
Cement is the most common type of binder used for holding everything together on a construction site. It is made by grinding various mineral-rich rocks and mixing them with substances like sand, gravel, and mortar to produce concrete. Cement is a chemical combination of several minerals like calcium, aluminum, silicon, and iron ore.
Full Answer
What is cement made out of?
When the word cement is used alone, generally portland cement is meant. Portland cement is a powder that hydrates (combines chemically with water), to form a paste that binds sand, gravel, and stone into a rocklike mass called concrete.
What is Portland cement made of?
Portland cement is the basic ingredient of concrete. Concrete is formed when portland cement creates a paste with water that binds with sand and rock to harden. Cement is manufactured through a closely controlled chemical combination of calcium, silicon, aluminum, iron and other ingredients.
What is cement making dry process?
Nowadays, the dry process is the most popular cement making process which is widely adopted by cement plants all over the world for its great advantages in energy saving and environmental protection. The cement making dry process includes six phases:
What are the raw materials needed for cement production?
The raw materials needed for cement production mainly include limestone (main material, providing CaO), clay materials (providing SiO 2, Al 2 O 3 and a small amount of Fe 2 O 3 ), correction raw materials (to supplement some insufficient ingredients), and auxiliary raw materials (such as mineralizer, cosolvent, grinding aid), etc.
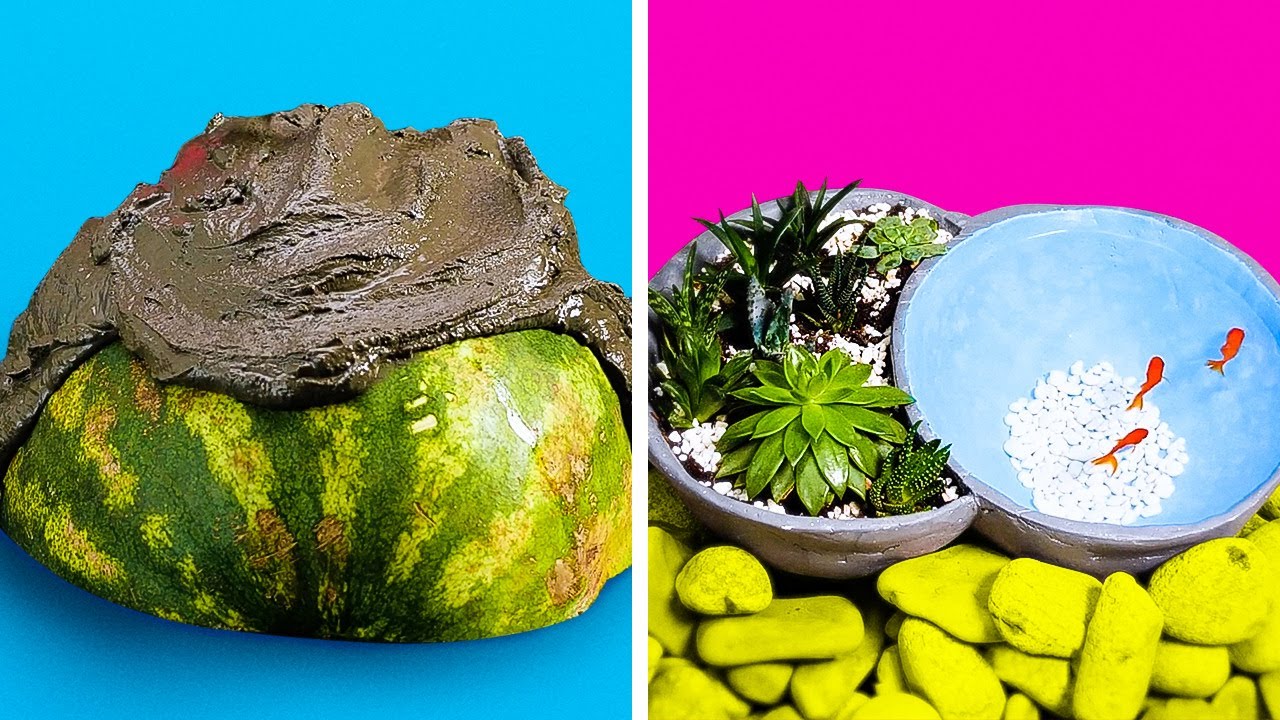
How do you make cement for kids?
3:2217:05Easy Make Concrete Kit. DIY with Kids - YouTubeYouTubeStart of suggested clipEnd of suggested clipWater sriracha water just water in a sriracha bottle you can put it in whatever kind of bottle youMoreWater sriracha water just water in a sriracha bottle you can put it in whatever kind of bottle you want but you want to make sure that it is easy to dispense small amounts of water at a time.
How are cement made?
