
What are traditional overhead allocations methods?
- Add up total overhead.
- Compute the overhead allocation rate by dividing total overhead by the number of direct labor hours.
- Apply overhead by multiplying the overhead allocation rate by the number of direct labor hours needed to make each product.
What are the best practices for overhead allocation?
- The need for independence may prevent the financial statement auditor from serving in this role;
- The selected preparer should have knowledge and experience that is specifically relevant to the purpose for which the cost allocation will be used;
- The government should obtain ownership of the final work product;
How to calculate overhead allocation?
To help you keep uneven allocations straight, remember that overhead allocation entails three steps:
- Add up total overhead. ...
- Compute the overhead allocation rate by dividing total overhead by the number of direct labor hours. ...
- Apply overhead by multiplying the overhead allocation rate by the number of direct labor hours needed to make each product. ...
How to determine your production cost and allocate overhead?
To calculate the overhead rate per employee, follow the steps below:
- Calculate the labor cost which includes not just the weekly or hourly pay but also health benefits, vacation pay, pension and retirement benefits paid by the employer.
- Compute the total overheads of the business.
- Divide the overhead costs by the number of billable hours. ...
What are the different types of allocation methods?
Types of Cost Allocation Methods for Government Contractors
- Indirect Cost Basics. Indirect costs cover a wide range of expenses incurred for multiple cost objectives. ...
- Allocation Requirements and Method. The aim of indirect cost allocation is to work out the proportion of non-direct expenses that each project will bear.
- Overhead Pool. ...
- G&A Pool. ...
- Fringe Pool. ...
- Facilities Pool. ...

What are the different overhead allocation methods?
What Are the Methods of Overhead Allocation?Rate of Total Direct Job Costs.Rate of Direct Job Costs.Proportion of Direct Costs.Weighted Proportion of Direct Costs.Combination.
What are the 3 allocation methods?
There are three methods for allocating service department costs: direct, sequential, and reciprocal. The first step of each method is to classify each organizational unit as either an operating or service department.
What are the three methods of allocating overhead costs?
When Hewlett-Packard produces printers, the company has three possible methods that can be used to allocate overhead costs to products—plantwide allocation, department allocation, and activity-based allocation (called activity-based costing).
What are traditional costing methods?
The traditional costing method uses an allocation of expenses based on the volume of resources used during the production of goods. This method typically uses machine hours or man-hours consumed as the basis for estimating costs of production.
What are the four cost allocation methods?
When allocating costs, there are four allocation methods to choose from.Direct labor.Machine time used.Square footage.Units produced.
What is overhead allocation?
Overhead allocation is the apportionment of indirect costs to produced goods. It is required under the rules of various accounting frameworks. In many businesses, the amount of overhead to be allocated is substantially greater than the direct cost of goods, so the overhead allocation method can be of some importance.
What is the best way to allocate overhead costs?
To allocate the overhead costs, you first need to calculate the overhead allocation rate. This is done by dividing total overhead by the number of direct labor hours. This means for every hour needed to make a product, you need to allocate $3.33 worth of overhead to that product.
How do you allocate overhead costs to a project?
To allocate overhead, you'd add that amount to your total job costs. While this tends to be a simpler method, it also tends to be less accurate. Using a proportion among jobs. Alternatively, contractors can track each overhead cost in their G/L and distribute them proportionally across all jobs.
What is traditional overhead absorption costing?
Absorption costing is a method which allows businesses to charge overheads to products produced, which will then allow them to work out an estimated full production cost per unit. Absorption costing is said to be a simple approach to absorb overheads into cost units.
What is the difference between traditional and activity-based costing?
Traditional costing adds an average overhead rate to the direct costs of manufacturing products and is best used when the overhead of a company is low compared to the direct costs of production. Activity-based costing identifies all of the specific overhead operations related to the manufacture of each product.
What are the types of costing methods?
Types of costingAbsorption costing. Absorption costing, sometimes referred to as full costing, is used by a company to determine all costs that go into the manufacturing of a specific product. ... Historical costing. ... Marginal costing. ... Standard costing. ... Lean costing. ... Activity-based costing.
