be written down and can cause large losses for a company. Obsolete inventory is also referred ...
How long does it take for inventory to become obsolete?
Inventory could become obsolete in three months to three or more years in the extremes, depending on the industry. Gaining awareness of your inventory movement, as well as checking with your Audit CPA’s is needed to settle on the acceptable definitions for your business.
What is the main method of identifying potential slow-moving inventory and the reduction of excess inventory?
Regular, frequent trend analysis of usage/sales is the main method of identifying potential slow-moving inventory and the reduction of excess inventory.
What is the path from valid inventory to obsolete inventory?
The path from valid inventory to obsolete inventory usually passes through the phases of slow-moving, to excess, to obsolete for both raw materials and finished goods.
What are the options to get whatever remaining value there is before excess inventory becomes obsolete?
Some of the options to get whatever remaining value there is before excess inventory becomes obsolete include: Price decreases. Discounting. Clearance sales. Once inventory becomes obsolete, your options for disposal become very limited so catching an inventory problem when it still has some value is very important.
What is the first step in inventory analysis?
One of the first steps in the analysis of inventory is for each company to define the critical terms used. Each company and industry have different dynamics that impact and define the following terms:
What considerations should be included in your decision to keep or dispose of obsolete inventory?
There are considerations such as tying up cash that could be used in more productive ways, the cost of warehousing, and the cost of managing the inventory, that should be included in your decision to keep or dispose of obsolete inventory.
What is Obsolete Inventory?
Inventory that has reached the end of its useful life and isn’t expected to be sold is known as obsolete inventory. Other terms include dead inventory or excess inventory.
How to Identify Inventory That May Become Obsolete
How do you know if your inventory might negatively affect your business? The first step is to do an inventory audit on a regular basis. You can either do this periodically or track it in real-time using a high-quality inventory system.
What Causes Dead Stock?
Why does a company end up with more of a product than it can sell? There are a variety of reasons. Preventing these issues will help you avoid obsolete inventory.
Getting Rid of Inventory Before It Loses Value
If you’ve identified slow-moving inventory, the first step is to notify your team that there’s a concern with that inventory item. That way no one will accidentally order more or fail to take action on a sales plan.
Key Takeaways
This article can help you identify issues that may be causing your dead stock and take steps to prevent them. By using inventory management software, you can identify slow-moving products and act quickly to sell them before you lose money.
What is obsolete inventory?
Obsolete inventory is excess stock that is difficult to sell because there is a lack of demand for the product. This inventory has already gone through the entire product lifecycle, transitioning from a slow-moving product, to excess inventory, and finally becoming obsolete.
Reasons to avoid obsolete inventory
Obsolete inventory is a drawback to any small business, cutting into profit margins, reducing working capital, and taking up warehouse storage space. Any inventory that cannot be sold needs to be written off as an expense at the end of the fiscal year.
Causes of obsolete inventory
Any type of product can eventually become obsolete. Here are some of the most common reasons products enter this stage of the inventory cycle:
Reasons to get rid of obsolete inventory
Obsolete inventory takes up space in the warehouse and counts as an expense on the balance sheet. Ultimately, obsolete products can decrease profitability and the success of a company. Lenders may be less likely to offer business loans to companies with a high level of obsolete products.
How to get rid of obsolete inventory
Small-business owners should do everything they can to sell obsolete inventory, rather than be forced to write it off as an expense. Here are a few ways to move stock and optimize returns on obsolete inventory:
How to avoid creating obsolete inventory
With the right inventory and supply chain management tactics, any small business can minimize or avoid obsolete inventory. Software programs can help business owners improve forecasting and order management in order to make better purchasing decisions.
The takeaway
Small-business owners should do everything they can to avoid high levels of obsolete inventory. Not only does too much excess inventory cut into profit margins and cash flow, but it can also limit the chances of getting a business loan.
What Is Obsolete Inventory?
Obsolete inventory, also called dead or excess inventory, refers to inventory a company still has after they should have sold it. This means that a product has reached the end of its product life cycle without being purchased or used by consumers.
Understanding Obsolete Inventory Management
Inventory management requires a person within the company to be in charge of overseeing the ordering, storing and selling of the company’s inventory. Related to this is obsolete inventory management, which is the process of tracking any excess products that the company cannot sell and reporting those losses.
Why Does Obsolete Inventory Matter?
Studies show that the average company has between 20 and 30 percent obsolete inventory at any given time. This matters because it costs your company a lot of money, and obsolete inventory creates waste in the disposal of unusable or unsellable products.
How to Identify Obsolete Inventory
Although the shelf life of inventory differs based on what type of company you have, there are two key terms leading up to obsolete inventory that can help you identify future obsolete inventory. Slow-moving inventory includes products that are not selling quickly and have been in storage or warehouses for a certain period.
How to Avoid Obsolete Inventory
Being able to identify slow-moving and excess inventory and knowing the sales trends of your products before they become obsolete can help you save your company from the financial burden of obsolete inventory.
Find the Inventory Management Product For You at Finale Inventory
Overall, inventory management is an important yet difficult part of keeping a business profitable. All industries, and even different companies within the same industry, have different strategies to avoid excess obsolete inventory. Regardless of the type of company, there is customizable software that will work for you.
