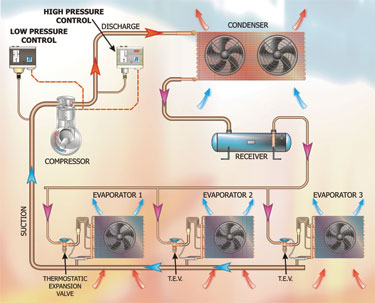
How does a pressure regulator work? The control knob is lifted and turned in a clockwise direction. This compresses a spring, which in turn places the load on the diaphragm assembly.
How do pressure monitoring and controls work?
There are two options that engineers can use to incorporate pressure monitoring and controls into their system. Pressure transducers use a variety of measuring techniques to take a pressure reading and turn it into an electrical signal. The electrical signal will normally be fed from the transducer and into the controller.
How does a pressure control valve work?
Most of the pressure control valves have their outlet diameter bigger than the inlet so that pressure can be reduced. The opening and closing of the pressure control valve are done with the help of piston and spring. The spring force can be changed so that the opening and closing speed of the valve can be changed.
How does a water pressure regulator work?
An adjustable spring-loaded diaphragm inside a water pressure regulator reduces the pressure of the water in the line within the valve body. Water coming into the valve is constricted and then released at reduced pressure.
How does an automatic water pump controller work?
With an automatic pressure controller, you don’t need to turn on your pressure booster or pressure pump every time you want to take a shower or wash the dishes. By opening a tap or sink, the electronic controller will automatically start the pump. It protects your water pump from damage with its built-in features.

What are the two types of pressure controllers?
There are basically two types of regulators: one regulates upstream pressure (back-pressure regulators) and the other regulates downstream pressure (pressure-reducing regulators).
How does a pneumatic pressure controller work?
When the liquid level decreases and the displacer reaches a low set point, the level controller removes the pneumatic signal to the valve and switches to vent. This allows the gas inside the valve actuator to vent through the level controller, which closes the valve.
How does a pressure regulator work water?
How does it work? An adjustable spring loaded diaphragm inside a water pressure regulator reduces the pressure of the water in the line within the valve body. Water coming into the valve is constricted and then released at a reduced pressure.
What are three types of pressure regulating devices?
Among the types of pressure regulators are back pressure, vacuum pressure, differential pressure, pressure-reducing and regulators for specific kinds of fluids like oil and fuel. The most important parameter to consider when specifying pressure regulators is the regulating or adjustment range.
What happens when a pressure regulator valve fails?
Symptoms of Regulator Failure If you have a regulator and it fails, you'll notice an immediate reaction in your home. For instance, you'll experience irregular water pressure that is hard to control with your sink, toilet, or bathtub faucets. The pressure is likely too high or too low.
How many psi should house water be?
between 40 and 60 PSINormal water pressure is generally between 40 and 60 PSI. Most homeowners prefer something right in the middle around 50 PSI. Once you measure the water pressure in your house, you can adjust it to a setting that is ideal for all family members and household uses.
What PSI should my pressure regulator be at?
Do I need a water pressure regulator? Building code requires that homes that receive water with pressure greater than 80 PSI have a water pressure regulator. A home's water pressure should stay in the range of 40 to 60 PSI.
How do you adjust the pressure on a water pressure regulator?
The screw acts as a water pressure regulator. If you tighten the screw the water pressure will be more and if you loosen the screw the water pressure will be less. Turn the screw clockwise to tighten it and increase the pressure, or turn it counterclockwise to decrease the pressure. Do not be too hasty.
How do you control pneumatic pressure?
Pressure is generally controlled by two valves. One valve functions as the inlet control, the other as the exhaust. In operation, internal pressure sensors track conditions and send signals to the electronic controller, which uses PID or similar algorithms to interpret the data.
How does a pneumatic transmitter work?
The force on the capsule is transmitted through a flexure to the lower end of the force bar. The metal diaphragm seal serves as both a fulcrum for the force bar and as a seal for the pressure chamber. The force is transmitted through the flexure connector to the range bar which pivots on the range wheel.
What is pneumatic control system?
WHAT ARE PNEUMATIC CONTROL SYSTEMS? Pneumatic control systems comprise equipment that utilise compressed air or gas, which is previously stored in a high-pressure tank, in order to direct energy.
What is the principle of pneumatic control and equipment?
A pneumatic control system uses compressed air that is carried through plastic and copper tubes—from a controller to a control device. Controlling systems with this method operate with the help of sensors and thermostats that can bleed or retain line pressure from the sensor to the actuator.
What is a pressure controller?
