
- 1G – (flat welding position)
- 2G – (horizontal welding position)
- 3G – (vertical welding position)
- 4G – (welding position overhead or overhead)
- 5G – (uphill/downhill vertical welding position)
- 6G/6GR – (overhead vertical welding position)
- 1G – (flat welding position)
- 2G – (horizontal welding position)
- 3G – (vertical welding position)
- 4G – (welding position overhead or overhead)
- 5G – (uphill/downhill vertical welding position)
- 6G/6GR – (overhead vertical welding position)
What are the basic welding positions?
Basic Welding Positions! The four basic welding positions are: flat, horizontal, vertical, and overhead. The most common type of weld you will do is a Fillet weld and a Groove weld, and you can accomplish these welds in all four positions.
What is 2G position in welding?
Another similar welding position is 2G, which means a horizontal welding position for groove not for fillet welds. In this position, the weld axis remains horizontal and the weld is facing the vertical plane. It is a vertical-up position used for both butt and fillet welds.
What is the groove weld position?
In the Groove Weld position the weld axis is in a horizontal plane (approximately), and the face of the weld is on a vertical plane (approximately). See Image B above.
What are the 5G welding positions?
The 5G welding positions are complex welding positions and can be classified into several. These are; This is an upward welding position used mainly for pipe welding. In this position, welders assume three welding positions in a sequence. It starts from overhead to a horizontal and then to a flat position.
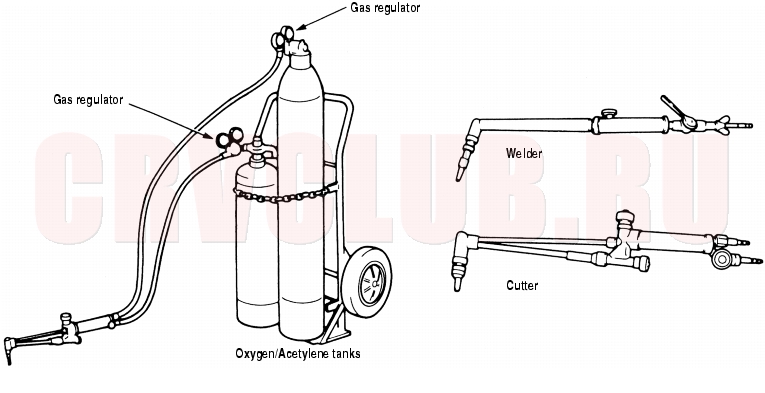
What does 1G 2G 3G and 4G mean in welding?
To help operators understand the type of weld joint (fillet or groove) and the weld position, each weld is given a number and a letter — 1G, 2G, 3G, 4G or 1F, 2F, 3F, 4F — to indicate the position and the type of weld required. Welds with a 1 are flat position, 2 is horizontal, 3 is vertical and 4 is overhead.
What is 1F 2F 3F 4F welding?
With the first digit representing the welding position: 1: welding position by. 2: Horizontal welding position. 3: standing position welding. 4: ceiling welding position.
What is 1G 2G welding?
The positions of groove welds are divided into 1G, 2G, 3G, 4G, 5G and 6G, respectively indicating flat welding, horizontal welding, vertical welding, overhead welding, horizontal fixed welding of pipeline and 45 °inclined fixed welding of pipeline.
What is the 5G 6G position in welding?
5G and 6G Welding Positions In the 5G welding position, the pipe is in the horizontal position, whereas in 6G position, the pipe slopes at approximately 45° from the horizontal (X) axis or 45° from the vertical (Y) axis. Unlike the 1G and 2G position, the pipe is in a fixed position and not rotating.
What is G welding?
Grove welds are the second most common type of weld. A grove weld is formed when filler metal is deposited in the groove between two pieces of metal.
What position is 4G?
Overhead PositionOverhead Position (4F or 4G) Overhead welding is performed from the underside of a joint. In overhead welding, the metal deposited tends to drop or sag on the plate, causing the bead to have a high crown.
What position is 5G?
5G – Horizontal Fixed Position In the 5G pipe welding position, the pipe will be in the horizontal position. Unlike the 1G weld position, the pipe will always remain fixed, and it can not be rotated. The welder moves around the pipe outer surface in the vertical direction to perform the welding.
