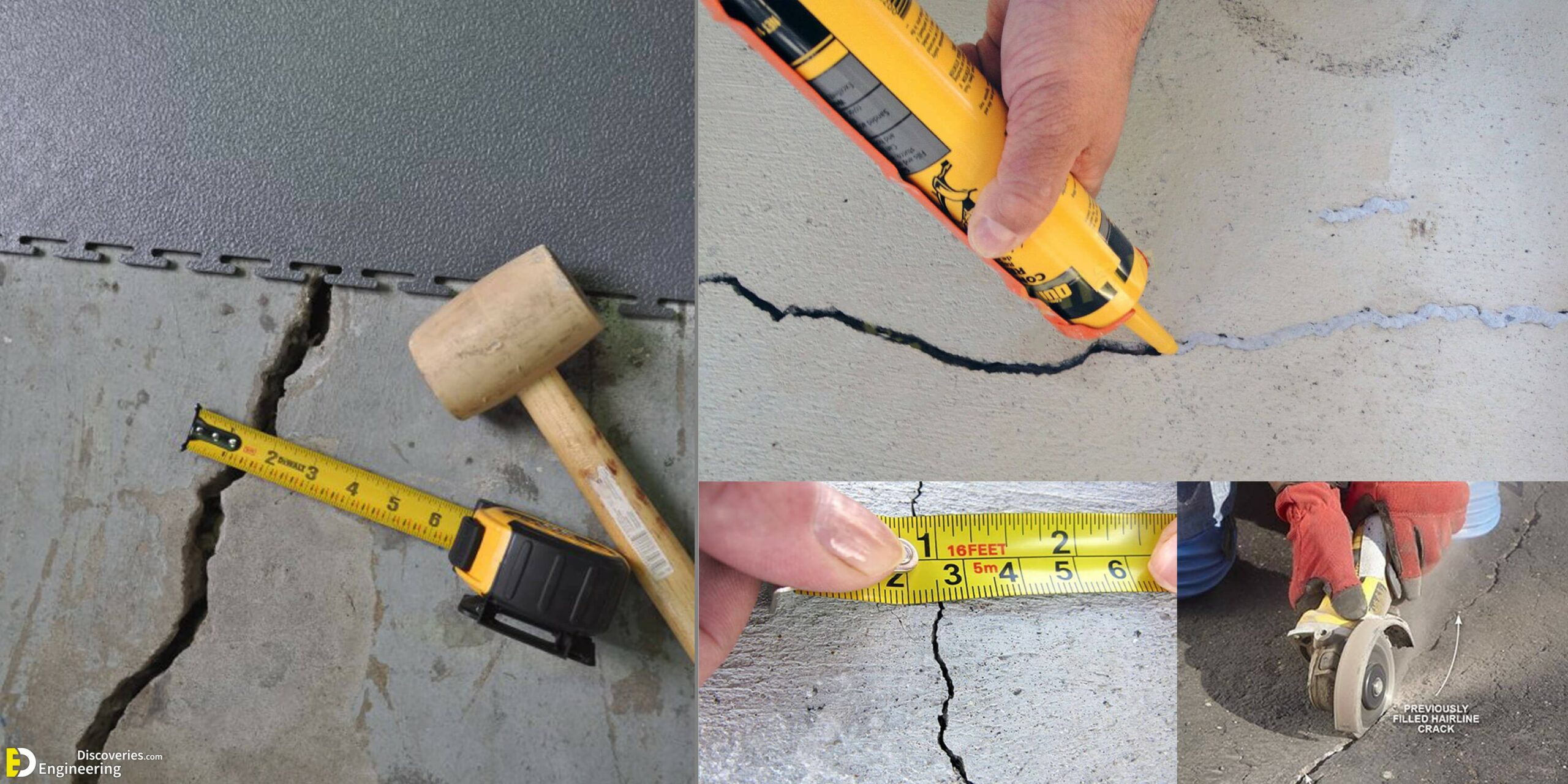
The external or environmental agencies causing the deterioration of concrete includes:
- Weathering.
- Attack by natural or industrial liquids and gases.
- Acids in the form of water solution.
- Fertilizers, insecticides and certain organic compounds.
- Attack by biological agents.
What is the leading cause of deterioration in concrete?
leading cause of deterioration in concrete. When steel corrodes, the resulting rust occupies a greater volume than the steel. This expan- sion creates tensile stresses in the concrete, which can eventually cause cracking, delamination, and spalling (Figs. 1 and 2).
What is corrosion of concrete?
