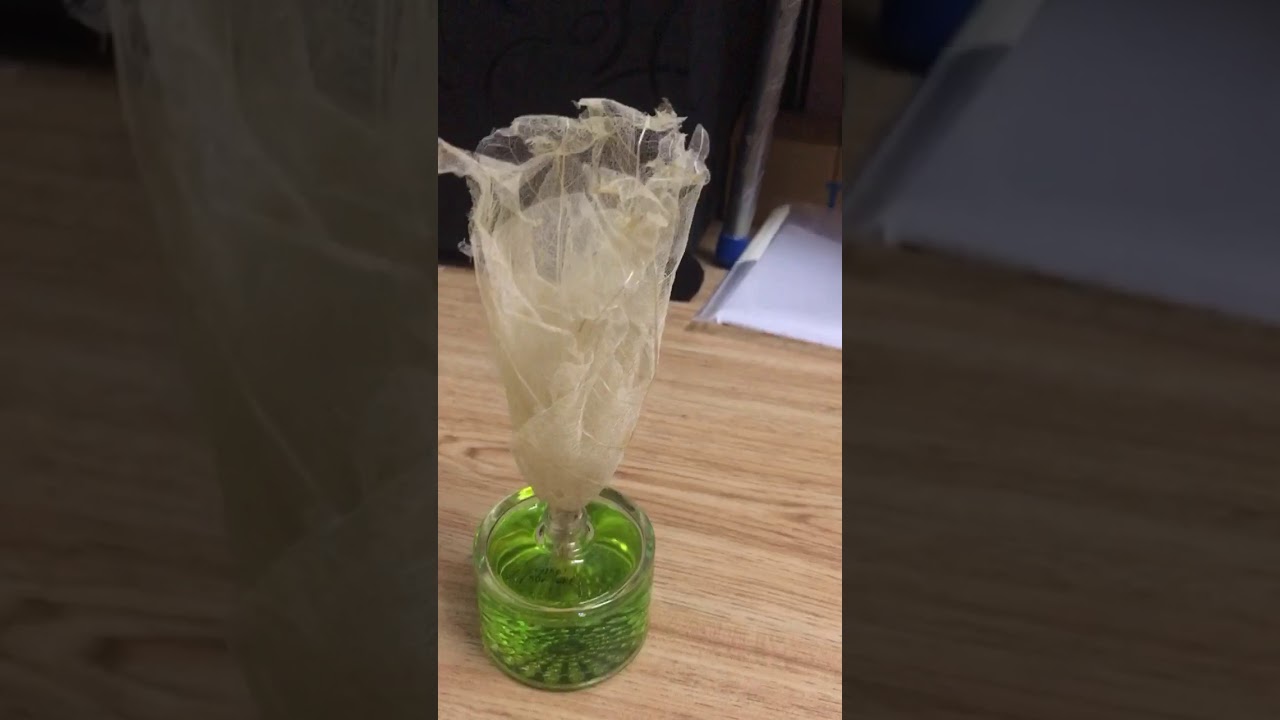
What is the difference between No 3 and No 4 finishes?
Like No. 3 finishes, No. 4 finishes are also characterized by short, uniform parallel polishing lines. They typically require a No. 3 finish with gradually finer abrasives. This final finish can end anywhere between 150- and 320-grit. Typically, as the grit number increases, polishing lines are finer and the reflective finish is greater.
What is 1D stainless steel surface finish?
1D stainless steel is sometimes used as the starting point for polished finishes. However, common applications of this stainless steel surface finish involve non-decorative purposes. Thus, the visual appearance is not always relevant. Some examples include: As this steel is cold rolled rather than hot rolled, the surface finish is more refined.
What are the different types of Mill finishes?
Let’s review two of the more common mill finishes: • 2B: This is achieved by cold rolling, heat treating and pickling, along with the application of a light rolling at the end in order to achieve a smooth and reflective sheen. Considered the most widely used surface finish, 2B is the basis for most polished and brushed finishes.
What are bright annealed and temper rolled stainless steel finishes?
Last in this guide to stainless steel finishes are Bright Annealed and Temper Rolled finishes. BA finishes are often confused with No. 8 finishes, but they are different as they do not provide a clear finish. While No. 7 and No. 8 finishes have a mirror-like quality, the annealing process of BA finishes does not produce the scale on the surface.
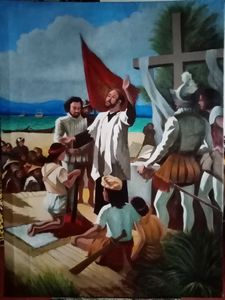
What is da style finish nails?
Angled finish nails may be “DA” or “FN” style. These styles offer 2 slightly different 15-gauge angled finish nail standards. DA angled finish nails will have an angle of about 34 degrees. FN angled finish nails will have an angle of about 25 degrees. DA angled finish nails were pioneered by Senco.
