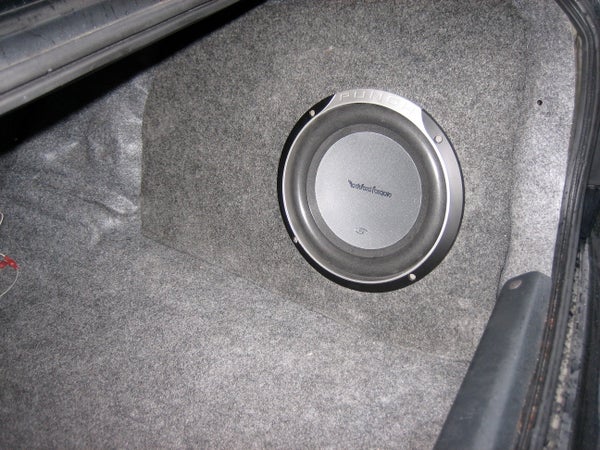
Steps in Making Fiberglass Molds from an Existing Part
- 1. Clean the Part Ensure that there are no dents or unnecessary buildups on the surface. ...
- 2. Mount the Part on a Clean Backing Board ...
- 3. Fill Any Gaps ...
- 4. Apply Mold Release Wax ...
- 5. Start Building the Fiberglass Mold ...
- 6. Wait for the Gelcoat to Cure ...
- 7. Apply Polyester Resin Over the First Coat ...
- 8. Allow the First Layer to Cure ...
Full Answer
How to make a fiberglass mold from an existing part?
Steps in Making Fiberglass Molds from an Existing Part
- Clean the Part. Ensure that there are no dents or unnecessary buildups on the surface. ...
- Mount the Part on a Clean Backing Board. Use whatever means available to secure the part on the mounting board. ...
- Fill Any Gaps. ...
- Apply Mold Release Wax. ...
- Start Building the Fiberglass Mold. ...
- Wait for the Gelcoat to Cure. ...
- Apply Polyester Resin Over the First Coat. ...
What material should I use for a fiberglass mold?
Materials used to make the Mold:
- West System 105A Epoxy Resin
- West System 205A Epoxy Fast Hardener
- West Systems 300 Epoxy Metering Pumps
- West Systems 406 Colloial Silica Filler
- West Systems A423 Graphite Powder
- CST Style G3733 5.8 oz Fiberglass Cloth
- Chavant Y2 Clay
- Coremat Flexible Core
- Partall High Temperature Mold Release wax
- Coverall Film Liquid Mold Release
How do you keep fiberglass from sticking to mold?
How do you keep fiberglass from sticking to wood? To prevent your mold from sticking to the plug, the plug must be coated with plastic film known as “PVA.” This is a plastic dissolved in alcohol and has a green color.
How to make Automotive fiberglass body molds?
Simple Methods for Molding Fiberglass and Carbon Fiber
- Materials. Mold release paste wax-available from Aircraft Spruce- http://www.aircraftspruce.com Woven carbon fiber cloth- available from Aircraft Spruce- http://www.aircraftspruce.com
- Method #1- Creating a Mold and Pulling a Positve. I used this method to modify existing bodywork on a friend's Ralt R5 CSR Mazda race car. ...
- Method#2- Lost Foam Molding. ...

How do you make a Fibreglass mold?
The first step is to cut a pattern from blue insulation foam and wrap it with clear packing tape. Next, cover the taped pattern with a mold release wax. Now cover the pattern with woven fiberglass cloth and wet out the resin. Make sure to leave a section uncovered- this is where the foam will be melted.
What material is used to make fiberglass molds?
If exceptionally rigid molds are required, carbon fiber can be used in place of fiberglass cloth. We recommend using epoxy resin with carbon fiber, and a flexible rubber squeegee works best for distributing resin through the fabric.
How many layers of fiberglass do you need for a mold?
6-8 coats are necessary, buffing after each coat. Allow the wax to fully cure (20 min.) between each coat. To ensure a proper release of the mold, several thin coats of PVA, can be added.
How do you mold plastic to fiberglass?
Clean the bonding surface on both the fiberglass and the plastic using a microfiber cloth dampened with a solvent. ... Roughen both of the surfaces slightly using a pad of fine grit sandpaper. ... Open your container of epoxy and mix according to the instructions printed on the container.More items...