A pressure controller is more or less a pressure transducer and controller all packed into one device. That may sound appealing to nearly everyone, but caution should be taken when incorporating a pressure controller into any system. With every component built into one device, there is greater risk for the system if the pressure controller drastically fails. Pressure controllers generally have a limited number of inputs and outputs. In large systems, pressure controllers simply will not work.#N#For low-level applications this may be the best choice for your systems, as this device will be more cost-effective. The device will measure the pressure and control aspects of the system.#N#At the end of the day, it all depends on your system’s application and unique needs. Here are a few characteristics to keep in consideration when evaluating your system design. These will help get your head in the right space to think about the pressure transducer controller requirements.
How does a pressure transducer work?
Pressure transducers use a variety of measuring techniques to take a pressure reading and turn it into an electrical signal. The electrical signal will normally be fed from the transducer and into the controller. The controller, in this case, is a separate unit from the pressure transducer in the system. Most industrial and complex systems will require the controller to be separate from the pressure transducer in order to achieve the proper accuracy.#N#For systems where there are multiple pressure transducers, having the controller distinctly separate will allow for a more reliable system. With multiple pressure readings coming from multiple pressure transducers, having a central controller can be beneficial for a number of reasons. If your system is robust enough, having multiple pressure transducers and controllers is unavoidable. The controller can manage separate parts of the system and keep the system’s pressure in check.
How many inputs does a controller need?
Smaller systems, which are considered less than 300 inputs and outputs, do not need a complex controller to successfully operate. If your system has more than 300 inputs and outputs, you will be faced with a more sophisticated (and expensive!) controller.
Can controllers be programmed?
Most controllers can be programmed to meet a system’s specific needs. There are controllers that allow engineers to create highly customized programs that can accurately control the system’s various pressures. Some applications need very little programming as they are simply not that complex.
What is an automatic pressure controller?
Basically, an automatic pressure controller is a motor that will automatically switch on when water in the overhead tank (OHT) falls below the lower limit and vice versa. The circuitry behind it is straightforward, minimising the potential for electrical issues, and it is very energy efficient too.
How to protect electric pump from water damage?
If not already sealed, install a cover to protect the electrical components from water damage. If recommended by the manufacturer, use Teflon tape when installing to prevent any leaks. Make sure you consider using a barrel union between the pressure controller and the electric pump.
Why does my water pump break?
As you probably know, many factors can cause a water pump to break, such as running dry, leaks, flow switch jamming, water shortages and more. An automatic pressure controller is designed to help prevent all of these problems and more.
Do you need an electrician to connect a pressure controller?
An electrician may be required to connect an automatic pressure controller if not pre-integrated with a water pump. Durability and longevity can vary depending on the price point – more expensive devices will inevitably deliver better results and offer more features.
Do you have to turn on pressure booster?
With an automatic pressure controller, you don’t need to turn on your pressure booster or pressure pump every time you want to take a shower or wash the dishes. By opening a tap or sink, the electronic controller will automatically start the pump.
Can you shower without a pressure pump?
When showering at home without a pressure pump or automated pressure control, you might notice the water’s inconsistent temperature or intermittent water pressure. With a device that maintains a constant water flow, you’re bound to enjoy your showers a lot more.
Do pump controllers work the same?
Most automatic pump controllers do the same thing , but because there are so many applications and benefits to using one, there are also different types made depending on your needs.
What is pressure controlled ventilation?
Pressure-controlled ventilation is a modality utilized in patients with an indwelling endotracheal tube or tracheostomy tube that affords the practitioner the ability to ventilate a patient with a maximal peak pressure. In contrast to volume-controlled ventilation, pressure-control involves the selection of an inspiratory pressure instead of a tidal volume target. The setting of an inspiratory pressure, as well as an associated positive end-expiratory pressure (PEEP), will allow a provider to control the peak pressure, thereby protecting from barotrauma.
Why is pressure based ventilation important?
The ability to have direct control of airway pressure will aid in the prevention of lung injury. Also, utilizing a pressure-based approach will encourage a full distribution of all lung units regarding ventilation. This full distribution may aid in V/Q mismatch in patients with poorly complaint lungs in conditions such as ARDS. [4][5] In one particular study, researchers prospectively evaluated volume control against pressure control. This study also demonstrated that pressure control ventilation might provide the same support with lower peak airway pressures and lead to an improvement in thoracic static compliance. [6]
What is the role of tidal volume, FRC, and end-inspiratory volume in?
Role of tidal volume, FRC, and end-inspiratory volume in the development of pulmonary edema following mechanical ventilation.
When utilizing pressure control ventilation, respiratory therapists, as well as nursing, should be actively involved in the answer?
