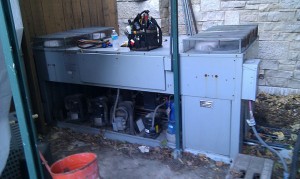
How do you pump down a carrier?
- Connect gauges to 25VNA8 liquid and vapor service valve.
- In the advanced menu of the UI, go to Checkout > Heat.
- Select mode to pump down in (COOL or HEAT), COOL.
- Select Start on UI to begin the pump- -down process.
- Close the liquid service valve.
- The unit will run in selected mode with the low pressure.
Full Answer
Can you pump down a non-recycling pump?
HVAC KNOW IT ALL | Apr 28, 2018 | Categories: Non-Recycling Pump Down , Recycling Pump Down , Refrigeration Pump Down Pumping down a refrigerant circuit is a great way to avoid liquid migration back to the compressor on the off-cycle. Refrigerant will naturally equalize and move to the section of the system with the lowest ambient temperature.
Are you looking for a simple solution to refrigeration rack systems?
In refrigeration racks. And the more compressors needed to control walk-ins, the larger the rack system must be to house the compressors. Traditional rack systems can weigh thousands of pounds and take up a good deal of space. Operators and consultants alike are looking for a simpler solution to refrigeration rack systems. And now there is one.
Why do we use a pump down type of refrigerant system?
If we lower the pressure in the crankcase to a point where the saturation temperature of the refrigerant is below the ambient temperature the compressor is in, the refrigerant cannot condense. This is why we use a “ pump down ” type system.
How does a pump down control work?
In operation, a pump down control consists of little more than a liquid line solenoid valve, a thermostat control, and a low-pressure control.
What is pump down control?
What is the most common control on refrigeration equipment?
What is refrigerant migration?
What is a crankcase heater?
How to prevent condensation in compressor?
What happens if you cycle a compressor off?
How low should I set my heatcraft vacuum?
See 2 more

How do you pump down a refrigeration system?
Pumping Down an AC or Refrigeration System Switch off the air conditioning unit.Connect the manifold to the low pressure service valve.Using your refrigeration service tools, release the nut on the service valve, to a mid-way position between fully opened and fully closed.More items...
What is purpose of pump down in refrigeration?
The purpose of a pump down system is to prevent liquid refrigerant from “migrating” back into the compressor during an off-cycle. This prevents catastrophic damage to the compressor when the system starts up.
What is pump out in refrigeration?
Pump-out systems, which used to be a relatively common component of many ammonia refrigeration systems, enable ammonia to be removed quickly and safely prior to maintenance work or system modifications.
Can you pump down a 410a system?
The scroll compressor can be used to pump down refrigerant in a unit as long as the pressures remain within the operating envelope. On a 410a compressor, do not allow pressure to go below 36 psi.
What happens during a pump down?
A system pump down utilizes a solenoid valve in the liquid line, when the system set-point temperature has been satisfied, the solenoid valve will close. The compressor will continue to pump refrigerant into the condenser and/or receiver, drawing it from the low side of the system.
What is mean by pump down?
A pump-down system consists of a normally closed solenoid valve installed in the liquid line and a low-pressure control that senses suction pressure. The system operation is as follows: A thermostat is wired to the liquid line solenoid valve. On a call for cooling, the thermostat contacts close.
How is air removed from a refrigeration system?
Refrigerant evacuation is the removal of moisture, air and non-condensable gases from a refrigeration system. During this process, a vacuum pump is used to draw the sealed HVAC system into a vacuum. This removes air, nitrogen and moisture from the unit.
When a system pumps down where is the refrigerant stored?
It typically takes less than 5 minutes to pump-down the average residential air conditioner or heat pump. He will definitely save time there. Simply closing off a valve in the liquid line and manually turning on the condenser the refrigerant is stored in the condenser to work on the low side of the system.
What PSI should 410A be at?
For R-410A, a working pressure capability of at least 400 psi is recommended (this includes recovery cylinders). Standard DOT recovery cylinders rated for 350 psi should not be used. Use only DOT recovery cylinders rated for 400 psi or higher when recovering R-410A.
Do you charge 410A as a liquid or vapor?
Unlike R-22 where refrigerant can be added in either the liquid or vaper state, blends like R-410a MUST be added in the liquid state only. In liquid form, R410a refrigerant is a 50/50 blend of R-32 and R-125.
Do you recover 410A as a liquid or vapor?
Liquid recovery is fast, but not all equipment can handle the process. Vapor recovery is slower, but is the most common recovery method used. The push-pull recovery method works best when recovering more than 10 pounds of refrigerant. all of your R-410A tanks and have them re-certified every five years.
What is the purpose of pumping down the vacuum chamber?
