
How do you make wood composite plastic? Wood-plastic composites (WPCs
WPCS
WPCS is a radio station broadcasting a Christian radio format. Licensed to Pensacola, Florida, United States, the station is currently owned by, and is a ministry of, Pensacola Christian College.
Thermoplastic
A thermoplastic, or thermosoftening plastic, is a plastic polymer material that becomes pliable or moldable at a certain elevated temperature and solidifies upon cooling. Most thermoplastics have a high molecular weight. The polymer chains associate by intermolecular forces, which weaken rapidly with increased temperature, yielding a viscous liquid. In this state, thermoplastics m…
How are wood-plastic composites made?
Wood-plastic composites (WPCs) are produced by thoroughly mixing ground wood particles and heated thermoplastic resin. The most common method of production is to extrude the material into the desired shape, though injection molding is also used.
What are wood polymer composites?
Wood polymer composites (WPCs) are a relatively recently developed product, the current market of 220,000 t per annum (Europe, in 2010) has been developed over about 20 years of intense activity.
Can wood plastic composite be recycled?
Although these materials continue the lifespan of used and discarded materials, they have their own considerable half life; the polymers and adhesives added make wood-plastic composite difficult to recycle again after use. They can however be recycled easily in a new wood-plastic composite, much like concrete.
What is wood plastic composite (WPC)?
Wood-plastic composite is a type of engineered wood. WPCs do not corrode and are highly resistant to rot, decay, and marine borer attack, though they do absorb water into the wood fibers embedded within the material.
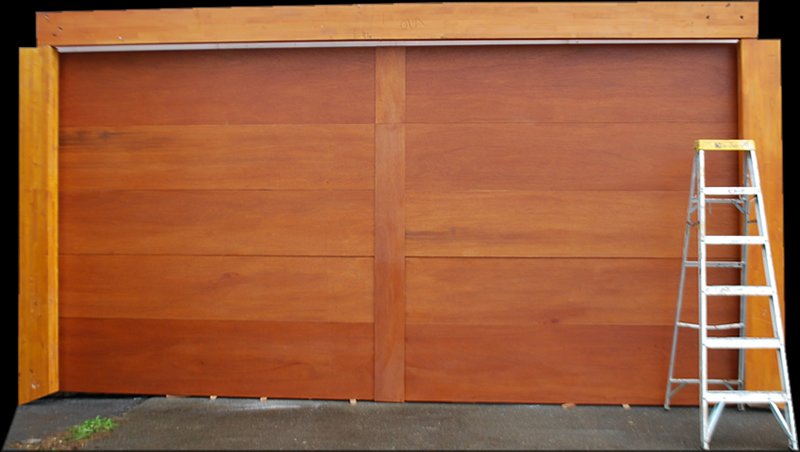
How is composite wood made?
How is wood composite made? Wood composite is usually made from the same hardwoods and softwoods used for lumber except using the sawmill's scraps and wood waste and created by mixing ground wood particles with heated thermoplastic resin.
How do you make plastic lumber at home?
0:1313:53How to Make Recycled BEAMS from Plastic Waste at Home - YouTubeYouTubeStart of suggested clipEnd of suggested clipSo we thought we'd try our hand at making recycled plastic beams in a way that you can do at home weMoreSo we thought we'd try our hand at making recycled plastic beams in a way that you can do at home we're going to use our tried and tested method of melting plastic in our panini.
Is Wood Plastic Composite good?
From a functional standpoint, wood plastic composite is moisture-resistant and rot-resistant, meaning that it will last aesthetically and integrally longer than normal wood. And WPC is more heat-resistant than typical lumber, creating a product that can be used in locations where normal lumber may bend or warp.
What is Wood Plastic Composite used for?
Wood plastic composite (WPC) that consists of polyethylene (PE) and wood sawdust tends to be used primarily in building and structural components. WPC comprised of wood sawdust and polypropylene (PP), on the other hand, is more commonly used for automotive and consumer products.
How do you make poly wood?
1:586:00How POLYWOOD® Furniture Is Made - YouTubeYouTubeStart of suggested clipEnd of suggested clipTogether the molten plastic is forced through a die giving shape to one single piece of genuineMoreTogether the molten plastic is forced through a die giving shape to one single piece of genuine hollywood lumber that stretches the entire length of the extrusion.
What type of plastic is used for plastic lumber?
They were manufactured with mixtures of 50 – 70% wood fiber and 30 – 50% polyethylene, either high or low-density PE or mixtures of the two polymers.
What is WPC made from?
Wood Plastic Composite (WPC) is a composite material made from sawdust and plastic as polymer bonding, that used in a variety of structural and non-structural applications.
What is WPC door made of?
WHAT IS WPC DOORS? WPC (Wood Plastic Composite) made from a unique combination of wood fiber and new plastic. WPC Door is a new green material that can be recycled. It offers the best advantages of plastic and wood.
Is WPC cheaper than wood?
The cost of WPC material is higher as compared to other material used for the same purpose. It lacks the natural wooden texture due to which the feeling of natural wood is missing.
Is Wood Plastic Composite waterproof?
