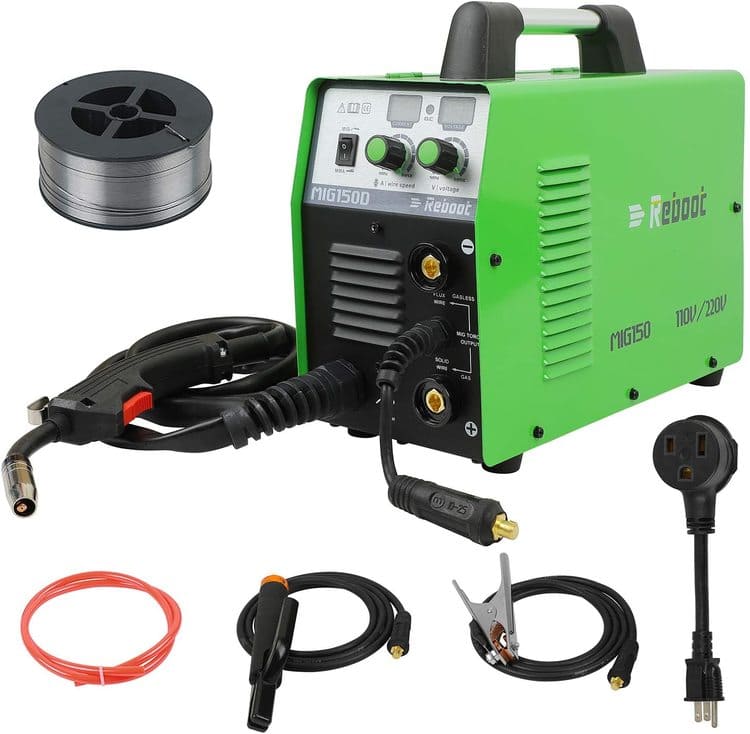
What are the dangers of being a welder?
Underwater Welding Risks
- Electric Shock. One of the biggest threats to underwater welders is electrocution. ...
- Explosion. The combination of hydrogen and oxygen can result in the formation of numerous gas pockets. ...
- Decompression sickness. ...
- Drowning. ...
- Hypothermia. ...
- Hearing Impairment. ...
- Marine Life. ...
How to weld steel with a flux cored welder?
- Start with a 3/4-inch wire stickout. ...
- Use a pull or drag technique when flux core welding.
- To achieve this, you’ll need to remember that you should always be moving away from your completed weld.
- Point the welding gun so it’s facing the weld puddle, and start dragging it away from the metal. ...
What is the best flux welding wire?
Top Pick: INETUB BA71TGS Carbon Steel Gasless Flux Cored Welding Wire
- Gasless flux cored welding wire AWS E71T-GS, Smooth arc action, High feedability, Easy to weld
- Shielding gas is not required, All positions, Single and multi pass welding
- Low spatter, Full slag coverage, Easy slag removal, Porosity free, Good bead appearance
Which flux is used in aluminium welding?
- Forney 37025 Aluminum Welding Flux
- Harris SCAF4 Stay Clean Alum Soldering Flux
- Hot Max 24184 Aluminum Brazing Flux for Welding

What are flux welders good for?
Flux core welding is used to weld thicker metals. It differs from flux core soldering and is ideal for heavy-duty or industrial applications since the finished bond is much more secure. This is essential when working on things like machine parts.
What can you weld with a flux welder?
Flux core can be used with a variety of metals, including stainless steel and some nickel and steel alloys.
What is the difference between an arc welder and a flux welder?
Flux welding does not use shielding gas, so it can be used outdoors and in windy conditions. It can also be used on a variety of metal alloys. The filler material is more expensive, compared to other types of arc welding. It also generates more fumes and smoke than other types of arc welding.
Is a flux welder the same as a Mig welder?
Similar to MIG, flux-cored arc welding (FCAW)* is a wire-feed process but differs in that self-shielded FCAW does not require shielding gas. Instead, flux-cored wire shields the arc from contamination. This is a simple and efficient approach, especially when welding outdoors, in windy conditions or on dirty materials.
What is a disadvantage of flux core welding?
