
A plasma cutter or plasma cutting system uses a plasma stream to transfer energy to a conductive work material. The plasma stream is typically formed by forcing a gas such as nitrogen, oxygen, argon Argon is a chemical element with the symbol Ar and atomic number 18. It is in group 18 of the periodic table and is a noble gas. Argon is the third-most abundant gas in the Earth's atmosphere, at 0.934%. It is more than twice as abundant as water vapor, 23 times as abundant …Argon
How do you set up a plasma cutter?
– [Complete Beginner’s Guide]
- Clean the Working Area. Before setting up a plasma cutter, ensure the working space is clean and free of any debris. ...
- Create a Stable Workspace. The next step is to set up a stable working surface. ...
- Plug in the Plasma Cutter. ...
- Connecting the Air Compressor. ...
- Turn on the Air Compressor. ...
- Attach the Ground Clamp. ...
- Turn on the machine. ...
- Setting the Amperage. ...
How to earn money with plasma cutters?
What are your business goals?
- Arrange Money. Next, you are need to arrange money actually lots of money for your new business. ...
- Register Your Business. Now you need to register your business formally, get authorizations and metal fabrication certifications.
- Start Your Business. Now, you are ready to start your metal fabrication business with CNC plasma table. ...
What to look for when buying a plasma cutter?
- High-performance and durable plasma machine
- Easy to operate
- Fitted with a 25-foot lead
- Suitable for heavy-duty cutting
- Comes with various torch styles
What can you do with a plasma cutter?
Plasma cutting is also used for repairing metals. Plasma cutters can be used for car repair, it can also work fenders, trailer hitches, quarter panels and mufflers. If you want to repair tractors, harvesters, watering tanks, implements, fencing and other elements, a plasma cutter is of great use for sure.

What is a plasma cutter made out of?
Plasma cutting is a process that cuts through electrically conductive materials by means of an accelerated jet of hot plasma. Typical materials cut with a plasma torch include steel, stainless steel, aluminum, brass and copper, although other conductive metals may be cut as well.
Are plasma cutters actually plasma?
States of Matter A plasma cutter can pass through metals with little or no resistance thanks to the unique properties of plasma.
What gas is used in plasma cutting?
Nitrogen is often used for higher current plasma systems and for cutting materials up to 3 inches thick. It produces excellent quality cuts on most materials. Oxygen is used when the highest quality mechanized cuts are desired on carbon steel up to 1 -1/4 inch thick. The cut face is smooth, and dross is easy to remove.
Can a plasma cutter cut your finger off?
0:047:46Can You Cut Your Finger Off with a Plasma Cutter? - YouTubeYouTubeStart of suggested clipEnd of suggested clipCut your body apart. Well. I did some research and it turns out that blood plasma is not the same asMoreCut your body apart. Well. I did some research and it turns out that blood plasma is not the same as plasma plasma.
What are the disadvantages of plasma cutting?
Unfortunately, plasma cutting does have a few drawbacks.Most plasma cutters aren't useful for thicker or denser metals. ... While it limits ambient heat, plasma cutting is noisy and generates excess fumes. ... Plasma is also infamous for creating very bright flashes while the cutting is ongoing.More items...•
Does a plasma cutter work underwater?
Stainless Steel and Aluminum up to 2 inches thick can be cut under water. This is achieved at 600 Amps with Nitrogen plasma, or up to 720 Amps with water-injection plasma. As with mild steel, the plate is submerged below 2 – 3 inches of water.
Can you use a plasma cutter without gas?
Do you need gas for a Plasma Cutter? Gas is needed for a plasma cutter in order for it to work and create the plasma. As mentioned, the most popular gases to use are oxygen, nitrogen or argon. Some plasma cutter systems include multi-gas features so a variety of gases can be used for different applications.
Does a plasma cutter require an air compressor?
First, the arc heats the metal until it's semi-gaseous. Second, the plasma is forced by blasts of air to finish the cut. Therefore, all plasma cutters need an air compressor to generate enough air pressure for the task. If you buy a plasma cutter without a built-in source of air, you'll need a separate air compressor.
How hot is plasma?
Source The core of plasma ranges in temperature from 11,000° – 14,500° Fahrenheit, thus limiting its applicable uses. As an ionized gas, plasma's electron density is balanced by positive ions and contains a sufficient amount of electrically charged particles to affect its electrical properties and behavior.
How loud is a plasma cutter?
It's about as loud as a two stroke chain saw about 30 feet away, or about the same as a loud toilet flush 3 feet away. Dry plasma cutting is going to range from around 90 to over 120 dB, which is well above the threshold that will cause hearing damage.