What does fiberglass not stick to?
Even though it's used a lot, you might wonder, “will fiberglass resin stick?”. Fiberglass Resin will bond to almost any surface be it plastic, metal, wood, or Styrofoam. But there's a twist to it here; fiberglass resins don't usually stick to treated wood.
How do you make a poor man's fiberglass?
Poor Mans Fiberglass is a process of combining an adhesive like Titebond 2 (sometimes diluted with water) or “gripper” primer that is made to help paint adhere to surfaces, Material like canvas or bed sheets, and outdoor paint. These three things combined are poor mans fiberglass.
Does fiberglass hold mold?
Fiberglass, a non-biodegradable substance is resistant to mold. With its sharp, ground glass, mold spores puncture before they can attach to it. Mold can grow on the fiberglass insulation backing, which is made of paper and is a mold food source.
What is stronger fiberglass mat or cloth?
Fiberglass mat has a higher density than fiberglass cloth. Fiberglass cloth is a layer of woven strands. It is strong, with a uniform appearance, and is used where the look of a project is important. The woven fibers do not intermesh with the fibers of other layers of fiberglass cloth.
What hardens fiberglass resin?
A 2 oz. tube of liquid hardener (MEK Peroxide) is sufficient to harden the entire contents of a gallon container. Add 14 drops of liquid hardener per 1 oz. of Fiberglass Resin (or for ¼ can of Fiberglass Resin, use ¼ tube of liquid hardener).
What can I use for Fibreglass Mould?
Fiberglass Mold ReleaseIt is very important to take the time to use a mold release on your mold or plug. ... The two most popular mold releases used are: Partall Paste #2 (wax) and Partall #10 (PVA). ... Partall paste #2 (or other brand wax) can be used on the mold. ... Next you can use PARTALL Film #10.More items...•
Can you mold fiberglass with heat?
Things You'll Need If you apply pressure to fiberglass it will bend, but its elastic nature means that once pressure is released the fiberglass will spring back to its original shape. In order to create a permanent bend in a fiberglass panel you will need to apply heat.
What kind of wax do you use for fiberglass molds?
Paste wax is an economical mould release formulated with hydrocarbon and microcrystalline waxes. Paste wax, or run in wax is designed as a general purpose mould release agent on fiberglass and metal molds and as a compatible prime coat for PVA coatings.
What material is used for making molds?
Most mold making materials are utilized are made from natural or manmade rubber because of their flexibility and the ability to reproduce extraordinary detail. But some molds are made with more rigid materials such as gypsum plasters. The most common mold rubbers are natural latex, polyurethane, epoxy and silicone.
What material do you use to make a mold?
Molds can be made from the following materials:Plaster.Silicone rubber.Latex molding rubber.Polyester resin.Epoxy resin.Polyurethane rubber.Alginate*Flexible molding wax*
What materials are used for casting molds?
Popular casting materials include: plaster (Gypsum), resin, metal (bronze, aluminum, lead, silver and gold), and casting rubber. While there are tools specifically designed for mold making and casting, many modeling and ceramic tools are equally functional in this discipline.
What materials can you make resin molds out of?
Choose Your Materials We recommend using melamine, medium density fibreboard (MDF), or smooth plywood for the base and walls. If you are wondering about other materials for your mold surface, see below for a list of materials that epoxy will and will not stick to.
Introduction
Here is everything you will need to know about fiberglass molding available on the internet.
Chapter One – What is Fiberglass Molding?
Fiberglass molding is a method for forming complex and intricate parts using fiberglass resin. Though there are several reasons for producing parts and components from fiberglass, the most pressing reasons are the cost of the materials, ease of production, durability, and replicability.
Chapter Two – Uses for Fiberglass Molding
Fiberglass molding is an inexpensive method for the production of durable and lasting products and parts. Aside from its cost effectiveness, fiberglass is stronger and sturdier than certain metals, non-conductive, can be formed into intricate and complex shapes, and is chemical inert.