FCAW Disadvantages A high level of noxious fumes which must be ventilated. Higher electrode wire cost compared to solid electrode wires. More costly equipment than many other welding processes. Less portable equipment than SMAW or GTAW.
Can you cut metal with a flux welder?
Welders are designed to join two pieces of metal, but in a pinch, they can be used to cut metal if you know how to properly set up your rig. The result is certainly not a clean cut, but if that is not a concern, or if you don't have the equipment needed to cut it properly, a welder is capable of doing the job.
What type of welder is best for a beginner?
MIG WeldingMIG Welding (Beginner) MIG welders are among the best type for beginners, as they're designed with a wire welding electrode on a spool that is fed at a pre-selected speed through a welding gun. As a semi-automatic or automatic process, gas metal arc welding (GMAW or MIG), is the easiest to learn.
What is better flux welder or stick welder?
The flux-cored wire has less flux material and more metal than a stick electrode and provides a deposition rate of 85%. Stick welding has further losses in the form of leftover stubs that lower the deposition efficiency to 60%.
What is the easiest welding to learn?
MIG welding (metal inert gas welding) is often considered the easiest type of welding for a beginner to learn. MIG welders have a wire welding electrode on a spool which is then fed through a welding gun at a preselected speed.
Do you push or pull when flux core welding?
With flux-cored welding, you should always use a drag (pull) technique, in which the tip of the welding gun is being pointed back at the weld pool and dragged away from the completed weld. An easy rule of thumb for remembering whether to use a push or drag (backhand) technique is: “If there's slag, you drag.”
Is flux stronger than MIG?
Is flux core as strong as MIG? Both MIG and flux-cored wires make very similar strength welds, and if the joint is properly welded, there is not a significant difference in strength between the processes.
Can you use regular wire in a flux core welder?
0:1711:04Can A Flux Core Only Machine Weld With Solid Wire - YouTubeYouTubeStart of suggested clipEnd of suggested clipI yes you do need to change polarity.MoreI yes you do need to change polarity.
Is flux welding strong?
They allow for a high deposition rate. They work well outdoors and in windy conditions. With the right filler materials, these electrodes can make FCAW an “all-position” process. Typically, flux-cored wires create clean, strong welds.
What can a 125 amp flux welder weld?
The Flux 125 welder can weld mild steel from 18 gauge up to 3/16in. thick which makes it ideal for jobs around the yard, shop or house.
Is flux core welding stronger than MIG?
Is flux core as strong as MIG? Both MIG and flux-cored wires make very similar strength welds, and if the joint is properly welded, there is not a significant difference in strength between the processes.
Can you weld aluminum with a flux core?
The short answer is no. You can't use steel based flux core wire in your FCAW welder to weld Aluminum. It just won't work.
How does a flux core welder work?
Most Flux core welders have thermal sensors that will automatically switch the welder off if the duty cycle is exceeded or the welder overheats.
What is wire feed in flux core?
A wire feed parts of a Flux Core welder feeds the wire through from the spool out to a hose or cable.
How many volts does a welder need?
A welder capable of welding dual shielded flux core wire will be to the high end of most home workshop welders, demanding power input of 220 volts as a minimum, which is why this type of wire is often used in fabrication shops.
What type of wire does a welder use?
There are other types of welders that use an electrical arc – TIG, MIG and Stick welders. Only Stick welders and Flux core welders use tubular welding wire – a wire that has a flux core and that flux core produces slag that covers the weld pool.
What is the arc of a welding gun?
This arc is what melts the base metal and the flux core welding wire and creates the weld pool – a molten pool of metal.
What is flux core welding?
It’s either an automatic or semi automatic welding machine that welds using electricity to produce a powerful electric arc. Inside the flux core welder is a spool of wire containing flux core welding wire. The wire in flux core welding is special as it is made like a tube.
Where is the heat output on a flux core welder?
On the front of the flux core welder are dials or buttons where the volts or amperage is set. This is where the welding output; the heat output of the welder is set according to the thickness or gauge of metal welded.
How Does Flux-Cored Arc Welding Work?
