
What is the purpose of field bus?
A fieldbus is a serial bus system used in machines and systems to connect sensors and actuators (motors) to each other and to one or multiple masters (industrial PCs, PLCs). Fieldbuses make it possible to exchange data between different system components over long distances and under high external load.
What is fieldbus in a VFD?
Fieldbus is an all-digital serial, two-way multi-drop communication system, which interconnects "field" equipment such as sensors, actuators and controllers.
What is a fieldbus controller?
Fieldbus is simply a means of communicating with input devices (sensors, switches, etc.) and output devices (valves, drives, indication lamps etc.) without the need to connect each individual device back to the controller (PLC, Industrial PC etc.). Therefore, overall, Fieldbus can reduce costs.
What are the two types of fieldbus?
Foundation Fieldbus H1 and PROFIBUS-PA are the two fieldbus technologies used in process control. In this two-way communication, it is possible to read data from the smart sensor and also write data into it.
What are the 4 parts of a VFD?
The four blocks or sections of a VFD are Rectifier, DC bus/filter, Inverter and Control Unit. The block diagram of a VFD is also given below.
What are the different types of fieldbus?
The different types of field bus are generally not compatible with each other. Network and field bus technologies types include brands such as: EtherNet/IP; DeviceNet; ControlNet; CompoNet; EtherCAT; PROFIBUS; PROFINET; Ethernet POWERLINK; CANopen; Interbus; CC-Link; Modbus TPC; AS-Interface; and IO-Link.
What are the benefits of fieldbus?
Fieldbus systems can provide tremendous benefits in terms of lower costs, increased uptime and better overall plant performance. But take care when selecting and deploying the fieldbus solution; it's often best to start small. A field device usually is first connected to the control system via a fieldbus.
Why is fieldbus important?
Fieldbus has the greater advantage in new installations in that it can significantly reduce the amount of cabling on the plant, and provide an increased amount of information than many other digital protocols. It also allows different venders equipment to be used (as long as they abide with a Fieldbus standard).
How many wires are in a fieldbus?
Fieldbus also uses two wires to carry power to the devices. A number of devices share the same Fieldbus wires. Fieldbus devices vary the voltage on the two wires to send signals.
Is fieldbus a Modbus?
Modbus is often classified as a fieldbus protocol but with its various enhancements, particularly Modbus TCP, it has an even wider range of communication applications. One of the reasons for its proliferation is that Modbus is simple and hardy.
What is the difference between fieldbus and HART?
HART is Master/Slave by design thus there can only be only two Masters eg., Control System/Hand Held. Foundation Fieldbus is a true Multidrop System and has numerous advantages including: Wiring savings. Hardware savings-fewer devices (instruments barriers and I/O)
What are the disadvantages of fieldbus?
Foundation Fieldbus is not utilized for applications requiring extremely fast control system response (200mS or below), such as Anti-Surge control, or for applications requiring high signal bandwidth, such as Machine Condition Monitoring systems.
What are the benefits of fieldbus?
Advantages of Fieldbus Technology:- Reduced installation effort: less cabling, smaller, simplified control cabinets.- Reduced troubleshooting in the event of a fault.- One cable for digital/binary and analog signals.- Protection against interference with analog values.More items...
Why is fieldbus important?
Fieldbus has the greater advantage in new installations in that it can significantly reduce the amount of cabling on the plant, and provide an increased amount of information than many other digital protocols. It also allows different venders equipment to be used (as long as they abide with a Fieldbus standard).
What is fieldbus and Modbus?
Modbus is a granddaddy of industrial communication protocols. Modbus is Modicon plus fieldbus. Modbus, a serial communication protocol developed by Modicon in 1979. It is developed by Modicon for PLC in industrial applications, now it an open protocol. It is used over serial and Ethernet cable.
What is difference between HART and fieldbus?
