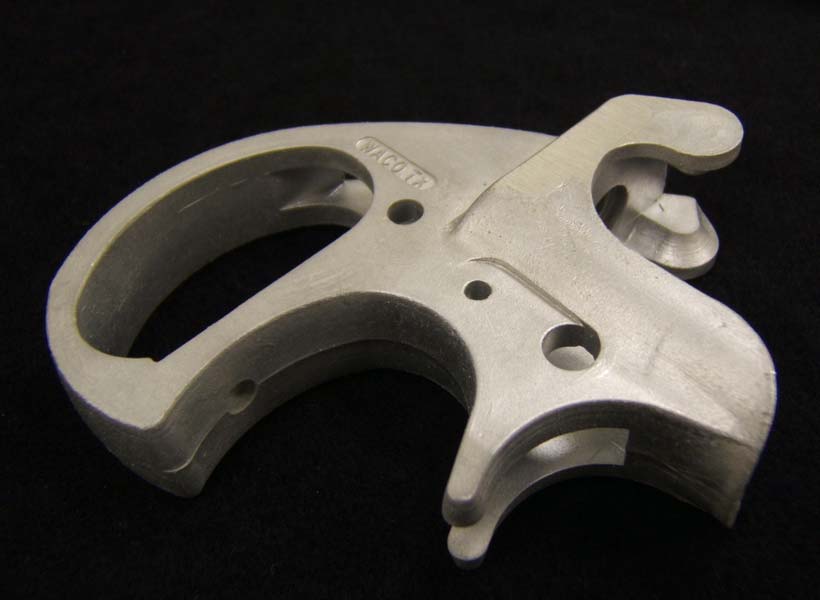
What is the cost of die casting?
- Generally speaking, the cost of the whole diecasting process ranges from $15,000 to $150,000 depending on the size,...
- Diecasting Cost Breakdown.
- Factors affecting diecast cost:. The massive obstacle for a potential diecasting consumer is the expense of tooling.
- Source.
What determines die casting cost?
The cost can be generally attributed to the following. Materials in die casting play a huge role in the die casting cost as they determine the type of mold you can make, the die casting process to use, and the quality of the casting itself. The cost also depends on the material’s weight, the part volume, material density, and unit price.
What is a die casting mold?
The die cast mold is the “container” with a design that the product will take into which you inject the molten metal. The die casting mold cost depends hugely on the mold, with materials and design playing a huge role.
Do Diedie castings need to be cooled?
Die castings are made from molten metal and need to be cooled property before it is removed from the cavity. Removing it before it cools and solidifies will compromise the structure. Some die casting companies will place a cooling circuit in the cavity block to save design and manufacturing costs.
How to choose the right die cast tool?
You want to make sure that the die cast tool is properly designed so that high-quality parts can be manufactured consistently. Using a low-quality tool increases the risk of casting mediocre parts, which may need post production corrections. This will no doubt drive up the overall cost of your project.

How much do die casting machines cost?
How much does a Hot Chamber Die Casting Machine cost? Because hot chamber die casting machines range in size from as small at 4 tons up to 1,200 tons the price varies dramatically. A 10 ton machine can cost as little as $30,000.00 and 1,200 ton machine can cost well over $1,000,000.00.
Why is die casting expensive?
The unavoidable fact is that die casting tooling costs are high, among the highest of any production process. This is because, due to the nature of die casting, the dies are subjected to exceptionally severe operating conditions over the course of normal service.
Is die casting cheaper than machining?
CNC machining tends to be more expensive than die casting, but this depends on the type of parts and level of production. Often, CNC machining is used to create the die, and/or to add more intricate features after a part has been die cast.
How much does it cost to have a casting made?
Sand casting pattern costs range from $500 to $7,500, depending on the size and complexity of the part. Because sand molds are relatively simple to make, there is a lower capital investment and lower tooling costs. Investment casting creates complex parts with excellent finishes from a ceramic mold tree.