Corrosion of reinforcing steel and other embedded metals is the leading cause of deterioration in concrete. When steel corrodes, the resulting rust occupies a greater volume than the steel. This expan- sion creates tensile stresses in the concrete, which can eventually cause cracking, delamination, and spalling (Figs. 1 and 2).
How does high temperature affect concrete?
The high temperature causes two principal kinds of damage in concrete: deterioration in mechanical properties of concrete and spalling of concrete ( William et al., 2013 ). Deterioration of mechanical properties of concrete due to thermal loading involves, in turn, three material factors ( Naus, 2010 ):
How does radiation damage concrete?
At the structural level, the thermal gradient due to the heat of radiation results in thermal stress, which may be high enough to create damage in concrete.

What is the most common cause of concrete deterioration?
Corrosion of reinforcing steel and other embedded metals is the leading cause of deterioration in concrete. When steel corrodes, the resulting rust occupies a greater volume than the steel. This expan- sion creates tensile stresses in the concrete, which can eventually cause cracking, delamination, and spalling (Figs.
What are the causes of deterioration of concrete explain any three?
a) Concrete can deteriorate when it is exposed to aggressive environment such as sea water or salt spray, raw sewage, acids, groundwater, acid rain, condensation, etc. This could lead to various defects such as staining, corrosion of reinforcement, cracking and spalling.
What are the causes of deterioration?
Physically - induced deterioration is caused by freeze–thaw loads, non-uniform volume changes, temperature gradients, abrasion, erosion, or cavitation. Chemically-induced deterioration consists of carbonation, corrosion of steel reinforcement, sulfate and acid attacks, or alkali–aggregate reactions.
What are the causes of distress and deterioration of concrete?
Common causes of concrete distress and deterioration, including Accidental loadings, Chemical reactions, Construction errors, Corrosion of embedded metals, Design errors, Erosion, Freezing and thawing, Settlement and movement, Shrinkage, Temperature chang.
What is concrete deterioration called?
Erosion is the deterioration of concrete surface as a result of particles in moving water scrubbing the surface. When concrete surface is exposed to the water-borne sand and gravel, the surface gets deteriorated by particles scrubbing against the surfaces. Flowing ice particles can also cause the problem.
What are types of deterioration?
Different types of Deterioration in Concrete StructuresDifferent types of Deterioration in Concrete Structures.Corrosion of Embedded Metals in concrete.Freeze thaw deterioration in concrete.Chemical attack in concrete.Alkali-Aggregate Reactivity in concrete.Abrasion Erosion in concrete.Plastic Shrinkage in concrete.More items...•
What causes structural deterioration?
One of the causes for this is weathering and ageing effect or inadequate maintenance and care. However, many poorly designed and / or constructed buildings are also found to be in a very bad structural and general health condition needing major structural repairs.
What are the signs of deterioration?
Rising respiratory rate often early sign of deterioration. accessory muscles, increased work of breathing, able to speak?, exhaustion, colour of patient. Position of resident is important.
How does concrete get weathered?
Weathering is the effect of pollution and natural forces, such as frost, rain and sunlight, on a structure. With concrete, the main weathering problem is unexpected variations in the visual appearance of the structure. Dust in the atmosphere will be deposited on the facade.
How do you stop concrete from deteriorating?
Topical sealants can be applied to further prevent concrete deterioration. Creto TopSeal is a hydrophobic, natural looking, topical sealant that is VOC free like all of the other Creto products. This combination of sealants can greatly reduce concrete deterioration and keep repair costs down on your property.
How do you fix deteriorated concrete?
1:205:16How To Repair Concrete | Pro Tips For Repairing Concrete - YouTubeYouTubeStart of suggested clipEnd of suggested clipAny loose debris from the damaged area with a wire brush and broom then you can use a caulk gunMoreAny loose debris from the damaged area with a wire brush and broom then you can use a caulk gun loaded with a masonry crack filler to fill the crack.
What are the factors affecting the durability of concrete?
Factors Affecting Durability of ConcreteCement Content.Aggregate Quality.Water Quality.Concrete Compaction.Curing Period.Permeability.Moisture.Temperature.More items...•
What are the causes of deterioration of materials?
In general, the main deterioration mechanisms include: (1) erosion, (2) volume change of the material and the volume changes of the material in pores, (3) dissolution of a material and the associated chemical changes, and (4) biological processes.
What are the 4 types of structural failure?
Compressive, tensile, bending and buckling are the basic types of structural failure for construction elements.
How do you keep concrete from deteriorating?
