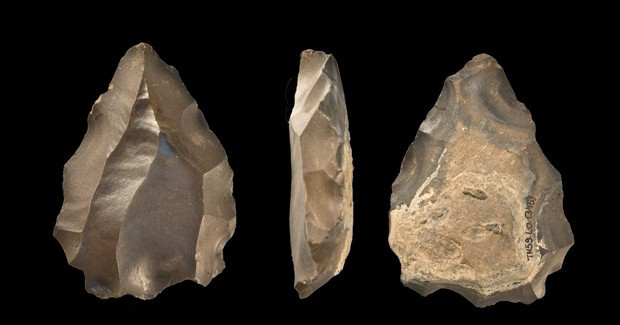
Automated Machine Type
Type | Function | Tool Material | Application | Tolerance |
Precision Boring | Produce a precise internal cylindrical s ... | Carbide, ceramic and diamond tools | Accurate finishing on internal bearing s ... | +/-0.0001 in. |
Lathe Boring | Produce conical and cylindrical surfaces | High Speed steel, brazed carbide, carbid ... | Straight holes, tapered holes, holes wit ... | +/- 0.002 in. for deep holes. +/-0.0005i ... |
Vertical Boring | produce an accurate internal cylindrical ... | High speed steel, carbides, ceramics, or ... | Small length-to-diameter ratio. The work ... | +/-0.005 in. for most. +/-0.002 for prec ... |
Jig Boring | Produces holes with highly precise dimen ... | High speed steel, carbides, ceramics, di ... | High level of dimensional accuracy such ... | +/-0.001 in. for diameter and +/-0.003 i ... |
Full Answer
What are the types of boring tools?
The common boring tools are braces, bits, gimlet etc. Joiners can also use different chisels for boring work. The hand boring tools get power from the hand pressure whereas electric power dill get power from electricity and battery. Likewise, what does a boring bar do?
What is a boring machine?
Boring is a machining process uses a specially designed cutting tool like a drill bit to enlarge a hole that is already in the part to improve the accuracy. The cutting removes material from the internal of the workpiece.
What is the use of bit boring?
Boring is a machining process uses a specially designed cutting tool like a drill bit to enlarge a hole that is already in the part to improve the accuracy. The cutting removes material from the internal of the workpiece. Boring has a wide range of applications, it can machine holes of different sizes and different precision grades.
What does boring stand for?
Boring (manufacturing) A part's-eye view of a boring bar. In machining, boring is the process of enlarging a hole that has already been drilled (or cast) by means of a single-point cutting tool (or of a boring head containing several such tools), such as in boring a gun barrel or an engine cylinder. Boring is used to achieve cylinder spherical ...

What are examples of boring tools?
The Different Types of Boring ToolsSolid boring bars. Typically made of carbide for finishing or heavy metal for roughing, solid boring bars have dense structures that make for a more stable cut as axial force is applied.Damping bars. ... Rough boring heads. ... Fine boring heads. ... Twin cutter boring heads. ... Digital boring heads.
What is meaning of boring tools?
Definition of boring tool : a boring bit with its supporting boring bar and arbor, used to enlarge and accurately finish a large bore previously formed by casting or otherwise.
What is the most common boring tool?
Boring tools in carpentry come in many sizes and shapes, and the most common boring tool in carpentry is the drill. In most cases, the terms “drill” and “boring tool” can be used interchangeably.
Where are boring tools used?
A boring bar is a tool used in metalworking and woodworking. Boring is a technique used in many aspects of building. Woodworkers have used boring as a form of drilling for centuries. In woodworking, the boring tool is static in size and used to form circular plunge cuts.
What are drilling and boring tools?
What is Difference between Drilling and Boring?DrillingBoringThe cutting tool used for drilling in a drilling operation is known as a drill bit.The cutting tool used for boring operations is known as the boring bar. A boring bar basically is a heavy metal bar with tools attached to the end.10 more rows•Nov 13, 2021
What is a boring carpentry tool?
