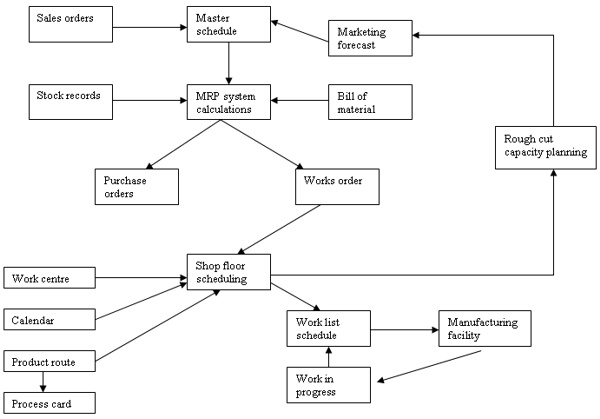
What is the difference between MRP versus ERP?
What Are The Differences Between MRP I, MRP II & ERP?
- MRP I first came into prominence in the 1970s. It is a business software designed to improve accuracy and efficiency in basic processes like production scheduling and inventory management.
- By the time the 1980s rolled around, MRP II was being utilized. ...
- ERP makes core business processes run smoothly. ...
How does MRP help your manufacturing business?
The modern-day MRP solutions can help businesses scale to new heights by tapping ... control Proper inventory control is the backbone of a manufacturing unit; thus, it is important to manage your inventory from raw materials to finished goods.
What is the function of MRP?
The MRP process can be broken down into four basic steps:
- Estimating demand and the materials required to meet it. The initial step of the MRP process is determining customer demand and the requirements to meet it. ...
- Check demand against inventory and allocate resources. This step involves checking demand against what you already have in inventory. ...
- Production scheduling. ...
- Monitor the process. ...
What does MRP mean on products?
What does MRP mean on products? Material requirements planning (MRP) is a system for calculating the materials and components needed to manufacture a product. It consists of three primary steps: taking inventory of the materials and components on hand, identifying which additional ones are needed and then scheduling their production or purchase.
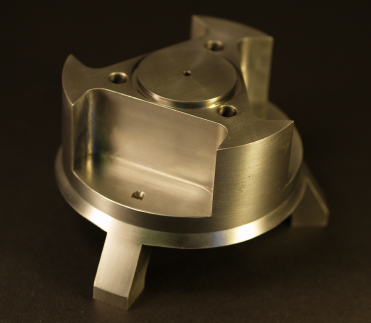
What does ERP and MRP stand for?
A complete guide outlining the differences between ERP (Enterprise Resource Planning) and MRP (Material Requirements Planning) systems to help you understand what solution best suits your business.
What does MRP stand for in management?
Material requirements planning (MRP) is a computer-based inventory management system designed to improve productivity for businesses. Companies use material requirements-planning systems to estimate quantities of raw materials and schedule their deliveries.
What do you mean by MRP and MFG?
Manufacturing Resource Planning (MRP II) is an integrated information system used by businesses. Manufacturing Resource Planning (MRP II) evolved from early Materials Requirement Planning (MRP) systems by including the integration of additional data, such as employee and financial needs.
How is MRP used in manufacturing?
MRP is a system that allows businesses – primarily manufacturers, but not exclusively so – to schedule production requirements, control inventory and plan deliveries of raw materials. It uses a production plan for the finished goods to schedule your requirements for the materials and components you need.
What is the difference between ERP & MRP?
The primary difference between ERP and MRP is that ERP systems help to plan and automate a variety of back-office business functions, whereas MRP systems focus on materials management. ERP directly touches accounting, manufacturing, supply chain, customer management, quality, processes and planning.
How does an MRP system work?
6 days agoAn MRP system accelerates the manufacturing production process by determining what raw materials, components and subassemblies are needed, and when to assemble the finished goods, based on demand and bill of materials (BOM).
How MRP is calculated?
Maximum Retail Price Calculation Formula= Manufacturing Cost + Packaging/presentation Cost + Profit Margin + CnF margin + Stockist Margin + Retailer Margin + GST + Transportation + Marketing/advertisement expenses + other expenses etc.
What is MRP in apparel industry?
This system is web-based, applying the MRP (Material Requirement Planning) method to develop raw material ordering planning systems, case studies at garment companies, using PHP programming and FIREBIRD databases.
What is the relationship between ERP and MRP?
MRPs are focused specifically on manufacturing processes, while ERPs provide a broader range of solutions including accounting, project management, business intelligence, sales, and customer relationship management.
Why MRP is necessary for a company?
Why is MRP important? MRP, which is done primarily through specialized software, helps ensure that the right inventory is available for the production process exactly when it is needed and at the lowest possible cost. As such, MRP improves the efficiency, flexibility and profitability of manufacturing operations.