Topical sealants can be applied to further prevent concrete deterioration. Creto TopSeal is a hydrophobic, natural looking, topical sealant that is VOC free like all of the other Creto products. This combination of sealants can greatly reduce concrete deterioration and keep repair costs down on your property.
What is deterioration in building?
For silicate. building materials such as concrete, plasters, mortars, we use the term deterioration. Deterioration of concrete is a gradual and irreversible permanent erosion of its. basic properties leading to its disintegration. The study of concrete and building.
Why is my concrete cracking?
Cracking can be caused by inadequate substrate or subbase preparation, high water-to-cement ratio, improper curing methods, poor concrete consolidation, timing of control-joint installation and many other placement factors.
What happens when concrete does not fully consolidate around steel?
If the concrete does not fully consolidate around the reinforcing steel, design capacity may not be reached, and cracking can result. Concrete expands and contracts with temperature changes. When these contraction forces exceed the tensile strength of the concrete, cracking can occur.
What is the purpose of rebar in concrete?
Reinforcing steel (rebar) is used to increase the tensile strength of concrete. When tensile forces acting upon a concrete element exceed its tensile strength, a crack may occur.
What are the effects of corrosion on steel?
Effect: Reduction in strength andincreased potential for water intrusion, corrosion of reinforcing steel and reduced abrasion resistance.
What is the best way to prevent metal corrosion?
Using concrete with a low water-to-cement ratio and proper rebar placement with adequate concrete cover are common measures used to prevent metal corrosion.
What are the factors that affect RPS?
When planning an RPS strategy for deteriorated concrete, one must consider and address the following in-service factors: 1 Environmental conditions 2 Chemical exposure 3 Exposure to water and mobile debris 4 Concrete properties (strength, type, aggregate, etc.)
What causes cement to lose its aggregate?
Causes: Exposure to acid rain, de-icing salts, in-service chemicals and naturally occurring sulfates in soils and ground water dissolve the cement matrix which results in aggregate loss.
What is the most damaging type of sulfate attack?
Sulfate attack is one of the most damaging causes of concrete deterioration, causing either softening and decay of the concrete matrix (the ‘acid’ type of sulfate attack) or expansive cracking and other disruption associated with the formation of ettringite (calcium sulfoaluminate hydrate) and other reaction products within the hardened concrete. Good summaries of sulfate attack are given by Figg308 and Eglinton; 309 more extensive treatments may be found in Swenson 310 and an American Concrete Institute publication. 311
What is the cause of expansion of cement and mortar made with serpentinite wadi aggregates?
French and Crammond 314 identified the cause of expansion of concrete and mortar made with serpentinite wadi aggregates from the United Arab Emirates as being internal sulfate attack involving contamination of the aggregate by up to 5 per cent coarsely crystalline gypsum ( Figure 16.31 ), and later work by Crammond 84 found that up to 2.5 per cent coarsely crystalline gypsum (or about 6 per cent total sulfate by weight of cement) could be tolerated for Portland cement concrete ( Figure 16.32 ).
How to diagnose concrete damage?
Diagnosis of any concrete deterioration or damage must start on site, preferably involving the materials scientist who will later conduct the laboratory investigation. Site inspection will include the identification of any evidence of deformation or displacement of concrete units and the recording of crack dispositions, patterns and intensities. It is important to relate cracking patterns variously to structural geometry and/or design, apparent concreting sequence, localized detailing (especially where cracking may be coincident with water leakage) and both environmental and in-service conditions. In complicated cases, it is helpful to undertake crack mapping of the main structural units. Superficial cracking patterns can often be reminiscent of ASR, but it is important to be aware that reliable diagnosis can never be adequately based upon the appearance of surface cracking alone. Other features that might be significant to ASR diagnosis include surface discolorations, exudations and sometimes pop-outs. Techniques for identifying gel on site have been developed, but investigators should note that the presence of gel can only confirm that some ASR has probably occurred, not that any damage has resulted. In some cases and when feasible, it is desirable to monitor affected structures over a period, variously using comparative visual and strain measurement techniques, to establish whether any movement is occurring outside the normal range.
Can thaumasite cause concrete to decay?
In its worst case, thaumasite formation can cause concrete to decay into a mush-like form losing its strength. It occurs as needle-like crystals, similar in appearance to ettringite. Analytical methods to determine sulfate contents of concrete are unable to distinguish between the two different forms of attack, ettringite and thaumasite. Differentiation between these two forms requires microscopical, X-ray diffraction or spectroscopic methods.
How does heat affect concrete?
