
What are 5 steps for Six Sigma?
- Define the problem. Craft a problem statement, goal statement, project charter, customer requirement, and process map.
- Measure the current process. Collect data on current performance and issues. Verify that the data is reliable, and update the project charter as needed.
- Analyze the cause of issues. ...
- Improve the process. ...
- Control. ...
How to ensure Six Sigma success?
- Visible, consistent support and an active role in communication and reward.
- Assuring linkage of Six Sigma to corporate strategies.
- Clear prioritization (relative to other initiatives, programs and priorities).
- Requiring the use of facts and data to support actions at all levels of decision-making.
How do you start a Lean Six Sigma project?
- Losing weight or improving heart rate
- Improving fitness routine/workouts (miles walked/run, weights lifted, workouts per week, basketball free throws made, golfing accuracy or distance, stretching/meditation routine, stress mitigation, resting heart rate, etc)
- Reducing debt, bills and expenses
What are the Six Sigma stages?
What are the 6 Sigma tools?
- Continuous Improvement.
- Culture of Quality.
- Lean.
- Process Management.
- Root Cause Analysis (RCA)
- Statistics.
- Value Stream Mapping (VSM)
How to implement lean Six Sigma successfully?
Six Sigma Implementation
- Deciding to Use Six Sigma. The first thing you have to do as a company when considering Six Sigma implementation is to develop a statement outlining why you need this ...
- Proper Six Sigma Implementation. ...
- Lean Six Sigma Implementation of the Red Cross Hospital in the Netherlands. ...
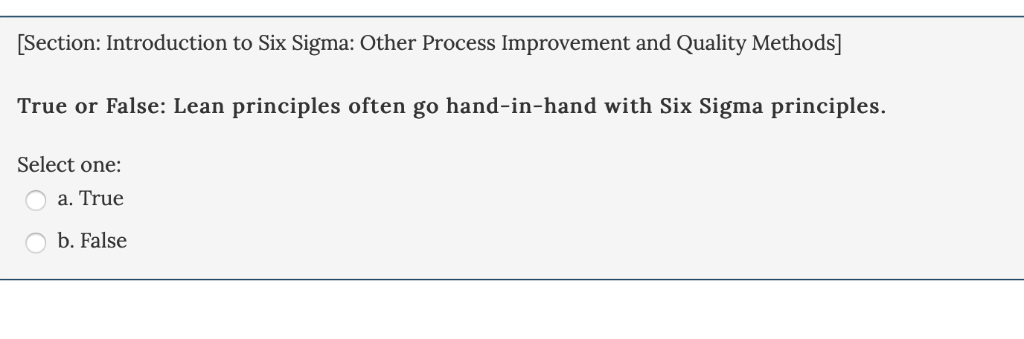
What are the 5 steps of Six Sigma?
What are 5 steps for Six Sigma?Define the problem. Craft a problem statement, goal statement, project charter, customer requirement, and process map.Measure the current process. Collect data on current performance and issues. ... Analyze the cause of issues. ... Improve the process. ... Control.
What are the 5 Whys in Six Sigma?
The 5 Whys is a basic root cause analysis technique used in the Analyze phase of the Six Sigma DMAIC (Define, Measure, Analyze, Improve, Control). To solve a problem, we need to identify the root cause and then eliminating it.
What are the 6 Six Sigma process?
Six Sigma methodologies DMAIC (define, measure, analyze, improve, control) is used to correct a process that already exists. DMADV (define, measure, analyze, design, validate) is used to create a new process.
What does the 5 Whys stand for?
Five whys (or 5 whys) is an iterative interrogative technique used to explore the cause-and-effect relationships underlying a particular problem. The primary goal of the technique is to determine the root cause of a defect or problem by repeating the question "Why?" five times.
What are the 5 steps of root cause analysis?
Identify Root Causes in 5 Easy StepsRealize the Problem. First, you need to identify what actually went wrong. ... Collect a Sufficient Amount of Data. ... Identify the Associated Causal Factors. ... Draw a Conclusion. ... Implement Any Necessary Changes.
What does the 6 in Six Sigma stand for?
6 standard deviationsSix Sigma stands for 6 standard deviations (6σ) between avarage and acceptable limits. LSL and USL stand for “Lower Specification Limit” and “Upper Specification Limit” respectively. Specification Limits are derived from the customer requirements, and they specify the minimum and maximum acceptable limits of a process.
What are the 6 Sigma Belts?
Get to know each of the rankings so you can build skills that will help your company function more smoothly and advance your career.White Belt. ... Yellow Belt. ... Green Belt. ... Black Belt. ... Master Black Belt. ... Champion.
Why it is called 6 Sigma?