Can you heat metal with a plasma cutter?
No. Plasma cutters use a jet of air along with the arc to cut they pretty thoroughly oxidise the metal, plus the jet would just spray molten metal everywhere if you tried to contain it.
Will a plasma cutter cut painted metal?
Although plasma can cut through painted metal, it does require a solid connection on a clean part of the workpiece as close as practical to the work area.
Step 1: Assembly
When I started assembling my cutter, I began with taking a good look at my parts. As shown in Section 5 and Section 6, my parts are laid out so I can begin checking off from my parts list.
Step 7: Board Lay Out
Now this is to demenstrate how I set it up before putting it in a case configuration. So dont think you would leave it like this for it would be to dangerous to do so.
Step 8: Transformer I Used
Its a control transformer I got off ebay for 50 bucks. It's 220 to 120 3kva 25 amps and works great in power isolation.
Step 10: Power to Contactor Terminals
These are the contactor terminal conections on the transformer side and then the contactor to large bridge rectifier connections. Also you will see Bridge rec to Capitor connections and how they are connected. This is your Main Current set up.
Step 16: Head Air Coupling
here is where you will connect your air line to your head if you dont have a fitting to do so then hook to board connections.
Step 18: Final Power Connections
Ok now you can put all your final connections together and keep going over your schematic to double or triple check everything.
Step 19: Extra Photos of Past Cutter Projects
Here are some photos of past cutter projects for you to enjoy. Now remember that you will need to put in a case for safty. It can be would metal or plastic just enclose it. My photos are in a testing stage and that is why you see them exposed. The photos of the red cutter was a china one that burnt up on my neighbor and I ripped out the guts and replaced it with my design. He just loves it. The black box on side is the housing for 2 elements to draw more current. You will also see here some other designs where I used a chevy control module as the hv arc start and my first plasma cutter on test stand using stove coils as current resistors. Have fun and be safe ya'll.
What is plasma cutting?
Plasma Cutting is a profile cutting technique which can cut through any conductive metal. This includes metals like steel, aluminium, brass, titanium and copper - both thick or thin.
How does plasma cutting work?
Plasma cutting works by passing a super fast jet of hot plasma through conductive metals to cut through it.
What sort of work is plasma cutting used for?
Plasma cutting is used for all sorts of metal fabrication projects and is typically used in on-site construction or salvage yards. For designers and artists, the most common uses are in both signage and sculpture, as well as being used in decorative panels for interior projects.
Where can I find plasma cutters on Make Works?
There are a number of manufacturers in Scotland that use plasma cutting. For example you can have sheets CNC plasma cut at JGB Steelcraft or you can do it yourself at workshops such as Edinburgh Sculpture Workshop or Glasgow Sculpture Workshop.
How does plasma cutting work?
plasma from the plasma cutter itself, through the workpiece to be cut, thus forming a completed electric circuit back to the plasma cutter through a grounding clamp. This is accomplished by a compressed gas (oxygen, air, inert and others depending on material being cut) which is blown through a focused nozzle at high speed toward the workpiece. An electrical arc is then formed within the gas, between an electrode near or integrated into the gas nozzle and the workpiece itself. The electrical arc ionizes some of the gas, thereby creating an electrically conductive channel of plasma. As electricity from the cutter torch travels down this plasma it delivers sufficient heat to melt through the workpiece. At the same time, much of the high-velocity plasma and compressed gas blow the hot molten metal away, thereby separating, i.e. cutting through, the workpiece.
How many kilowatts does a plasma cutter use?
Analog plasma cutters, typically requiring more than 2 kilowatts, use a heavy mains-frequency transformer. Inverter plasma cutters rectify the mains supply to DC, which is fed into a high-frequency transistor inverter between 10 kHz to about 200 kHz.
How does an electrical arc form?
An electrical arc is then formed within the gas, between an electrode near or integrated into the gas nozzle and the workpiece itself. The electrical arc ionizes some of the gas, thereby creating an electrically conductive channel of plasma. As electricity from the cutter torch travels down this plasma it delivers sufficient heat to melt ...
What shade of eye protection is best for plasma cutting?
Proper eye protection and face shields are needed to prevent eye damage called arc eye as well as damage from debris. It is recommended to use green lens shade #5. OSHA recommends a shade 8 for arc current less than 300 A, but notes that "These values apply where the actual arc is clearly seen. Experience has shown that lighter filters may be used when the arc is hidden by the workpiece." Lincoln Electric, a manufacturer of plasma cutting equipment, says, "Typically a darkness shade of #7 to #9 is acceptable." Longevity Global, Inc., another manufacturer, offers this more specific table for Eye Protection for Plasma Arc Cutting at lower amperages:
How thick can a plasma torch cut?