A carpenters boring machine is a hand-driven machine to bore holes in beams such in the process of making a mortise or making holes for the wooden pegs which hold mortise and tenon joints together.
Is chisel is a boring tool?
Dowel Drill, Mortising Chisels, Plug Cutters, Brad Point and Forstner Bits.
What's the difference between drilling and boring?
Drilling is the primary process used to create the hole, while boring is a secondary process that can enlarge or finish a preexisting hole. As the size of the initial hole is entirely dependent on the drill bit, boring can be a vital step in creating a hole closer to required tolerances.
Is ratchet brace a boring tool?
boring tools Holes are bored in materials with tools called bits or drills. The boring tools are: The ratchet brace:This is the tool used to hold bits of various sizes in the chucks.
What is automated boring machine?
Automated boring machines are operated and powered by motors and machinery. In addition to type, industrial buyers should consider application, precision, power, cost and time requirements for the job.
How does a jig boring machine work?
Jig Boring produces a precise internal cylindrical surface by enlarging an existing opening in a workpiece. The single-edge cutter is advanced parallel to the axis of the hole and rotated inside a stationary workpiece. The machine has a bade, precision work table, column, and spindle housing. The spindle and work table are used for positioning and have a high level of accuracy. Jig boring machines use rigid, solid boring bars to create deep holes and single point tool bits for creating small holes. Other tools include adjustable insert boring bars, and offset heads. The tolerance and surface finish depend upon tool geometry, environmental conditions and the alignment of machine components and fixtures. The rigidity of the system, along with the cutting speed, fluid and chip removal, can also have an effect on the system. Cutting fluid needs to be used with a jig boring machine to keep the tool cool and reduce wear. Cutting fluid also allows for higher cutting speeds and feed rates.
How does horizontal boring work?
Horizontal Boring uses a single-point cutting tool to create accurate internal cylindrical surface by enlarging an existing opening in a workpiece. The machine has tool motion parallel to the axis of rotation. Holes are created by advancing one or more rotating single-point cutters horizontally into a medium to large stationary workpiece. Material chips are formed as the workpiece is advanced and helical internal feed marks are left. Horizontal boring machines can be used for milling, drilling, reaming and tapping, which saves setup time when changing application. They are designed for heavy workpieces and have a rotating worktable which can feed horizontally, parallel, and at right angles to the spindle axis.
How is vertical boring used?
Vertical Boring is used to produce an accurate internal cylindrical or conical surface by enlarging an existing opening. The large workpieces rotate about a vertical axis as the single-point cutting operation is fed into the work. The tool advances vertically and horizontally in order to control the depth and diameter of the cut produced. The bore hole is always concentric with the axis of rotation of the work piece. The machine for vertical boring is similar to lathe boring and consists of a base, a rotating horizontal work table, a column, and a cross rail. The cross rail supports one or more tool heads. Tolerance and surface finish for vertical boring depends on the tool geometry, cutting speed and feed rate. The rigidity of the tool, workpiece and machine, as well as system for chip removal can also have an effect on the process results.
What is precision boring?
Precision Boring is a single-point cutting operation. The workpiece moves parallel to the axis of rotation of the cutting tool and enlarges an existing opening in a workpiece, producing a precise internal cylindrical surface. Precision boring can also be used to straighten and enlarge existing holes by advancing the workpiece into a rotating single-point. The material is removed as small chips. Precision boring machines are available in a wide range of sizes and types.
How does a lathe bore work?
To produce a taper on the workpiece, the cutting tool moves at an angle to the axis of rotation. The workpiece is held in a chuck and rotated as a boring bar with an insert attached to the tip of the bar is fed into an existing hole. When the tool comes into contact with the workpiece a chip is formed that may be continuous or segmented, and the surface produced is called a bore . This process does not require any special set equipment, except the boring bar. Tools are available in a wide range of sizes and shapes for use in different applications. There are several factors that can affect the results of the processing, including tool geometry, cutting speed and feed rate, rigidity of tool, workpiece, and machine, and the chip removal. Also important are the environmental conditions and the alignment of the machine components and fixtures.
