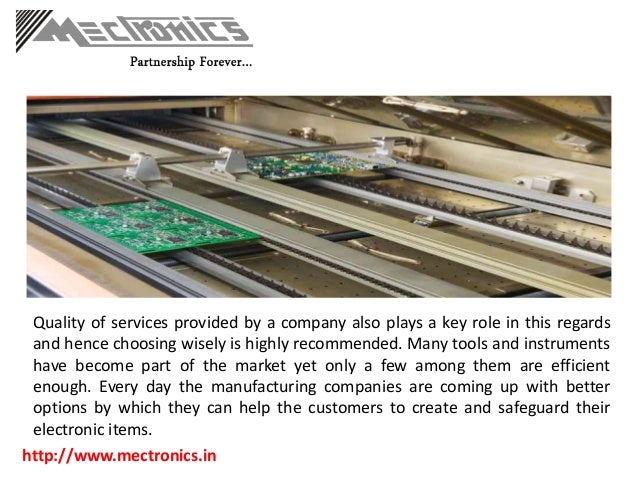
Basically, to perform reflow soldering, solder paste is placed on a printed circuit board, and the components to be soldered is placed on top of the solder paste. When the oven heats the solder paste past the melting temperature, the solder paste melts and solders the component to the circuit board.
- Preheat the oven to ~ 100 degrees Celsius.
- Insert board into the oven.
- Raise the temperature gradually up to 220 degrees and let it stay there for 1-2 minutes.
- Take out board and let it cool.
How to do reflow soldering?
To do reflow soldering, you should have the following tools: Solder paste in a syringe Flux Tweezers And one of the following: A hot plate/skillet A toaster oven A “real” reflow oven Apply flux Start the process by applying flux to the pads to make sure they are clean and will get heated properly. Apply solder paste
Can a toaster oven be used as a reflow soldering oven?
To solve this problem, I decided to hack a toaster oven to become a reflow soldering oven. Basically, to perform reflow soldering, solder paste is placed on a printed circuit board, and the components to be soldered is placed on top of the solder paste.
How to use a reflow oven?
A “real” reflow oven Apply flux Start the process by applying flux to the pads to make sure they are clean and will get heated properly. Apply solder paste Apply a dash of solder paste to each of the pads. You don’t need to be too precise with applying the solder paste.
How to use thermometer in soldering oven?
The first point: there are two kinds of thermometer, one is to start recording data immediately after triggering, which requires that the thermometer be put into reflow soldering oven in the shortest time after triggering, so as to ensure the accuracy of the measured reflow time.

Can you melt solder in an oven?
Other ways to do it is to use a heat gun, or toss it in the oven and hope for the best. I have taken old video cards and baked them at 390-400 for 10-15 minutes to reflow the solder. Keep in mind that the oven trick will void any warranty, but works well on cards that have all metal caps.
What temperature should I reflow solder?
The typical reflow temperature range for Pb-Free (Sn/Ag) solder is 240-250°C with 40-80 seconds over 220°C. It should be noted that the recommended Sn/Pb reflow temperature range are less critical, and that minor deviations in temperature of equipment and components generally do not create soldering problems.
How do you reflow a solder?
0:312:18What Is Reflow Soldering? - YouTubeYouTubeStart of suggested clipEnd of suggested clipWith all the devices in place on the printed circuit board the board is placed in an oven. WhereMoreWith all the devices in place on the printed circuit board the board is placed in an oven. Where it's raised to a temperature above the melting point of the solder.
How long does it take to reflow solder?
30 to 60 secondsThe time is usually 30 to 60 seconds and shouldn't be exceeded to avoid the formation of brittle solder joints. It is important to control the peak temperature during the reflow phase as some components can fail if exposed to excessive heat.
At what temperature does solder melt?
360 and 370 °FSoft solder typically has a melting point range of 90 to 450 °C (190 to 840 °F; 360 to 720 K), and is commonly used in electronics, plumbing, and sheet metal work. Alloys that melt between 180 and 190 °C (360 and 370 °F; 450 and 460 K) are the most commonly used.
Can you reflow solder with a heat gun?
A common heat gun is an inexpensive way to reflow, or reattach, electronic components that have been soldered together. While a regular hot-air solder rework station could cost more than $100, a common heat gun available from most home improvement stores should cost no more than $50.
Can you reflow a circuit board in an oven?
Preheat the oven to ~ 100 degrees Celsius. Insert board into the oven. Raise the temperature gradually up to 220 degrees and let it stay there for 1-2 minutes. Take out board and let it cool.
What is the purpose of reflow oven?
A reflow oven is a machine used primarily for reflow soldering of surface mount electronic components to printed circuit boards (PCBs).
Why is reflow soldering important?
Reflow soldering is the most widely used form of soldering for PCB assembly both in mass production and for prototype PCB assembly. Reflow soldering enables is reliable and effective for all pitches of leads and pads, enabling very high quality circuit boards to be manufactured.