It's called Six Sigma because the term sigma refers to one standard deviation in a data set. The idea is that six such deviations should occur before the process results in a defect. When a process achieves Six Sigma, it reaches a point where only 3.4 errors per one million process events result in a defect.
What are the 5 Whys technique?
The method is remarkably simple: when a problem occurs, you drill down to its root cause by asking "Why?" five times. Then, when a counter-measure becomes apparent, you follow it through to prevent the issue from recurring.
What is 5 why analysis example?
#1 – Taiichi Ohno, the creator of the 5-Why technique, is quoted using the following example to teach using 5-Why's for root cause analysis: “Why did the robot stop?” The circuit has overloaded, causing a fuse to blow. “Why is the circuit overloaded?”
What are the 5 Whys in quality?
Five whys (5 whys) is a problem-solving method that explores the underlying cause-and-effect of particular problems. The primary goal is to determine the root cause of a defect or a problem by successively asking the question “Why?”.
How do you perform 5 Whys?
Here's the process for conducting a successful 5 Whys analysis of your own:Gather a team. Collect the team members who are knowledgeable about the process that is to be examined. ... Define the problem. ... Ask “why?” five times. ... Take corrective action. ... Monitor and share your results.
What is the Six Sigma method?
The steps in Six Sigma methodology is essentially one that endeavours to adopt a smarter way of doing things so as to minimize the occurrence of defects. It emphasizes on doing things right the first time, rather than spending effort on correcting the defects.
What is the third step of Six Sigma?
During this phase, the data collected during the measure phase is used to analyze the gap between the current and desired performance. Next, you perform a root-cause analysis to define the possible reasons for the performance gap and quantify the main causes for variation. The gap between the current and desired state is also calculated in financial terms.
How many stages are there in Six Sigma?
Seems logical, right? But how do we ensure that we do it right the first time? Well, the steps in six sigma methodology propagates adopting a simple five stage process as detailed below:
What are the tools used in the analysis phase?
The key tools used during the Analyze phase are Cause and Effect diagram, Regression analysis, and Flow diagrams.
What tools are used during the define phase?
The key tools used during the define phase are: Project Charter, stakeholder analysis, and SIPOC (Suppliers, Inputs, Process, Outputs, and Customers) diagram which visually depicts the key elements for the Six Sigma project.
How many phases are there in 6 Sigma?
Below are the 5 phases of six sigma, which are as follows:
What is Six Sigma?
Basically, it is a measure by which defects in production, manufacturing, and development of any product, as well as service, can be eliminated. Well, elimination of defects is not virtually possible but minimizing it to negligible.
What is the DMADV method?
Another Six Sigma method that is widely employed is the DMADV method. This involves the Design of the procedure, ensuring customer satisfaction, Measure the parameters required for quality maintenance, Analyze so that an alternative is always present to maintain the superior quality, Design the details, and finally, Verify all the processes before implementing them.
How many defects per million units of a product can be produced in six sigma?
Statistically, when six sigma is achieved, the process must not produce 3.4 defects per million units of any product or opportunity.
What is the control phase of an improvement process?
This process is called the Control phase, where one needs to maintain the improvement achieved.
What was the period when excellence through inspection was started?
1920 -1940 was the period when “Excellence through Inspection” was started. This was how the quality of products was maintained by a quality controlling inspection department in companies.
Why should teams and leaders be appointed and trained in Six Sigma’s methods?
Teams and leaders should be appointed and trained in Six Sigma’s methods so that they can serve properly.
How many principles are there in Six Sigma?
There are five main principles of Six Sigma:
What is Six Sigma?
Six Sigma is a term used to define various techniques and management tools designed to make business processes more efficient and effective. It provides statistical tools to eliminate defects, identify the cause of the error, and reduce the possibilities of error. Thus, Six Sigma creates an environment of continuous process improvement, ...
What is the objective of Six Sigma?
The primary objective of Six Sigma is customer satisfaction , and to achieve the objective, various methods are followed to improve the performance of a product or business process. DMAIC and DMADV are the main methodologies of Six Sigma that apply to different business environments.
Why is structured process important?
A structured process should be adopted where all stakeholders collaborate and contribute to finding solutions to complex issues. The team needs to achieve proficiency in the methodologies and principles applied. Hence, specialized knowledge and training are required to lower project failure risks and ensure optimal performance of the processes.
When was Six Sigma developed?
It was developed by Motorola, Inc. in 1986. Six Sigma can be applied to any process in any industry to establish a management system for identifying errors and eliminating them. It provides methods to improve the efficiency of business structure and quality of processes, enhancing the profitability of the business.
What happens when an inefficient process is eliminated?
Whenever an inefficient or faulty process is eliminated, the employee approach and work practices need to be changed. A flexible and responsive environment to the changes in processes can lead to the efficient implementation of the projects.