What is 1G 2G 3G 4G 5G 6G?
1G, 2G, 3G, 4G and 5G are the five generations of mobile networks where G stands for Generation, and the number denotes the generation number. 5G is the latest generation, whereas 1G networks are now obsolete. The cellular technologies GSM, UMTS, LTE and NR enable 2G, 3G, 4G and 5G, respectively. Term.
What is 3G welding position?
Welding in a 3G position means moving the torch vertically, up and down across a surface. This is in contrast with 1G (flat surface welding), 2G (horizontal welding), and 4G (overhead ceiling welding).
What is a 4G weld test?
What Is A 4G Weld Test? A 4G weld test is a type of welding test that enables welders to obtain certification. What 4G weld in general covers is the position of which the welders can perform his welding services and get the job done.
What is a 2F weld?
PB / 2F: This is the horizontal position for fillet welds. The welder will be holding the torch at around 45º most of the times (although it depends on the plate or pipe position) with the piece right next to him: PC / 2G: Commonly referred to as the horizontal position for butt welds.
What is 5f welding position?
A 5f joint is a tube or pipe to plate where the plate is. vertical and the pipe axis is running horizontal. in this video, I used an upside down V technique to. trace the leading edge of the weld puddle .
What is a 4F weld?
PD / 4F: This is the overhead position for fillet welds. The welder will be holding the torch at around 45º most of the times (even if it depends on the plate or pipe position), this time while being below the piece. PE / 4G: Overhead position for butt welds.
What are F numbers in welding?
The F number grouping of filler metals refers to their similarity on their usability characteristics. The usability determines the ability of a welder to deposit a sound weld metal with a certain filler metal.
What is the meaning of E6013 in welding electrode?
Thus the number E6013 written on an electrode indicates that it is a rutile potassium based flux coated mild steel electrode with 62,000 psi minimum tensile strength having light penetration which can be used in all positions of welding except vertically down.
What is F6 in welding?
F6 - Most Bare Wire ER70 / ER309 / FCAW (Fluxcored) F43 - Inconel. Backing: indicaes if a root pass/backing plate is needed. WITH - qualifed to weld on a backing (root pass or baking plate) WITHOUT - qualifed to weld root passes. Progression: indicates the direction of the weld.
What Is Welding Position?
In welding, the welding position is the relative position of the welding gun (hand-held welding torch) and workpiece. The welding gun is held differently for each welding process because different positions affect what type of weld joint can be made. Welding joints are classified according to how the weld pool forms in each particular position. There Are five basic welding positions.
Which position is the most difficult to weld?
The first is the horizontal position, which is difficult and is followed by the flat position and finally, the vertical position. A Lot of practice is needed to perfect this weld position.
What certification do you need to weld a pipe?
In particular, pipe welders can apply for a 5G and 6G certification . These two are used for the most complex welding positions. Therefore they require more experience. The 6G certification is seen as the gold standard of welding certification. Welders with this certification can weld all-around a stationary pipe.
What does the 3 digit mean in welding?
These numbers refer to the characteristics of the electrode. And the third digit in an electrode’s number designation refers to the welding position it can be used in. For instance, the number “1” means an electrode can be used in all ...
What does the R in 6G welding mean?
This is another 6G weld position that is also challenging. The “R” in the name stands for restricted. In this position, welding is performed in a ring mode. What this means is that a steel plate is placed under the weld site with an inch gap.
What is horizontal 2G welding?
The horizontal or 2G position is a little bit more complicated than the flat position. In this position, the workpiece is placed parallel to your body when welding. Thus the workpiece remains in front of you when welding.
What is it called when two metals are welded together?
When Two metals joints are welded between their surfaces or their edges or both their surface and edges is called groove weld. They create a V, J, or U-shaped cross-section.
What is welding position?
A welding position is a technique that allows a welder to join metals in the position in which they are found or the position in which a specific component will be used. 1. 1. Flat position.
Why Are There Different Welding Positions?
Those who’ve never taken welding classes or fused metal in the field might assume a welder simply sits at a workstation and fuses the metal components in front of them, moving freely around the table and repositioning the workpiece as needed.