Flux-cored welding uses the same equipment as MIG welding. This includes welder/inverter, wire feeder, semi-automatic welding gun, and ground clamp. Since the power source is based on CV (constant voltage) which can be adjusted, this means that the arc length will stay constant throughout welding. The overall current can be changed by increasing or decreasing the wire-feed speed (WFS).
What is FCAW wire?
The most common FCAW wires are geared toward welding mild steel. But others are high in nickel and are designed for welding special alloys. All of these wires come in a variety of sizes as well. In a fabrication setting, the selection will usually depend upon the WPS (Welding Procedure Specification).
What is inner shield?
Innershield is Lincoln Electric’s brand name for what we know as self-shielded FCAW (FCAW-S). It uses DCEN (Direct Current Electrode Negative) as its polarity. This means that about ⅔ of the heat from the arc is concentrated on the workpiece while ⅓ of the heat is burning the electrode. Unlike Dual Shield, the wire for Self-Shielded FCAW does not require a shielding gas. It is intended to be used without shielding gas. Between these two wires, this is the preferred method for those who work outdoors. Ironworkers and people who do a lot of mobile welding repairs tend to prefer Self-Shielded.
What type of wire is used for welding mobile?
Other Variables. These two wires that are listed are simply the two largest categories for Flux-Cored welding wire. The most common FCAW wires are geared toward welding mild steel.
Why is FCAW used?
It’s used by fabricators and construction workers alike. The primary reason that it is used so widely is its efficiency. The deposition rate can be 10 times higher than Stick welding. Since the filler metal runs off of a wire-feeder, this also means that you will not have to make as many stops and starts. With SMAW, 14-inch rod electrodes will not get you as many passes as FCAW.
How to simulate welding in the outdoors?
This will provide you with more gas coverage to counteract the wind. Secondly, utilize welding screens, fire blankets, cardboard, or any sort of barrier that you can find to simulate welding ‘indoors,’ outdoors. Do note that turning your shielding gas up too high on the regulator attached to the gas cylinder, can cause strain and damage over time to the regulator.
Why is FCAW-G called dual shield welding?
FCAW-G is called Dual Shield welding because it has two complementary ways that the weld is ‘shielded’ during welding.
Why is flux important for welding?
The flux of the welding wire increases the durability and the longevity of the weld. It cools down really slow compared to the other welding methods. It can do well in the case of manufacturing because of its great portability. The flux makes a shield on the surface and makes a strong hold. This is why there is no need for a gas tank for ...
What wire to use for flux welding?
If you are doing a mild steel welding, then it will be wise to use the E71T-11 Flux core wire. It is a versatile wire and comes in a wide range of shapes and sizes. It also provides great performance on both thick and thin materials. We even have listed the best wires for flux-welding for you.
What is the best way to clean rusty metal?
A wire brush shall be used to clean the rusty metal surface. Be sure to clean the surface of the base metal where the ground clamp will be attached to. If the clamp is less contacted with the surface ground, then it might lead to a welding of poor quality.
What is the best diameter for a welder?
It would be better to stick with 0.30 inches. This is a diameter that is suitable for general purposes and versatile as well. If you are using a high temperature to weld a thick metal, then go for .35 inches. For your information, the highest diameter range is 0.45 inches for powerful welder ranges.
What is the best way to prepare for welding?
Preparation will help you to avoid unwanted fires and injuries. The best preparation is to prepare your workspace by removing the things which might catch fire. The second suggestion is not to do welding in enclosed and low ventilation areas.
What are the most important parts in flux core welding?
The cables are the most important parts in flux-core-welding.
Is flux core welding more tolerant of weather?
I must mention here that flux core welding is more tolerant to weather contamination than MIG welding. So, to ensure less contamination of the welded surfaces it is necessary to prepare the metal surface first. A wire brush shall be used to clean the rusty metal surface.
What is the stickout of a flux core?
Stickout is the length of unmelted electrode extending from the tip of the contact tube, and it does not include arc length . Generally, flux-cored welding requires a stickout of around 3/4 inch, which is about twice the recommended stickout for MIG welding.
What is flux core welding?
Flux-cored welding does produce a slag that sits on top of the finished weld and must be chipped off, similar to stick welding, and it also tends to produce welds that aren’t as visually attractive as MIG welds.
Why is flux used in MIG welding?