What should be considered when selecting an automated boring machine?
Specifications including cutting speed and removal rate should be considered when selecting an automated boring machine.
What is a boring tool?
: a boring bit with its supporting boring bar and arbor, used to enlarge and accurately finish a large bore previously formed by casting or otherwise.
What are the tools used for boring?
The common boring tools are braces, bits, gimlet etc. Joiners can also use different chisels for boring work. The hand boring tools get power from the hand pressure whereas electric power dill get power from electricity and battery.
What is boring in construction?
In the construction industry, boring is a technique used to explore the underground surface and to determine if it is capable of holding up a building.
What is an auger bit?
Auger Bit is a tool that bores holes through wood, metal, rock, concrete, soil or ice. The spade bit and paddle bits are the most common and have wide, flat cutting surfaces. Chisels are hand tools for a shaped cutting edge on its end for carving or cutting hard material.
What is a reamer tool?
A reamer is a type of rotary cutting tool used in metalworking. Precision reamers are designed to enlarge the size of a previously formed hole by a small amount but with a high degree of accuracy to leave smooth sides. The process of enlarging the hole is called reaming.
What is a drill bit?
Drilling is a cutting process that uses a drill bit to cut a hole of circular cross-section in solid materials. The drill bit is usually a rotary cutting tool, often multi-point.
What is reaming in a drill?
Definition of 'reaming' Reaming is a cutting process in which a cutting tool produces a hole of a very accurate size. Reaming is done to a hole which has been already drilled, to produce a truly circular hole of exactly the right diameter. Reaming involves widening the opening of a hole.
Boring bars
Boring deep holes can involve extreme length-to-diameter ratios, or overhang, when it comes to tooling assemblies. Since it can be difficult to maintain accuracy and stability in these scenarios, we need boring bars to extend tooling assemblies and while maintaining the rigidity to make perfect circles with on-spec finishes.
Boring heads
Boring heads are specifically designed to enlarge an existing hole. They hold cutters in position so they can rotate and gradually remove material until the hole is at the desired diameter.
Starter drills
Since cutters are on diameter of boring heads and not their face, they are not able to initiate a hole on a flat surface or raw material. Especially in smaller bores, fluted drills called starter drills can be used to get the hole started before rough boring.
Specialty boring heads
Back boring and face grooving heads, as well as chamfering insert holders, are available for some of the most common secondary operations, after a hole is bored. We produce specific heads with cutters at the appropriate angles so each of these operations can be done without manually moving the part, changing the tool or adjusting the cutter angle.
Modular boring tools
Since limiting length-to-diameter ratios is so crucial to boring success, it’s extremely valuable to be able to make your tooling assembly as short as possible.
How do boring heads work?
The most commonly used boring heads shift the boring bar closer to or farther away from the axis of the hole to achieve the desired hole diameter. These boring heads are inexpensive. Users can bore a large range of hole sizes with these heads because the boring bar can be mounted in several different. positions.
Why are boring bars so common?
Because of their lower cost, steel boring bars are the most common, but other materials are also available. For example, cutting tool manufacturers have developed heavy-metal and carbide bars to fight chatter. Heavy-metal bars are made from tungsten alloys, which are denser than steel. These alloys work to damp vibration. Although heavy-metal bars are more expensive than steel ones, they can be applied at higher length-to-diameter ratios. Whereas steel allows a 4:1 ratio, heavy-metal bars can boost the ratio into the 6:1 or higher range with some speed-and-feed tuning.
What are boring bars made of?
Because of their lower cost, steel boring bars are the most common, but other materials are also available. For example, cutting tool manufacturers have developed heavy-metal and carbide bars to fight chatter. Heavy-metal bars are made from tungsten alloys, which are denser than steel. These alloys work to damp vibration.
Why are carbide bars not practical?