Chapter Three – How Fiberglass is Made
The first form of fiberglass was produced in the middle of the first industrial revolution. The form that we know today was created by a researcher at Owens-Illinois, which later became Owens Corning. The name that Owens Corning patented was fiberglas with one "s".
Chapter Four – Fiberglass Molding Processes
The determination of the process used to mold fiberglass depends on the type of part or component that is being created. The next consideration is the type of fiberglass material, which can be vinyl ester or polyester resin, fiberglass roving or matting, and gelcoat. Each of the different materials has their advantages depending on the application.
Chapter Five – Benefits of Using Fiberglass Molded Parts
Of the many fabricating materials, fiberglass is the most popular for reinforcing and stabilizing polymers due to its many positive properties. The initial use of fiberglass was for a supplement for plywood in the building of aircraft during World War II.
Chapter Six – Types of Fiberglass
Fiberglass can be fabricated to fit specific uses. Each type varies in composition resulting in distinct and unique characteristics. Regardless of the different types of fiberglass, the basic composition of fiberglass is pretty much the same with the exception of certain raw materials.
How is fiberglass made?
Fiberglass starts off as a liquid. This liquid is then extruded through tiny little holes, which turn it into thin strands of threads. These threads are coated with a chemical solution and bundled together to form rovings, or long bundles of fibre. Add a bit of resin and you have strong, durable, flexible fiberglass.
How to cover a form with fiberglass?
Prepare the fiberglass mat or cloth in sheets cut to suitable sizes to cover your form, allowing for plenty of overlap where you need to join it at corners or sharp curves. The material will become very flexible when the resin is applied, so don't worry if you cannot get it to conform to an exact shape while it is dry.
How to build a large project?
Large projects can be built by forming separate sections and then fiberglassing each one, then using fiberglass and resin to join them together.
What happens if you don't add wax to fiberglass?
The wax will make it easier to remove the fiberglass from the mold. If you don't add the wax, the resin will glue your project to the mold.
What is the best way to clean fiberglass?
Acetone is great for cleaning up fiberglass because it's strong and evaporates quickly. Just be sure not to soak any portion of the fiberglass in acetone, and keep acetone away from any caulking, plastic, or rubber. ...
What material to use for molds?
Use cardboard, plywood, MDF, or other stiff materials for molds with linear or geometric shapes. These stiffer materials are best for large projects like dog houses or even boats. For these molds, cover the entire surface either with wax paper, or a good, even coat of paraffin wax.
What to wear when applying resin?
Wear gloves and safety glasses when applying the resin, and avoid contact with skin.
How to mold carbon fiber positive?
To mold a carbon fiber positive from the fiberglass mold you first apply a mold release wax to the fiberglass mold. Then start wetting out the carbon cloth with resin and laying it inside the fiberglass mold. When wetting out the resin use a short bristled paintbrush and a "stippling" action to make sure the resin has fully penetrated ...
What to use to wet out resin?
When wetting out the resin use a short bristled paintbrush and a "stippling" action to make sure the resin has fully penetrated the carbon cloth as is placed in the mold. I tend to use epoxy resin when laminating carbon cloth as it produces a much stiffer final product.
Why use fiberglass molds?
Fiberglass molds are commonly used to make multiple copies of a part that may have a complex shape. Some of the advantages of using a fiberglass mold are: the materials are inexpensive, they are easy to make, last many years and can be used to produce hundreds of parts. The process starts with a pattern that you wish to copy.
How to increase viscosity of fiberglass?
Mix a little more Colloidal Silica into the mixed epoxy in the pot to increase the viscosity. Apply some additional tooling coat in the corners of the mold to fill in small radii corners. It is difficult to wet out the fiberglass cloth and keep it in tight corners of less than ¼” radius.
How to seal fuselage pattern?
The small opening around the edges of the fuselage pattern must be sealed. This can be done by first mold releasing the pattern. Then place the fuselage pattern into the parting surface with half the pattern exposed. Fill the opening around the edge with a mixture of West Systems Epoxy and 406 filler. After the epoxy has cured remove the pattern from the parting surface and block sand the parting surface flat along the edges. After you have the edge gaps filled build up the areas where openings in the mold are needed with clay. These openings give you access to the inside of the mold so you can join the half's of the molded part together. I have built up the areas of the hatch opening and tail boom connection opening. It is important to apply both Partall mold release wax and Coverall liquid mold release to the fuselage pattern and the parting surface as you did in step 1.
