
Full Answer
How much does an air leak cost?
Cost of a 1/8″ diameter air leak for a year at 90 psi is $4.636.00.. Cost of a 1/8″ diameter air leak for a year at 125 psi is $6,186.00.. Cost of 31.54 scfm for a year: 31.54 x 60 minutes per hour = 1892.4 cubic feet per hour
How to find and seal air leaks in your home?
- On a cold day with the heat on inside your home, place your hand around the edges of all exterior doors, windows, and bathroom and kitchen air vents and fans. ...
- You can also use the hand test to detect leaks around electrical outlets.
- The hand test is best for finding large leaks of air coming into the home.
How to fix air leaks?
- tighten any leaking hose joints and fittings (check with soapy water, or even better, an ultrasonic detector)
- if necessary, cut hose just above the tank fitting and place a new compression ring here
- fit a wrench to the nut of the pressure valve and rotate it clockwise to release pressure
How to inspect your air ducts for leaks?
How to Locate Leaks in Your Ductwork
- Ductwork Inspection. Locating leaks in your ductwork starts with getting an inspection from your trusted HVAC company. ...
- Turn Your HVAC System On Full Blast. Turning your HVAC system on full blast can make it easier to find the less obvious leaks. ...
- Check the Duct Joints. ...
- Signs of Duct Tape. ...
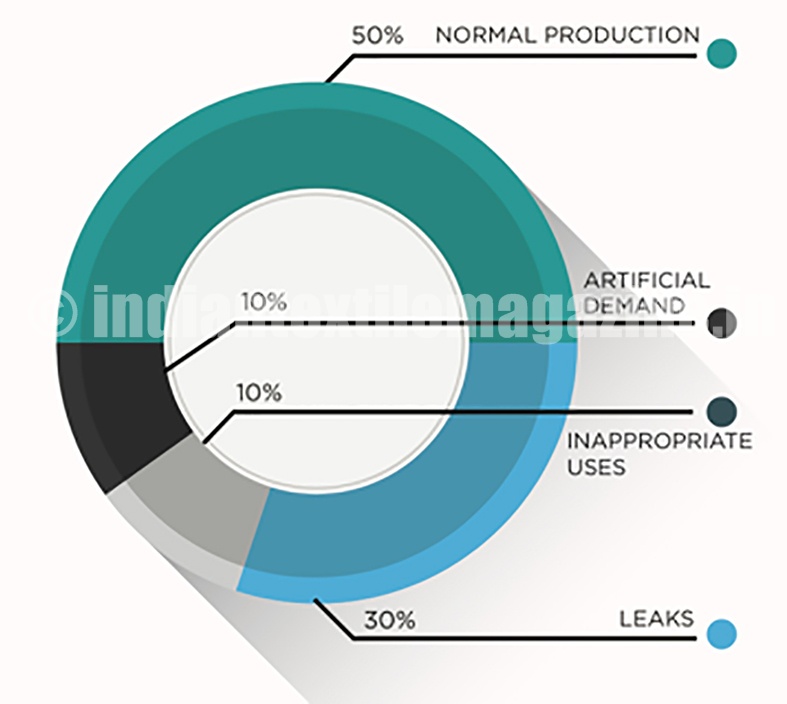
How much are compressed air leaks?
COMPRESSED AIR LEAKS ARE DANGEROUS They found that a single ¼-inch leak in a compressed air line can cost a facility anywhere from $2,500 to $8,000/yr. The scary part is, you may not even know it. Leaks not only increase energy cost, but they can also upset the functionality of the whole system.
How much does compressed air cost?
Compressed air cost $0.30 per 1000 standard cubic feet per minute (scfm) including investment and maintenance costs.
Why are air leaks considered high cost problems?
Increased maintenance expenses: Air leaks not only reduce your compressor's longevity by putting a higher demand on the system, but leaks also likely mean more frequent repairs and maintenance expenses than if the compressor were operating at peak performance and output.
Can you fix a leaking air compressor?
If your leak is at a place like an air hose connection, coupling, seal, gasket or control or shut-off valves, you might be able to fix the leak by tightening the connection. Tightening parts is one of the most straightforward ways to fix air compressor leaks.
