
In a hydraulic circuit, a hydraulic pressure regulator opens and bypasses fluid when pressure exceeds its setting. The valve then closes again when pressure falls. The valve acts as a pressure relief valve and can bypass fluid anytime without intervention.
What is a hydraulic pressure regulator?
Hydraulic pressure regulators maintain the output pressure of a hydraulic system at a set value to minimize fluctuations in a pressurized line. Hydraulic pressure regulators maintain a specific pressure range and are commonly known as unloading valves or unloading relief valves.
How does a hydraulic flow control valve work?
Within a hydraulic system, a flow-control valve will be used to control the rate of flow to hydraulic cylinders and motors, which in turn will impact the speed of both of those devices. Hydraulic flow-control valves also have a secondary function of managing the energy transfer rate at a specified pressure.
How do hydraulics work?
Learn how hydraulic systems work and see common examples from our everyday lives. So how do hydraulics work? They use Pascal's Law, which states that a pressure change on an incompressible fluid can be transmitted throughout that fluid.
What is the function of flow rate in hydraulic actuator?
A flow-control valve in any hydraulic system is tasked with the regulation of fluid speed, and by regulating the rate, it can control the speed of an actuator in the system. The flow rate is also responsible for determining the rate of energy transfer at any specific level of pressure.
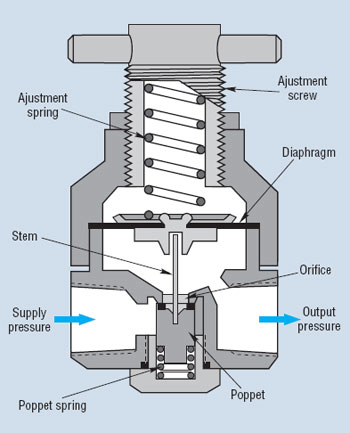
How does a regulator work?
0:134:27Understanding How Regulators Function - YouTubeYouTubeStart of suggested clipEnd of suggested clipThe basic function of a regulator is to control pressure reliably and consistently. You take theMoreThe basic function of a regulator is to control pressure reliably and consistently. You take the upstream. Pressure you regulate it down to a downstream.
How does a hydraulic reducing valve work?
Hydraulic reducing valves always have a drain line open to tank for control oil flow. Drain oil flows when reducing valve outlet is lower than its inlet. This generates a small amount of heat in the system. Blocking the drain line forces the valve wide open and lets outlet pressure rise to system pressure.
How do you adjust a hydraulic pressure regulator?
To adjust the spool valve, loosen the valve-locking nut on the side. Removing the locking nut gives you access to the adjustment screw. Turn the screw clockwise to raise the pressure, and twist it counter-clockwise to lower the pressure.
How does a pressure-reducing regulator work?
On the bottom of the diaphragm, the outlet pressure of the valve forces the diaphragm upward to shut the valve. When the outlet pressure drops below the set point of the valve, the spring pressure overcomes the outlet pressure and forces the valve stem downward, opening the valve.
What happens when a pressure regulator valve fails?
Symptoms of Regulator Failure If you have a regulator and it fails, you'll notice an immediate reaction in your home. For instance, you'll experience irregular water pressure that is hard to control with your sink, toilet, or bathtub faucets. The pressure is likely too high or too low.
How is hydraulic pressure controlled?
Pressure control is achieved in hydraulic systems by metering the flow of a fluid into or out of a constrained volume. Pressure control is achieved in hydraulic systems by metering the flow of a fluid into or out of a constrained volume. Relief valves and pressure-reducing valves are not pressure controllers.
What happens if hydraulic pressure is too high?
If the pressure is found to be too high, the system will use excessive input energy and the fluid may overheat. In addition, excessive pressure may stress components and create a very real danger to humans.
What causes hydraulics to run slow?
The most common causes of poor hydraulic performance are particulate contamination, water contamination, clogged filters, high fluid temperature and incorrect hydraulic fluids.
How do I know if my hydraulic pressure valve is bad?
3 Signs Of Pressure Relief Valve FailureSystem Cannot Reach Pressure. If your system isn't reaching pressure, this could be a sign of pressure relief valve failure. ... System is Over Maximum Pressure. ... Pressure Relief Valve is Leaking or Has No Pressure.
What are the two types of pressure regulators?
There are basically two types of regulators: one regulates upstream pressure (back-pressure regulators) and the other regulates downstream pressure (pressure-reducing regulators).
Can a pressure regulator increase pressure?
The pressure regulator is designed to regulate pressure. This does not always mean it can increase pressure. The regulator can only increase pressure if additional pressure is available.
Does a pressure regulator affect flow?
Pressure regulators are not designed to control flow rates. Although pressure regulators used in flowing systems inherently affect the flow by controlling the pressure, they are not designed to act as flow controllers.