How to release hatch mold?
Mold release the hatch mold by the method in step 1 and apply a thin coat of epoxy to the inside of the mold. After that cures to a solid, about 30 minutes, lay in a layer of glass cloth and let it cure overnight. Pull the rough hatch from the mold and trim to the finished shape with a Dremel tool and sand paper.
How to increase strength of mold?
Now we will increase the strength of the mold by building up the thickness. An easy way to accomplish this is with a core material such as Coremat, Aeromat or chopped strand mat as oppose to many layers of fiberglass cloth. Cut the mat material into sizes and shapes to fit the mold. Apply this layer with epoxy as you did the fiberglass cloth and apply another layer of fiberglass cloth over the top of the core material creating a sandwich. As you can see, the core material is needed most around the edges of the mold and any large flat areas.
How to lay up a G3733 mold?
While the tooling gel coat is setting to a solid state, about 30 minutes, cut your fiberglass cloth. Use a coarse weave fiberglass cloth to lay up the mold. CST style G3733 wets out easily and builds up thickness more quickly than lighter materials. If the mold has a complex shape cut the fiberglass cloth on the bias so the fibers run on a diagonal. Strips 2 to 3 inches wide work well for complex shapes as the cloth will stretch and distort as needed to follow the surface.
How to make a fuselage hatch mold?
To make the mold for the fuselage hatch, apply a tooling coat layer of epoxy to the pattern in the area where the hatch will be located . Tooling coat is made by mixing a batch of West Systems 105/205 Epoxy add a teaspoon of graphite powder to the mixture then stir in 406 filler to thicken the mixture to the viscosity of ketchup. Make the mold a little larger than the intended hatch size. Allow the tooling coat to cure to a soft solid; this should take about 30 minutes. Apply two layers of fiberglass cloth and epoxy over the tooling coat layer. On this small mold for the hatch, this lay up should be sufficiently strong.
How to build a fiberglass mold?
Start Building the Fiberglass Mold. You can now start building the fiberglass mold. Apply the gel coat over the surface of the existing part. You can use a spray gun for easier application. You should make sure that the gel coat thickness is about 20 mils wet or 0.02 inch over the plug’s surface. 6.
What to do before you proceed with fiberglass mold?
So, before you proceed, make the necessary corrections on the backing board and the existing part so that you will obtain the surface finish that you want your final fiberglass mold to have.
What is the most commonly used adhesive in fiberglass mold production for boat parts?
The most commonly used adhesive in fiberglass mold production for boat parts is polyester resin.
What is the best glue to use for fiberglass molding?
Here are the 9 steps to make fiberglass molding from an existing spare part: The most common adhesive used in gluing fiberglass plies from each other is polyester resin or boat resin. Boatbuilders commonly use this resin because it is the cheapest option for fiberglass reinforcements for new boat constructions.
Why use fiberglass resin for boating?
Boatbuilders commonly use this resin because it is the cheapest option for fiberglass reinforcements for new boat constructions. Read on to learn more about making a fiberglass mold out of an existing part, the materials required, and the steps involved.
What is the best mold release agent for fiberglass?
Once you are satisfied with the surface finish of the unit, apply mold release wax. Professional mold makers recommend using paste wax and PVA (polyvinyl alcohol) as the best mold releasing agents. This wax will form a physical barrier between the existing part and the fiberglass mold’s gel coat.
How many layers of fiberglass mat to make a mold?
Here is a layering tip that will help you produce a good fiberglass mold: you may need to apply 2 to 3 layers of fiberglass mat or cloth until you obtain the mold’s desired thickness.
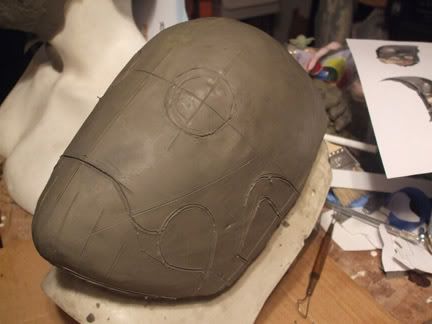