
To make the most of Six Sigma process improvement, Wils has several tips:
- Bring in an external consultant. “We often don’t see our own blind spots,” says Wils. People are used to the process and...
- Pay attention to the human component. “Everyone listens to their favorite radio station: WIIFM (What’s in it for me?).
- Ensure data is reliable and reproducible. “Remember this...
What are the benefits of six sigma process?
- Defects
- Transportation
- Overproduction
- Waiting
- Non Utilized talent
- Inventory
- Motion
- Overprocessing
What are the 5 phases of Lean Six Sigma?
The other critical steps at this stage are:
- Identify the opportunities with high potential for improvement
- Outline the scope of the project
- Create a value stream map ( VSM) to document every step in the process
- Develop a voice of the customer table ( VOCT) to pinpoint the customer needs
- Identify all stakeholders
- Estimate project impact and completion
- Identify and document business opportunity
What is Six Sigma methodology?
would you consider your problem-solving approach as more of following the model of Lean Production rather than Six Sigma? Schnider says their system is "mainly inspired by the lean thinking model developed" under TPS. By "using the lean methodology ...
When to use Six Sigma?
- It is the most effective problem-solving method that an organization can use to improve performance.
- Any organization aims to achieve the Six Sigma performance. ...
- A Six Sigma improvement is achieved when a work process or business has key outcomes that are dramatically improved, ideally by 70% or more.
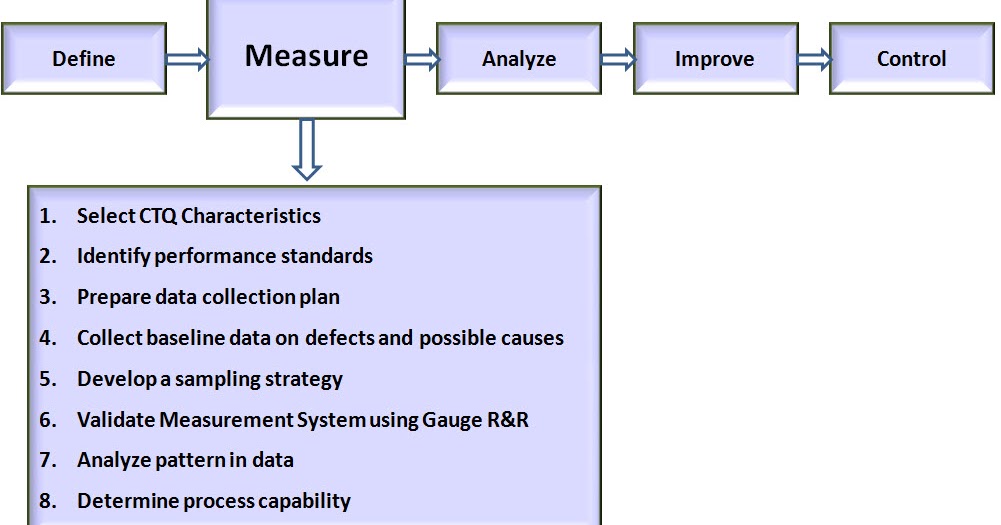
How is Six Sigma approach to process improvement different than other process improvement approaches?
Six Sigma relies on data and statistics to make decisions more than other methodologies. By using DMAIC and DMADV, Six Sigma organizations should see clear financial returns and strive for less than 3.4 defective features in every million opportunities, or chances for a defect.
What does the Six Sigma process reduce?
The main focus of Lean Six Sigma is to reduce waste by minimizing variability in business processes and creating a continuous flow between each step. The methodology categorizes eight types of waste: defects, overproduction, waiting, nonutilized talent, transportation, inventory, motion, and extra-processing.
What is Six Sigma and its benefits?
Six sigma is defined as a project management methodology or set of practices to eliminate the waste or the unwanted/defects from the existing or developing process. Six-Sigma is a data-driven approach for eliminating the defects from the process and it is calculated as the standard deviation from the data collected.
What is the main purpose of Six Sigma?
The goal of Six Sigma is to reduce variation for optimal quality control. The discipline known as Lean Six Sigma (LSS) blends these two approaches. Refinements to the production process are essential to managing and reducing the 8 wastes analyzed by the Lean method.
What is the objective of Six Sigma?
The primary objective of Six Sigma is customer satisfaction , and to achieve the objective, various methods are followed to improve the performance of a product or business process. DMAIC and DMADV are the main methodologies of Six Sigma that apply to different business environments.
What is Six Sigma?
Six Sigma is a term used to define various techniques and management tools designed to make business processes more efficient and effective. It provides statistical tools to eliminate defects, identify the cause of the error, and reduce the possibilities of error. Thus, Six Sigma creates an environment of continuous process improvement, ...
What are the principles of Six Sigma?
There are five main principles of Six Sigma: 1. Customer focus. The main objective is to maximize the benefits for customers. Hence, a business must understand the needs of their customers. Types of Customers Customers play a significant role in any business. By better understanding the different types of customers, ...
What happens when an inefficient process is eliminated?
Whenever an inefficient or faulty process is eliminated, the employee approach and work practices need to be changed. A flexible and responsive environment to the changes in processes can lead to the efficient implementation of the projects.
Why is structured process important?
A structured process should be adopted where all stakeholders collaborate and contribute to finding solutions to complex issues. The team needs to achieve proficiency in the methodologies and principles applied. Hence, specialized knowledge and training are required to lower project failure risks and ensure optimal performance of the processes.
When was Six Sigma developed?
It was developed by Motorola, Inc. in 1986. Six Sigma can be applied to any process in any industry to establish a management system for identifying errors and eliminating them. It provides methods to improve the efficiency of business structure and quality of processes, enhancing the profitability of the business.
What is DMAIC in business?
DMAIC is a data-driven approach used for optimizing and improving the existing business designs and processes. It is an effective method of controlled change management. The five phases of DMAIC are listed below, and each phase involves tools and tasks to help find the final solution.
Why use Six Sigma?
You can use Six Sigma projects to specifically improve customer and vendor satisfaction. Better Cash Flow. Six Sigma methodology can be used specifically to improve your business’s DSO – Days Sales Outstanding – by reducing its value which comes from the variations within processes.
Why is Six Sigma important?
Just like money, time is an asset. Six Sigma tools can be used, for example, to reduce the number of hours or the number of machines in a manufacturing process.
What is Six Sigma methodology?
Six Sigma methodology is not a mysterious magic solution but a well-studied and tested set of tools and techniques that aim to solve problems of inefficiency within your business or projects.
What is Six Sigma project?
Six Sigma projects can aim towards improving the three aspects of regulatory compliance within your business: Finance and Audit; Information Technology and Legal. In the case of Finance and Audit, some of the methodologies can be used for example to improve fund allocation processes or reduce the turnaround time in the cost estimation processes.
What are the benefits of Six Sigma?
You can measure and quantify these benefits, especially financial ones. Improved Efficiency and Timeliness. Just like money, time is an asset.
When was Six Sigma invented?
The concept of Six Sigma dates back to the 19th century and it has been used in business since 1986 when it was first introduced by mobile communications giant Motorola after research and analysis of its benefits.