Wood Plastic Composite is made from a blend PVC, limestone, foaming agents, inert ingredients. Laid down in powder form and pressed and heated to expand the polymer. The core material is waterproof, rigid and dimensionally stable.
Is composite wood waterproof?
Composite decking is not waterproof but is water-resistant. Composite decking will absorb water if submerge or rained on for an extended period of time.
What is WPC construction?
Wood plastic composites (WPCs) are composites manufactured from predominantly (typically synthetic) thermoplastic resins and wood flour filler, though thermoset resins and naturally derived resin systems may also be used.
What is the core ingredient of WPC?
But all share some basic principles. The core ingredient for both WPCs and PVC products is plastic. Typically it's one of two things. The first is virgin PVC, a byproduct of the refining of oil and natural gas. The second is polyethylene.
Can you use wood in a WPC?
It's ground into what's known as flour–particles so small that you can put 100 in a line and not cover an inch. Technically, any type of wood can be used in WPCs, but manufacturers prefer hardwoods over softwoods and look for woods free of tannins (e.g., maple rather than oak).
Can you use wood flour for PVC?
If you're making PVC products , there's no wood flour used, so only plastics and additives get mixed. Ingredients for a top coat, or capstock, on WPCs are mixed separately.
How are WPCs made?
WPCs are produced by thoroughly mixing ground wood particles and heated thermoplastic resin. The most common method of production is to extrude the material into the desired shape, though injection molding is also used.
Who invented WPC?
History. The company that invented and patented the process to create WPC was Covema of Milan in 1960, founded by Terragni brothers ( Dino and Marco ). Covema called WPC under the tradename Plastic-Wood. After a few years from the invention of the Plastic-Wood the company Icma San Giorgio patented the first process to add wood fiber / wood flour ...
What is WPC lumber?
WPCs are still new materials relative to the long history of natural lumber as a building material. The most widespread use of WPCs in North America is in outdoor deck floors, but it is also used for railings, fences, landscaping timbers, cladding and siding, park benches, molding and trim, prefab houses under the tradename Woodpecker WPC., window and door frames, and indoor furniture. WPCs were first introduced into the decking market in the early 1990s. Manufacturers claim that WPC is more environmentally friendly and requires less maintenance than the alternatives of solid wood treated with preservatives or solid wood of rot-resistant species. These materials can be molded with or without simulated wood grain details.
What is WPC board?
WPC boards show a good set of performance but monolithic composite sheets are relatively heavy (most often heavier than pure plastics) which limits their use to applications where low weight is not essential. WPC in a sandwich-structured composite form allows for a combination of the benefits of traditional wood polymer composites with the lightness of a sandwich panel technology. WPC sandwich boards consist of wood polymer composite skins and usually low-density polymer core which leads to a very effective increase of panel's rigidity. WPC sandwich boards are used mainly in automotive, transportation and building applications, but furniture applications are also being developed. New efficient and often in-line integrated production processes allow to produce stronger and stiffer WPC sandwich boards at lower costs compared to traditional plastic sheets or monolithic WPC panels.
What is a WPC sandwich board?
WPC sandwich boards consist of wood polymer composite skins and usually low-density polymer core which leads to a very effective increase of panel's rigidity. WPC sandwich boards are used mainly in automotive, transportation and building applications, but furniture applications are also being developed.
Is WPC wood more environmentally friendly?
Manufacturers claim that WPC is more environmentally friendly and requires less maintenance than the alternatives of solid wood treated with preservatives or solid wood of rot-resistant species. These materials can be molded with or without simulated wood grain details.
Does Trex composite decking corrode?
Advantages and disadvantages. Trex Composite Decking. WPCs do not corrode and are highly resistant to rot, decay, and marine borer attack, though they do absorb water into the wood fibers embedded within the material.
What are composite products made of?
Similar composite products can also be made from vegetable fibers using lignin-containing materials such as hemp stalks, sugar cane residue, rye and wheat straw, with chemical additives enabling the integration of polymer and wood flour while helping facilitate optimal processing conditions. They are fixed using adhesives ...
What is composite wood used for?
Composite wood products can be used in a variety of different ways, including both home and industrial construction, and is often used to replace steel for joists and beams in building projects. Their most widespread use, however, is in outdoor deck flooring, but they are also popular for railings, fencing, benches, window and door frames, cladding and landscaping work.
What is laminated wood veneer?
Laminated timber is created using dimensional timber glued together into structural columns or beams, while laminated veneers bond thin wooden veneers into a large billet which can be used for rafters, beams, columns and joints.
Why is composite wood better than regular wood?
One of the main advantages of wood composite is that because it is man-made, it can be designed for specific qualities or performance requirements. It can be made into different thicknesses, grades, sizes and exposure durabilities, as well as manufactured to take advantage of the natural strength characteristics of wood (and sometimes results in a greater structural strength and stability than regular wood).
Why are plastics fire hazard?
The plastic materials often used in the creation of wood composites also have a higher fire hazard when compared to solid wood products, due to their higher chemical heat content and melting properties.
Why are petroleum based polymers bad for the environment?
But its environmental impact depends largely on the ratio of renewable to non-renewable materials used in its construction, with petroleum-based polymers having a negative impact because of their reliance on non-renewable raw materials.