Because the flux creates the shielding gas in self-shielded flux-cored welding, this process does not encounter the weld problems that can occur when a strong wind blows the shielding gas away when MIG welding outside. The flux contained in the electrode also allows the process to be more forgiving of base metal that is somewhat rusty, dirty or otherwise contaminated.
What is self shielded flux core welding?
Self-shielded flux-cored welding is a wire welding process in which a continuous hollow wire electrode is fed through the welding gun into the weld joint. Self-shielded flux-cored welding differs from MIG welding in that it doesn’t require an external shielding gas, such as carbon dioxide or argon, to protect the weld pool from contamination.
Why does the welding gun work angle have to be dropped?
Because of the effects of gravity, the gun work angle must be dropped slightly by 0 to 15 degrees so that the welding gun is pointing upward toward the top piece of metal. Without changing the work angle, the filler metal may sag or rollover on the bottom side of the weld joint. The travel angle generally remains the same as for a weld joint in the flat position.
What is the best way to clean base metal?
A metal brush or grinder work well for cleaning the base metals. Also, be sure to clean the portion of the base metal where the ground clamp will be attached. Poor contact with the ground clamp will create resistance in the welding circuit and could result in poor weld quality.
What is E71T-11?
For general purpose mild steel applications, a flux-cored wire with the designation E71T-11 can be used in any position, is available in a wide range of sizes and provides excellent welding characteristics for both thin and thicker material. Hobart® Filler Metals offers such a wire under the name Fabshield® 21B (E71T-11).
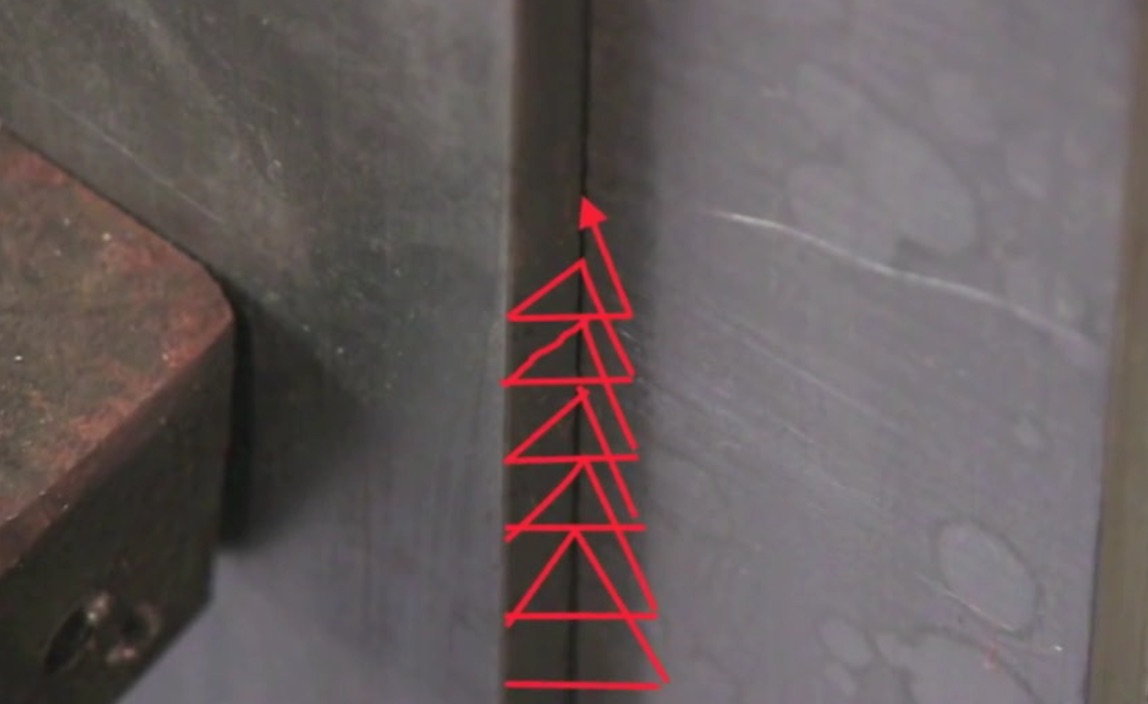