HART is Master/Slave by design thus there can only be only two Masters eg., Control System/Hand Held. Foundation Fieldbus is a true Multidrop System and has numerous advantages including: Wiring savings. Hardware savings-fewer devices (instruments barriers and I/O)
What is a fieldbus?
What is Fieldbus? Fieldbus is simply a means of communicating with input devices (sensors, switches, etc.) and output devices (valves, drives, indication lamps etc.) without the need to connect each individual device back to the controller (PLC, Industrial PC etc.). Therefore, overall, Fieldbus can reduce costs.
Why are fieldbuses open?
Due to market pressure , most Fieldbuses now claim to be ‘open’ (some more so than others). This is because large end companies wanted to be able to connect and use the installed control platform (e.g. PLC) to communicate via the Fieldbus to specialist devices from a range of different manufacturers to essentially ‘talk’ to the control platform.
Does a fieldbus reduce costs?
Therefore, overall, Fieldbus can reduce costs . Murrelektonik explain just what a Fieldbus is and also how Fieldbus control platforms work and perform. Prior to its introduction, computers would connect using direct serial connections whereby only two devices could communicate per connection. The Fieldbus, on the other hand, allows hundreds ...
How many mA does a fieldbus need?
Most devices are two-wire bus-powered units requiring 10 to 20mA, but it is also possible to have 4-wire fieldbus devices, typically where a device has a particularly high current draw. The fieldbus segment begins at an interface device at the control system. On a FOUNDATION fieldbus H1 (FF) system, the interface is called an H1 card;
How does DC power work in a bus?
The DC power required by the bus is normally sourced through a fieldbus power supply or “power conditioner” which prevents the high frequency communications signal from being shorted out by the DC voltage regulators.
What is the difference between a fieldbus and a profibus?
One primary difference is that PROFIBUS is a polling system, while FOUNDATION fieldbus utilizes cyclic transmission. Other differences include:
What is fieldbus in instrumentation?
Instead of running individual cables, fieldbus allows multiple instruments to use a single cable, called a “trunk” or a “segment,” (Figure 2); each instrument connects to the cable as a “drop.” Instruments, of course, must have a fieldbus interface to connect to the segment, and some sort of software running to provide the fieldbus communications.
How many devices can be connected to a fieldbus?
A fieldbus trunk or segment—either FOUNDATION fieldbus H1 or PROFIBUS PA—is a single twisted pair wire carrying both a digital signal and DC power that connects up to 32 fieldbus devices (temperature, flow, level and pressure transmitters, smart valves, actuators, etc.) to a DCS or similar control system. Most devices are two-wire bus-powered units requiring 10 to 20mA, but it is also possible to have 4-wire fieldbus devices, typically where a device has a particularly high current draw.
Why was the fieldbus used?
Fieldbus was initially justified by the considerable cost savings that resulted from using less wiring. Instead of running hundreds or thousands of wires, fieldbus often required only a few dozen segments or trunks.
How to determine how many devices can fit on a fieldbus?
When calculating how many devices can fit on a fieldbus segment, a user must take into account the maximum current requirement of each device, the length of the segment (because of voltage drops along the cable), and other factors.
How does Fieldbus control work?
Organized Hierarchy The Fieldbus Control System works on network structures that normally allow daisy-chains, stars, rings, branches. Previously computers connected using RS-232 (serial connection) with only two devices can communicate.
Why is Fieldbus used in cable routing?
The use of Fieldbus also functions as savings on cable routing because the addressing system carried out by Fieldbus allows many devices to communicate via one cable pair.
How many departures can a Modbus have?
Raw bits or words move without placing many restrictions on the vendor. Modbus allows for communication between multiple departures (around 240 ) connected to the same network, for example a system that measures temperature and humidity and communicates the results to a computer.
What is a modbus?
ModBus: is a serial communication protocol published by Modicon in 1979 for use with logic programmable controllers (PLC). Simple and powerful, it has since become one of the standard de facto communication protocols in industry, and is now among the most common ways available to connect industrial electronic devices.
