
Today’s steel is generally produced in one of two ways:
- Blast furnace: The blast furnace process, also known as the basic oxygen process (BOP), combines raw iron ore with small amounts of steel scrap metal into a furnace. Then, pure oxygen is blown into the furnace, raising its temperature. ...
- Electric arc furnaces: In the electric arc furnace (EAF) method, high-current electric arcs from electrodes melt large quantities of steel scraps into liquid. ...
What is the cheapest type of steel?
Water-Hardening Tool Steel As the cheapest type, water-hardening tool steel is the most widely used tool steel in the production of tools. To incorporate hardness into the objects or tools, this steel is water quenched. Featuring high resistance to surface wear, this steel is often used to make files, cutters, hammers, blades and similar items.
Which metal is harder, cast iron or stainless steel?
Which is stronger cast iron or stainless steel? The higher carbon content in cast iron makes it heavier and harder. However, this also makes cast iron more brittle. Stainless steel is lighter because it has a lower carbon content.
How much iron ore for a ton of steel?
Iron makes up close to 5% of the Earth's crust. It takes around 1.6 tons of iron ore to produce one ton of steel. The world uses 20 times more iron (in the form of steel) than all other metals put together. Our iron ore trains are over 2.5km (264 ore cars) long, meaning it can take half an hour to walk from one end to the other.
Is iron used for making steel?
Steel is made by putting iron through a process known as smelting, where iron is extracted from the iron ore and excess oxygen is removed and the iron is combined with chemical partners such as carbon. Steel, compared to pure iron is more rust resistant and has a better weldability.
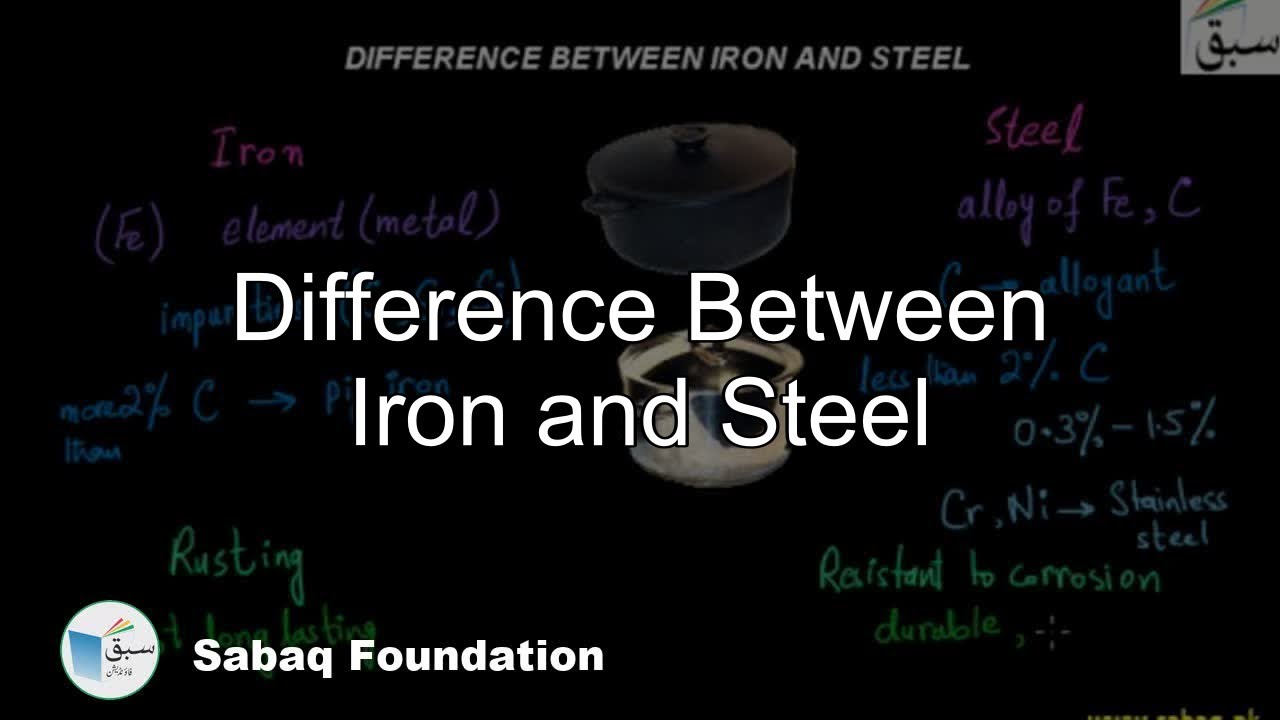
How is steel extracted from iron?