Is die casting cost effective?
Die casting can be incredibly cost effective because one part can be designed to replace multiple components. It is also possible to incorporate other features into the casting that eliminate secondary milling, boring, reaming, and grinding operations.
How much is a die cast mold?
Tooling prices can run anywhere from $15,000 to $150,000 (for Lakeshore Die Cast's size range) depending on the size and complexity of the part.
Is die casting quick?
Die casting is fast and excellent for producing highly accurate and repeatable parts.
Is CNC better than cast?
One advantage of using CNC machining is that it is better for low volume parts since no tooling cost is required. Die casting is the preferred option if you're looking for a high volume of consistent, reliable parts. On the other hand, if your part has a lot of surface detail, you may prefer to use die casting.
Why is forging better than casting?
Forged steel is generally stronger and more reliable than castings and plate steel due to the fact that the grain flows of the steel are altered, conforming to the shape of the part. The advantages of forging include: Generally tougher than alternatives. Will handle impact better than castings.
What is diecast metal made of?
Die casting is a metal casting process that involves feeding molten nonferrous alloys into dies under high pressure and at high speed to rapidly create molded products. The main materials used in die casting are alloys of aluminum, magnesium and zinc.
How much does an aluminum casting cost?
Kinetic Die Casting Tooling Cost. Aluminum sand cast tooling costs from $500 to $7,500 depending on size and complexity of the aluminum casting part life is 5,000 parts. Aluminum die casting tooling costs from $5,000 to $75,000 depending on size and complexity of the aluminum die cast part.
Is cast Iron stronger than bronze?
Bronze is stronger than iron because it is an alloy of two other metals, making it denser and difficult to break with less friction. On the other hand, iron is a natural ore and less dense, and can be bent easily. Bronze can be melted easily, whereas iron needs a special furnace.
Is sand casting or die casting more expensive?
The pattern cost (tooling cost) of sand castings is much cheaper than die casting's, one set of die (pattern) for die casting may be 5 to 10 times more expensive than sand casting's.
What are the advantages of die casting?
Advantages of Die CastingDie casting provides complex shapes within closer tolerances than many other mass production processes.Die Castings are produced at high rates of production. ... Die casting provides parts which are durable, dimensionally stable, and have the feel and appearance of quality.More items...•
What are the advantages of die casting over sand casting?
Compared to sand casting, die casting produces parts that have thinner walls and smoother surfaces. They also have closer dimensional limits. Overall, the die casting process is much more economical than sand casting. The production is faster, finishing costs are lower, and significant overall savings are seen.
Is sand casting better than die casting?
Die casting can also produce features that cannot be made in sand casting, reducing the secondary costs over sand. If your company is a high-volume producer of products with a long service life (casting runs of 1,000 or more), the die casting process is most likely going to be the right choice over sand casting.
How to reduce cost of die casting?
In the die casting industry, optimization of mold design and reuse of existing molds is one of the most effective and practical ways to reduce the cost of die casting.
What is die casting?
Die casting is a casting method in which a molten alloy liquid is poured into a pressure chamber, where a cavity of a steel mold is filled at a high speed, and the alloy liquid is solidified under pressure to form a casting. The main features of die casting that distinguish it from other casting methods are high pressure and high speed.
How does material cost work?
The material cost depends on the weight of material required and the unit price of the material. The weight of the material is clearly the result of part volume and material density; but, the maximum wall thickness of parts can also work.
What affects the cost of a cold chamber machine?
In addition to the size of the machine, the type of machine (hot chamber and cold chamber) also affects the cost. The use of materials with high melting temperatures, such as aluminum, would require a more expensive cold chamber machine.
What factors affect die casting tool cost?
Tooling material is another factor that will influence die casting tool cost. Die casting mold should be evaluated according to the customer’s casting requirements and the number of die castings that are to be created.
Why is die casting important?