Is compressed air free?
Compressed air is a costly utility that is often taken for granted. It is not free. In fact, it is one of the most costly utilities in plants today.
How is cost of air calculated?
So, if we look at the average of 4 CFM/hp and an average electrical rate of $0.08/KWh, we can use Equation 3 to determine the average cost to make 1000 cubic feet of air. C = 1000 * $0.08/KWh * 0.746 / (4 CFM/hp * 60) = $0.25/1000ft3.
How do you stop a compressed air leak?
How to Stop Air Compressor Leaks#1 Tighten Connections. Anything that can loosen is a prime spot for an air leak. ... #2 Repair or Replace Parts. ... #3 Swap Out Hose and Tube Sections. ... #4 Replace O-Rings and Valve Seals. ... #5 Tighten Fasteners. ... Establish a Maintenance Schedule. ... Regularly Inspect Compressors. ... Complete a System Audit.
How do you detect a compressed air leak?
The best way to detect leaks is to use an ultrasonic acoustic detector, which can recognize high frequency hissing sounds associated with air leaks.
How do you prevent a compressed air leak?
Try this: Ongoing and systematic maintenance of the entire compressed air system is the most effective way to prevent new leaks from forming. Be sure to check, clean or replace filters throughout the compressed air system. Filter maintenance goes a long way in decreasing pressure drops and increasing energy efficiency.
What is the most common location for compressor leaks?
While leakage can come from any part of the system, the most common problem areas are: Couplings, hoses, tubes, and fittings.
How do you fix a leaking air line?
2:027:10How to Repair Leaking Air Compressor Hose - YouTubeYouTubeStart of suggested clipEnd of suggested clipThis you want to take your two hose ends take hose clamps put one over each end you couldMoreThis you want to take your two hose ends take hose clamps put one over each end you could technically put them on one end.
Are compressors expensive to run?
One significant but surprisingly often neglected disadvantage is the cost. Air is frequently regarded as “free”, but running an air compressor can often be highly expensive. In this article we look at some of the costs involved in using air compressors and the inefficiencies of using air-powered equipment.
Can I use compressed air to clean my PC?
Yes, you can use canned air, it makes short work of what can be a messy task. Your PC is like a vacuum cleaner sucking in air and blowing it out all the time it is running.
Where does Walmart keep compressed air?
It's usually located where they sell printer refill cartridges. fyi. if you go to walmart or any large retailer get it from the arts and crafts department. they usually have cans that are much cheaper than in the electronics department.
Is WD 40 compressed air?
0:100:59How to Remove Dirt and Dust Build up From Workbenches & Electronics ...YouTubeStart of suggested clipEnd of suggested clipFast safe and easy to use wd-40 specialist air duster produces continuous 70 psi air pressure andMoreFast safe and easy to use wd-40 specialist air duster produces continuous 70 psi air pressure and can get into those tight spots making it ideal for keeping your workspaces.
What is the leak rate of 1/16 of an inch?
The amount of air that’s wasted is exponential when compared to the diameter of the hole. At 1/16th of an inch, at 150psi, the leak rate is 9.1CFM, at 1/8th of an inch, that number more than triples to 37.3CFM!
Can you hear air leaks in a shop?
At just about any shop you walkthrough, you can hear air leaks.
The Cost of Lost Air
Food and beverage plants use compressed air for a wide variety of purposes including moving products, operating pneumatic tools or pumping liquids. Compressed air is a clean, reliable, accessible 4th utility which is often undervalued per unit compared to its other utility counterparts - water, gas and electricity.
How Much Does Compressed Air Cost?
How is compressed air created? The Department of Energy (DOE) provides a simplified estimation of the cost of air using the direct components required to create compressed air: the size of the compressor, the time the compressors are on (control system - unload/load etc), the efficiency of the motor and operational hours.
How the Compressed Air System can Impact Productivity
During food and beverage manufacturing, compressed air needs to be available at the required pressure to achieve production targets. Systems that are not regularly maintained after installation could be losing 20 to 30% of compressed air in leaks.