Is wood composite good for outdoor use?
Some particle and fiber-based composite woods are also not suitable for outdoor use as they can absorb water and be more prone to humidity-induced warping than solid woods.
Outdoor durability of wood–polymer composites
Wood–plastic composite (WPC) lumber is promoted as a low-maintenance, high-durability product ( Clemons, 2002 ). However, after a decade of exterior use in the construction industry, questions have arisen regarding durability.
Improving wood–polymer composite products: a case study
WPC materials will absorb variable amounts of moisture, some more, some less. Why this is so is discussed by Klyosov. 2 When immersed in water, WPCs absorb typically between 0.7% and 3% by weight after 24 h immersion.
The use of wood fibers as reinforcements in composites
L.M. Matuana, N.M. Stark, in Biofiber Reinforcements in Composite Materials, 2015
Creep behavior and damage of wood–polymer composites
WPCs absorb less humidity than wood, but the effect of water on the composites is not negligible and deserves attention.
UV DEGRADATION & STABILIZATION OF INDUSTRIAL PRODUCTS
Table 8.41 gives examples of general requirements typically used in the assessment of siding.
Development of biobased wood polymer nanocomposites: industrial applications, market, and future trends
Moon Mandal, ... Tarun K. Maji, in Handbook of Polymer Nanocomposites for Industrial Applications, 2021
Preservation, protection and modification of wood composites
Early wood plastic composite products were thought to be a decay-free product, with low or no maintenance requirement due to the encapsulation of the wood flour or fibre in the polymer matrix.
Is heating plastic toxic?
Be safe with this. There are various types of plastic, and not all are compatible. Besides, heating plastic materials can be toxic.
Can you extrude plastic for lumber?
Melted plastic in quantities needed for making lumber pieces has to be extruded into a mold the size and shape of the piece you need. An extruder can be rented to use at home for this process. For the best fibers to use to strengthen your lumber, check with your resin supplier.
Can you make plastic lumber at home?
You can make plastic lumber at home for projects that you have in mind. It's not easy, however, and there are dangers as well as expenses involved in addition to the materials you need. Whether you would save money in the long run is worth looking into. As noted, there are dangers. So heed the warning from various suppliers.
Can you melt plastic pellets?
Your best bet is to buy plastic pellets of the type you want and melt them according to the supplier's instructions. Craft and hobby materials suppliers have plastic pellets that can be melted and molded, but these would be too expensive to use for making lumber.

Overview
Wood-plastic composites (WPCs) are composite materials made of wood fiber/wood flour and thermoplastic(s) such as polythene (PE), polypropylene (PP), polyvinyl chloride (PVC), or polylactic acid (PLA).
In addition to wood fiber and plastic, WPCs can also contain other ligno-cellulosic and/or inorganic filler materials. WPCs are a subset of a larger categ…
History
The company that invented and patented the process to create WPC was Covema of Milan in 1960, founded by Terragni brothers (Dino and Marco). Covema called WPC under the tradename Plastic-Wood. After a few years from the invention of the Plastic-Wood the company Icma San Giorgio patented the first process to add wood fiber/wood flour to the thermoplastics (WPCs).
Uses
Also sometimes known as Composite Timber, WPCs are still new materials relative to the long history of natural lumber as a building material. The most widespread use of WPCs in North America is in outdoor deck floors, but it is also used for railings, fences, landscaping timbers, cladding and siding, park benches, molding and trim, prefab houses under the tradename Woodpecker WPC., window and door frames, and indoor furniture. WPCs were first introduced int…
Production
WPCs are produced by thoroughly mixing ground wood particles and heated thermoplastic resin. The most common method of production is to extrude the material into the desired shape, though injection molding is also used. WPCs may be produced from either virgin or recycled thermoplastics including high-density polyethylene (HDPE), low-density polyethylene (LDPE), polyvinyl chloride (PVC), p…
Advantages and disadvantages
WPCs do not corrode and are highly resistant to rot, decay, and marine borer attack, though they do absorb water into the wood fibers embedded within the material. Water absorption is more pronounced in WFCs with a hydrophilic matrix such as PLA and also leads to decreased mechanical stiffness and strength. The mechanical performance in a wet environment can be enhanced …
WPC sandwich boards
WPC boards show a good set of performance but monolithic composite sheets are relatively heavy (most often heavier than pure plastics) which limits their use to applications where low weight is not essential. WPC in a sandwich-structured composite form allows for a combination of the benefits of traditional wood polymer composites with the lightness of a sandwich panel technology. WPC sandwich boards consist of wood polymer composite skins and usually low-de…
Issues
The environmental impact of WPCs is directly affected by the ratio of renewable to non-renewable materials. The commonly used petroleum-based polymers have a negative environmental impact because they rely on non-renewable raw materials and the non-biodegradability of plastics.
The types of plastic normally used in WPC formulations have higher fire hazard properties than wood alone, as plastic has a higher chemical heat content and can melt. The inclusion of plastic …
See also
• Composite lumber
• Glued laminated timber
• Laminate panel
• Plastic composite (disambiguation)
• Plastic lumber