How are overhead costs allocated?
In the past, overhead costs were typically allocated based on factors such as total direct labor hours, total direct labor costs, or total machine hours. This allocation process, often called the traditional allocation method, works most effectively when direct labor is a dominant component in production. However, many industries have evolved, primarily due to changes in technology, and their production processes have become more complicated, with more steps or components. Many of these industries have significantly reduced their use of direct labor and replaced it with technology, such as robotics or other machinery. For example, a mobile phone production facility in China replaced 90 percent of its workforce with robots. 1
How is factory overhead allocated?
Traditional allocation involves the allocation of factory overhead to products based on the volume of production resources consumed, such as the amount of direct labor hours consumed, direct labor cost, or machine hours used . In order to perform the traditional method, it is also important to understand each of the involved cost components: direct materials, direct labor, and manufacturing overhead. Direct materials and direct labor are cost categories that are relatively easy to trace to a product. Direct material comprises the supplies used in manufacturing that can be traced directly to the product. Direct labor is the work used in manufacturing that can be directly traced to the product. Although the processes for tracing the costs differ, both job order costing and process costing trace the material and labor through materials requisition requests and time cards or electronic mechanisms for measuring labor input. Job order costing traces the costs directly to the product, and process costing traces the costs to the manufacturing department.
How is predetermined overhead calculated?
A predetermined overhead rate is calculated at the start of the accounting period by dividing the estimated manufacturing overhead by the estimated activity base. The predetermined overhead rate is then applied to production to facilitate determining a standard cost for a product. This estimated overhead rate will allow a company to determine a cost for the product without having to wait, possibly several months, until all of the actual overhead costs are determined, and to help with issues such as seasonal production or variable overhead costs, such as utilities.
What is manufacturing overhead?
The more challenging product component to track is manufacturing overhead. Overhead consists of indirect materials, indirect labor, and other costs closely associated with the manufacturing process but not tied to a specific product. Examples of other overhead costs include such items as depreciation on the factory machinery and insurance on the factory building. Indirect material comprises the supplies used in production that cannot be traced to an individual product, and indirect labor is the work done by employees not directly involved in the manufacturing process, such as the supervisors’ salaries or the maintenance staff’s wages. Because these costs cannot be traced directly to the product like direct costs are, they have to be allocated among all of the products produced and added, or applied, to the production and product cost.
What is activity based costing?
Activity-based costing is an accounting method that recognizes the relationship between product costs and a production activity, such as the number of hours of engineering or design activity, the costs of the set up or preparation for the production of different products, or the costs of packaging different products after the production process is completed. Overhead costs are then allocated to production according to the use of that activity, such as the number of machine setups needed. In contrast, the traditional allocation method commonly uses cost drivers, such as direct labor or machine hours, as the single activity.
Why is ABC costing important?
Because of the use of multiple activities as cost drivers, ABC costing has advantages over the traditional allocation method, which assigns overhead using a single predetermined overhead rate. Those advantages come at a cost, both in resources and time, since additional information needs to be collected and analyzed. Chrysler, for instance, shifted its overhead allocation to ABC in 1991 and estimates that the benefits of cost savings, product improvement, and elimination of inefficiencies have been ten to twenty times greater than the investment in the program at some sites. It believes other sites experienced savings of fifty to one hundred times the cost to implement the system. 2
What is the activity base for overhead?
An activity base is considered to be a primary driver of overhead costs, and traditionally, direct labor hours or machine hours were used for it . For example, a production facility that is fairly labor intensive would likely determine that the more labor hours worked, the higher the overhead will be. As a result, management would likely view labor hours as the activity base when applying overhead costs.
How was manufacturing overhead allocated in the 1900s?
In the early 1900s it was logical to allocate manufacturing overhead on the basis of direct labor hours ( or direct labor cost). The manufacturing process was not automated, there were hardly any variations in the products made (think Model T cars), and customers did not demand such things as just-in-time (JIT) deliveries or bar coding. In those days, when manufacturers increased the amount of direct labor, there was likely to be a related increase in such things as the number of factory supervisors, the factory space to be maintained, and factory supplies and utilities consumed. In other words, there was a high degree of correlation between the quantity of direct labor used and the amount of manufacturing overhead used. By allocating manufacturing overhead on the basis of direct labor hours, a product requiring 30 direct labor hours would be allocated twice as much manufacturing overhead as a product requiring 15 direct labor hours.