What is the purpose of reducing valve?
The reducing valve is a regulating device which serves to reduce the air pressure supply to the required delivery pressure.
How do you adjust a pressure reducing valve?
Many valves have a nut, screw, or knob attached to them that allow you to do the actual adjusting. Turning the screw or knob clockwise typically increases the water pressure while turning it counter-clockwise lowers the pressure.
How does a hydraulic counterbalance valve work?
Counterbalance valves are hydraulic devices that function using this basic principle: fluid can freely flow through a check valve into the actuator, and reverse flow will be blocked using a relief valve until a pre-set pressure is reached that is set based on the system pressure and load capability.
How does a 3 way pressure reducing valve work?
The function of the 3-way pressure reducing valve is to maintain a constant set pressure at port A, against fluctuating supply pressures and loads from consuming devices. This valve is a combination of a pressure reducing valve and pressure relief valve.
What is a hydraulic pressure regulator?
Hydraulic pressure regulators maintain a specific pressure range and are commonly known as unloading valves or unloading relief valves. In hydraulic power systems, these regulators both unload the fluid being pumped and regulate a set operating pressure.
Why do hydraulic pumps need an unloading valve?
All positive displacement fixed-volume pumps for hydraulic circuits require an unloading valve to protect the system from excess pressure. Fixed-volume pumps move a set amount of fluid when they turn, regardless of pressure. If the system is not using that fluid it must be relieved to prevent system overpressure.
When is a relief valve required?
When a pump is unloading through an open-center circuit or actuators are in motion, fluid movement is not a problem. When actuators or motors stop with a valve still sending fluid to those devices, a relief valve is required.
Do hydraulic pumps bypass fluid?
A well-designed circuit rarely bypasses fluid unless there is a malfunction. Limiting bypassed fluids eliminates most overheating problems and saves energy.
How does hydraulics work?
Hydraulic systems use liquid to transfer energy from one part of a machine to another. You'll find them on the construction site and in factories, but you can find hydraulic systems in your household, as well. Learn how hydraulic systems work and see common examples from our everyday lives. hydraulic systems diagram.
What is the law of hydraulics?
They use Pascal's Law, which states that a pressure change on an incompressible fluid can be transmitted throughout that fluid. Hydraulic systems allow a user to exert force on one part of the system, which applies the pressure to the liquid and sends the energy to another part of the system, where it is converted to do work. YouTube.
What is hydraulic jack?
Hydraulic jacks help you lift heavy loads, such as cars, large containers and even house foundations. They're most often found in mechanic shops. Hydraulic jacks are more powerful than the emergency mechanical jacks used to change tires.
What are the systems of an airplane?
Airplane Systems. Hydraulic systems are present all over airplanes, including in their landing gear, doors, wing retraction, brakes, and steering systems. Even the earliest airplanes used hydraulic brake systems.
What is hydraulic steering?
Every turn of the wheel created pressure that was then carried through the entire steering system to turn the car in the desired direction. Although hydraulic steering systems can still be found in the automotive market, modern vehicles are typically equipped with the more fuel-efficient electric power steering systems.
How does the heart pump work?
Your heart (the pump) uses electrical energy to send oxygen via pressurized blood (the fluid) through the tubing (your veins and arteries) to different areas of the body (the actuators). This hydraulic system does the most important work of all — keeping you alive!
Why is hydraulics important?
Hydraulic systems allow us to complete large jobs with minimal effort. Without hydraulic systems, industrialized countries might not be so industrialized. They are a prime example of the power of engineering and how it helps us function in our modern world. Learn more about engineering affects your day-to-day life with these examples of mechanical energy that you see every day.
What is the principle of hydraulics?
The science behind hydraulics is called Pascal's principle. Essentially, because the liquid in the pipe is incompressible, the pressure must stay constant all the way through it, even when you're pushing it hard at one end or the other. Now pressure is defined as the force acting per unit of area. So if we press down with a small force on a small area, at the narrow end of the tube on the left, there must be a large force acting upward on the larger area piston on the right to keep the pressure equal. That's how the force becomes magnified.
How does a hydraulic digger work?
When the driver pulls a handle, the digger's engine pumps fluid into the narrow pipes and cables (shown in blue), forcing the hydraulic rams (shown in red) to extend. The rams look a bit like bicycle pumps working in reverse. If you put several rams together, you can make a digger's arm extend and move much like a person's—only with far greater force. The hydraulic rams are effectively the digger's muscles:
Why is hydraulics used in heavy duty machines?
Hydraulics runs this process in reverse to produce lower speed but more force, which is used to power heavy-duty machines. It's exactly the same in a water pistol, which is effectively just a syringe shaped like a gun. The fact that liquids don't compress easily is incredibly useful.
