
What is the PDCA cycle in Lean management?
The PDCA cycle is a Lean tool that can be used at any stage of an organizational transformation to drive progress and gauge success. It’s name is derived from its four steps: Plan, Do, Check, Act (or Adjust). The are many instances where the PDCA cycle can be used to drive progress.
What is PDCA and how to use it?
It can be used to monitor a single issues or guide an entire improvement project or initiative. PDCA was made popular by W. Edwards Deming, who is considered by many to be the father of modern quality control. He always referred to it as the “Shewhart cycle”. Establish objectives and processes in order to deliver the desired results.
What is the modified PDCA cycle developed by Deming?
Later in Deming’s career, he modified PDCA to “Plan, Do, Study, Act” (PDSA) because he felt that “check” emphasized inspection over analysis. Modified PDCA cycle developed by Deming. He mentioned that the PDSA Cycle originated in his teaching in Japan in 1950.
How do you analyze student data in PDCA?
Data can be analyzed for individual students or stratified by grade, gender, or any other subgroup. Because PDCA does not specify how to analyze data, a separate data analysis process (Figure 3) is used here as well as in other processes throughout the organization.

What does PDCA stands for in lean?
Plan-do-check-act cycleThe Plan-do-check-act cycle (Figure 1) is a four-step model for carrying out change. Just as a circle has no end, the PDCA cycle should be repeated again and again for continuous improvement. The PDCA cycle is considered a project planning tool.
Is PDCA a TQM tool?
The PDCA cycle, also known as the Shewhart Cycle or the Deming Cycle, is a popular TQM problem-solving tool. PDCA (The Plan-Do-Check-Act) cycle involves four basic steps for carrying out continuous improvement in a process.
Is PDCA a kaizen tool?
It is a methodical approach for problem solving and continuous improvement. PDCA wheel should be considered a never-ending cycle for improvement towards an ideal condition. PDCA cycle is the concept behind the KAIZEN approach. Look at how PDCA cycle is used in KAIZEN approach.
Is PDCA a Six Sigma?
There are many great tools and templates used in Six Sigma, and today we are going to spend a little time with PDCA (Plan-Do-Check-Act). PDCA is a template or cycle used for problem solving.
What is Kaizen in TQM?
What Is Kaizen? Kaizen is a Japanese term meaning change for the better or continuous improvement. It is a Japanese business philosophy that concerns the processes that continuously improve operations and involve all employees. Kaizen sees improvement in productivity as a gradual and methodical process.
What is PDSA cycle in TQM?
PDSA, or Plan-Do-Study-Act, is an iterative, four-stage problem-solving model used for improving a process or carrying out change. When using the PDSA cycle, it's important to include internal and external customers; they can provide feedback about what works and what doesn't.
Is PDSA part of lean?
PDSA is a part of Kaizen, Lean and Six Sigma methods. All of them entail steps to: examine the problem and its root causes and identify potential solutions (plan); test the solutions (do); analyze the results of the test (study); and implement the new process (act).
What tools does PDCA use?
Tools to Support PDCAClarify the problem (with 5W2H)Breakdown problems.Set the target.Analyze the root cause.Develop countermeasures.Implement countermeasures.Monitor results.Standardize.
What is Kaizen 5S?
• 5S is a philosophy and a way of organizing. and managing the workspace and work. flow with the intent to improve efficiency by. eliminating waste, improving flow and. reducing process unreasonableness.
Is PDCA the same as DMAIC?
The major difference between PDCA and DMAIC is that PDCA is a repetitive four-stage model applied to achieve continuous improvement in business process management while DMAIC represents a data-driven improvement approach used for improving, enhancing, and stabilizing business processes in 5 stages from defining to ...
Is Plan Do Check Act Six Sigma project type?
Six Sigma typically uses a five-phased approach – DEFINE, MEASURE, ANALYZE, IMPROVE, CONTROL (known as “DMAIC”). Dr. W. Edwards Deming used a four-step process, which is more of a cycle – PLAN, DO, CHECK, ACT for process improvement.
What's the difference between PDCA and DMAIC?