When utilizing pressure control ventilation, respiratory therapists, as well as nursing, should be actively involved in the co-management and surveillance of the patient on the ventilator while in the ICU or emergency room. Discussion as a collective team should take place at the time of deciding to place the patient on pressure control. Concerning features that require immediate intervention should also be discussed as a team at that time.
Is volume control better than pressure control?
While volume control is the more common mode of ventilation, patients may better tolerate pressure control ventilation. The critical difference in pressure control that may explain the difference in tolerance is the ability of the mode to maintain constant airway pressure by altering the inspiratory flow rates to meet the demand of the patient.[2] While tidal volume does vary in this mode, maintaining the constant airway pressure does permit improved alveolar distention universally instead of within regions that are more readily available. This generalized distention may also improve dead space ventilation, promoting active alveolar ventilation, which will result in improved comfort.
Does pressure control improve ventilator synchrony?
Although pressure control has demonstrated improved ventilator synchrony, some findings are observable on the ventilator display that indicates adjustments are necessary to continue to maintain optimum conditions [3]. These abnormalities will usually present themselves in the flow waveforms as they are the dynamic portion of the cycle. Figure 2 demonstrates a shortened inspiratory time, as shown by the flow waveform ending prematurely and not returning to zero before exhalation. Most commonly, this will require a change in the I to E ratio, which may result from changing the respiratory rate or improving airflow resistance at the time of exhalation.
How is pressure converted into electrical signal?
The conversion of pressure into an electrical signal, is achieved by the physical deformation of strain gauges, which are bonded into the diaphragm of the pressure transducer, and wired into a Wheatstone bridge configuration.
What is a pressure transmitter?
A pressure transducer often called a pressure transmitter, is a transducer that converts pressure into an analog electrical signal.
How much does it cost a pressure transducer?
There are a number of factors, that will impact the price of a pressure transducer.
What happens when the diaphragm is under pressure?
When the diaphragm is under pressure, it is sent to the measuring diaphragm, and the diaphragm is deformed under the action of pressure , which causes the relative position of the capacitive movable plate, and the spherical fixed plate to also change, and the capacitance changes in the motor.
What are the parts of differential pressure transmitter?
The installation of the differential pressure transmitter measurement system consists of three parts. Namely the laying of the pressure guiding tube, the laying of the electrical signal cable and the installation of the differential pressure transmitter .
What happens when pressure is applied to a transducer?
Pressure applied to the pressure transducer produces a deflection of the diaphragm, which introduces strain to the gages. The strain will produce an electrical resistance change proportional to the pressure.
How is chamber pressure applied to the isolating diaphragm?
The chamber pressure is applied to the isolating diaphragm on both sides of the δ element (ie, the sensitive element) by atmospheric pressure or vacuum , and is transmitted to both sides of the measuring diaphragm, through the spacer and the filling liquid in the element.
What is the primary concern of pressure regulators?
The primary concern is whether or not the elastomer chosen will function properly throughout the expected temperature range. Additionally, the operating temperature may affect flow capacity and/or the spring rate in extreme applications.
Why does pressure regulator hysteresis occur?
Hysteresis. Hysteresis can occur in mechanical systems, such as pressure regulators, due to friction forces caused by springs and seals. Take a look at the graph and you will notice, for a given flow rate, that the outlet pressure will be higher with decreasing flow than it will be with increasing flow.
Why does my regulator droop?
As the inlet pressure rises from the initial setting, the outlet pressure falls. Conversely, as the inlet pressure falls, the outlet pressure rises.
What are the factors to consider when choosing a pressure regulator?
Important considerations include: operating pressure ranges for the inlet and outlet, flow requirements, the fluid (Is it a gas, a liquid, toxic, or flammable?), expected operating temperature range, material selection for the regulator components including seals, as well as size and weight constraints.
How to determine the accuracy of a pressure regulator?
The accuracy of a pressure regulator is determined by charting outlet pressure versus flow rate. The resulting graph shows the drop in outlet pressure as the flow rate increases. This phenomenon is known as droop. Pressure regulator accuracy is defined as how much droop the device exhibits over a range of flows; less droop equals greater accuracy. The pressure versus flow curves provided in the graph “Direct Acting Pressure Regulator Operating Map”, indicates the useful regulating capacity of the regulator. When selecting a regulator, engineers should examine pressure versus flow curves to ensure the regulator can meet the performance requirements necessary for the proposed application.
What are the parts of a regulator in contact with the fluid called?
The parts of the regulator in contact with the fluid are known as the “wetted” components.
Why are pistons sluggish?
Piston designs tend to be sluggish, as compared to diaphragm designs, because of the friction between the piston seal and the regulator body. In low pressure applications, or when high accuracy is required, the diaphragm style is preferred.
When to use a pressure sensor?