What are the 8 features of the MRP system?
Here are the top 8 benefits of MRP systems.Inventory control. Inventory management is crucial to realising manufacturing efficiency. ... Purchase planning. ... Production planning. ... Work scheduling. ... Resource management. ... Data management and documentation. ... Economic purchasing. ... Time-saving.
What is ERP in manufacturing?
ERP stands for enterprise resource planning. It's software that manages a company's financials, supply chain, operations, commerce, reporting, manufacturing, and human resource activities.
Why do companies need MRP?
MRP helps companies maintain low inventory levels.
How does MRP work?
MRP works backward from a production plan for finished goods, which is converted into a list of requirements for the subassemblies, component parts, and raw materials needed to produce the final product within the established schedule.
What are the inputs for MRP?
The three basic inputs of an MRP system are the master production schedule (MPS), inventory status file (ISF), and bill of materials (BOM). The MPS is simply the quantity and timing of all end goods to be produced over a specific time period. MPS is estimated through customer orders and demand forecasts.
What are the steps of MRP?
Steps of Material Requirements Planning (MRP) The MRP process can be broken down into four basic steps: Estimating demand and the materials required to meet it. The initial step of the MRP process is determining customer demand and the requirements to meet it. Utilizing the bill of materials—which is simply a list of raw materials, assemblies, ...
What are the advantages of MRP?
Advantages of the MRP process include the assurance that materials and components will be available when needed, minimized inventory levels, reduced customer lead times, optimized inventory management, and improved overall customer satisfaction.
What is BOM in manufacturing?
A critical input for material requirements planning is a bill of materials (BOM) —an extensive list of raw materials, components, and assemblies required to construct, manufacture or repair a product or service.
What is material requirements planning?
Material requirements planning was the earliest of the integrated information technology (IT) systems that aimed to improve productivity for businesses by using computers and software technology. The first MRP systems of inventory management evolved in the 1940s and 1950s. They used mainframe computers to extrapolate information from a bill ...
What is MRP in manufacturing?
MRP is a planning and scheduling system for all the materials and processes needed to carry out production. It allows you to manage production planning and inventory control in such a way that no element is ever missing for the flow of your business processes.
Why is ERP better than MRP?
Due to its comprehensive and sprawling modules, an ERP-system is best suited for large enterprises also because it is more scalable. An MRP, on the other hand, can be used for companies of all categories. If the company does not need to integrate an MRP module with several other processes, it can use it regardless of its size.
Is MRP a standalone system?
MRP works as standalone software, while ERP-system is integrated. ERP can connect smoothly with other software modules and systems, making it a modular network. MRP can be connected to some systems, but the process is more complicated and less common.
Is ERP more expensive than MRP?
Budget is often a delimiting factor. It is important to note that ERP solutions are usually much more expensive than MRP systems. However, the benefits of ERP systems often justify the higher cost because they offer a tremendous variety of features.
Acronyms & Abbreviations
Get instant explanation for any acronym or abbreviation that hits you anywhere on the web!
A Member Of The STANDS4 Network
Get instant explanation for any acronym or abbreviation that hits you anywhere on the web!
What is MRP?
MRP stands for material requirements planning. It’s a solution that helps manufacturers plan what raw materials are needed for production, when, and how much is needed. MRP is a stand-alone system that works with production-related features. Basic MRP processes include:
What is ERP?
ERP stands for enterprise resource planning, a comprehensive software system or package for managing day-to-day business operations. Thus, ERP systems are more suitable for large businesses and enterprises. However, for SME retailers, you can combine different utilities from popular open source platforms like Magento ERP to meet your unique needs.
What is the difference between ERP and MRP? (with ERP vs MRP comparison chart)
The 2 acronyms sound so similar that they’re often confused with each other. However, they’re separate systems and have many differences that affect how retailers use them in their businesses.
ERP vs MRP: Which should I implement?
Data is the key for retailers to survive in business in the digital age. Deciding whether to implement MRP or ERP is essential in ensuring that you’re on the right track. If you already understand the main difference between ERP and MRP, here is what you can expect from each system:
Is SAP an MRP or ERP?
SAP is the name of an ERP system. It’s the largest and most famous product of the SAP corporation. However, SAP isn’t necessarily an ERP or MRP system but is an ERP implementation provider. SAP ERP has many modules that cover all aspects of business management.