What is the Six Sigma method?
There are many other ways to handle problem-solving, but the Six Sigma way is one of the top tools as it uses solid, reliable data instead of a gut-feel approach. By collecting data, the problem-solving team also has evidence to back up their decisions to solve a problem in a specific way.
What is 6 sigma?
Six Sigma is a problem-solving process that is used by engineers and other professionals worldwide. The Six Sigma process is a structured, data-driven approach to problem-solving. There are many aspects to the 6 Sigma ranging in difficulty which is why there are levels of Six Sigma Certification: green belts, black belts, and master black belts. Becoming a Six Sigma practitioner requires completing a Lean Six Sigma Green Belt training. There are also free Lean Six Sigma courses which explain the main process that is our topic for the day: DMAIC.
What is the acronym for Six Sigma?
The process for Six Sigma is abbreviated as “DMAIC” and each letter in this abbreviation corresponds to a phase. The phases associated with each letter of the acronym is listed below. The advantage of the DMAIC as the Six Sigma approach is not the top-level phases themselves but what is contained in each phase.
What is the second phase of DMAIC?
The second phase of DMAIC is Measure. This phase aims to collect data from the process and understand current quality level. The team measures the existing system in this stage by establishing valid and reliable metrics to help monitor progress towards the goal defined in the previous step. In other words, the team identifies what data is available and from what source. It is important that the measurements are accurate, so it helps to do a test stage during which different operators collect data. In this way, it is possible to determine how the data should be collected to get the most reliable results. Unreliable data collection defeats the purpose of Six Sigma as it is a data-driven approach. They develop a plan to gather it, do the actual data collection and summarize it. In this phase of DMAIC, the team answers the question “How are we doing with the current process?”
What is the process of Lean Six Sigma?
Lean Six Sigma is simply a process for solving a problem. It consists of five phases: Define, Measure, Analyze, Improve, & Control. This process is also known as DMAIC (“duh-may-ik”), its acronym. DMAIC is a five-step method for improving existing process problems with unknown causes.
What is the definition phase of Lean Six Sigma?
Define the problem. What problem would you like to fix? The Define Phase is the first phase of the Lean Six Sigma improvement process. In this phase the project team creates a Project Charter, a high-level map of the process and begins to understand the needs of the customers of the process. This is a critical phase in which the team outlines the project focus for themselves and the leadership of the organization.
How do you sustain the improvement?
How do you sustain the improvement? Now that the process problem is fixed and improvements are in place, the team must ensure that the process maintains the gains. In the Control Phase the team is focused on creating a Monitoring Plan to continue measuring the success of the updated process and developing a Response Plan in case there is a dip in performance. Once in place, the team hands these plans off to the Process Owner for ongoing maintenance.
What is the analysis phase?
What is causing the problem? The Analyze Phase is often not given enough attention and, without analysis, teams jump to solutions before knowing the true root causes of the issues. The result is teams who implement solutions but don’t resolve the problem! These efforts waste time, consume resources, create more variation and, often cause new problems. The ideal is for teams to brainstorm potential root causes (not solutions), develop hypotheses as to why problems exist and then work to prove or disprove their hypotheses. Verification includes both process analysis and data analysis and has to be completed before implementing solutions. This is the crux of the Analyze Phase!
What is Six Sigma methodology?
At its core, Six Sigma involves collecting and leveraging data to eliminate defects and waste in manufacturing, with the end goal of improving overall efficiency and quality.
What is Six Sigma?
Six Sigma should be recognized and celebrated for what it is: a data-driven approach to streamlining production and manufacturing. For industries and businesses outside of manufacturing, though, teams should explore more flexible project management or process improvement methodologies. For all its successes, Six Sigma can’t replace human ingenuity and hard work. Look instead to the brain power in your organization, and find a methodology that works with your team’s creativity and can be customized where needed.
How is Six Sigma used?
However, just because companies in different sectors have applied this methodology doesn’t necessarily mean that these companies have used it correctly or effectively. Outside of a manufacturing operation, Six Sigma often fails to yield the kind of results needed to justify such a time-consuming and expensive management change.
What are the limitations of Six Sigma?
One of the challenges of the fact-driven process of identifying a problem and working toward a solution is that it tends to leave out a key component: humans—and more importantly, how humans impact and work through different obstacles. Sometimes it is often beneficial to give employees a chance to tackle issues head-on before investing in a complete operational overhaul.
What can you use instead of Six Sigma?
Dozens of project management methodologies exist with varying degrees of structure, rules, and processes. Here are just a few of the most common:
How many defects should a company reduce in a 6 sigma process?