The heat of radiation affects properties of concrete at two levels: the structural level and the microstructural level. At the structural level, the thermal gradient due to the heat of radiation results in thermal stress, which may be high enough to create damage in concrete. At the microstructural level, the mismatch of thermal strains in cement paste and in aggregate responding to the heat of radiation may cause large stress at the interface between the aggregate and cement paste, which may cause microcracking in cement paste ( William et al., 2013 ).
What causes cracks in concrete?
Freeze and thaw cycles are a major cause of concrete deterioration in the continental type of climatic environment, especially when the surface of the material is not protected with a watertight cover. These cycles can result either in surface scaling and spalling, or in material volumic expansion which usually induces a network of cracks. Both phenomena can occur simultaneously (Balayssac, 2005 ). On road pavements, the use of de-icing salts can create a thermal shock when the ice melts, and this has consequences on cracking. This is commonly a top-down distress with fractures running parallel with the pavement surface, decreasing in number with depth.
How to reduce electrical conductivity of concrete patch?
The electrical conductivity between the patching material and the parent concrete can be reduced by reducing the conductivity of the patching material. The inclusion of silica fume or a latex modifier will reduce the conductivity of the patching material. The inclusion of a corrosion-inhibiting admixture has also shown promise in reducing the impact of the anodic ring. The use of an epoxy or polyester mortar/concrete can eliminate electrical conductivity between the patch and the parent concrete. Another means by which the anodic ring has been eliminated has been with the introduction of a sacrificial anode attached to the reinforcing steel within the patched cavity.
Where Can You Turn to Prevent and Repair Concrete Deterioration?
Seeking solutions for your industrial or commercial concrete deterioration problem in Maryland or Northern Virginia?
What causes concrete to deteriorate?
Chlorides are one of the most common causes of concrete deterioration. They can be found in:
What happens when a load exceeds the limit?
When a load exceeds the limit and the steel structure starts to bend, you can expect concrete cracks and resulting damages.
How to contact Concrete Deterioration?
If you’d like to discuss concrete deterioration with the experts, call (301) 261-4933 or click here and fill in the form and a specialist will contact you shortly.
What is the reaction of calcium hydroxide in concrete?
The reaction is capable of decreasing the pH to an undesirable level , exposing the steel for corrosion.
Can carbon dioxide cause concrete to deteriorate?
Carbon Dioxide: Believe it or not, carbon dioxide in the air we breathe can cause the deterioration of. concrete. It can make its way through the porous concrete and cause real problems. The steel matrix embedded in reinforced concrete actually depends on the alkalinity of the concrete itself for protection from corrosion.
Why does the outer layer of a surface expand?
When the surface is exposed to the extreme heat of fire or lightning, the outer layer expands due to the temperature increase. The inner layer remains at a much cooler temperature and the outer layer can break away if the difference between temperatures breaks threshold.
What Is Rapid Set Concrete?from antoun.com.au
It’s a durable, fast-curing, and strong product that sets in as little as 15 minutes. It can also be retarded for as long as 45 minutes, if the project needs more working time.
What is UHPC cement?from researchgate.net
Ultra-high-performance concrete (UHPC) incorporates a relatively large volume fraction of very dense cementitious binder with microscale fibers. The dense binder in UHPC can effectively interact with nano- and microscale reinforcement, which offers the promise to overcome the brittleness of UHPC. Nanoscale reinforcement can act synergistically with microscale fibers by providing reinforcing action of a finer scale, and also by improving the bond and pullout behavior of microscale fibers. Carbon nanofiber (CNF) and polyvinyl alcohol (PVA) fiber were used as nano- and microscale reinforcement, respectively, in UHPC. An optimization experimental program was conducted in order to identify the optimum dosages of CNF and PVA fiber for realizing balanced gains in flexural strength, energy absorption capacity, ductility, impact resistance, abrasion resistance, and compressive strength of UHPC without compromising the fresh mix workability. Experimental results indicated that significant and balanced gains in the UHPC performance characteristics could be realized when a relatively low volume fraction of CNF (0.047 vol.% of concrete) is used in combination with a moderate volume fraction of PVA fibers (0.37 vol.% of concrete).