When was the CAN bus developed?
CAN bus development began initially in 1983 at Robert Bosch GmbH. [1] . This protocol was officially released in 1986 at the congress’s Society of Automotive Engineers (SAE) in Detroit. The CAN bus is one of five protocols used in OBD-II vehicle diagnostic standards.
Does Fieldbus use linearization?
Unlike HART technology, Fieldbus does not do linearization data that occurs on HART technology by using 4-20 mA analog signals to be converted, while Fieldbus technology uses data programming. You could say Fieldbus technology relies more on software engineers from all sides, such as checking, sending data in the control unit, calibrating, etc.
What is the foundation fieldbus?
FOUNDATION Fieldbus is the ultimate realization of this trend, where the field instruments themselves can do all necessary control functions.
What is fieldbus cable?
Each “fieldbus” cable is a multi-drop digital network, permitting multiple field devices per cable and consequently reducing total cable length and connection count. Coupling devices may be used in lieu of terminal blocks to conveniently connect multiple instruments together on common networks leading to the DCS.
How does a DCS controller communicate with a field instrument?
Information is communicated in analog form between the DCS controllers and the field instruments. If equipped with the proper types of I/O cards, the DCS may even communicate digitally with some of the field instruments using HART protocol.
How do Profibus PA instruments communicate?
Now let us examine Profibus PA again. Here, the field instruments are entirely digital, communicating with each other via digital signals over a network cable to the DCS.
Where does 4-20 mA conversion take place?
The conversion of 4-20 mA signals from transmitters into a scaled digital number values inside the DCS takes place inside “analog input” (AI) function blocks programmed into the DCS. These converted values then pass to PID function blocks where the arithmetic for control loop decisions takes place.
Do all control algorithms have to be executed within the field instruments in a FOUNDATION Fieldbus control system?
This is not to say that all control algorithms must be executed within the field instruments in a FOUNDATION Fieldbus control system.
Is DCS necessary for operations?
In fact, the DCS would not even be necessary if not for the need of operations personnel to monitor and alter control system status:
What is DCS System?
A distributed control system (DCS) is a specially designed automated control system that consists of geographically distributed control elements over the plant or control area.
What is DCS in industrial?
In recent years, the use of smart devices and field buses makes distributed control system (DCS) to be prominent in large and complex industrial processes as compared to the former centralized control system. This distribution of control system architecture around the plant has led to produce more efficient ways to improve reliability of control, process quality and plant efficiency.
How does DCS work?
The operation of DCS goes like this; Sensors senses the process information and send it to the local I/O modules, to which actuators are also connected so as to control the process parameters. The information or data from these remote modules is gathered to the process control unit via field bus. If smart field devices are used, the sensed information directly transferred to process control unit via field bus.
What is DCS in manufacturing?
DCS is most suited for large-scale processing or manufacturing plants wherein a large number of continuous control loops are to be monitored and controlled. The main advantage of dividing control tasks for distributed controllers is that if any part of DCS fails, the plant can continue to operate irrespective of failed section.
What is DCS controller?
In DCS control system, data acquisition and control functions are carried through a number of DCS controllers which are microprocessor based units distributed functionally and geographically over the plant and are situated near area where control or data gathering functions being performed as shown in the figure above. These controllers able to communicate among themselves and also with other controllers like supervisory terminals, operator terminals, historians, etc.
What is the second attribute of DCS?
The second attribute of DCS is the automation of manufacturing process by integrating advanced control strategies. And the third characteristic is the arranging the things as a system. DCS organizes the entire control structure as a single automation system where various subsystems are unified through a proper command structure and information flow.
Where are DCS controllers located?
In DCS, data acquisition and control modules or controllers are usually located within a more confined area and the communication between various distributed control units carried via a local area network. SCADA generally covers larger geographical areas that use different communication systems which are generally less reliable than a local area network.
