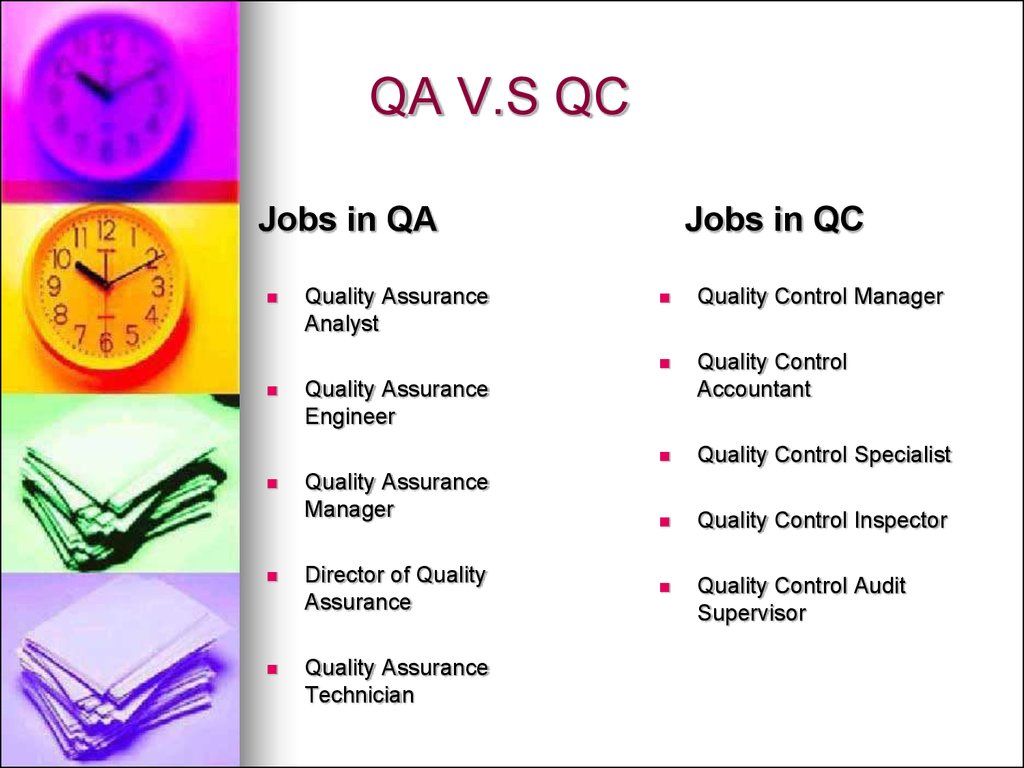
Quality control (QC
Quebec
Quebec (/k(w)ɪˈbɛk/ ; French: Québec ) is one of the thirteen provinces and territories of Canada. It is bordered to the west by the province of Ontario and the bodies of water James Bay and Hudson Bay; to the north by Hudson Strait and Ungava Bay; to the east by the Gulf of Saint Lawrence and the …
What are the steps of quality control?
What are the five stages of total quality management process?
- Commitment and Understanding from Employees. …
- Quality Improvement Culture. …
- Continuous Improvement in Process. …
- Focus on Customer Requirements. …
- Effective Control.
What are the pros and cons of quality control?
- There is always something new to learn and challenge you
- My particular side of Quality control involves an everchanging workday so I never know exactly what my day will look like
- Flexibility: because of the nature of my industry I work a lot of flex days (start early, end early, work some short days and some long days, bank extra hours ...
What are quality control policies and procedures?
- Independence, Integrity, and Objectivity
- Personnel Management
- Acceptance and Continuance of Clients and Engagements
- Engagement Performance
- Monitoring
What are the objectives of quality control?
- Market segment towards which the product or service is directed
- What are the expectations of the clients?
- Where is the company headed?
- What do you want to achieve in the short, medium and long term?

What is quality control procedures examples?
QC process assures that that the product being developed is of the required quality. Examples of quality control activities include inspection, deliverable peer reviews and the software testing process.
What are the 4 types of quality control?
What Are the 4 Types of Quality Control? There are several methods of quality control. These include an x-bar chart, Six Sigma, 100% inspection mode, and the Taguchi Method.
What are quality control procedures in audit?
The quality control policies and procedures applicable to a firm's accounting and auditing practice should encompass the following elements: Independence, Integrity, and Objectivity. Personnel Management. Acceptance and Continuance of Clients and Engagements.
What are the steps in the quality control process in order?
7-Step Quality Control ProcessStep 1: Harvester Accreditation. ... Step 2: Plant Accreditation. ... Step 3: Raw Material Inspection. ... Step 4: Processing Supervision. ... Step 5: Finished Product Inspection. ... Step 6: Inspection Reports. ... Step 7: Loading & Shipping.