Carbide bars above 1" in diameter are not practical because of the expense. In situations where carbide would be cost-prohibitive, a tunable bar may be warranted. As the name implies, these bars have an adjustment feature that enables a user to tune the bar to a specific application.
What is tungsten carbide?
Tungsten-carbide bars provide even higher depth-to-diameter ratios. Carbide bars are made by brazing a steel head that is machined to accept an insert onto a carbide bar. Carbide is extremely dense. It provides superior damping, allowing length-to-diameter ratios in the 8:1 or higher range.
What is drilling reaming?
Drilling, reaming and boring are the basic holemaking operations of machining. In simple terms, drilling creates a hole in a workpiece where there was no existing hole. Reaming and boring accurately enlarge holes that already exist.
Why use twin style head for roughing?
Twin-style heads are best-suited for roughing because they are not easily adjusted for those times that small incremental changes to the boring diameter are necessary. When finishing, it is better to select a finish-boring head to make those small adjustments to the diameter.
When was the first boring machine tool invented?
The first boring machine tool was invented by John Wilkinson in 1775. Boring and turning have abrasive counterparts in internal and external cylindrical grinding. Each process is chosen based on the requirements and parameter values of a particular application.
What is the purpose of boring?
Boring is used to achieve greater accuracy of the diameter of a hole, and can be used to cut a tapered hole. Boring can be viewed as the internal-diameter counterpart to turning, which cuts external diameters. There are various types of boring.
What are the limitations of boring?
The limitations of boring in terms of its geometric accuracy (form, position) and the hardness of the workpiece have been shrinking in recent decades as machining technology continues to advance. For example, new grades of carbide and ceramic cutting inserts have increased the accuracy and surface quality that can be achieved without grinding, and have increased the range of workpiece hardness values that are workable. However, working to tolerances of only a few micrometres (a few tenths) forces the manufacturing process to rationally confront, and compensate for, the fact that no actual workpiece is ideally rigid and immobile. Each time a cut is taken (no matter how small), or a temperature change of a few hundred degrees takes place (no matter how temporary), the workpiece, or a portion of it, is likely to spring into a new shape, even if the movement is extremely small. In some cases a movement of a fraction of a micrometre in one area is amplified in lever fashion to create a positional error of several micrometres for a feature of the workpiece several decimetres away. It is factors such as these that sometimes preclude finishing by boring and turning as opposed to internal and external cylindrical grinding. At the extreme, no perfection of machining or grinding may be enough when, despite the part being within tolerance when it is made, it warps out of tolerance in following days or months. When engineers are confronted with such a case, it drives the quest to find other workpiece materials, or alternate designs that avoid relying so heavily on the immobility of part features on the micro or nano scales.
What tolerances are needed for a lathe boring?
For most lathe boring applications, tolerances greater than ±0.010 in (±0.25 mm) are easily held. Tolerances from there down to ±0.005 in (±0.13 mm) are usually held without especial difficulty or expense, even in deep holes. Tolerances between ±0.004 in (±0.10 mm) and ±0.001 in (±0.025 mm) are where the challenge begins rising. In deep holes with tolerances this tight, the limiting factor is just as often the geometric constraint as the size constraint. In other words, it may be easy to hold the diameter within .002" at any diametrical measurement point, but difficult to hold the cylindricity of the hole to within a zone delimited by the .002" constraint, across more than 5 diameters of hole depth (depth measured in terms of diameter:depth aspect ratio ). For highest-precision applications, tolerances can generally be held within ±0.0005 in (±0.013 mm) only for shallow holes. In some cases tolerances as tight as ±0.0001 in (±0.0038 mm) can be held in shallow holes, but it is expensive, with 100% inspection and loss of nonconforming parts adding to the cost. Grinding, honing, and lapping are the recourse for when the limits of boring repeatability and accuracy have been met.
Why is boring more difficult than turning?