What Are the Main Types of Welds?
Often considered the most popular type of weld, a fillet weld fuses two pieces of metal at an approximate right angle to each other. 4
What Are the Primary Types of Weld Joints?
When joints and welds are combined, you get weld joints. 4 The location where two or more pieces of metal are joined is what sets weld joints apart. Below are 5 common types of weld joints. 5
What Are the Welding Symbols for the Different Positions?
Let’s bring all of these concepts together so you know which welding position to use when reading the welding symbols on an architect’s blueprints:
What is fillet welding?
Often considered the most popular type of weld, a fillet weld fuses two pieces of metal at an approximate right angle to each other. 4
What is flat position welding?
1. Flat position. Also referred to as a “downhand” position, the flat position weld is the easiest and often the first weld that new students learn. The metals to be joined are placed flat, and the welder passes the electric arc over them, moving across the workpiece in a horizontal direction.
What are the four positions of welding?
Generally, welding positions are the angles at which metals are joined. They usually fall into four categories: horizontal, vertical, flat, and overhead.
What position is the metal piece in a flat welder?
For flat welding, the metal piece is in the horizontal position and remains parallel to the welder’s torso as he welds it while he stands in front of the machine.
Why is butt welding more complicated than flat welding?
The butt weld in the 2F/2f position may be somewhat more complicated than flat welding because the molten metal flows downward, and the torch is heated upward from the joint. Therefore, a uniform deposit is not possible at joints. Generally, welders should align the metals and secure the joint at both ends.
What clamps do you use for gripping pipes?
For gripping pipes, they can use steel bridge clamps when welding with a torch. Among other welding positions, 2G, a horizontal welding position for groove welds that do not involve fillet welding, is another. In this position, the weld axis lies horizontally, and the weld faces the vertical plane.
What is a F weld?
F-weld (F) – F-welding can be used to weld two separate parts of metal straight up or at a slight angle. Groove Welds (G)- Groove Welds (G) can be made in the groove if they can penetrate through the lower surface. This type of weld calls for full penetration to yield strong welds.
How many stages of welding 5G?
By doing so, welders are more productive and produce better welding results. When welding 5G, welders travel through three stages, beginning at flat, then horizontal, and concluding with overhead.
What is 5G welding?
Pipe welding is done in a 5G position in which the pipe axis does not turn or rotate horizontally. 5G stands for “ groove welding ” on the American Welding Society/American Society of Mechanical Engineer’s standard; ISO/EN standard calls it PF.
What Is a Welding Position?
Welding position is a technique that allows the welder to join metal in the position in which they are found or position in which specifics components would be used. Often this can be on the ceiling, in a corner, or on the floor.
Why Are There Different Welding Positions?
Those who have never taken a welding class or fielded fused metal may assume that a welder simply sits at a workstation and fuses metal components in front of them, moving freely around the table, and Restores the workpiece as needed.
What is the 1G 2G 5G 6G Pipe Welding Positions?
In the constructions phase of a project in the oil & gas industry, we often find welding activities on pipes or welding on tanks. In order to maintain the quality of welding, professional organizations (ASME, AWS, ISO, JWES) make rules and classifications of welding positions.
Why is welding important in 1G position?
Welding positions are important variables to determine weld quality. If welders have the qualification of 1G position, he is not allowed to perform welding in a more difficult condition such as 6G positions.
What is 1G welding?
The 1G welding position is a position where the pipe is in horizontal positions & the pipe can be rotated against the horizontals axis or the X-axis. The welder does the welding from the top of the pipe. The position of the welder does not change.
What is vertical position welding?
For verticals position welds, both the weld & the plate will be located vertically. One of the major problems when performing these welds is the molten metal flowing down and accumulating. Welding in a vertical position downhill or uphill can prevent this problem.
What angle should the torch be held at when welding?
This position can be used to obtain either a fillet or a groove weld. For a fillet weld, the torch will be held at a 45-degree angle. The weld axis is horizontal. How the positions are executed depends on the type of weld.
What to use when welding in overhead position?