To make steel, the iron needs to be separated from the oxygen and a tiny amount of carbon needs to be added. Both are accomplished by melting the iron ore at a very high temperature (1,700 degrees Celsius or over 3,000 degrees Fahrenheit) in the presence of oxygen (from the air) and a type of coal called coke.
How is steel made step by step?
2:096:44STEEL: From Start to Finish - YouTubeYouTubeStart of suggested clipEnd of suggested clipIn fact we produce over 1,500 different chemistry's to meet customer demand for cutting-edge value-MoreIn fact we produce over 1,500 different chemistry's to meet customer demand for cutting-edge value-added steel look for another show of sparks as we tap molten steel from the bottle into a ladle.
How is metal obtained from iron ore?
Iron is extracted from iron ore in a huge container called a blast furnace. Iron ores such as haematite contain iron(III) oxide, Fe 2O 3. The oxygen must be removed from the iron(III) oxide in order to leave the iron behind. Reactions in which oxygen is removed are called reduction reactions.
How is steel made from iron and coal?
About 70 percent of steel today is made how it's always been made: in giant, extremely hot furnaces. Purified coal, or “coke,” is heated and melted with iron oxide and limestone, then injected with oxygen to reduce the carbon content of the mixture and to remove impurities.
What are the 4 methods of steel production?
In the steel production, following stages are identified: production of pig iron; production of liquid steel; hot rolling and cold rolling; applying a metallic and/or organic coating.
What are the three basic steel making processes?
Of the three major steelmaking processes—basic oxygen, open hearth, and electric arc—the first two, with few exceptions, use liquid blast-furnace iron and scrap as raw material and the latter uses a solid charge of scrap and DRI.
How is metal obtained?
Most metals are obtained in the form of compounds and they need to be filtered from their impurities to be further used for various applications. The process of procuring metals from ores is called metallurgy and these naturally occurring compounds of metals are known as minerals.
How is steel made chemistry?
Steel is made from iron by removing impurities and adding substances such as manganese, chromium, nickel, tungsten, molybdenum, and vanadium to produce alloys with properties that make the material suitable for specific uses. Most steels also contain small but definite percentages of carbon (0.04%–2.5%).
What is the process of making iron?
Iron is manufactured in a blast furnace. First, iron ore is mixed with coke and heated to form an iron-rich clinker called 'sinter'. Sintering is an important part of the overall process as it reduces waste and provides an efficient raw material for iron making. Coke is produced from carefully selected grades of coal.
Why is iron used in steel?
Steel is an alloy made up of iron with typically a few tenths of a percent of carbon to improve its strength and fracture resistance compared to other forms of iron. Many other elements may be present or added.
Can steel be made without coal?
Now, nearly all new steel globally is produced using iron oxide and coking coal. Coking coal is usually bituminous-rank coal with special qualities that are needed in the blast furnace. While an increasing amount of steel is being recycled, there is currently no technology to make steel at scale without using coal.
How was steel first made?
One of the earliest forms of steel, blister steel, began production in Germany and England in the 17th century and was produced by increasing the carbon content in molten pig iron using a process known as cementation. In this process, bars of wrought iron were layered with powdered charcoal in stone boxes and heated.
What are the 5 ways of making steel?
Manufacturing and Finishingshaping (cold rolling methods)machining (eg: drilling)joining (by means of welding)coating – galvanising with zinc, or cold coating and electro coating.heat treatment (usually tempering)surface treatment (carburising).
What is the process of steel making class 10?