The key difference between PDCA and DMAIC is that PDCA is a repetitive four stage model (Plan, Do, Check, and Act) used to achieve continuous improvement in business process management whereas DMAIC is a data-driven improvement cycle used for improving, enhancing and stabilizing business processes containing 5 stages ( ...
What is TQM and its elements?
A core definition of total quality management (TQM) describes a management approach to long-term success through customer satisfaction. In a TQM effort, all members of an organization participate in improving processes, products, services, and the culture in which they work. Primary elements of TQM.
What is TQM in management?
Total Quality Management (TQM) is a management framework based on the belief that an organization can build long-term success by having all its members, from low-level workers to its highest ranking executives, focus on improving quality and, thus, delivering customer satisfaction.
How Benchmarking is used in TQM?
Benchmarking can become a tool to sustain this new TQM paradigm, providing a means to increase an organization's competitive performance by a comparison with the best-in-class. The challenge is driving the change and not being driven. That is why benchmarking in TQM can become the helm to drive the change.
What is the purpose of PDCA cycle?
The PDCA/PDSA cycle is a continuous loop of planning, doing, checking (or studying), and acting. It provides a simple and effective approach for solving problems and managing change. The model is useful for testing improvement measures on a small scale before updating procedures and working practices.
What is the first step in PDCA?
The first step in the PDCA is the Plan. As the name says, you plan what you are going to do. Depending on the project, this may be the largest part of the effort of the PDCA. In fact, you can see it as a number of sub-steps or points that you have to address in the Plan. Depending on your progress, you may even have to do some ...
How long does PDCA repeat?
The PDCA repeats until the problem is solved.
What is the key to lean manufacturing?
The Key to Lean – Plan, Do, Check, Act! Plan-Do-Check-Act (or PDCA) is one of the key elements in lean manufacturing, or for that matter in any kind of improvement process. In my view, it is the most basic framework for any kind of change. All other lean tools are only on top of the PDCA.
Why do lean projects fail?
All other lean tools are only on top of the PDCA. In my experience, most lean projects in the Western world fail not because they do not have some detailed tool , but because the PDCA is neglected. Of course, (almost) everybody knows what the PDCA is, but there is a huge difference between knowing the theory and doing it correctly.
What is PDCA in a tool?
The PDCA portion of the tool identifies the process to successfully implement the changes and verify that the desired result has been achieved.
What is lean management?
With a core objective of maximizing customer value while minimizing waste, Lean management principles are widely used in most industries, and healthcare is no exception.
What is a lean approach to employee suggestions?
A Lean Approach To Promoting Employee Suggestions ( Quality Progress) This simple , low-tech approach maintains the visual process and easily communicates where each suggestion is in the PDCA process without the need for email, databases or other technological means.
What is planning data collection and analysis?
Planning data collection and analysis in order to verify and prioritize problems or root causes
What is modular kaizen?
A Systematic View ( Lean & Six Sigma Review) Modular Kaizen is an improvement approach that integrates quality techniques into the busy schedule of everyday activities. The Modular Kaizen approach is complementary to the PDCA and DMAIC models of quality improvement, as described in this article.
What is the Plan Do Check Act cycle?
The Plan-do-check-act cycle (Figure 1) is a four-step model for carrying out change. Just as a circle has no end, the PDCA cycle should be repeated again and again for continuous improvement. The PDCA cycle is considered a project planning tool.
What is aligning in education?
The "align" step asks what the national and state standards require and how they will be assessed. Teaching staff also plans curricula by looking at what is taught at earlier and later grade levels and in other disciplines to ensure a clear continuity of instruction throughout the student’s schooling. Teachers develop individual goals to improve their instruction where the "analyze" step showed any gaps.
What happens if assessments show students are not learning as expected?
Throughout the school year, if assessments show students are not learning as expected, mid-course corrections are made (such as re-instruction, changing teaching methods, and more direct teacher mentoring). Assessment data become input for the next step in the cycle.
What is PDCA cycle?
The PDCA cycle is a Lean tool that can be used at any stage of an organizational transformation to drive progress and gauge success. It’s name is derived from its four steps: Plan, Do, Check, Act (or Adjust).
What is a poka yoke?
Poka-yoke: Any mechanism in the process that help operators to avoid mistakes.
Is PDCA an ongoing process?