Because of the limitations on tooling design imposed by the fact that the workpiece mostly surrounds the tool, boring is inherently somewhat more challenging than turning, in terms of decreased toolholding rigidity, increased clearance angle requirements (limiting the amount of support that can be given to the cutting edge), and difficulty of inspection of the resulting surface (size, form, surface roughness ). These are the reasons why boring is viewed as an area of machining practice in its own right, separate from turning, with its own tips, tricks, challenges, and body of expertise, despite the fact that they are in some ways identical.
Why is boring important?
Because boring is meant to decrease the product tolerances on pre-existing holes , several design considerations apply. First, large length-to-bore-diameters are not preferred due to cutting tool deflection.
How big is a boring machine?
Boring operations on small workpieces can be carried out on a lathe while larger workpieces are machined on boring mills. Workpieces are commonly 1 to 4 metres (3 ft 3 in to 13 ft 1 in) in diameter, but can be as large as 20 m (66 ft). Power requirements can be as much as 200 horsepower (150 kW). Cooling of the bores is done through a hollow passageway through the boring bar where coolant can flow freely. Tungsten-alloy disks are sealed in the bar to counteract vibration and chatter during boring. The control systems can be computer-based, allowing for automation and increased consistency.
What is boring in machining?
Boring is a common machining method, which can be used to correct errors. In this guide, we’ll introduce what is boring process and types of machines it uses, as well as the difference between boring and drilling.
What is Boring Process?
Boring is a machining process uses a specially designed cutting tool like a drill bit to enlarge a hole that is already in the part to improve the accuracy. The cutting removes material from the internal of the workpiece. Boring has a wide range of applications, it can machine holes of different sizes and different precision grades. For holes with large diameter, high precision of size and location, boring is almost the only processing method. Boring on the lathe can be completed through mounting the holder and boring tool bar with cutter bit on the tool post and revolving the part.
How many types of boring machines are there?
There are three boring machines according to the processing: - Horizontal boring machines: bore holes with a spindle that is parallel to the work table. - Vertical boring machines: uses a rotating piece attached to a horizontal table, the borer is able to move upwards or downwards. - Line-boring machines: the boring bar is supported on both ends.
Can drilling increase the axial length of a hole?
Drilling process can increase the axial length of the hole while boring can’t.
Is boring a bit or a bar?
Boring should be executed after drilling. Drilling uses drill bit while boring uses boring bar. In addition, boring bar is a single point cutter, and drill is based on multi-point. Drilling process can increase the axial length of the hole while boring can’t.
What Is Boring?
Boring is a cutting process that involves the use of a single-point cutting tool or boring head to enlarge an existing hole in a workpiece. This is in stark contrast to drilling, which is performed to create an initial hole in a workpiece.
What is reaming in a rotary cutter?
What Is Reaming? Finally, reaming is a cutting process that involves the use of a rotary cutting tool to create smooth interior walls in an existing hole in a workpiece. The rotary cutting tool used in reaming is known as a reamer.
What Is Drilling?
Drilling is a cutting process that involves the use of a drill bit to cut a circular-shape hole in a workpiece. The drill bit used in drilling is a type of rotary cutting tool that, like other rotary cutting tools, rotates while subsequently scraping material out of the workpiece. To drill a workpiece, a manufacturing company must press the drill bit against the workpiece. When the drill is activated, the drill bit will dig its way into the workpiece while creating a circular-shaped hole in the process.
How to drill a workpiece?
To drill a workpiece, a manufacturing company must press the drill bit against the workpiece. When the drill is activated, the drill bit will dig its way into the workpiece while creating a circular-shaped hole in the process. It’s a common assumption that drilling can only be performed on soft materials like wood.
Can you drill on wood?
It’s a common assumption that drilling can only be performed on soft materials like wood. Many drilling processes do, in fact, involve wooden workpieces, but others involve workpieces made of harder materials, including metal.
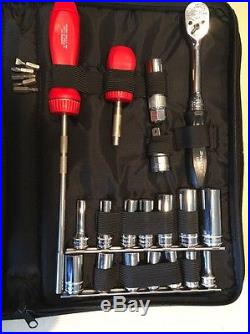