What are the 3 types of quality control?
The Three Types of Quality Inspections There are three primary types of quality inspections: pre-production, in-line, and final. There are a variety of details that must be inspected and approved during each phase in order to detect and correct quality problems.
What is quality control checklist?
A quality control checklist is basically a written guide for your products' contents, packaging, color, barcodes, appearance, possible defects, functions and special requirements. It's also sometimes called an “inspection criteria sheet” or inspection checklist.
What are the 6 elements of quality control?
ISQC-1 outlines the elements of a system of quality control to be: a) Leadership responsibilities for quality within the firm; b) Relevant ethical requirements; c) Acceptance and continuance of client relationships and specific engagements; d) Human resources; e) Engagement performance; and f) Monitoring.
What are the standards for quality control?
Quality management standards are details of requirements, specifications, guidelines and characteristics that products, services and processes should consistently meet in order to ensure:their quality matches expectations.they are fit for purpose.they meet the needs of their users.
What are the 5 types of quality control?
There are seven primary quality control tools which include:Checklists. At its most basic, quality control requires you to check off a list of items that are imperative to manufacture and sell your product.Fishbone diagram. ... Control chart. ... Stratification. ... Pareto chart. ... Histogram. ... Scatter Diagram.
What is the first step in quality control?
Feedback: The first step in quality control is to determine criteria and standards. Measuring performance or making corrections is impossible if standards have not been clearly established.
What is control quality?
Control Quality is the process of monitoring and recording results of executing the quality activities to assess performance and recommend necessary changes . The key benefits of this process include: (1) identifying the causes of poor process or product quality and recommending and/or taking action to eliminate them;
What are some examples of quality control?
Examples of quality control include: 1 Inspection of products leaving the production line. 2 Expert technical review of reports. 3 Trial runs prior to plant commissioning.
What is the difference between Quality Control and Quality Assurance?
This distinction is commonly misunderstood. Quality Control (QC) is the measurement of outputs to determine whether they meet the accepted criteria. Quality Assurance (QA), on the other hand, analyzes the processes and systems that are producing the outputs. If you’re measuring the systems, it’s QA. If you’re measuring the outputs, it’s QC.
What happens when quality is poor?
On the flip side, a single poor quality deliverable can create a cycle of low performance, creating an environment where quality is not valued and people do not put in the extra effort.
When project deliverables are produced, they are subjected to quality control before they are delivered to their end user?
When project deliverables are produced, they are subjected to quality control before they are delivered to their end user. That means they need to be measured and compared against the standard that’s been identified in the project management plan. If you don’t know the quality of your outputs, you cannot make effective decisions.
Why should the planned results be identified and then actual results tracked side by side?
For some projects, the planned results should be identified and then actual results tracked side by side to ensure the conformance of the deliverables. This type of comparison helps tremendously in the identification of schedule and cost related to quality improvement.
What is a project management plan?
The project management plan will identify what will be measured and the pass/fail criteria. In the case of a manufacturing facility for a new line of pens, you might measure whether they draw a straight line without problems, if they come apart after using them for 10 minutes, or if the ink dries up after leaving them open for 4 hours. You would choose to take a predefined number of pens off the assembly line for testing. The results would be graphed, analyzed or presented to the interested parties.
Why is it important to implement quality control procedures?
Implementing quality control procedures ensures you are selling the best products to your customers. In addition, practicing quality control has a positive impact on employee conduct. Quality control can inspire employees to create high-quality goods leading to greater customer satisfaction.
What Is Quality Control?
Quality control (QC) is a process through which a business seeks to ensure that product quality is maintained or improved. Quality control requires the company to create an environment in which both management and employees strive for perfection. This is done by training personnel, creating benchmarks for product quality, and testing products to check for statistically significant variations.
How does quality control affect a company?
Having quality control in place within a business can only help ensure product quality and the overall success of a business. The environment of quality control influences employees' attitudes about the workplace and creates a sense of ownership in the products and company as a whole. Quality control can be done in various ways, from training personnel to creating data-driven tools to test products and set standards. Quality control methods help create a safe work environment and product safety that benefits customers and the company alike.
What is quality control in food production?
An aspect of quality control in food production would be overseeing the ingredient specifications, reviewing supplier lists, and ensuring the facility where the food product is made is sanitary.
Why are quality control protocols important?
Quality control protocols may help you lower your inspection costs and use your resources in a more cost-effective manner, too.
What is quality control in manufacturing?
In food and drug manufacturing, quality control includes ensuring the product does not make a consumer sick, so the company performs chemical and microbiological testing of samples from the production line .
Why does the food industry use quality control methods?
The food industry uses quality control methods to ensure customers do not get sick from their products.
What is quality control?
It is a process that strives for business perfection through well-defined controls. A quality control process ensures your business is delivering a consistent product, service, and customer experience.