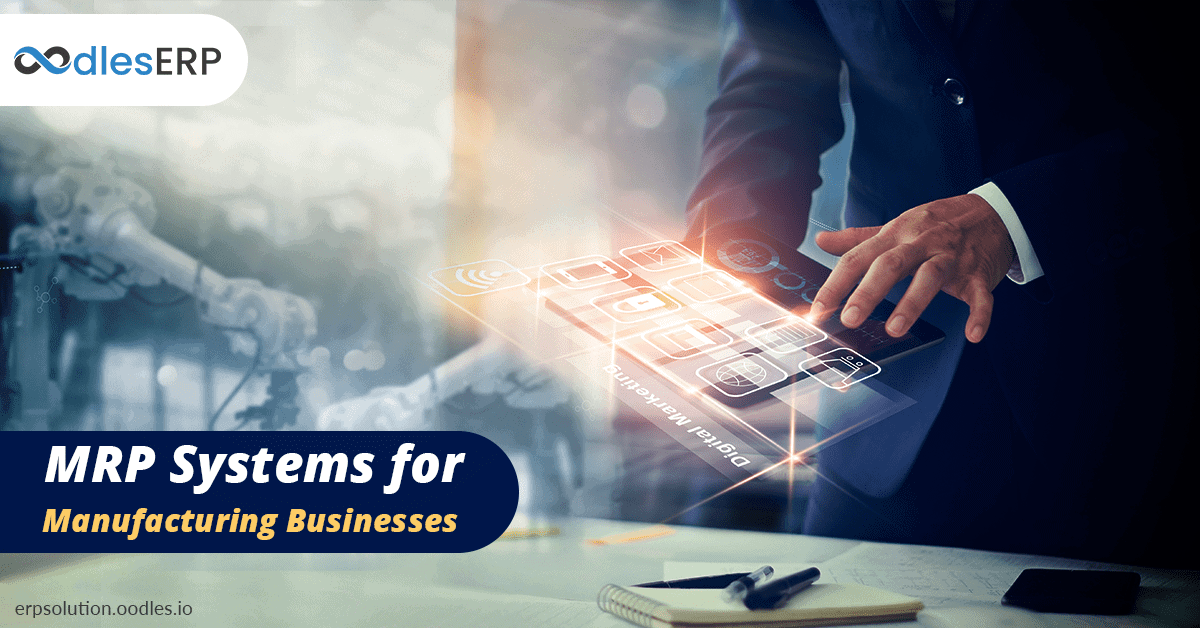
What Is Material Requirements Planning (MRP)?
How Material Requirements Planning (MRP) Works
- MRP is designed to answer three questions: 1. Whatis needed? 2. How muchis needed? 3. Whenis it needed? MRP works backward from a production plan for finished goods, which is converted into a list of requirements for the subassemblies, component parts, and raw materials needed to produce the final product within the established schedule. In other words, it's basically a system …
Steps of Material Requirements Planning
- The MRP process can be broken down into four basic steps: 1. Estimating demand and the materials required to meet it.The initial step of the MRP process is determining customer demand and the requirements to meet it. Utilizing the bill of materials—which is simply a list of raw materials, assemblies, and components needed to manufacture an end product—MRP breaks do…
Material Requirements Planning (MRP) in Manufacturing
- A critical input for material requirements planning is a bill of materials (BOM)—an extensive list of raw materials, components, and assemblies required to construct, manufacture or repair a product or service. BOM specifies the relationship between the end product (independent demand) and the components (dependent demand). Independent demand origi...
Types of Data Considered by Material Requirements Planning
- The data that must be considered in an MRP scheme include: 1. Name of the final product that's being created: This is sometimes called independent demand or Level "0" on BOM. 2. What and when info: How much quantity is required to meet demand? When is it needed? 3. The shelf life of stored materials. 4. Inventory status records: Records of net materials available for use that are …
Advantages and Disadvantages of Material Requirements Planning
- There are several advantages to the MRP process: 1. Assurance that materials and components will be available when needed 2. Minimized inventory levels and costs associated 3. Optimized inventory management 4. Reduced customer lead times 5. Increased manufacturing efficiency 6. Increased labor productivity 7. Increased overall customer satisfaction Of course, there are also …
MRP Systems: Background
- Material requirements planning was the earliest of the integrated information technology (IT) systems that aimed to improve productivity for businesses by using computers and software technology. The first MRP systems of inventory management evolved in the 1940s and 1950s. They used mainframe computers to extrapolate information from a bill of materials for a specifi…
MRP FAQs
- What Is MRP?
Material requirements planning (MRP) is a system that helps manufacturers plan, schedule, and manage their inventory during the manufacturing process. It is primarily a software-based system. MRP's objective is threefold: 1. Make sure raw materials are available for production when requir… - How Does MRP Benefit a Business?
MRP benefits a business in the following ways: 1. Ensures that materials and components are available when they're needed 2. Inventory levels are optimized and associated costs are minimized 3. Manufacturing efficiency is improved significantly 4. Customer satisfaction is incr…