What is the difference between a DCS and a foundation field bus?
You seem to be confused regarding these two items. DCS is a control platform while Foundation Field bus is a communication protocol. Foundation Field bus is a digital signal that replaces the traditional 4 - 20mAmp signal. This allows a more comprehensive information transfer on both primary measurement and final control equipment being made available at the DCS. In some instances the use of microprocessors at the instrument level allows for closed loop control at a local level, this would require the DCS to provide a remote setpoint only.
What is a fieldbus?
FOUNDATION (tm) Fieldbus is a system architecture consisting of H1 bus at the field-level and HSE bus at the host level. It also includes a graphical function block diagram for building control strategies according to the IEC 61804 standard. This also permits control in the field as opposed to centralized in a shared controller, thus achieving single loop integrity. FOUNDATION (tm) Fieldbus also includes the Device Description mechanism for interoperability with the host computers, also per IEC 61804. See this architecture overview article "An Open Architecture for Information Integration " by the Fieldbus Foundation: http://www.sensorsmag.com/articles/0501/22/main.shtml
Why do brown field plants use fieldbus?
There are many cases where existing "brown field" plants go Fieldbus because they need to replace their old DCS as spares and support becomes difficult to get. Here Fieldbus also makes sense because the savings are not just on wiring reduction (which only is a benefit in a new installation) but also from the fact that you don't need the analog I/O cards, and far fewer controllers etc. But most attractive is the savings from more diagnostics in the instruments that result in reduced maintenance when used with asset management software. This makes sense also for an existing plant.
How much more is a fieldbus than a smart phone?
2. FOUNDATION (tm) Fieldbus devices cost about $70-140 more than their smart counterparts do. This is less than only a few years ago, and the difference is likely to get smaller over the next few years. However, using FOUNDATION (tm) Fieldbus you get much more functionality than in conventional or smart devices. Using FOUNDATION (tm) Fieldbus your instruments are permanently networked to the host computers giving users access to all information any time. This means that faults are reported to the user as soon as they self diagnostics in the device detects it, not the next time somebody happens to connect a handheld. You can verify device configuration
What are the advantages of Fieldbus?
An advantage with Fieldbus is the ability to continuously monitor the device temperature remotely over the Fieldbus. This way you can be notified if the temperature gets too high or deduce the heat tracing failed. This can be very useful from a maintenance perspective.
How many mA is a foundation fieldbus?
FOUNDATION Fieldbus is not just a "digital 4-20 mA", it goes far beyond that.
Where are function blocks moved in DCS?
Then function blocks are moved to the field instrument or control valve positioner close to the inputs and outputs . The new DCS's are seamless with the Fieldbus.
What is DCS in plant?
The DCS is the control system that continuously monitors and controls the process during normal plant operation and may provide three different types of safety functions: Continuous control action, keeping the process at set point values within the normal operating envelope.
What is DCS in valves?
Upon receipt of information from the operator, the DCS interacts with the processes continuously. Distributed control system also facilitates the opening and closing of valves using operator manual control. To achieve all these functions DCS consists of various elements like
What is DCS sensor?
Sensors in a DCS control system senses the process information and then send it to the local I/O modules. The actuators connected with these modules control the process parameters. The collected information is used to the process control unit via field bus.
What are some examples of DCS failure?
The Control functions are composed of many components that can fail. Examples of control function failure are: Field sensor fails. Inadequate control loop tuning.
What is distributed control system?
Distributed control system, by organizing the entire control structure as a single automation system , are unified through a proper command structure and information flow. The basic elements of a DCS consists of engineering workstation, process control unit or local control unit, operating station or HMI, smart devices, and communication system.
What is state controller?
State controllers (logic solver or control relays), to take automatic action to trip the process, rather than attempt to return the process to within the normal operating envelope.
What are the characteristics of a distributed control system?