Why is quality control important?
It makes it easier to monitor your operations, delegate duties, and even expand to new locations. The process forms a key component of a well-run business. Quality control processes can be used for all types of businesses, whether product-based or service-based.
What is IPQC in manufacturing?
IPQC - In-process Quality Control. IPQC refers to quality control during the assembly process. It is crucial because you can detect and handle the problem that occurs ahead of time. OQC - Outgoing Quality Control. OQA is the inspection of products before shipping.
Why use flowcharts in a process?
Flowcharts make it easy to understand the product or service process, outline quality control, and increase efficiency. You could try EdrawMax and build the quality control process with flowcharts that deliver results. Flowchart made simple clearly illustrates the equipment and materials included in the process. It also makes it simple to know every personnel contribution at each stage.
What is quality assurance?
Quality assurance provides confidence (both internally to management and externally to customers and other regulators) that the quality requirements will be fulfilled. Briefly, QC can be taken as the operational activities or techniques used to fulfill quality requirements. On the other hand, quality assurance is all the planned ...
What is OQA inspection?
OQA is the inspection of products before shipping. It's a crucial step in ensuring the shipment is defect-free.
What is the purpose of well-designed processes?
Well-designed processes lead to high-quality products and services. Create operational processes to deliver quality and continuously measure the results. If you and your company work consistently to improve the processes, your product or service will get better and better. 4.
Why is quality control important?
Establishing stakeholder trust: Quality control is an important aspect of functional business operations. Having a functioning QC process builds trust with stakeholders and business leaders by providing a clear path toward achieving goals.
What is the QC process?
The QC process, or quality control process, refers to the steps involved with upholding consistent standards and specifications for the products and services you provide to consumers. Any business can have a QC process, regardless of the type of goods or services it offers. The QC process involves identifying standards for quality, regularly reviewing products to ensure they meet those benchmarks and removing any products that don't meet quality expectations. It also involves ensuring that the people creating goods or offering services have the necessary skills and training to provide an excellent experience.
How does QC help customers?
Improving customer relationships: By implementing and upholding a QC process, you output functional, durable products to consumers. This can help you develop positive relationships with consumers and create a lasting base of dedicated returning customers who trust the quality of your products.
How to improve quality of work?
Develop instructions for workflows that coordinate with your quality expectations. Determine what protocols result in the best quality outcomes that consistently meet your standards, then write them down as company procedures. Select equipment and tools that en able staff to accomplish goals. Consider testing different operational methods to find the best practices for each aspect of quality control. If multiple team members have different methods for completing a task, see which technique produces the best quality in the most efficient manner.
How to have a good QC process?
To have an excellent QC process, it's important to prepare detailed training materials so that all incoming staff members understand quality expectations. Compile onboarding documents, handbooks and blueprints that explain how to manufacture products, deliver services and complete quality checks. Describe the steps in the quality control process and explain what to do when a product doesn't meet the standards. This creates consistent QC results for the company as people change positions and as teams expand.
Why is QA important?
Creating automation: A good QA process makes it easier to delegate tasks and automate business responsibilities. When you have a system to check the quality of products at each step in the supply chain, you can help company operations function without direct supervision.
How to maintain a reliable business reputation?
One of the best ways to maintain a reliable business reputation and provide consumers with high-quality products is to have a thorough quality control (QC) process. Understanding what the QC process is and how to develop one is a useful step toward implementing best practices at your workplace and being a top competitor in your field.
What is quality control procedure?
Quality control procedures are a code of guidelines (usually written down and kept in quality documentation) which set and establish the quality standards and norms which ensure consistent quality across the company and across projects. Many of these quality control procedures don't originate in thin air and aren't down to interpretation.
What are construction quality control procedures?
Construction quality control is at the heart of the construction industry. Construction projects create and deliver the assets and infrastructure which people rely on to move around and conduct life safely. Because of this - every supply, every piece of equipment and every activity conducted on construction projects must be conducted in such a manner that quality can be almost guaranteed. And where it can't, there must be adequate testing in place to catch these mishaps and rectify them before the end of the project or end of that phase of works.
How many quality procedures and processes do you document?
How many quality procedures and processes you document will largely be based on the clients and contractors you work with - as well as the nature of work you conduct.
What are the mechanisms for creating and 'keeping' these quality control procedures?
So the mechanisms for creating and 'keeping' these quality control procedures are quality policy and procedure documents. These documents can long and short, and contained in word docs, PDFs, excel spreadsheets and more.
Why is quality control important in construction?
So the objective of quality control procedures is to establish the quality requirements of your company and workers whilst seeking to continuously improve the quality ...
How many pronged are quality control procedures?
But your quality control procedures will be generally two pronged:
What is quality control?