In the primary steelmaking step, liquid iron is converted into steel by the basic oxygen furnace (BOF) process, or by melting scrap steel or direct reduced iron (DRI) in an electric arc furnace. Secondary steelmaking is a refining process in which alloying metals are added and impurities are removed.
How is steel made from scrap?
The main sources of steel scrap are automobiles, construction and ship-breaking. While most scrap is usually melted and re-used, a large part of ship-breaking scrap is re-rolled by steel mills into bars and rods for use in the construction industry.
How is metal made?
The first step in metal alloy manufacturing is extracting the raw ore from the ground. The ore is then processed to remove non-metal material, such as rock and debris. Metal alloys are then created by melting different metal substances and mixing them.
How is steel made?
At the most basic, steel is made by mixing carbon and iron at very high temperatures (above 2600°F).
What are the elements that make up steel?
Steel can also include other elements like nickel, molybdenum, manganese, titanium, boron, cobalt, or vanadium. Adding different elements to the “recipe” for a steel alloy affects its material properties. The method of manufacture and treatment of the steel further enhances those abilities.
What is secondary steelmaking?
Secondary steelmaking is done “in the ladle.”. It is a process of refining and alloying steel. Secondary steelmaking can start by melting scrap, or continues a primary process. Elements can be added to get a specific alloy.
How did oxidation help steelmaking?
In reaction to the air, impurities would oxidize and off-gas. Oxidization also helped create and sustain the high heat necessary for steelmaking. A process that once a full day in the foundry and more time in the forge was replaced with a 20-minute process that could create 5 tons of steel.
Why is steel used in construction?
Steel is so commonly used because of its specific material properties combined with its relative low cost. Compared to other many other building and tool making materials (like wood, stone, concrete, or cast iron), alloys of steel offer:
How many tons of steel are produced in 2019?
An introduction to the production and properties of steel alloys. A steelworker in a steel mill. According to the World Steel Association, 1869.9 million tons of steel were produced in 2019. This represents a 3.4% increase in output from 2018 and is more than double the output in 1999. The world has an ever growing need for steel.
When was steel invented?
Crucible steels, like the famous South Indian Wootz steel, were made consistently as early as the 4 th century BC. However, until the mid-1800s, steelmaking was incredibly challenging.
What is the first step in producing steel from iron oxides?
The blast furnace is the first step in producing steel from iron oxides. The first blast furnaces appeared in the 14th century and produced one ton per day. Even though equipment is improved and higher production rates can be achieved, the processes inside the blast furnace remain the same. The blast furnace uses coke, iron ore ...
How is coke made?
As the oven is heated, the coal begins to melt so most of the volatile matter such as oil, tar, hydrogen, nitrogen and sulfur are removed. The cooked coal, called coke, is removed from the oven after 18 to 24 hours of reaction time. The coke is cooled and screened into pieces ranging from one inch to four inches. The coke is a porous, hard black rock of concentrated carbon (contains 90 to 93 percent carbon), which has some ash and sulfur but compared to raw coal is very strong. The strong pieces of coke with a high energy value provide permeability, heat and gases which are required to reduce and melt the iron ore, pellets and sinter.
What is the process of combining raw iron ore with small amounts of steel scrap metal into a furnace?
Blast furnace: The blast furnace process, also known as the basic oxygen process (BOP), combines raw iron ore with small amounts of steel scrap metal into a furnace. Then, pure oxygen is blown into the furnace, raising its temperature. Not only does the scrap metal melt into a liquid at this temperature, but the iron’s impurities are also oxidized, evaporating completely. Additionally, the high temperature reduces the carbon content down to its ideal ratio, resulting in liquid steel.
When was steel made?
The modern-day steel production process began in 1856 under a process known as the Bessemer process. It’s largely considered to be the first process used to mass-produce steel. According to historians, two different inventors, one in the UK and one in Pittsburgh, both simultaneously developed a steel production process that involved removing iron’s impurities through the use of an air blast.
How does a furnace purify steel?