The evacuation of vacuum chambers, i.e. removing gas out of closed tanks in a given time, is one of the most common applications of vacuum pumps. In general, evacuation is the process of lowering the pressure in a chamber from a starting pressure to a target pressure.
What is an advantage of a pump down system over a standard refrigeration system?
The advantage of a pump down system is that the liquid refrigerant is stored in the receiver and condenser when the compressor is not operating. This prevents liquid migrating to the compressor crankcase during the off cycle and the ensuing possibility of liquid refrigerant in the oil during compressor start-up.
What is pump down in a vacuum?
A pump down curve describes a time- dependent pressure drop in a vacuum system. In a graphical representation, the time is applied to the X-axis and the pressure to the Y-axis. For the known geometry of the vacuum chamber and pumps, a pump down curve can be calculated.
What is the main purpose of a pump?
A pump is a device that moves fluids (liquids or gases), or sometimes slurries, by mechanical action, typically converted from electrical energy into hydraulic energy. Pumps can be classified into three major groups according to the method they use to move the fluid: direct lift, displacement, and gravity pumps.
What is pump down control?
In operation, a pump down control consists of little more than a liquid line solenoid valve, a thermostat control, and a low-pressure control. When the thermostat or defrost control opens, the solenoid de-energizes, stopping the refrigerant flow and allowing the system to pump the suction pressure down before the low-pressure control turns the compressor off.
What is the most common control on refrigeration equipment?
A very common means of control seen on refrigeration equipment is the pump down control . Why do we use this rather than just cycling the compressor off and on like a residential HVAC unit?
What is refrigerant migration?
Refrigerant migration is a natural process that occurs during the off-cycle. The refrigerants have an affinity for oil and seek out the lowest-pressure areas, so it only makes sense that some refrigerant would be drawn to the compressor crankcase and may condense there. When the refrigerants condense, they saturate the…
What is a crankcase heater?
One thing that is applied across almost all sectors of our industry is crankcase heaters. These small heaters, either immersion-style heaters or wrap-around style heaters, add a small amount of heat to help keep the compressor oil warm and help to prevent vapor from condensing there. The effectiveness of these is limited by the wattage of the heater, the ambient temperature, and the size of the compressor. Too low an ambient or too large a compressor, and they start to lose some effectiveness. ( Read more about crankcase heaters HERE .)
How to prevent condensation in compressor?
So, how else can we prevent condensation within the compressor? Let’s look at the pressure/temperature relationship of refrigerants for the answer. If we lower the pressure in the crankcase to a point where the saturation temperature of the refrigerant is below the ambient temperature the compressor is in, the refrigerant cannot condense. This is why we use a “pump down” type system.
What happens if you cycle a compressor off?
If the compressor cycles off for long enough, as it would during a defrost cycle, refrigerant vapor will start to condense within the crankcase. If we are lucky, the extent of this problem will be a unit that doesn’t start because the pressure of the refrigerant is lower than the cut-in setting of the pressure control. However, what typically happens is that enough refrigerant will condense to start to settle under the lubricating oil, causing a lack of lubrication upon restarting, leading to bearing wear and premature failure. If enough refrigerant condenses within the compressor housing, the resulting damage could cause valves, pistons, and other internal parts to break if liquid gets into the cylinders.
How low should I set my heatcraft vacuum?
How low should we set that cut-out? The Heatcraft installation manual has us setting the cut-out as low as 1” Hg vacuum, depending on the minimum expected ambient. I like to set the cut-in just below the lowest expected ambient temperature so that you don’t wind up in a situation like the one I mentioned earlier. If the ambient gets too low and the cut-in is too high, your unit won’t cycle on until it warms up enough, resulting in a preventable service call.
Why pump down refrigerant?
Pumping down a refrigerant circuit is a great way to avoid liquid migration back to the compressor on the off-cycle. Refrigerant will naturally equalize and move to the section of the system with the lowest ambient temperature. If that section happens to be anywhere on the low side of the system, we could potentially have a liquid slug on start up.
Does off cycle refrigerant creep?
However, if on the off cycle refrigerant is able to creep by internally leaking solenoid valves or compressor valve plates this will increase the low side pressure closing the LPS. In this case, the compressor will start and perform a pump down during the off cycle to ensure that liquid migration is not taking place.
Does a LPS compressor close?
The LPS will still close if valves are internally leaking by, but the compressor will not start until there is a call for cooling. A direct disadvantage of this method is quite obvious, the compressor may start with liquid refrigerant present in the sump.
How a Refrigeration Rack System Works?
A typical rack refrigeration system schematics and flow diagram is provided below. The principle followed is same as that of any refrigeration system. However the only major difference is in the configuration and number of components.
How does refrigeration work in racks?
In rack refrigeration system an extensive amount of refrigerant flows through refrigerant tubes going through processes of compression, conduction, expansion and evaporation. Then the refrigerant is dried and sent to the compressor after the extraction of water.