As such, it is important to make routine maintenance and timely repairs.
What is die casting tooling made of?
Because this process employs molten metals at very high temperatures and pressure, die cast tooling is created from special steels that can withstand these conditions.
Do die castings need to be cooled?
Die castings are made from molten metal and need to be cooled property before it is removed from the cavity. Removing it before it cools and solidifies will compromise the structure.
Do tooling inserts play a role in die casting?
Tooling inserts will also play a part in the total cost of your die cast mold. While some die cast companies may manufacture the tool as a whole, others incorporate smaller inserts into the design.
What is Die Casting?
Die casting is a process that involves melting low melting point metals and injecting them into already made mold known as die casting mold. A mold or tools come from steel fabricated for a single project using manufacturing processes such as CNC machining.
Steps of Die Casting Process
Whether hot or cold chamber die casting, the standard process involves injecting molten metal into a die mold under high pressure. Below are the intricate die casting process steps:
Die Casting Alloys
Most alloys used in die casting are non-ferrous with strong mechanical properties. The non-ferrous moiety is responsible for the low melting point in agreement with the strong mechanical properties. The type of properties needed depends on the material being worked on. Consequently, there is no limitation when choosing a material.
Surface Finish Options for Die Casting Parts
The diecast must have a good surface finish that will promote durability, protection, or aesthetic effect. There are different finishing options you can use for die casting parts. However, choices are based on the size of the cast parts and the alloy you are using.
Applications of Die Casting Parts
The die casting process is applicable in creating different parts and components that are truly unique and highly functional. Below are a few applications of the process:
Advantages of Die Casting Process
Die casting is an important metal fabrication method due to its low-cost production and ease of operation. However, there are other benefits of using the process: Here are the advantages of the die casting process.
Factors That Affect Die Casting Costs
Generally, die casting has a low-cost production. However, the cost depends on several factors. Below are a few factors you can consider when tailoring the best for your diecast project cost-wise.
What happens after a mold is delivered?
After the mold manufacturing is delivered for use, the production of the parts is started , and a part of the profit is extracted for each part produced and returned to the mold manufacturer as a mold fee.
What is settlement of mold?
The settlement of the mold is the ultimate goal of mold design and manufacturing. The price of the mold is also subject to the final settlement price, which is the settlement price. Is the final actual mold price.
What is Die Casting?
The die casting process consists of red hot liquid metal forced into a die under extreme pressure. In this scenario, the “die” is simply the steel mold which is created to shape the actual product that is being manufactured. Once the liquid metal is poured and injected into the mold, it solidifies, and then is removed from the mold. As soon as the liquid metal cools down, the gating material which is used as a protection source for the liquid metal, is removed and the product is finished. The steel mold is then closed and is immediately ready for your next casting project. This entire cycle is lightning fast, and lasts anywhere between thirty seconds and one minute.
What is the difference between sand casting and die casting?
The biggest and most obvious difference between the die and sand casting process is the materials used to form the molds. As we reviewed above, die casting uses a metal mold, while sand casting uses a mold made out of sand.
How is sand mold made?
The sand mold is created when a matchplate, or a pattern made out of wood or plastic, is placed into an enclosure. Sand is then distributed around the matchplate and inside the enclosure. Once the sand is packed in, the matchplate is then removed and the cavity is inserted with molten metal.
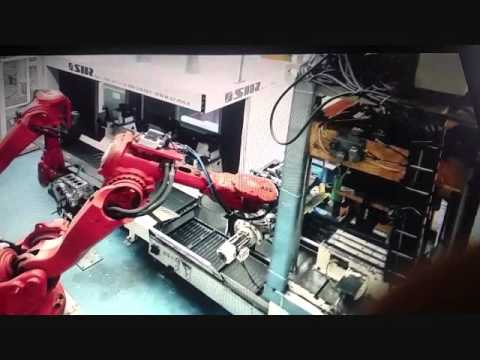