They are often minimum standards derived from standards set by authorities, governing bodies and governments. In fact, your quality control procedures are often simply aligning your project and company activities with these ISO and other standards - and then bolstering the edges and inputs where required.
What is QA/QC in BSPR?
QA/QC as applied to sample collection is intended to provide a context for thesubsequent review, interpretation, and validation of the resulting analytical data.The BSPR QA/QC guidelines for the collection of trip and field blanks, duplicateand spiked samples, and background samples are contained in Exhibit 2.4-3.While the number of QA/QC samples varies on a case-by-case basis, a good rule-of-thumb is that 10 percent of the total number of samples collected should beQA/QC samples to assure the control of sample quality.
What is QA in data collection?
# Quality assurance (QA) is a process designed to ensure that all data collected areadequate for the purpose for which they are collected, that is, the data are complete,reliable, and representative. Quality control (QC) is the routine application ofprocedures for controlling the accuracy and precision of data measurements. PracticingQA/QC ensures that all samples collected are of adequate quality to ensure an efficientand effective cleanup and, when necessary, to withstand legal scrutiny in a court case.
Who Can Perform Quality Control Procedures for Manufacturing?
Ultimately, finding a trusted quality control inspection company can be a bit daunting if you don’t know where to look. That’s where we come in.
Why is quality control important?
Furthermore, quality control ensures that only top-shelf products and services are released into the world. In the same way, the ones that don’t meet the recommended requirements should be discarded immediately.
What Are the Benefits of Quality Control?
Most people think that quality control only benefits customers, however, that couldn’t be farther from the truth. Yes, your customers will get to buy high-quality products, but, in turn, by providing those products, you will get the following:
What can inspectors do after inspection?
After this inspection is complete, the inspectors can then look into why a product with unacceptable standards was made, and take measures to correct the mistake so it doesn’t happen again.
What is pre production inspection?
Through our pre-production inspections, we check the raw materials (and their condition), inspect the storage, and the supplier’s production quality.
How many ways are there to perform statistical quality control?
There are two ways to perform statistical quality control:
How many ways are there to perform quality control checks?
There are two ways to perform quality control checks:
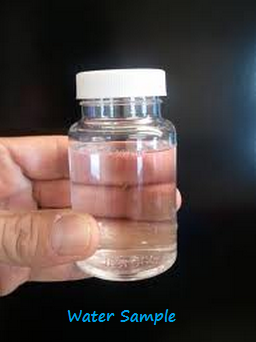
Quality Control vs. Quality Assurance
Measuring Outputs
- Quality criteria should have been identified during the planning phase (PMBOK: Plan Quality Management) for each project deliverable. When project deliverablesare produced, they are subjected to quality control before they are delivered to their end user. That means they need to be measured and compared against the standard that’s been identified in the project manageme…
QC Forms
- During the planning phase the project manager should develop appropriate forms for measuring the quality of the deliverables. This ensures that consideration has been given at the outset to measuring the right things and how they will be reported. When the inevitable issues arise and questions are asked, it is often invaluable to be able to produce a document that confirms the q…
Quality Metrics
- The project management plan will identify what will be measured and the pass/fail criteria. In the case of a manufacturing facility for a new line of pens, you might measure whether they draw a straight line without problems, if they come apart after using them for 10 minutes, or if the ink dries up after leaving them open for 4 hours. You would choose to take a predefined number of …
Prevention vs. Inspection
- It is important to note the distinction between prevention, which keeps errors from happening, and inspection, which keeps errors out of the hands of the customer. Inspection is generally the domain of Quality Control, while prevention is concerned with improving the processes so that problems do not occur, thus it is Quality Assurance. But there is an overlap, particularly when Qu…
Tolerance vs. Control Limits
- A few definitions which should guide your world view in the area of quality: 1. Toleranceis the range of acceptable results. If a result is out of tolerance, it must be rejected. 2. Control limitsare boundaries which represent acceptable variation for the purpose of controlling and manipulating the process. A result can be within acceptable tolerances, but signify a process which exhibits c…
Attributes vs. Variables Sampling
- When taking quality control measurements, the data can be collected based on the following two methods: 1. Attributes samplingcontains a single pass/fail criteria. The product either passes, or fails. 2. Variables samplingcontains a sliding scale criteria. The product is rated on a scale of 1-10, class A-E, or similar.
Planned vs. Actual Data
- For some projects, the planned results should be identified and then actual results tracked side by side to ensure the conformance of the deliverables. This type of comparison helps tremendously in the identification of schedule and cost related to quality improvement.
Project Changes
- The PMBOK dictates that quality control activities result in project changes (see above Outputs: Change Requests). If the quality control measurements reveal quality levels below the standards specified within the Quality Management Plan(a component of the overall Project Management Plan) a change to the project must be initiated through the change procedures within the projec…