Cement is manufactured through a closely controlled chemical combination of calcium, silicon, aluminum, iron and other ingredients. Common materials used to manufacture cement include limestone, shells, and chalk or marl combined with shale, clay, slate, blast furnace slag, silica sand, and iron ore.
How is cement made step by step?
There are four stages in the manufacture of portland cement: (1) crushing and grinding the raw materials, (2) blending the materials in the correct proportions, (3) burning the prepared mix in a kiln, and (4) grinding the burned product, known as “clinker,” together with some 5 percent of gypsum (to control the time of ...
How is cement made simple?
The clinker is ground to a fine powder in a cement mill and mixed with gypsum to create cement. The powdered cement is then mixed with water and aggregates to form concrete that is used in construction.
What is cement short answer?
A cement is a binder, a substance used for construction that sets, hardens, and adheres to other materials to bind them together. Cement is seldom used on its own, but rather to bind sand and gravel (aggregate) together.
How do you make cement from nature?
To make cement from scratch, buy or collect limestone and break it into 2 inch chunks. Put the chunks into a kiln, set the kiln to 900 °C, and let the limestone bake for 4-5 hours. Be sure to wear a respirator when you pull out the limestone, then let it cool completely.
What is used to make cement?
But cement isn't some sort of naturally occurring organic material - it's manufactured through the chemical combination of 8 main ingredients during the cement production process. These ingredients are generally extracted from limestone, clay, marl, shale, chalk, sand, bauxite, and iron ore.
What are the five stages of cement production?
And … Cement Substitutes1 Extraction. Materials are extracted / quarried / recovered and transported to the cement plant.2 Crushing and milling. The raw materials, limestone, shale, silica and iron oxice are crushed and milled into fine powders.3 Mixing and preheating. ... 4 Heating. ... 5 Cooling and final grinding.
What are the six steps to manufacture cement?
From the limestone quarry to the delivery of the end product, follow every step in the cement manufacturing process.Step 1: Mining. ... Step 2: Crushing, stacking, and reclaiming of raw materials. ... Step 3: Raw meal drying, grinding, and homogenization. ... Step 4: Clinkerization. ... Step 5: Cement grinding and storage. ... Step 6: Packing.
How do you make cement from scratch?
0:583:53How to Make Your Own Concrete | Ask This Old House - YouTubeYouTubeStart of suggested clipEnd of suggested clipSo we have three buckets of sand two buckets of aggregate. And one bucket of portland cement sandMoreSo we have three buckets of sand two buckets of aggregate. And one bucket of portland cement sand aggregate portland cement is this basic ingredient for all concrete.
Who invented cement?
Joseph AspdinCement as we know it was first developed by Joseph Aspdin, an enterprising 19th-century British stonemason, who heated a mix of ground limestone and clay in his kitchen stove, then pulverized the concoction into a fine powder.
Where is cement produced?
China produces the most cement globally by a large margin, at an estimated 2.5 billion metric tons in 2021. China's cement production share equates to over half of the world's cement. India was the world's second-largest cement producer, with production amounting to a distant 330 million metric tons in 2021.
What are the 4 main ingredients in concrete?
Concrete is a mixture of cement, air, water, sand, and gravel–it's as simple as that! Not exactly. The typical concrete mix is made up of roughly 10% cement, 20% air and water, 30% sand, and 40% gravel. This is called the 10-20-30-40 Rule–though proportions may vary depending on the type of cement and other factors.
Is there a difference between concrete and cement?
What is the difference between cement and concrete? Although the terms cement and concrete often are used interchangeably, cement is actually an ingredient of concrete. Concrete is a mixture of aggregates and paste. The aggregates are sand and gravel or crushed stone; the paste is water and portland cement.
Why is cement bad for the environment?
The cement industry is one of the main producers of carbon dioxide, a potent greenhouse gas. Concrete causes damage to the most fertile layer of the earth, the topsoil. Concrete is used to create hard surfaces which contribute to surface runoff that may cause soil erosion, water pollution and flooding.
What is the mix for cement?
In terms of the ratio for concrete, it depends on what strength you are trying to achieve, but as a general guide a standard concrete mix would be 1 part cement to 2 parts sand to 4 parts aggregates. For foundations, a mix of 1 part cement to 3 parts sand to 6 parts aggregates can be used.
What are the materials used to make cement?
Common materials used to manufacture cement include limestone, shells, and chalk or marl combined with shale, clay, slate, blast furnace slag, silica sand, and iron ore. These ingredients, when heated at high temperatures form a rock-like substance that is ground into the fine powder that we commonly think of as cement.
What is the most common way to make cement?
Although the dry process is the most modern and popular way to manufacture cement, some kilns in the United States use a wet process. The two processes are essentially alike except in the wet process, the raw materials are ground with water before being fed into the kiln.