Distributed Control System has three important attributes. The first quality is that it distributes various control functions into relatively small subset systems. These sub system sets are semiautonomous, and a high speed communication bus interconnects them. Functions like process control, process supervision, data acquisition, data presentation, reporting information, storing, information retrieval, etc are performed by this sets.
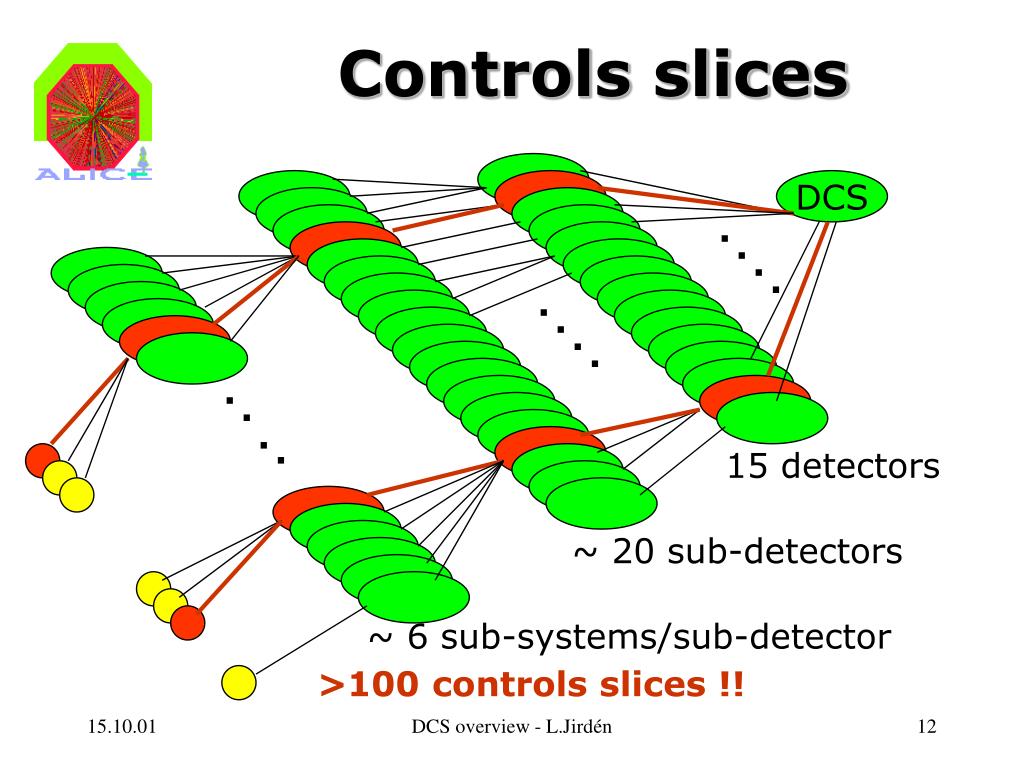
Foundation Fieldbus
Connecting Instruments
Segment Termination
- Every fieldbus segment must be terminated at both ends for proper communication. If a segment is not terminated properly, communications errors from signal reflections may occur. Most device couplers use manual on/off DIP switches to terminate couplers. In a segment, the last device coupler should contain the terminator, and all couplers between the last coupler and the H1 car…
Advantages of Fieldbus Communication
- Fieldbus was initially justified by the considerable cost savings that resulted from using less wiring. Instead of running hundreds or thousands of wires, fieldbus often required only a few dozen segments or trunks. In recent years, the savings from running cables has been offset by the high cost of fieldbus components, and the reluctance of many users to install all the instrument…
Foundation Fieldbus h1 vs. Profibus PA
- From a field wiring perspective, FOUNDATION fieldbus and PROFIBUS are physically identical. They use the same twisted-pair cables and device couplers, and require the same segment terminators. Both handle up to 32 devices per segment. One primary difference is that PROFIBUS is a polling system, while FOUNDATION fieldbus utilizes cyclic transmission...