What happens if you don't allocate factory overhead?
Keep in mind that if the method does not allocate the true amount of factory overhead, the cost per unit of product will be wrong and could result in management making a flawed decision. As you review these methods, ask yourself for each given product, will the allocated amount of overhead reflect the actual amount of overhead used in that item's production? If a cause-and-effect relationship is not evident, is there at least an obvious correlation between manufacturing overhead and the basis for the allocation (such as machine hours)? If there is no correlation, the allocation method is suspect and could result in the improper amount of overhead being assigned to individual products.
How did direct labor affect manufacturing?
As the 20th century moved on, manufacturers studied and controlled direct labor's time and motion (think of Frederick Taylor's work) and began replacing direct labor with machines. The increased use of machines resulted in an increase in factory overhead due to such things as additional depreciation of the machinery, maintenance of the machinery, and machine setups. With direct labor being reduced and manufacturing overhead increasing, the correlation between direct labor and manufacturing overhead began to wane. A logical response was to begin allocating manufacturing overhead on the basis of machine hours instead of direct labor hours.
Why is it important to base manufacturing overhead rates on production departments?
Basing the manufacturing overhead rates on a company's production departments was an improvement over using just one rate for the entire plant —particularly when companies began manufacturing a greater variety of products. Some products being manufactured may have required many machine hours in one department but very few hours in another department, while other products may have used a much different combination of machine hours.
How much overhead is assigned to each unit of product X?
As shown in the above table, each unit of Product X will be assigned $30 of overhead, and each unit of Product Y will be assigned $60 of overhead. This is reasonable so long as there is a correlation between the quantity of direct labor hours and the cost of manufacturing overhead.
What happened when manufacturers increased the amount of direct labor?
In those days, when manufacturers increased the amount of direct labor, there was likely to be a related increase in such things as the number of factory supervisors, the factory space to be maintained, and factory supplies and utilities consumed. In other words, there was a high degree of correlation between the quantity ...
Do you need accurate allocations?
Although you don't necessarily need accurate allocations for purposes of preparing your company's financial statements, the odds are that at some point down the road those inaccurate allocations may result in poor pricing decisions, and that's something you can't afford to do in an increasingly competitive global market.
What is Overhead Allocation?
Overhead allocation is the apportionment of indirect costs to produced goods. It is required under the rules of various accounting frameworks. In many businesses, the amount of overhead to be allocated is substantially greater than the direct cost of goods, so the overhead allocation method can be of some importance.
Types of Overhead
There are two types of overhead, which are administrative overhead and manufacturing overhead. Administrative overhead includes those costs not involved in the development or production of goods or services, such as the costs of front office administration and sales; this is essentially all overhead that is not included in manufacturing overhead.
How to Calculate Overhead
The typical procedure for allocating overhead is to accumulate all manufacturing overhead costs into one or more cost pools, and to then use an activity measure to apportion the overhead costs in the cost pools to inventory. Thus, the overhead allocation formula is:
Standard Overhead Rates
Thus, far we have assumed that only actual overhead costs incurred are allocated. However, it is also possible to set up a standard overhead rate that you continue to use for multiple reporting periods, based on long-term expectations regarding how much overhead will be incurred and how many units will be produced.
Examples of Overhead Allocation
Mulligan Imports has a small golf shaft production line, which manufactures a titanium shaft and an aluminum shaft. Considerable machining is required for both shafts, so Mulligan concludes that it should allocate overhead to these products based on the total hours of machine time used.
How to allocate overhead in construction?
After all, the idea is to allocate (or, distribute) costs that each job shares responsibility for — meaning the job either caused or benefited from the cost. But, the costs should also be proportional to that responsibility. Figuring out how to strike that balance is the art of overhead allocation.
Does overhead allocation go through the roof?