What is RCA in concrete?from researchgate.net
Reutilizing industrial by-products and recycled concrete aggregates (RCA) to replace cement and natural aggregates (NA) in concrete is becoming increasingly important for sustainable development. Yet, experimental evidence is needed prior to the widespread use of this sustainable concrete by the construction industry. This study examines the performance of alkali-activated slag concrete made with RCA and reinforced with steel fibers. Natural coarse aggregates were replaced with RCA. Steel fibers were added to mixes incorporating RCA at different volume fractions. Desert dune sand was used as fine aggregate. The mechanical and durability properties of plain and steel fiber-reinforced concrete made with RCA were experimentally examined. The results showed that the compressive strength did not decrease in plain concrete mixes with 30 and 70% RCA replacement. However, full replacement of NA with RCA resulted in a 20% reduction in the compressive strength of the plain mix. In fact, 100% RCA mixes could only be produced with compressive strength comparable to that of an NA-based control mix in conjunction with 2% steel fiber, by volume. In turn, at least 1% steel fiber, by volume, was required to maintain comparable splitting tensile strength. Furthermore, RCA replacement led to higher water absorption and sorptivity and lower bulk resistivity, ultrasonic pulse velocity, and abrasion resistance. Steel fiber incorporation in RCA-based mixes densified the concrete and improved its resistance to abrasion, water permeation, and transport, thereby enhancing its mechanical properties to exceed that of the NA-based counterpart. The hardened properties were correlated to 28-day cylinder compressive strength through analytical regression models.
What is abrasion resistance?from theconstructor.org
Abrasion resistance is a critical property for concrete structures subjected to abrasion deterioration, such as industry floors, pavement, or hydraulic structures. Studies on abrasion resistance of normal concrete have been well established, whereas there is limited research on the abrasion behavior of ultra-high performance concrete (UHPC). This study developed lower-cement UHPC incorporating basalt and calcined bauxite coarse aggregate, and a normal concrete was prepared for comparison. The abrasion resistance was evaluated based on the mass loss and abraded depth of concrete. A nanoindentation test was also conducted to investigate the underlying mechanisms that determine the macro-behavior. The UHPC with calcined bauxite aggregate showed 28% higher compressive strength than UHPC with basalt aggregate due to the rough surface texture and super high stiffness of the calcined bauxite. The evaluated UHPCs with coarse aggregate show good mechanical strength as well as excellent abrasion resistance than normal concrete that their abraded depth or mass loss was only approximately one-third of that of the normal concrete. The high strength and densified paste matrix of UHPC has a relatively bigger effect on the abrasion resistance of UHPC than the effect of coarse aggregate type, ITZ properties, or steel fiber which contribute more to the strength of UHPC.
What is the most damaging type of sulfate attack?from sciencedirect.com
Sulfate attack is one of the most damaging causes of concrete deterioration, causing either softening and decay of the concrete matrix (the ‘acid’ type of sulfate attack) or expansive cracking and other disruption associated with the formation of ettringite (calcium sulfoaluminate hydrate) and other reaction products within the hardened concrete. Good summaries of sulfate attack are given by Figg308 and Eglinton; 309 more extensive treatments may be found in Swenson 310 and an American Concrete Institute publication. 311
What is the abrasive charge of concrete?from theconstructor.org
An abrasive charge is impinged on the surface of the concrete cubes. As a result, the concrete surface of the cubes abrades, and the consequent loss in mass of the cubes is referred to as concrete abrasion loss.
What is RMSCC?from researchgate.net
In the studies carried out until today, rubber-modified self-compacting concretes (RMSCC) had been manufactured by replacing the aggregates of the waste vehicle tires (WVT) in the grain size distribution and particles that have different workability, different mechanical, and physical properties. However, variation of the carrying capacity of the RMSCC elements produced with different slenderness ratio h/b ratio under axial load had not been researched in previous studies. Within the scope of this study, the change in physical and mechanical properties of RMSCC elements produced by using different h/b ratios had been examined both experimentally and theoretically. Since the natural sand and WVT aggregate used in the production of concrete and their grain sizes are in the same range, WVT aggregate has been replaced by natural sand in 4 different proportions. These ratios were used as 5%, 10%, 15% and 20% of the natural sand volume, respectively. Slenderness ratios, h/b ratios were 1.0, 1.5, 2.0, 2.5, 3.0 and 3.5, and experimental and theoretical investigations had been performed for 90 samples in total. The linear regression models of the obtained results had been analyzed and the equations with the h/b ratios according to these models had been produced. The results of the obtained equations and the results of experimental axial pressure had been compared. In addition to the amount of WVT aggregate used and the increase in the ratio of h/b, the compressive strength losses had caused by different rates on the samples. The effect of the WVT aggregate ratio on the compressive strength had become more significant with the increase in use rate. Besides, regression analyzes had been performed to determine the effect of h/b ratio on the compressive strength. In conclusion, regression R2 (coefficient of determination) values that belong to equations obtained had been found over 0.95.