Best use: When it’s a short distance between the transducer and the readout instrument, there is minimal electrical noise, or a more durable pressure sensor is required to withstand a harsh environment.
How does a static pressure transmitter work?
How static pressure transmitter works? Static pressure transducers measure the pressure of a fluid when it is at rest. Static pressure transducers are the most commonly used pressure monitoring devices. When a fluid exerts pressure on the pressure transducers, the strain gage (or the sensor) within it gets deformed.
What does a pressure transducer measure?
A pressure transducer measures pressure. It uses a sensor capable of converting the pressure acting on it into electrical signals. These electrical signals are then relayed to controllers or PLCs where they are then processed and recorded.
What sensors do pressure transducers use?
There are also advanced versions of pressure transducers that use capacitance or piezoelectric sensors instead of the strain gauges. They are chosen based on the range, work environment and precision required from the pressure sensor.
What is a piezoelectric transducer?
Piezoelectric pressure transducers are an example of non-static or dynamic pressure transducers. They cannot measure static pressure, instead, they measure pressure variances in real-time.
Why is my sensor not noisy?
The sensor should not be in an electrically noisy environment because the output signal is so low. However, these devices can easily handle harsher environments than other output types due to the output’s lack of signal conditioning stage and its compact design.
How many pressure references are there?
There are three defined pressure references for measuring pressure. While there are other types, like vacuum or sealed gage, all can be classified into these three categories. With diaphragm type pressure sensors, it is easiest to understand the reference pressure as the pressure that is exerted on the other side of the diaphragm from the process being measured.
How does a water pressure regulator work?
When the water enters the regulator at high pressure, the inner mechanism constricts the diaphragm to narrow the flow of water. This can reduce the pressure into ...
What is a pressure regulator?
A water pressure regulator (sometimes called a pressure-reducing valve, or PRV) is a specialized plumbing valve that reduces the water pressure coming into the home through the main water line. This valve brings down the pressure to a safe level before the water reaches any plumbing fixtures inside the home.
What happens when a water pressure regulator is used?
When the system is protected by a water pressure regulator, there is less stress on the inner valves of appliances, faucets and shutoff valves will be less likely to leak, and fluctuations in water pressure are evened out.
What pressure should I use for a water pressure regulator?
Most home plumbing fixtures are designed to work best at a pressure of about 50 psi (pounds per square inch), but it is not uncommon for municipal water supplies to enter the home with pressures as high as 150 or 200 psi. If such high pressures is present on a regular basis, the strain can eventually cause joints to fail, faucets and other fixtures to leak, and appliances to break down. Clothes washers, dishwashers, and some other household appliances have built-in pressure regulators, but a whole-house water pressure regulator still offers protection to those appliances, and it also serves to protect all the pipes and fixtures throughout the house.
Why is it important to have a water pressure regulator?
Too much water pressure can cause many plumbing problems, so it is very important to keep the water pressure under control. Although it is not necessary for every plumbing installation, a water pressure regulator can be essential in situations where the municipal water supply enters the home at a very high pressure, ...
Why tighten the adjustment screw on a water regulator?
An adjustment screw on the top of the regulator can be tightened to increase the tension on the inner spring (thereby reducing the pressure of the water as it exits the valve), or loosened to allow water to flow more freely through the valve (thereby increasing the outgoing water pressure). When the system is protected by a water pressure ...
Do dishwashers have pressure regulators?
Clothes washers, dishwashers, and some other household appliances have built-in pressure regulators, but a whole-house water pressure regulator still offers protection to those appliances, and it also serves to protect all the pipes and fixtures throughout the house.

Introduction
Pressure Controller
- A pressure controller is more or less a pressure transducer and controller all packed into one device. That may sound appealing to nearly everyone, but caution should be taken when incorporating a pressure controller into any system. With every component built into one device, there is greater risk for the system if the pressure controller drastically fails. Pressure controller…
Programmability
- Most controllers can be programmed to meet a system’s specific needs. There are controllers that allow engineers to create highly customized programs that can accurately control the system’s various pressures. Some applications need very little programming as they are simply not that complex.
Number of Inputs and Outputs
- The smaller the system is, the easier it is to find a controller that will suit your needs. Smaller systems, which are considered less than 300 inputs and outputs, do not need a complex controller to successfully operate. If your system has more than 300 inputs and outputs, you will be faced with a more sophisticated (and expensive!) controller.
Physical Environment
- The pressure transducer controller still has to function in the system’s environment. In many industrial applications the environment can be extremely harsh. Dust, high or low temperatures, high pressure, and many other factors can completely render a functional controller inoperable. There are many other factors that need to be considered, but these will give your team a startin…