Why are multiple compressors connected to multiple refrigerated cases?
It consists of multiple compressors piped together connected to multiple refrigerated cases to provide more efficiency, more effectiveness and cover less space in large refrigeration requirements. It is sub-classified into several configuration from which you can choose depending upon your requirements.
Why use multiple parallel compressors in rack?
Using multiple parallel compressors in the rack are very useful. As they allow variable operation of refrigeration depending on how much cooling power is required.
What is the process of evaporation?
Evaporator allows the absorption of heat through the surrounding as the refrigerant moves through the refrigerant coils. The process is called evaporation.
What is the role of condensation in refrigeration?
Condenser plays the role of removal of heat from the refrigerant at high pressure . The heat removed from the refrigerant theoretically neither affects pressure nor temperature. Thereby in theory condensation is isobaric (constant pressure) as well as isothermal (constant temperature).
Which is better, refrigeration rack or refrigeration system?
But if we have multiple zones which have to be cooled. In this case refrigeration rack system performs better compared to traditional refrigeration system.
How many compressors does an RDT refrigeration rack use?
With an RDT refrigeration rack system comes a small footprint. Typically needing just two digital scroll compressors to cool all the fixtures of a foodservice operation, this rack system takes up minimal space on the roof as opposed to most traditional racks. The Eco-Cool system only requires one roof curb as opposed to the more common setups requiring multiple curbs.
Does a commercial kitchen have a walk in cooler?
Say your commercial kitchen has multiple walk-in coolers and freezers. It also has several prep tables that need proper cooling temperatures. For foodservice consultants or operators, this might present a complex challenge to implement an efficient refrigeration rack system.
What is pump down control?
In operation, a pump down control consists of little more than a liquid line solenoid valve, a thermostat control, and a low-pressure control. When the thermostat or defrost control opens, the solenoid de-energizes, stopping the refrigerant flow and allowing the system to pump the suction pressure down before the low-pressure control turns the compressor off.
What is the most common control on refrigeration equipment?
A very common means of control seen on refrigeration equipment is the pump down control . Why do we use this rather than just cycling the compressor off and on like a residential HVAC unit?
What is refrigerant migration?
Refrigerant migration is a natural process that occurs during the off-cycle. The refrigerants have an affinity for oil and seek out the lowest-pressure areas, so it only makes sense that some refrigerant would be drawn to the compressor crankcase and may condense there. When the refrigerants condense, they saturate the…
What is a crankcase heater?
One thing that is applied across almost all sectors of our industry is crankcase heaters. These small heaters, either immersion-style heaters or wrap-around style heaters, add a small amount of heat to help keep the compressor oil warm and help to prevent vapor from condensing there. The effectiveness of these is limited by the wattage of the heater, the ambient temperature, and the size of the compressor. Too low an ambient or too large a compressor, and they start to lose some effectiveness. ( Read more about crankcase heaters HERE .)
How to prevent condensation in compressor?
So, how else can we prevent condensation within the compressor? Let’s look at the pressure/temperature relationship of refrigerants for the answer. If we lower the pressure in the crankcase to a point where the saturation temperature of the refrigerant is below the ambient temperature the compressor is in, the refrigerant cannot condense. This is why we use a “pump down” type system.
What happens if you cycle a compressor off?
If the compressor cycles off for long enough, as it would during a defrost cycle, refrigerant vapor will start to condense within the crankcase. If we are lucky, the extent of this problem will be a unit that doesn’t start because the pressure of the refrigerant is lower than the cut-in setting of the pressure control. However, what typically happens is that enough refrigerant will condense to start to settle under the lubricating oil, causing a lack of lubrication upon restarting, leading to bearing wear and premature failure. If enough refrigerant condenses within the compressor housing, the resulting damage could cause valves, pistons, and other internal parts to break if liquid gets into the cylinders.
How low should I set my heatcraft vacuum?
How low should we set that cut-out? The Heatcraft installation manual has us setting the cut-out as low as 1” Hg vacuum, depending on the minimum expected ambient. I like to set the cut-in just below the lowest expected ambient temperature so that you don’t wind up in a situation like the one I mentioned earlier. If the ambient gets too low and the cut-in is too high, your unit won’t cycle on until it warms up enough, resulting in a preventable service call.
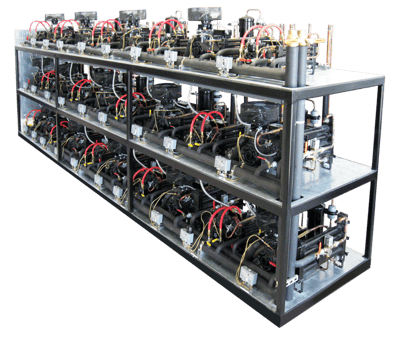