In fact, the PDCA cycle should be an ongoing process. No matter the results of your project, it’s likely to create new opportunities for improvement that can be studied and adjusted.
What does PDCA mean in economics?
As shown in the book, The New Economics. Taiichi Ohno took the acronym PDCA from Deming’s improvement cycle, but he decided that the cycle should start with Check, so it would be reordered as CAPD.
Who invented the PDCA?
PDCA was made popular by W. Edwards Deming, who is considered by many to be the father of modern quality control.
What does PDCA stand for?
Abbreviation for Plan Do Check Act, which is a model that provides a framework for the improvement of a process or system. It can be used to monitor a single issues or guide an entire improvement project or initiative. PDCA was made popular by W. Edwards Deming, who is considered by many to be the father of modern quality control.
Why did Deming change the PDCA?
Later in Deming’s career, he modified PDCA to “Plan, Do, Study, Act” (PDSA) because he felt that “check” emphasized inspection over analysis. Modified PDCA cycle developed by Deming. He mentioned that the PDSA Cycle originated in his teaching in Japan in 1950.
What is the purpose of a plan?
A plan is developed to experiment with ideas to see if they will improve the process or results. Executes the plan developed from the previous step. Small changes are usually tested, and data is gathered to measure the effectiveness of the change. Data and results gathered from the Do phase are evaluated.
What is the Lean Process?
The lean process has four stages: Plan, Do, Check, Act. The first stage is to develop a plan for improving the results of a process. The Do stage involves executing the plan. This produces feedback that is then checked to confirm or adjust the plan. The final stage is to act based on the evaluation completed in the check phase.
What is the key success criteria for a lean implementation?
One of the key success criteria for a lean implementation will be to what degree the process can be embedded and made part of the culture. A culture is defined as a set of unwritten rules and behaviours observed by a group. When the plan, do, check, act cycle becomes second nature for employees, the company will continuously improve.
Is lean process a good investment?
If you are interested in learning more about the lean process then this really is one of the best investments you can make. Your company, colleagues and customers will be glad you did!
Is lean process iterative?
The lean process is iterative. After one cycle, it may be necessary to continue with further cycles until the process is producing the desired results consistently. Think of it as a series of mini experiments, with the aim of learning as much about the process as quickly as possible.
What is the purpose of inspecting in lean manufacturing?
Inspecting throughout the manufacturing process can play a key role in preventing defects and fixing problems before they cause significant damage.
What is bottleneck analysis?
The goal of Bottleneck Analysis is to determine the slowest parts of the manufacturing process and then figure out how to speed them up. The process can be costly, but will usually lead to increased efficiency and profits. Ignoring a bottleneck issue can be very costly down the line.
What is bottleneck in supply chain?
Bottleneck (or constraint) in a supply chain refers to the resource that takes the longest time in operations. When hiking, for example, a bottleneck refers to the slowest member of a hiking group. That member can determine the speed of the entire group. The same goes for processes in manufacturing.
What is demand management?
Demand Management is a lean tool used to identify all demand coming from an external environment, manage it, and input it into a supply chain within a company.
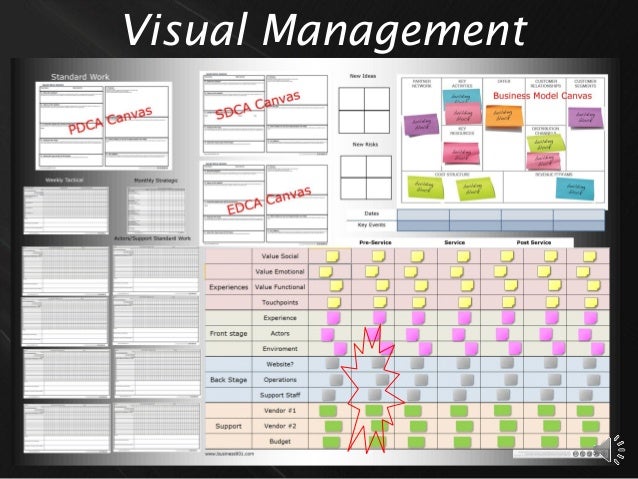
Focus – Identifying The Processimprovement
Pdca– Implementing The Solution
Apractical Application