The term “sigma” is a measurement of how far from perfect a system or producer can get—by Six Sigma standards, companies should reduce manufacturing defects to less than 3.4 per 1 million units.
How to improve a process?
Improve the process. Decide on solutions to fix issues and create process maps for those new solutions. Take steps to implement the new fixes and continue to measure improvement.
What is the extra step to DMAIC?
Some organizations add an extra step to DMAIC at the beginning called Recognize where they evaluate whether DMAIC is the correct tool to use for their needs.
What is the analysis step?
The analysis step is where we have to dig in deep into the existing processes and work out the root causes of the problems.
Why is it important to draw up a process map?
In order to have a clear and easy to understand overview of the planned DMAIC process, it is useful to draw up a high level process map.
What is the improve section of DMAIC?
The improve section of the DMAIC process is where we take advantage of all the preparatory work we’ve done so far.
What is the potential of DMAIC?
The potential is there to reduce variables like lead times or defects while improving variables like cost savings or productivity.
When you have scope, can you map the process?
Once you have your scope, you can begin to map the existing process .
Can BPMN be used to map business processes?
We’ve already mentioned in this article how you can use strategies like BPMN to map business processes, but it isn’t the only approach. A very similar approach might be to use an As Is Process Map, which can incorporate BPMN elements but is not defined by it.
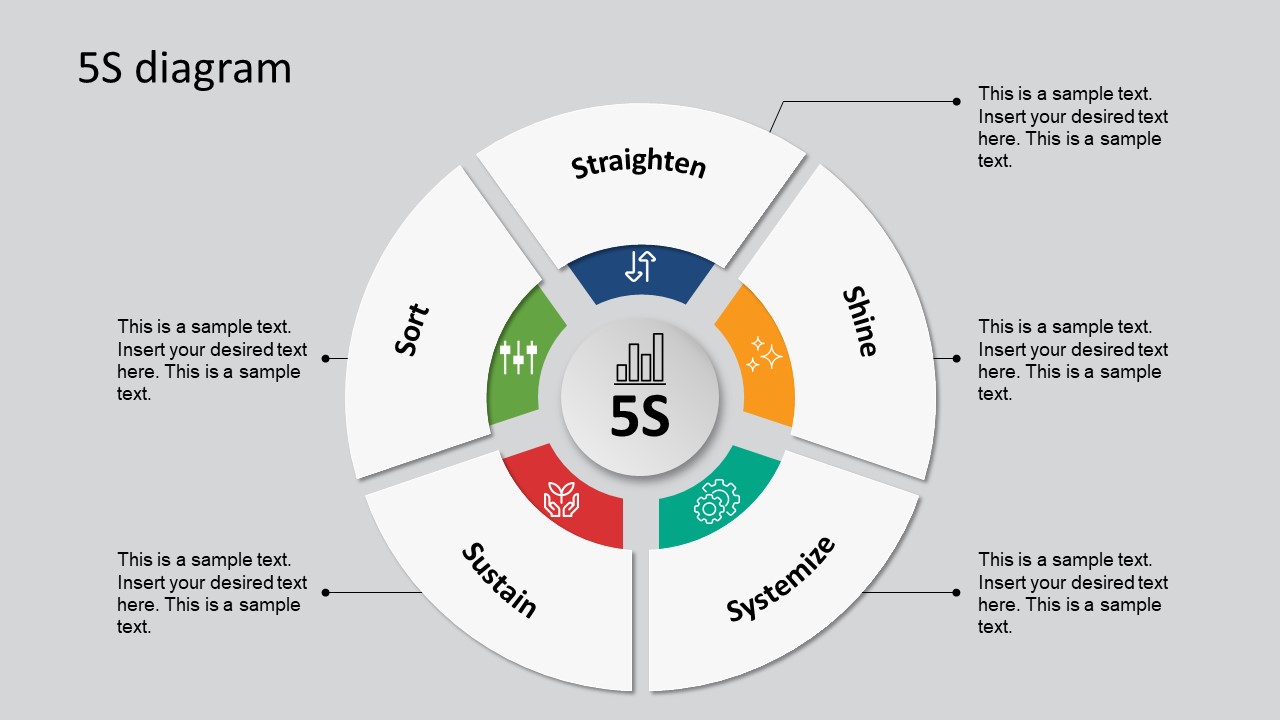
History of Six Sigma
Customer Focus
Principles of Six Sigma
Concept of Six Sigma Project
Implementation of Six Sigma
Conclusion – Concept of Six Sigma
- Another Six Sigma method that is widely employed is the DMADV method. This involves the Design of the procedure, ensuring customer satisfaction, Measure the parameters required for quality maintenance, Analyze so that an alternative is always present to maintain the superior quality, Design the details, and finally, Verify all the processes before ...
Recommended Articles