Plasma cutting is an effective way of cutting thin and thick materials alike. Hand-held torches can usually cut up to 38 mm (1.5 in) thick steel plate, and stronger computer-controlled torches can cut steel up to 150 mm (6 in) thick.
How many configurations of plasma cutting?
CNC plasma cutting configurations. There are 3 main configurations of CNC Plasma Cutting, and they are largely differentiated by the forms of materials before processing, and the flexibility of the cutting head.
What is plasma cutting?
Plasma cutting is a process that cuts through electrically conductive materials by means of an accelerated jet of hot plasma. Typical materials cut with a plasma torch include steel, stainless steel, aluminum, brass and copper, although other conductive metals may be cut as well. Plasma cutting is often used in fabrication shops, automotive repair and restoration, industrial construction, and salvage and scrapping operations. Due to the high speed and precision cuts combined with low cost, plasma cutting sees widespread use from large-scale industrial CNC applications down to small hobbyist shops.
States of Matter
A plasma cutter can pass through metals with little or no resistance thanks to the unique properties of plasma. So what is plasma?
What is Plasma?
If you boost a gas to extremely high temperatures, you get plasma. The energy begins to break apart the gas molecules, and the atoms begin to split. Normal atoms are made up of protons and neutrons in the nucleus (see How Atoms Work ), surrounded by a cloud of electrons. In plasma, the electrons separate from the nucleus.
Inside a Plasma Cutter
Inside a plasma cutter: The electrode is at the center, and the nozzle is just below it. The orange piece is the swirl ring, which causes the plasma to turn rapidly as it passes.
Plasma on the Job
In CNC (computer numerically controlled) cutting, you arrange your shapes on the computer screen and cut them automatically, without having to touch the material.
Plasma Art
In the past, plasma cutters were prohibitively expensive and were used primarily for huge metal-cutting jobs. In recent years, the cost and size of plasma cutters have dropped considerably, making them available for more personal projects.
How does plasma cutting work?
A plasma cutting system uses a plasma stream to transfer energy to a conductive work material. The plasma stream is typically formed by forcing a gas such as nitrogen, oxygen, argon — or even air — through a narrow nozzle.
What is plasma cutting software?
For mechanized cutting applications, plasma cutting software is used to program the cutting machine. In some cases the CNC software can be used to program individual parts or small runs, but most fabricators and manufacturers rely on software commonly referred to as CAD/CAM nesting software which offers far greater features and capabilities.
What is plasma used for?
Plasma is used in both handheld and mechanized systems to cut a wide range of conductive materials, including mild steel, carbon steel, stainless steel, aluminum, copper, brass, and other metals .
What is an air plasma torch?
Rather than the high frequency starting circuit above, air plasma torches typically use a moving electrode, or “blowback start” technology to ionize the gas. Torch – This serves as the holder for the consumable nozzle and electrode, and provides cooling (either gas or water) to these parts.
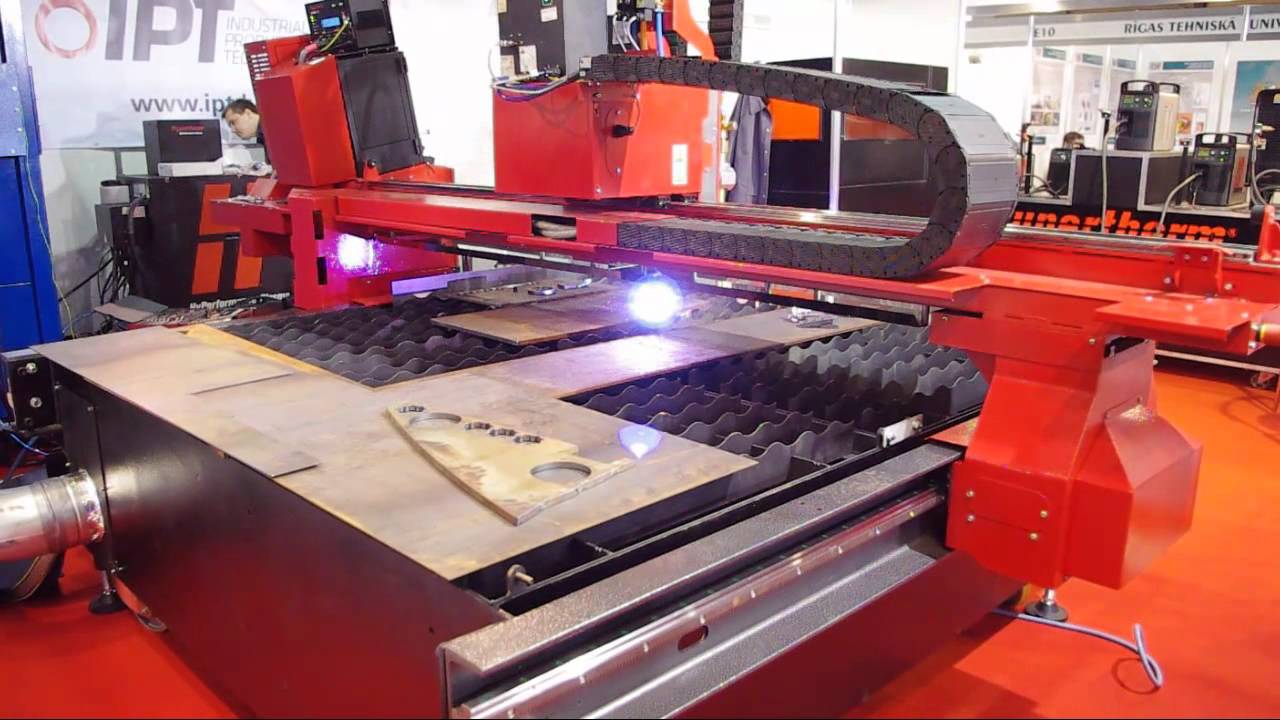
Overview
