
Acronym | Definition |
MRP | Manufacturing Resource (s) Planning |
MRP | Manufacturer's Recommended Price |
MRP | Mariposa (Amtrak station code; Mariposa, ... |
MRP | Material Requirement Planning |
What does MRP mean in manufacturing?
What are the main features of an MRP system?
- A master production schedule: A statement of the planning including orders, forecasts and capacity.
- Bill of materials (BOM): All the materials and components required to make the final product.
- Inventory status file: Stock records that allow gross requirements to be adjusted to net requirements.
What is MRP area and how is it defined?
What is MRP Area. How it is defined? What are the points to be considered while defining a MRP Area? The MRP area is an organizational unit for which material requirements planning can be carried out independently outside of total plant level MRP run which is done using MD01 for entire plant. by creating a specific scope of planning and is maintained in the MRP view of the material master
What is MRP an acronym for?
MRP : Maximum Retail Price. MRP Stands for Maximum Retail Price. MRP is used as an acronym in Marketing to represent Maximum Retail Price. The maximum price fixed for any product by its manufacturer is called the MRP of that product. MRP is inclusive of all taxes including GST.
What are benefits of MRP?
- Higher degree holder and experienced experts network
- Punctuality and responsibility of work
- Quality solution with 100% plagiarism free answers
- Time on Delivery
- Privacy of information and details
- Excellence in solving Operations Management questions in excels and word format.
- Best tutoring assistance 24x7 hours

What does the acronym MRP mean?
the retail price that a manufacturer recommends for selling their product. ▶ USAGE The abbreviation for manufacturers' recommended price is MRP.
What does MRP mean in finance?
Marginal revenue productKey Takeaways Marginal revenue product (MRP) is the marginal revenue created by using one additional unit of resource. MRP is used to make critical decisions on business production and determine the optimal level of a resource. The MRP assumes that the expenditures on other factors remain unchanged.
What is the full form of MRP in medical?
Magnetic resonance pancreatography (MRP)
What does MRP mean in SAP?
Material Requirements PlanningMaterial Requirements Planning (MRP), a module in SAP ERP, is a planning tool to help production and procurement planners create feasible and realistic plans so they can quickly initiate the procurement or production processes.
What is MRP explain with an example?
Material requirements planning or MRP is a computerized system that allows manufacturers to plan, manage, and control their inventories more efficiently. It, thus, helps them schedule the manufacturing per bills of materials and deliver the right product at the right time and the best possible price.
What does MRP mean in pharmacy?
At Cureatr, one of our areas of focus is medication reconciliation post-discharge (MRP). It's a topic that's getting increasing attention because of its importance in reducing hospital readmissions, adverse drug events (ADEs), and unnecessary costs.
What does MTP mean in medical terms?
MTP, which stands for Medical Termination of Pregnancy, is a procedure of terminating pregnancy using medicines. In the early stages of pregnancy (7-9 weeks), it can be terminated with the help of medicine, otherwise, the surgical process is needed.
What are medication related problems?
A medication-related problem is anything involving drug therapy that interferes with (or has the potential to interfere with) the desired outcome for a patient. Some types of medication-related problems include: Untreated conditions. Drug use without an indication.
What is the MRP formula?
Maximum Retail Price = Product's actual Cost + Profit Margin + CnF margin + Distributor Margin + Retailer Margin + GST + Transportation + other expenses etc.
How MRP planning is done?
Material requirements planning (MRP) is a system for calculating the materials and components needed to manufacture a product. It consists of three primary steps: taking inventory of the materials and components on hand, identifying which additional ones are needed and then scheduling their production or purchase.
How is the decision of employing an extra unit of Labour related to the concept of marginal revenue?
A profit-maximizing firm will base its decision to hire additional units of labor on the marginal decision rule: If the extra output that is produced by hiring one more unit of labor adds more to total revenue than it adds to total cost, the firm will increase profit by increasing its use of labor.
Acronyms & Abbreviations
Get instant explanation for any acronym or abbreviation that hits you anywhere on the web!
A Member Of The STANDS4 Network
Get instant explanation for any acronym or abbreviation that hits you anywhere on the web!
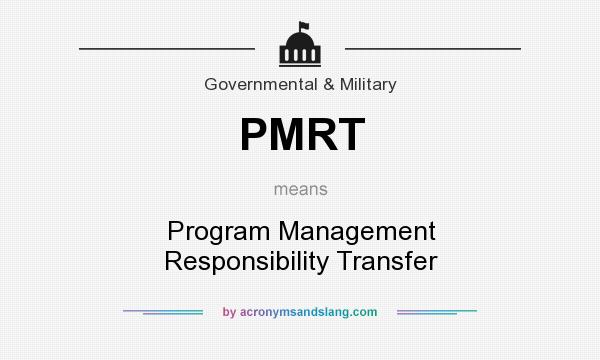