Notice how their overhead allocation rate skyrocketed! Won’t that mean the allocated amounts in their job costing will go through the roof? It actually won’t. Here’s the trick: Under this method, our contractors would only apply this rate to certain job costs. In this case, since their rate is based on field labor, they’ll only apply it to incoming field labor costs. As a result, as long as their estimates are good, we would expect their allocation to be different with each method — but within the same ballpark.
Can contractors use one allocation basis?
That means contractors aren ’t necessarily locked in to using just one allocation basis or method for allocation — especially if they have the guidance of a CPA experienced in construction and the assistance of construction accounting software that’s built to be flexible.
Can a contractor use a method based on direct job costs but not total?
Alternatively, but using the same principle, our example contractor can use a method based on some direct job costs but not the total. If they decide that field labor costs are really what indicate whether their overhead costs are high or low, they might look just at that rate.
Can coating contractors allocate overhead?
Let’s look at an example. A coatings contractor might allocate most of their overhead by labor hours, but as an exception, they could also choose to allocate just their consumable supplies overhead (like roller heads and towels) based on their materials cost. The thinking would go like this: How many consumable materials they use may or may not have much to do with their job hours, but the more paint they use on a job, the more roller heads they can bet they’re going through.
Get professional help and free up your time for more important courses
Overhead allocation methods. (2016, Aug 11). Retrieved from https://phdessay.com/overhead-allocation-methods/
Cite this page
Overhead allocation methods. (2016, Aug 11). Retrieved from https://phdessay.com/overhead-allocation-methods/
How are factory overheads allocated?
Under the traditional method of allocating factory overhead ( manufacturing overhead, burden), most of the factory overhead costs are allocated on the basis of just one factor such as machine hours or direct labor hours. In other words, the traditional method implies there is only one driver of the factory overhead and the driver is machine hours (or direct labor hours, or some other indicator of volume produced).
What are the drivers of factory overhead?
In reality there are many drivers of the factory overhead: machine setups, unique inspections, special handling, special storage, and so on. The more diversity in products and/or in customer demands, the bigger the problem of allocating all the costs of these various activities via only one activity such as the production machine's hours.
What is activity based costing?
Activity-based costing is intended to overcome the weakness of the traditional method by having various pools of costs and then allocating each pool's costs on the basis of its root cause.
What are the methods of allocating support or service department cost to production department?
Methods of allocating support or service department cost to production department include direct method, step-down method and reciprocal method.
What is overhead cost?
Overhead cost is an ongoing expense of operating a business and is usually used to group expenses that are necessary to the continued functioning of the business, but cannot be immediately associated with the products/services being offered as in the costs do not directly generate profits.
What are the stages of absorption costing?
Absorption costing includes 3 stages, namely apportionment of overheads, reapportionment or allocation of service (non-production) cost centre overheads and also absorption of overhead.
Why is the direct, step down and reciprocal method of support department cost allocation different?
It is because of the different recognition that each method gives to support relationships. The direct method does not recognize any relationships that exist between support departments whereas step-down method gives only partial recognition to these relationships.
Why is the reciprocal method more powerful than the direct method?
However the application of this more powerful method is rare. It is because it is more complicated than other methods and it requires sophisticated computer aid. Some firms that use ERP software since this method requires additional modification in coding. Therefore most of the companies prefer employing either of direct or step down methods. Reciprocal method considers mutual services provided among all service departments, direct method and step-down method ignore this point. Moreover service department cost used by other service departments are also ignored in direct method. The drawback of direct method is partially reduced by step-down method by following a hierarchy among service departments while considering cost allocation.
How is production overhead recovered?
Production overhead, or usually refer to as manufacturing overhead, is recovered by absorbing them into the cost of a product. This process is known as absorption costing. Absorption costing means that all of the manufacturing costs are absorbed by the units produced.
Which method gives the most accurate results when allocating of multiple service departments’ costs to operating departments?
Reciprocal method gives the most accurate results when allocating of multiple service departments’ costs to operating departments. The power of reciprocal method over other methods (direct method, step-down method) lies in its considering the mutual services provided among all service departments which means the costs of service departments are allocated to each service department (except the service provider) besides operating departments.