To purify the steel, the furnace then blasts in oxygen, and lime and fluorspar are added. These substances combine with the steel’s impurities, turning into slag. The slag then floats to the top of the molten steel where it is removed, leaving behind the pure steel.
What did blacksmiths do to iron?
These tradespeople learned to heat up iron ore, and using a hammer-and-anvil process, the blacksmiths would remove impurities from the metal and produce a durable and malleable final iron product. Iron took a few other forms before eventually arriving at what is today considered steel.
Why did blacksmiths coat iron in charcoal?
After cast iron, blacksmiths of Central Europe began coating wrought-iron products in charcoal to improve the iron’s strength while maintaining its flexibility. Afterward, iron went through a final iteration, which most resembles today’s steel material.
Why is steel important?
Since the Iron Age, humans have looked to perfect the steel manufacturing process, not only to produce it in greater quantities but to produce it more effectively. The continuous improvement of steel production is the reason why steel today has become such a crucial global commodity.
What is steel manufacturing?
Steel manufacturing is a critical industry that has a significant impact on our global economy. Since the mid-1800s, steel has become one of the most relied-upon materials globally, serving countless manufacturing and construction markets.
How is iron made?
The process of making iron begins with the preparation of the metallic ore. The first stage begins in the mine itself as the metallic ores are separated from the non-metallic earth and stones. The metallic ores are then removed from the mine and crushed into manageable pieces.
What is the difference between iron and steel?
The difference between iron and steel is based on the amount of carbon contained in the metal. If less than 0.1% carbon is present in the metal, it is termed wrought iron, ...
How is ore roasting done?
The ore is broken into pieces weighing 3-5 kg and placed on a sloping bed of coal 7 m long, 2.5 m long, and 15 cm deep.
Why is it important to roast hard ores?
Roasting ore serves two purposes. First, it softens hard ores, making them more easily broken or crushed, which helps the melting process . Secondly, roasting reduces the sulfur content of ores, which is harmful to the iron-making process.
What is wrought iron?
If less than 0.1% carbon is present in the metal, it is termed wrought iron, and it remains a ductile metal that can be heated and welded, but not hardened; it can be softened but not made fluid by an ordinary furnace, even with an intense blast.
What is cast iron?
The ability to cast iron made a strong and comparatively inexpensive metal available to the mass market, instead of the more expensive wrought iron and crucible steel bars which were beaten into strips and laminated into tools and weapons. The process of making iron begins with the preparation of the metallic ore.
Where was Damascus steel made?
Damascus steel was produced in India where it was called wootz. This steel was traded in the form of castings, cakes of metal, which were approximately the size of a hockey puck. The process began with wrought iron produced by the direct reduction of iron oxide to metal, as described above.
What is the process of making steel?
Modern steelmaking processes can be divided into two categories: primary and secondary. Primary steelmaking involves converting liquid iron from a blast furnace and steel scrap into steel via basic oxygen steelmaking, or melting scrap steel or direct reduced iron (DRI) in an electric arc furnace.
Where was steel made?
Early processes of steel making were made during the classical era in Ancient Iran, Ancient China, India, and Rome .
What is steel mill?
Steel mill with two arc furnaces. Steelmaking is the process of producing steel from iron ore and/or scrap. In steelmaking, impurities such as nitrogen, silicon, phosphorus, sulfur and excess carbon (the most important impurity) are removed from the sourced iron, and alloying elements such as manganese, nickel, chromium, ...
What is basic oxygen steelmaking?
Basic oxygen steelmaking is a method of primary steelmaking in which carbon-rich molten pig iron is converted into steel. Blowing oxygen through molten pig iron lowers the carbon content of the alloy and changes it into steel. The process is known as basic due to the chemical nature of the refractories — calcium oxide and magnesium oxide —that line the vessel to withstand the high temperature and corrosive nature of the molten metal and slag in the vessel. The slag chemistry of the process is also controlled to ensure that impurities such as silicon and phosphorus are removed from the metal.
How long does it take for a furnace to turn iron into steel?
