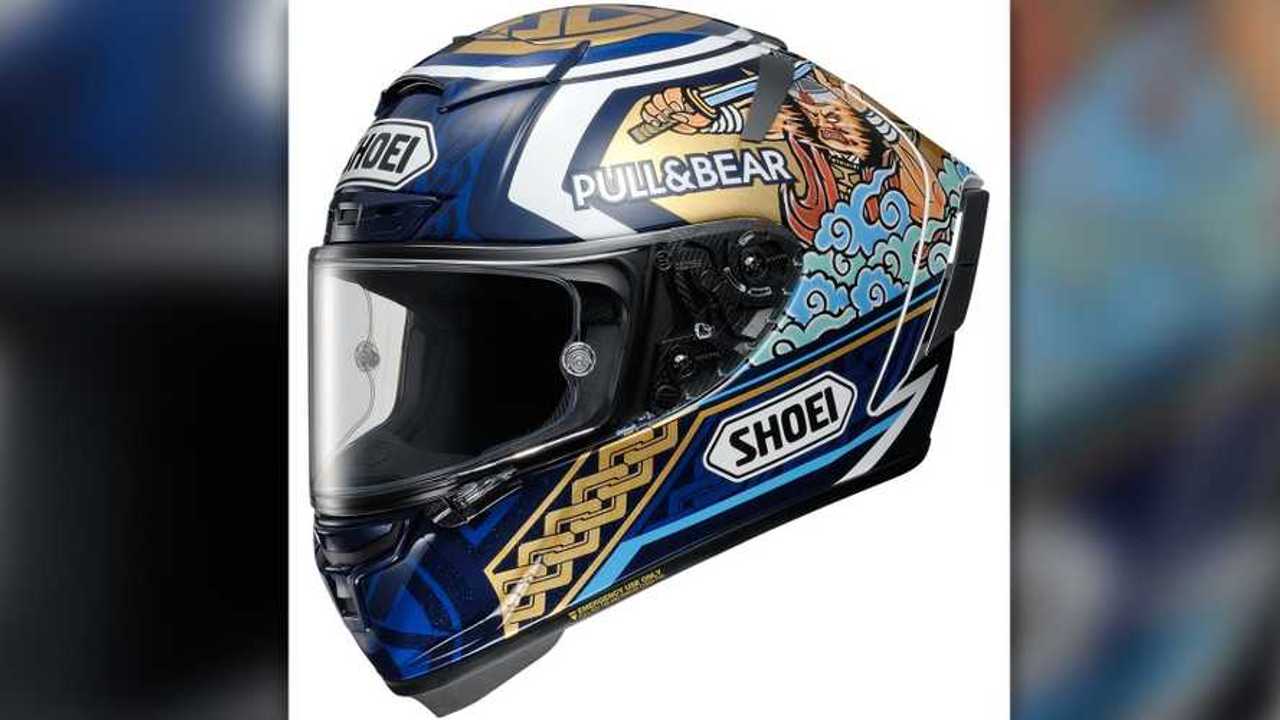
AGV navigation may be guided using one or more of the following mechanisms:
- Magnetic guide tape — some AGVs have magnetic sensors and follow a track using magnetic tape.
- Wired navigation — some AGVs follow wire paths embedded into the facility floor. The wire transmits a signal that AGVs detect via an antenna or sensor.
- Laser target navigation — with this method, reflective tape is mounted on objects such as walls, fixed machines and poles. AGVs are equipped with a laser transmitter and receiver. ...
- Inertial (gyroscopic) navigation — some AGVs are controlled by a computer system with the aid of transponders embedded into the facility floor to verify that the AGV is on the ...
- Vision guidance — No modification is required to the infrastructure for vision-guided AGVs. Cameras record the features along the route, and AGVs rely on these recorded features to navigate.
- Geoguidance — Like vision-guided AGVs, no infrastructure modifications are required for AGVs that use geoguidance. ...
- LiDAR — LiDAR (Light Detection and Ranging) is a sophisticated navigation technology utilizing sensors that transmit laser pulses to measure the distance between the robot and objects in its environment. ...
What is an AGV?
Many AGVs are similar to other human-operated vehicles but are designed to operate without direct human intervention or guidance. An automatic guided cart (AGC) is the most basic type of AGV with minimal features.
How do AGVs navigate?
AGVs can navigate following small cylindrical magnetic spots embedded on the floor. Magnetic spots are commonly cylindrical magnets with dimensions close 20x10 mm (0,8x04 inch). Magnetic spots and AGV sensor. Image from AMERDEN AGVs Magnetic spots are installed every 250-500 mm (near 15 feet) creating a virtual path.