How are overhead costs allocated?
In the past, overhead costs were typically allocated based on factors such as total direct labor hours, total direct labor costs, or total machine hours. This allocation process, often called the traditional allocation method, works most effectively when direct labor is a dominant component in production. However, many industries have evolved, primarily due to changes in technology, and their production processes have become more complicated, with more steps or components. Many of these industries have significantly reduced their use of direct labor and replaced it with technology, such as robotics or other machinery. For example, a mobile phone production facility in China replaced 90 percent of its workforce with robots. 1
How is factory overhead allocated?
Traditional allocation involves the allocation of factory overhead to products based on the volume of production resources consumed, such as the amount of direct labor hours consumed, direct labor cost, or machine hours used . In order to perform the traditional method, it is also important to understand each of the involved cost components: direct materials, direct labor, and manufacturing overhead. Direct materials and direct labor are cost categories that are relatively easy to trace to a product. Direct material comprises the supplies used in manufacturing that can be traced directly to the product. Direct labor is the work used in manufacturing that can be directly traced to the product. Although the processes for tracing the costs differ, both job order costing and process costing trace the material and labor through materials requisition requests and time cards or electronic mechanisms for measuring labor input. Job order costing traces the costs directly to the product, and process costing traces the costs to the manufacturing department.
How is predetermined overhead calculated?
A predetermined overhead rate is calculated at the start of the accounting period by dividing the estimated manufacturing overhead by the estimated activity base. The predetermined overhead rate is then applied to production to facilitate determining a standard cost for a product. This estimated overhead rate will allow a company to determine a cost for the product without having to wait, possibly several months, until all of the actual overhead costs are determined, and to help with issues such as seasonal production or variable overhead costs, such as utilities.
What is manufacturing overhead?
The more challenging product component to track is manufacturing overhead. Overhead consists of indirect materials, indirect labor, and other costs closely associated with the manufacturing process but not tied to a specific product. Examples of other overhead costs include such items as depreciation on the factory machinery and insurance on the factory building. Indirect material comprises the supplies used in production that cannot be traced to an individual product, and indirect labor is the work done by employees not directly involved in the manufacturing process, such as the supervisors’ salaries or the maintenance staff’s wages. Because these costs cannot be traced directly to the product like direct costs are, they have to be allocated among all of the products produced and added, or applied, to the production and product cost.
What are roommates' points about allocating limited resources?
Both roommates make valid points about allocating limited resources. Ultimately, each must decide which method to use to allocate time, and they can make that decision based on their own analyses. Similarly, businesses and other organizations must create an allocation system for assigning limited resources, such as overhead. Whereas Kamil and Barry are discussing the allocation of hours, the issue of allocating costs raises similar questions. For example, for a manufacturer allocating maintenance costs, which are an overhead cost, is it better to allocate to each production department equally by the number of machines that need to be maintained or by the square footage of space that needs to be maintained?
Why does manufacturing technology become less expensive and more efficient?
As manufacturing technology becomes less expensive and more efficient, the mix between overhead and labor changes so that tasks are more computerized tasks and involve less direct labor; the traditional use of direct labor hours or direct labor dollars changes accordingly.
What is activity based costing?
Activity-based costing is an accounting method that recognizes the relationship between product costs and a production activity, such as the number of hours of engineering or design activity, the costs of the set up or preparation for the production of different products, or the costs of packaging different products after the production process is completed. Overhead costs are then allocated to production according to the use of that activity, such as the number of machine setups needed. In contrast, the traditional allocation method commonly uses cost drivers, such as direct labor or machine hours, as the single activity.
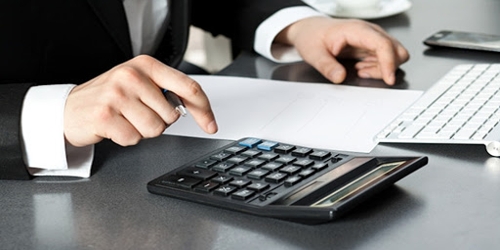