You may want extra protection on the top of your head, such as a bandana under your welding helmet. Use a fully leather welding jacket, especially with a process like stick welding, which produces more sparks and spatter.
How to get better results in vertical welds?
Adjust the weld parameters to achieve the best results in vertical welds. Use a reduced wire feed speed and voltage to make sure the puddle does not get too fluid and falls or sags out of the joint. If you’re using a welding power source with Auto-Set™ technology, be sure to use the parameters designed for a thinner material, even if you’re welding thicker base metal. This helps keep the heat input lower to fight gravity.
What is vertical weld?
Vertical welds can be done in either vertical up (moving bottom to top in the weld joint) or vertical down (moving top to bottom in the weld joint). Vertical up is typically more common, especially on thicker materials. This welding position may be required when you’re working on a large weldment that cannot be easily moved into the flat or horizontal position.
What is a weld number?
To help operators understand the type of weld joint (fillet or groove) and the weld position, each weld is given a number and a letter — 1G, 2G, 3G, 4G or 1F, 2F, 3F, 4F — to indicate the position and the type of weld required. Welds with a 1 are flat position, 2 is horizontal, 3 is vertical and 4 is overhead. F stands for fillet weld, while G is a groove weld. A fillet weld joins together two pieces of metal that are perpendicular or at an angle. A groove weld is made in a groove between workpieces or between workpiece edges. Using this system, a 2G weld is a groove weld in the horizontal position.
What is the best welding method?
Regarding processes and modes of transfer, here are some general guidelines: 1 TIG welding can be done in all positions. 2 Short-circuit MIG can be done in all positions. 3 Spray transfer MIG is recommended for flat and horizontal welding only. 4 Pulsed MIG can be used in all positions. 5 Stick and flux-cored welding can be used in all positions, but the choice of filler metal is the main driver in this.
Why is flat welding easier?
Generally, flat is an easier position to weld in since you’re not fighting gravity. The weld puddle stays fluid and wets into the joint evenly. As a result, operators can typically run hotter with higher deposition rates in the flat position because there is no worry about the puddle becoming too fluid and gravity pulling it out of the joint.
What is a WPS welding?
Welders are likely to see these designations in a welding procedure specification (WPS) or on filler metal data sheets, which use them to call out the positional capabilities of specific filler metals.
What are the different welding positions?
The above-mentioned welding positions, i.e, flat, horizontal, vertical, and overhead are the most basic types of welding positions used for plate welding. However, these do not completely describe pipe welding positions. As far as pipe welding is concerned, there are four types of piping welding positions. They are: 1 Horizontal Rolled Pipe Weld Position 1G 2 Vertical Position 2G 3 Horizontal Fixed Position 5G, and 4 Inclined Weld Position 6G
What is welding position 2F?
Welding position 2F is for a fillet weld where the welding is performed on the upper side of a horizontal surface and against an approximately vertical surface keeping to welding torch at a 45-degree angle.
Why care about Pipe Welding Positions?
Welding position is one of the most important variables that determine weld quality. For each pipe weld position, welders need to undergo certification processes. If a welder is qualified to weld in a 1G position, he is not allowed to weld hard positions like the 6G position. But on the other hand, if the welder is certified for the hardest 6G position then he can work in the 1G position. So, expertise over each weld position levels up a welder’s skills and qualifications.
What is vertical welding?
In vertical position welding, the weld axis is almost vertical. Both the weld and the plate will lie vertically. For welding vertical surfaces, the molten metal runs downward by gravity and pile up. Welding in an upward or downhill vertical position can resolve this problem.
Why is welding important?
The welding position is very important as it affects the flow of molten filler material. It’s desirable that the welding operator understands the types of welding positions to smoothly accomplish the task. Also, at a certain position of the welder different welding processes are performed. In this article, we will learn about ...
How to get rid of a high crown in welding?
In overhead welding positions, the metal deposited tends to drop or sag on the plate that results in a bead with a high crown. To get rid of this difficulty, the molten puddle should be kept small. When the puddle becomes too large, one can remove the flame momentarily for molten metal to cool.
What is flat welding?
The flat welding position is easier and faster and the molten metal is drawn downward. Flat welding position is also known as down hand welding position.