Better Compressed Air Stewardship
Better stewardship of compressed air systems and distribution of air can be achieved by:
Optimization Tips for Compressed Air Systems
Once the distribution system has been validated as leak-free, further optimization can be achieved by addressing the following questions:
Diversey AirCheck
Compressed air/gas leaks are often overlooked in favour of more complex energy-saving solutions. With Diversey AirCheck, you can start and end with the confidence that your compressed air systems are not losing 20-30% of what is being produced to the atmosphere.
What percentage of compressor capacity is lost?
The percentage of compressor capacity that is lost should be under 10% for a system that is properly maintained.
How much energy does a compressed air system waste?
Leaks in a compressed air system can waste thousands of dollars of electricity per year. In fact, in many plants, the leakage can account for up to 30% of the total operational cost of the compressor.
How to contact Exair for leaks?
If you’d like to discuss how EXAIR products can help identify and locate costly leaks in your compressed air system, please contact one of our application engineers at 800-903-9247. Justin Nicholl. Application Engineer. [email protected]. @EXAIR_JN.
How much energy does an air compressor use?
Many plants know their actual energy costs but if not, a reasonable average to use is $0.25/1,000 SCF generated. As you can see, that’s a lot of money and energy being lost to just one small leak.
How to calculate leak cost?
To calculate the cost of leaks in your systems, begin by multiplying the compressor horsepower by kW conversion rate of .746 to determine the kW used. Next use your energy cost (you can use $0.12 if unknown) and multiply that by the kW used to come up with your hourly energy cost.
Does compressed air increase energy bills?
Leaks in your compressed air system may be increasing your compressed air energy bills by more than 30%. Since compressed air is usually one of the largest energy expenses for a manufacturer using air-powered equipment, that represents a significant opportunity for energy savings.
How much does it cost to leak air?
And if you can hear a leak, it’s probably costing your facility at least $500 per year.
How Much Are Air Leaks Costing My Facility?
If your compressor has an air leak, it’s costing you money in more than one way. Reduced pressure, wasted energy, and slower operation are all results of air leaks, and they all carry a price tag.
Where is the TMI air compressor made?
At TMI, we’re the only air compressor manufacturer in West Michigan with a team that specializes in finding and fixing leaks, as well as working with utility companies’ energy rebates. As experts in energy efficiency, we understand these rebate programs and work with energy companies like Consumers’ Energy to help you make the best use of yours.
Can you pay for air leaks?
The good news? In many cases, air leak repairs can be paid for through utility companies’ energy rebate programs .
Do compressors use electricity?
Utility companies know that air compressors use a ton of electricity, which is why they’ll reward you for any energy-saving efforts. These rebates vary in dollar amount but cover anything from prescriptive measures to custom repairs. By working with a compressed air supplier that understands and accepts these rebate programs, you can use your utility incentives and get the repair work you need for no out-of-pocket cost.
How much does it cost to leak compressed air?
Consider a study done by the Compressed Air & Gas Institute. They found that a single ¼-inch leak in a compressed air line can cost a facility anywhere from $2,500 to $8,000/yr. The scary part is, you may not even know it.
How many CFM should a compressed air system leak?
A typical system should average around 4 CFM each and a high leak system should average around 5 CFM each. The numbers above or below these levels should have a clear explanation! (Source)
What is the best way to detect a leak in a compressed air system?
Specialized equipment and a skilled technician should be deployed for reliable compressed air leak identification, especially in loud environments. Ultrasonic leak detection devices are the best tool to recognize leaks. Their regular use can help maintain consistent and high functionality of a compressed air system. Regular leak audits reduce wasted energy expenses, unnecessary wear on air compressors and help prevent air compressor downtime.
Why is it important to use a leak audit?
Regular leak audits reduce wasted energy expenses, unnecessary wear on air compressors and help prevent air compressor downtime.
Why are leaks bad for compressors?
Leaks not only increase energy cost, but they can also upset the functionality of the whole system. Leaks make compressors work harder to produce the same amount of compressed air.
How to determine leakage rate?