Plasma cutting is a process that cuts through electrically conductive materials by means of an accelerated jet of hot plasma. Typical materials cut with a plasma torch include steel, stainless steel, aluminum, brass and copper, although other conductive metals may be cut as well. Plasma cutting is often used in fabrication shops, automotive repair and restoration, industrial construction, and salvage and scrapping operations. Due to the high speed and precision cuts combined with low c…
History
Plasma cutting grew out of plasma welding in the 1960s, and emerged as a very productive way to cut sheet metal and plate in the 1980s. It had the advantages over traditional "metal against metal" cutting of producing no metal chips, giving accurate cuts, and producing a cleaner edge than oxy-fuel cutting. Early plasma cutters were large, somewhat slow and expensive and, therefore, tended to be dedicated to repeating cutting patterns in a "mass production" mode.
Safety
Proper eye protection and face shields are needed to prevent eye damage called arc eye as well as damage from debris. It is recommended to use green lens shade #5. OSHA recommends a shade 8 for arc current less than 300 A, but notes that "These values apply where the actual arc is clearly seen. Experience has shown that lighter filters may be used when the arc is hidden by the workpiece." Lincoln Electric, a manufacturer of plasma cutting equipment, says, "Typically a dark…
Starting methods
Plasma cutters use a number of methods to start the arc. In some units, the arc is created by putting the torch in contact with the work piece. Some cutters use a high voltage, high frequency circuit to start the arc. This method has a number of disadvantages, including risk of electrocution, difficulty of repair, spark gap maintenance, and the large amount of radio frequency emissions. Plasma cutters working near sensitive electronics, such as CNC hardware or comput…
Inverter plasma cutters
Analog plasma cutters, typically requiring more than 2 kilowatts, use a heavy mains-frequency transformer. Inverter plasma cutters rectify the mains supply to DC, which is fed into a high-frequency transistor inverter between 10 kHz to about 200 kHz. Higher switching frequencies allow smaller transformer resulting in overall size and weight reduction.
The transistors used were initially MOSFETs, but are now increasingly using IGBTs. With parallele…
CNC cutting methods
Some plasma cutter manufacturers build CNC cutting tables, and some have the cutter built into the table. CNC tables allow a computer to control the torch head producing clean sharp cuts. Modern CNC plasma equipment is capable of multi-axis cutting of thick material, allowing opportunities for complex welding seams that are not possible otherwise. For thinner material, plasma cutting is being progressively replaced by laser cutting, due mainly to the laser cutter's s…
CNC plasma cutting configurations
There are three main configurations of CNC plasma cutting, and they are largely differentiated by the forms of materials before processing, and the flexibility of the cutting head.
This is the most common and conventional form of CNC plasma cutting. Producing flat profiles, where the cut edges are at 90 degrees to the material surface. High powered cnc plasma cutting beds are configured in this way, able to cut profiles from metal plate up to 150 mm thick.
New technology
In the past decade plasma torch manufacturers have engineered new models with a smaller nozzle and a thinner plasma arc. This allows near-laser precision on plasma cut edges. Several manufacturers have combined precision CNC control with these torches to allow fabricators to produce parts that require little or no finishing.
The transistors used were initially MOSFETs, but are now increasingly using IGBTs. With parallel…