Does the guide path of the AGV obstruct other systems?
Generally, guide path does not obstruct another systems. The guidance systems can be selected based on the type of AGV selected, its application, requirement and environmental limitation. Wire-guided – An energized wire is rooted along the guide path. The antenna of the AGV follows the rooted wire.
What are automated guided vehicles (AGVs)?
What are automated guided vehicles? Sometimes called self-guided vehicles or autonomous guided vehicles, automated guided vehicles (AGVs) are material handling systems or load carriers that travel autonomously throughout a warehouse, distribution center, or manufacturing facility, without an onboard operator or driver.

How does an AGV move?
The earliest AGVs were guided around the factory by a wired method. To navigate in this way, a wire is embedded into a slot in the floor, and transmits a radio signal, which can be detected by a sensor on the AGV. The AGV is then guided around the facility following the wire.
What are the main parts of an AGV?
An AGV is mainly composed by 5 elements: Navigation System, Safety System, Power System, Motion System and Vehicle Controller.
What are the types of navigation used in AGV?
AGV Navigation Technologies are Laser Guided Navigation, Magnetic Navigation, Natural Feature or Free navigation (including SLAM Navigation with LiDAR Sensors), Magnetic spot navigation, inductive wire navigation, optical navigation, vision navigation.
Which sensor is used in AGV?
In general, AGVs use 2D LiDAR sensors, specially designed for navigation and featuring integrated position calculation of Laser Guided Vehicles.
What is AGV control system?
Automatic Guided Vehicle (AGVs) systems, automatic steering vehicles represent self-contained vehicles, i.e., without a driver. They are designed to provide materials, especially in sequenced processes.
What is AGV and its functions?
An automated guided vehicle or automatic guided vehicle (AGV), also called autonomous mobile robot (AMR), is a portable robot that follows along marked long lines or wires on the floor, or uses radio waves, vision cameras, magnets, or lasers for navigation.
How does laser guided AGV work?
The navigation Laser emits a continuous beam of modulated laser light in a 360 degree pattern. The laser beam interacts with reflectors (also called "targets") positioned in the AGV working area. Depending on the Laser device manufacturer, LGVs calculate and correct their positioning between 30 and 40 times per second.
What is natural navigation AGV?
Step by step “free” or natural feature navigation is entering in the AGV (or Autonomous Mobile Robots, AMR) industry. The concept is simple, “free” navigation, so a navigation without need of hardware installation such wires, tapes, reflectors.
What companies use AGVs?
Applications. AGVs are important to operators in a wide range of industries, such as: manufacturing and product assembly, military and defense, aerospace, warehouse, material handling, food and beverage, automotive assembly, plastics and metal and goods packaging.
What does AGV stand for?
automatic guided vehicle• An automated guided vehicle or automatic guided vehicle (AGV) is. a mobile robot that follows markers or wires in the floor, or uses. vision or lasers. They are most often used in industrial.
How an AGV will differ with robot?
The AGV can detect obstacles in front of it, but it is not able to navigate around them, so it simply stops in its tracks until the obstacle is removed. In contrast, the AMR navigates via maps that its software constructs on-site or via pre-loaded facility drawings.
Types of AGV Navigation Systems
What Are The Most Popular AGV Navigation Methods?
Magnetic Tape Navigation AGVs
- AGVs are self-propelled vehicles with movement guided by software and sensors. Most AGVs move along defined pathways, but as mentioned, AMRs typically have more advanced technology with dynamic navigation capabilities.
Natural Navigation AGV - Free Navigation
- Automated Guided Vehicles (AGVs) are also known by other names such as LGV (Laser-Guided Vehicle), Mobile Robots, SGV (Self-Guided Vehicle), Guided Carts, Autonomous Vehicles, and Driverless Vehicles. Regardless the type of automated guided vehicle (forklift, tow tractor, cart, etc), the sel-driving robot requires an Automated Guidance Systemthat drives the AGV and infor…
Magnetic Spots Navigation
- As you can see, there are several Navigation Methods for Automated Guided Vehicles and Autonomous Mobile Robots. In these TABS, you can find some videos and presentations of the main Navigation Suppliersfor the Mobile Robot Industry. Let's dive into the different navigation technologies... here they are:
AGV Robots Navigation Benchmark Comparison
- In this case, automated guided vehicles are equipped with magnetic sensors and follow a defined track made by a magnetic tape track. Watch the following video to understand how do magnetic guided vehicles work: The guided route is made by a magnetic tape that is placed on the floor surface. The AGV magnetic sensor detects the magnetic field from th...