Identifying and quantifying the leak load is important when considering the entire effect of leaks on your system. Use a bleed down test to quantify the leakage rate of a whole system. Alternatively you can estimate leakage in systems if there is a pressure gauge downstream of the receiver. This method requires an estimate of total system volume, including any downstream secondary air receivers, air mains and piping (V, in cubic feet). Then start the system and bring to the normal operating pressure (P1) and then turn the compressor off.
What are the problems caused by compressed air leaks?
Compressed air leaks can contribute to problems with system operations, including: Fluctuating system pressure can cause air tools and other air-operated equipment to no function correctly, negatively affecting production. Excess compressor capacity, resulting in higher than necessary costs.
How much does a leak in a compressed air line cost?
On average, a small quarter-inch leak in a compressed air line can cost upwards of $8,000 per year. Leaks also cause the overall performance of your system to decline, ranging anywhere between a 25 percent to 50 percent waste in the system’s total output, negatively impacting pressure settings.
Why is compressed air leak management important?
For the best performance, like most process improvement programs, compressed air leak management is vital in saving you money and operating at peak efficiency. It’s imperative for you to develop a program to routinely identify and fix leaks and to develop a trained workforce that can help you prevent future leaks.
Why do you need an ultrasonic leak detector?
Additionally, the cost of purchasing an ultrasonic leak detector may be justified as it will allow you do perform audits with more accuracy —thus reducing wasted energy expenses. When searching for leaks in your compressed air systems, some specific areas might be more susceptible to leakage than others.
Why do compressors need to cycle more?
Reduction in the longevity of your equipment: Because leaks cause a higher demand for air power than what is typically needed , compressors need to cycle more frequently, which can result in a decreased lifespan of your compressed air system.
How does air pressure affect productivity?
Inefficient tools and lower productivity: Drops in air pressure resulting from leaks can greatly impact the productivity of your plant by causing tools to operate inefficiently and creating an overall less-productive environment.
How much power is used in compressed air?
Approximately 19 percent of the total power used in a compressed air system, even on a well maintained one, is converted into clean, compressed air flow. The other 81 percent is lost as heat. It also takes a much higher amount of electrical horsepower to be converted into compressed air power. According to the average estimate, between 7 ...
Why is compressed air considered a fourth utility?
Because of its common use, cleanness, availability and ease of use, compressed air is often considered a “fourth utility” in its wide industrial use, and it is likely the most expensive utility you’ll find in your plant. Approximately 19 percent of the total power used in a compressed air system, even on a well maintained one, is converted into clean, compressed air flow. The other 81 percent is lost as heat.
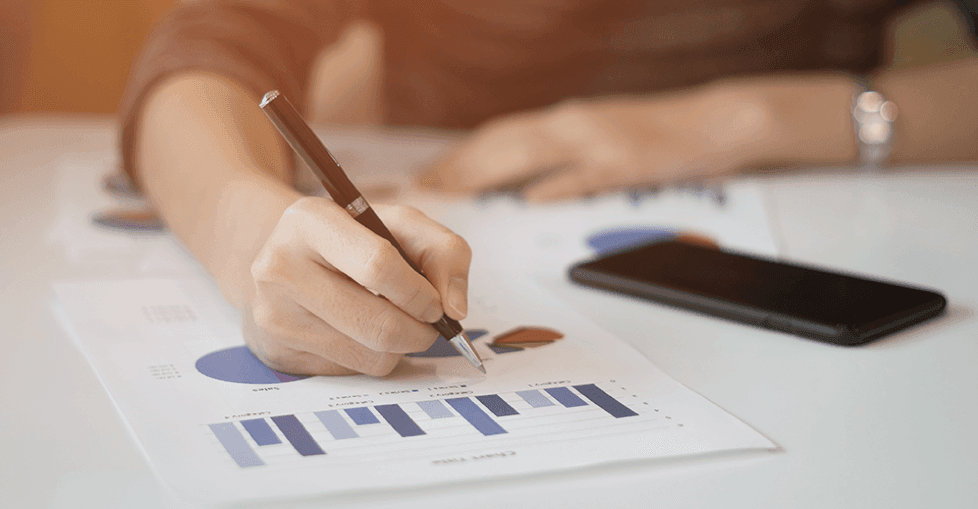