How does water get forced through a pistol?
Because the water won't squeeze into a smaller space, it gets forced through the body of the pistol to the narrow nozzle and squirts out with less force but more speed.
Which direction does a hydraulic ram move?
Photo: A hydraulic ram moves either inward or outward depending on which direction the hydraulic fluid is flowing.
Who wrote Understanding Hydraulics?
Understanding hydraulics by Leslie Hamill. Palgrave Macmillan, 2011. A huge and very popular introduction to hydraulics for college-level engineering students.
What is the connection between a water pistol and a crane?
W hat's the connection between a water pistol and this gigantic crane? On the face of it, no connection at all. But think about the science behind them and you'll reach a surprising conclusion: water pistols and cranes use the power of moving liquids in a very similar way. This technology is called hydraulics and it's used to power everything from car brakes and garbage trucks to motorboat steering and garage jacks. Let's take a closer look at how it works!
What are regulators made of?
Common regulator component materials include brass, plastic, and aluminum. Various grades of stainless steel (such as 303, 304, and 316) are available too. Springs used inside the regulator are typically made of music wire (carbon steel) or stainless steel.
What are the parts of a regulator in contact with the fluid called?
The parts of the regulator in contact with the fluid are known as the “wetted” components.
Why does my regulator droop?
As the inlet pressure rises from the initial setting, the outlet pressure falls. Conversely, as the inlet pressure falls, the outlet pressure rises.
What are the factors to consider when choosing a pressure regulator?
Important considerations include: operating pressure ranges for the inlet and outlet, flow requirements, the fluid (Is it a gas, a liquid, toxic, or flammable?), expected operating temperature range, material selection for the regulator components including seals, as well as size and weight constraints.
How to determine the accuracy of a pressure regulator?
The accuracy of a pressure regulator is determined by charting outlet pressure versus flow rate. The resulting graph shows the drop in outlet pressure as the flow rate increases. This phenomenon is known as droop. Pressure regulator accuracy is defined as how much droop the device exhibits over a range of flows; less droop equals greater accuracy. The pressure versus flow curves provided in the graph “Direct Acting Pressure Regulator Operating Map”, indicates the useful regulating capacity of the regulator. When selecting a regulator, engineers should examine pressure versus flow curves to ensure the regulator can meet the performance requirements necessary for the proposed application.
Why are pistons sluggish?
Piston designs tend to be sluggish, as compared to diaphragm designs, because of the friction between the piston seal and the regulator body. In low pressure applications, or when high accuracy is required, the diaphragm style is preferred.
Why is a non-relieving regulator used?
A non-relieving regulator is preferred for use with hazardous, explosive, or expensive gases because the design does not vent excessive downstream pressure into the atmosphere.
Where does oil go in a hydraulic lifter?
Similar in operation to the hydraulic piston of a tractor bucket, engine oil flows to the cavity in the hydraulic lifter. When the valve is closed the lifter is on the base circle of the cam (the round part of the lobe) and its cavity fills with oil. The internal piston is now at its maximum travel upward since the oil is below it.
What is the difference between a solid lifter and a hydraulic lifter?
The difference in lifter design. For our discussion a solid lifter is as its name implies: one piece of metal. It can be considered simply a means to transfer camshaft lobe action to the pushrod. In contrast, a hydraulic lifter is hollow, has an internal piston, spring, and allows oil to enter and exit. Similar in operation to the hydraulic piston ...
What is the valve lift of a 1.6:1 engine?
For example, if the cam lobe is 0.350 inch and the rocker arm ratio is 1.6:1, the valve lift would be 0.350 X 1.6 = 0.560 inch, if the engine used a hydraulic lifter, which has no lash. However, if it were a mechanical design with 0.020-inch lash, then the valve lift would be 0.540 inch.
What determines the action of a valve?
It’s the profile of the camshaft lobe that determines the valve action, and that motion is first transmitted to the valve lifter and onto the pushrod and finally the rocker arm that contacts the stem of the valve.
How does oil work in camshaft lift?
During the lift of the camshaft and due to valve spring pressure, oil is forced from the lifter cavity by the time the lifter dwells on the nose of the lobe. Once the travel of the lifter on the lobe is complete, the pressure from the pushrod is decreased on the piston and it enters its at-rest position. The cavity is now replenished with oil.
What is the role of the camshaft in a cam in block engine?
In a cam-in-block engine, this is accomplished by the camshaft working with intermediate components: valve lifter (or tappet), pushrod, and rocker arm.
Why is my hydraulic lifter noisy?
If an engine with hydraulic lifters is noisy, either the internal spring has lost some tension or the check ball is not sealing or allowing the oil to fill the cavity. The remedy is to replace the tappet.