How hot is a cement kiln?
The cement kiln heats all the ingredients to about 2,700 degrees Fahrenheit in huge cylindrical steel rotary kilns lined with special firebrick. Kilns are frequently as much as 12 feet in diameter—large enough to accommodate an automobile and longer in many instances than the height of a 40-story building.
What is Portland cement?
Portland cement is the basic ingredient of concrete. Concrete is formed when portland cement creates a paste with water that binds with sand and rock to harden. Cement is manufactured through a closely controlled chemical combination of calcium, silicon, aluminum, iron and other ingredients. Common materials used to manufacture cement include ...
What is the name of the substance that comes out of a kiln?
The remaining elements unite to form a new substance called clinker . Clinker comes out of the kiln as grey balls, about the size of marbles. Clinker is discharged red-hot from the lower end of the kiln and generally is brought down to handling temperature in various types of coolers.
What is the name of the substance that is formed by the burning of coal?
As the material moves through the kiln, certain elements are driven off in the form of gases. The remaining elements unite to form a new substance called clinker.
How big is a rock after quarrying?
After quarrying the rock is crushed. This involves several stages. The first crushing reduces the rock to a maximum size of about 6 inches. The rock then goes to secondary crushers or hammer mills for reduction to about 3 inches or smaller.
How is cement made?
The result is then sent to an oven that is shaped like a giant tube. The materials are heated to a very high temperature as they flow down the tube. Some of the materials melt. This liquid mixes with the solid materials to form cement chunks about the size of marbles. The chunks are called clinker.
What is the powder that makes concrete?
The fine powder called cement is one of the main ingredients of concrete. When cement combines with water it becomes a paste. This paste is used to hold together all of the other materials that make up concrete.
What was used to hold buildings together?
In ancient times people used clay or a paste made of ground-up stone and other ingredients to hold their buildings together. Over the years people tried other combinations of materials. In the 1800s they came up with the combination that is still used today.
What type of cement is used in portland?
Five types of portland cement are made in the United States. Type I , which dries gradually and continues to gain strength for years, is used in general concrete construction. Type II resists moderate exposures to sulfate-bearing waters. Type III, also called a “high early strength” cement, dries quickly to high strength. It is used for cold-weather construction. Type IV generates less heat in the hydration process than the other types. It may be used in massive concrete structures such as dams. Type V has a very high resistance to sulfate-bearing waters and soils.
What is Portland cement?
Portland cement is a powder that hydrates (combines chemically with water), to form a paste that binds sand, gravel, and stone into a rocklike mass called concrete.
Which country produces the most cement?
Measured by weight, concrete is the world’s most widely used building material. Therefore, cement is in great demand. China produces more cement by far than any other country. India, the United States, and Japan were other leading cement-producing countries at the start of the 21st century.
What did the ancient Egyptians use to build their pyramids?
The Assyrians and Babylonians had no better cement than this for their stone buildings. The Egyptians applied a thin lime mortar before they slid the stones of their Great Pyramid into position. The Greeks used little mortar, relying upon precise masonry and interlocking joints to fasten the stones of their great buildings.
What are the raw materials used in cement making?
Apart from limestone, there are also other raw materials used in the cement making process, such as clay, fly ash, iron ore, and coal. The need for these raw materials in cement production is relatively small so it is OK to just buy them from a supplier.
What is the most popular cement making process?
Nowadays, the dry process is the most popular cement making process which is widely adopted by cement plants all over the world for its great advantages in energy saving and environmental protection.
How does a roller crusher work?
In a roller crusher, the rotating table rotates continuously under the roller and brought the raw mix in contact with the roller. Roller crushes the material to fine powders and finishes the job. The raw mix is stored in a pre-homogenization pile after it was ground to fine powders.
What is the core phase of cement making?
The calcination is the core phase of the cement making dry process . The calcination of the preheated raw meal takes place in the rotary kiln of the cement plant. The rotary kiln is a huge rotating furnace in which the raw meal is heated up to 1450 ⁰C and turned to clinker.
What is the heat source of a rotary kiln?
The heat source of the rotary kiln is the flame from the burner locates on the kiln’s front end. Using natural gas or coal as fuels, the burner shoots high-temperature flames to calcine the raw meal. After calcination, the cement clinker will enter a cooler for cooling.
What happens when you heat up a rotary kiln?
The high temperature in the rotary kiln initiates a series of chemical reactions between calcium and silicon dioxide compounds, which eventually turn the raw meal into cement clinker.
What is portland cement?
It is widely used in civil engineering, water conservancy, national defense, and other projects. The most commonly seen and used cement is portland cement, or ordinary portland cement (OPC). This type of cement was invented in the early 19th century by Joseph Aspdin. It is named ‘portland cement’ because its property is similar to ...