What is reflow technique?
Reflow soldering is a type of soldering technique in which solder paste is applied over copper plates and melted to assemble electrical components on the board. In this, the board is subjected to controlled heat to prevent thermal shock.
At which zone the maximum allowable temperature of the reflow soldering process is reached?
Reflow zone An important consideration is peak temperature, which is the maximum allowable temperature of the entire process. A common peak temperature is 20–40 °C above liquidus.
What is the difference between reflow soldering and wave soldering?
The essential difference between wave soldering and reflow soldering lies in flux spraying — wave soldering contains this step, while reflow soldering does not. Flux enables dioxide elimination and surface tension reduction in the material to be soldered.
How many times can you reflow a PCB?
Our PCBs contain BGAs, leadless components and large fine pitch components. Most enterprise and telecom companies require the ability to withstand six thermal cycles (two reflows, wave, and three reworks).
What is the range of peak temperature reached at reflow zone of reflow soldering process?
Reflow zone An important consideration is peak temperature, which is the maximum allowable temperature of the entire process. A common peak temperature is 20–40 °C above liquidus.
What temperature do you bake a circuit board at?
If the boards are stacked on top of one another or flat on the base of the oven, etc., then it can be more difficult for the moisture to escape....PCB bake-out in a nutshell.ParameterExplanationBaking Temperature100-125°CDisadvantageHigher production cost and time2 more rows•Aug 13, 2020
What is soak time in reflow profile?
The results indicate a soak time of 60 seconds and time above liquidus of 60 seconds is preferred to achieve a thin IMC layer. The recommended time to peak temperature is 240 seconds and the soak temperature is 150°C.
Suitable Machine
There are various types of reflow soldering machine available depending on the required line speed and design/material of the PCB assemblies to be processed. The selected oven needs to be of a suitable size to handle the production rate of the pick and place equipment.
Acceptable Reflow Profile
In order to create an acceptable reflow profile each assembly needs to be considered separately as there are many different aspects that can affect how the reflow oven is programmed. Factors such as:-
Carefully printed PCB using well designed stencil
The earlier process steps within surface mount assembly are critical to an effective reflow soldering process. The solder paste printing process is key to ensure a consistent deposit of solder paste onto the PCB.
Repeatable placement of surface mount components
The placement of surface mount components must be repeatable and so a reliable, well maintained pick and place machine is necessary. If component packages are not taught in the correct way it can cause the machines vision system to not see each part in the same way and so variation in placement will be observed.
Good quality PCB, components and solder paste
The quality of all items used during the process must be high because anything of a poor quality will lead to undesirable results. Depending on the manufacturing process of the PCB’s and the way in which they have been stored the finish of the PCB’s can lead to poor solderabilty during the reflow soldering process.
Conclusion
The ideal reflow solder profile for each assembly does exist. The reflow soldering process can be time consuming to setup but is essential to ensure all components are fully soldered without being damaged.
An Increase in Efficiency and Productivity
It’s a shocking statistic to read that within the electronics industry many surface mount operations, particularly within the sub-contract manufacturing sector, run as low as 20% efficient. There are many reasons that contribute to this figure but it fundamentally means that only 20% of the capital investment is being utilized.
Step 1: Find a Toaster Oven
You're looking for two main things, an adjustable temperature knob, and a timer that will time down.
Step 2: Get a Thermometer and Timer
Even though the toaster oven has a temperature set point and an integrated timer, you still want to get some more accuracte readings. Get a cheap oven thermometer and toss it inside the oven and get a timer with an alarm to remind you to check on your baking PCBs.
Step 3: Make Your PCBs
In this exampe I'm working with an ADXRS300 which is a 1 axis Gyrometer made by Analog Devices. It comes in a ball grid array package with the balls already attached to the bottom of the component.
Step 4: Add Flux to the PCB
The balls in the BGA don't have flux so you *absolutely* have to put down flux on the board prior to doing the reflow. If you don't add flux then the oxide on the top of the pads will keep the balls from flowing and you'll end up with slightly squished balls that are not actually connected to the underlying PCB.
Step 5: Align the Components on the PCB
Position the PCB on the tray of the toaster oven, preferably oriented so that you can keep an eye on it through the window of the oven. Precisely position the component on the PCB using the silk screened outline to do the alignment.
Step 6: Start 'em Cooking
Close the toaster oven door, (make sure you don't bump the component out of alignment.) Set the temperature dial for somewhere around 450 and start the timer at around 20 minutes. Later on once you've determined the characteristics of your particular toaster oven then you can start using exact values.
Step 7: Watch the Temperature
Keep on eye on the thermometer. You'll have to check the reflow profile for your particular components to know what temperature you're trying to reach. In my case, the solder balls would start to melt at 183C and I wanted to hit a top temperature of 210C.