Modern furnaces will take a charge of iron of up to 350 tons and convert it into steel in less than 40 minutes compared to 10–12 hours in an open hearth furnace. Electric arc furnace steelmaking is the manufacture of steel from scrap or direct reduced iron melted by electric arcs.
What is the difference between EAF and oxygen steelmaking?
Oxygen steelmaking is fueled predominantly by the exothermic nature of the reactions inside the vessel; in contrast, in EAF steelmaking, electrical energy is used to melt the solid scrap and/or DRI materials. In recent times, EAF steelmaking technology has evolved closer to oxygen steelmaking as more chemical energy is introduced into the process.
How to reduce carbon in pig iron?
To reduce the carbon content in pig iron and obtain the desired carbon content of steel, the pig iron is re-melted and oxygen is blown through in a process called basic oxygen steelmaking, which occurs in a ladle . In this step, the oxygen binds with the undesired carbon, carrying it away in the form of carbon dioxide gas, an additional source of emissions. After this step, the carbon content in the pig iron is lowered sufficiently and steel is obtained.
What is the process of calcination of iron ore?
The second step in the process is calcination or roasting of the ore, which removes certain impurities, carbon dioxide and other substances.
What is the second step in iron ore reduction?
The second step in the process is calcination or roasting of the ore, which removes certain impurities, carbon dioxide and other substances. Through this process, ferrous oxide also oxidizes to ferric oxide. The blast furnace reduces iron from the iron oxide, but the complete reduction reaction requires the addition of coke and limestone to ...
Why is heavy mining necessary?
The use of heavy mining equipment is necessary to dig out large pits in an area with a large deposit of iron ore ; however, because iron does not occur naturally, it is necessary to use a blast furnace to separate or refine iron from the other substances in the iron ore.
Is molten iron cast iron?
This molten iron may be utilized as cast iron. A high purity iron, such as wrought iron, requires the complete removal of carbon from this iron. Likewise, the steel-making process requires the removal of other impurities like sulfur and phosphorus from molten iron. Many other different types of steel also are fabricated from this molten iron.
How is Iron made?
Because Iron reacts so easily with oxygen to form iron oxide it does not exist on the surface of the planet in a usable form. The first step to process iron is to remove that oxygen. In the mid bronze age, the first signs of production of Iron are seen. Most of this early iron was smelted in these furnaces called bloomeries.
What is the difference between iron and steel?
The main difference between Iron and Steel is the amount of carbon they contain. Anything with a carbon content above 2% is cast iron. Higher carbon content typically results in a harder and less ductile material.
Why are iron cannons dangerous?
Iron was cheap to manufacture and could be fired more often without being damaged. However, these material properties meant that cast iron cannons had a tendency to explode without warning. This made them dangerous to operate.
Why were iron plows important?
Iron plows were stronger and heavier allowing farmers to plow their land quicker and thus grow more food. Likewise, iron scythes could cut more hay. A single farmer could feed more people, allowing more people to dedicate their lives to different trades. Society was becoming more stratified and trade was increasing and things began to accelerate even more as we discovered better ways of extracting iron, like the blast furnace.
How long did the Iron Age last?
If we continued to define human history by the materials being mastered at that time, it could be argued that the Iron age lasted right up until a little over 150 years ago , when steel was first mass-produced.
Why was meteoric iron important to Tutankhamun?
Meteoric iron was a highly prized material due to its heavenly association. Tutankhamun was buried with a dagger made of the material. But meteoric iron was the only naturally occurring source of iron at the time.
Who invented the method of mass production?
So you can see why finding a method of mass production was so important. And this is where the British Metallurgist Sir Henry Bessemer came in. Bessemer created a converter where molten iron was poured from a blast furnace and hot air is passed through the bottom. This oxygen in the air oxidizes the impurities in the iron. The carbon reacts to form carbon monoxide which is expelled as a gas.
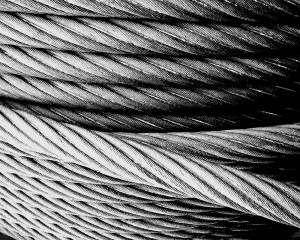