What does DA mean for nail gun?
“DA” and “FN” are two slightly different 15-gauge angled finish nail standards. DA finish nails have an angle of around 34 degrees. FN finish nails have an angle of around 25 degrees.
What degree are Senco finish nails?
34 degreeThese nails are 34 degree nails.
What is the difference between a straight and angled finish nailer?
The difference between a straight and angled nailer is the shape of the nail magazines. A straight nailer has a magazine that is parallel to the surface you are nailing. With an angled nailer, the magazine comes up at an angle from the head of the nailer.
Are all finish nails the same?
finish nails, it depends on your project and the type of wood you're using. In general, go with finish nails for thick wood and brads for thin wood. Finish nails are stronger than brads, so choose them if your project needs to be durable. Brads are thin, 18-gauge nails made for more delicate woodworking jobs.
What does GA stand for in nails?
These are found in most joinery workshops and are used in moulding, decorative trim, furniture manufacturing,window beading and much more. Available on our range in 18 Gauge Galvanised Finish Nails and 18 Gauge Stainless SteelBrads. These 2nd fix 18 Ga brads can be obtained in leg lengths from 10mm to 50mm.
Are Senco nails galvanized?
SENCO 15-Gauge Galvanized/Coated Steel Finish Nail (3000-Count)
What nails work in a Senco finish nailer?
2-1/2" x 15 Gauge Angled Finish Nails - to fit Senco Nailers - 1000 pc.
Can an 18 gauge nail gun shoot 16 gauge nails?
0:161:29what HAPPENS when you put the WRONG nails in your air nailerYouTubeStart of suggested clipEnd of suggested clipBut there's also different lengths of each type on accident we put the 18 gauge nails into the 16MoreBut there's also different lengths of each type on accident we put the 18 gauge nails into the 16 gauge nailer. And about every 5 times we'd. Actually drive a nail.
What is the advantage of an angled finish nailer?
Reach Corners: There are several advantages to the angled finish nailer starting with its shape. Because the magazine is angled back, you can drive nails into tighter locations without having the handle of the nail gun contact the opposing surface. For work in tight spaces, the angled finish nailer is superior.
Which is better 15 or 16 gauge finish nailer?
The 15 gauge finish nailer is ideal for heavier jobs. If you're working with thin wood, delicate molding or want a smaller nail head to fill, then the 16 gauge nailer is the better option.
What gauge finish nailer is best?
16-gauge finish nailer If you're shopping for a finish nailer, I'd recommend the larger 15-gauge gun, simply because the fatter nails provide more holding power.
What is a DA Brad?
The Ryobi Airwave 15Ga DA brad nailer is the perfect tool for a range of home renovation and DIY projects. It neatly, quickly and easily drives brad nails, which can be very difficult to drive manually. Like all the quality power tools in Ryobi's Airwave range, this brad nailer is pneumatic -...
How big is a 15Ga nail?
What Are 15-Gauge Nailers Used For? 15-gauge nailers shoot a thick nail between 1-1/4” to 2-1/2” long. They have substantial holding power thanks to the heavier head.
What's the difference between a 16 gauge and 18 gauge brad nailer?
Gauge is actually the number of nails that are lined up. This indicates that 16-gauge nails are thicker and can hold better when compared to 18-gauge brads. You will have to keep in mind that a low gauge number will have a thicker nail.
What are 15-gauge nails used for?
15-gauge – For the outer nail on casing (through drywall) and for base trim or other large trim , and sturdy install of door jambs, particularly heavy, solid-core doors. Non-structural interior applications such as crown molding, door casings or chair rail offer the most choice in the tools and fasteners you use.
Woodworking Network
I’m building louver panels for an outdoor shower using 1 x 4 for rails and 5/4 x 6 …
Woodworking Network
I have managed to get the old and damaged veneer off of this antique table top. …
What would YOU charge?
Pricing Survey reveals why prices vary so much for custom woodworking.
FN vs DA Style 15 Gauge Finish Nails
While many of you probably know the difference between FN and DA 15 gauge finish nails there are still many guys confused and frustrated with this topic. 15 gauge angled finish nailers are very popular and on any given day you’re likely to find several different models on the jobsite.
About the author
Todd Fratzel is the Editor of Tool Box Buzz and the President of Front Steps Media, LLC, a web based media company focused on the Home Improvement and Construction Industry.He is also the Principal Engineer for United Construction Corp., located in Newport, NH.
What are the different finishes of stainless steel?
From mill finishes to applied finishes, the stainless steel finishes that are applied to the surface of your stainless steel can play a bigger role than you may realize.
What is a 2b finish on stainless steel?
Let’s start with basic protection—which applies itself organically. All stainless steels are iron-based alloys containing at least 10.5% chromium. A reaction between that chromium and the oxygen in the atmosphere produces a chromium oxide film at the surface.
Still not finished?
In some cases, even with an applied finish your material could be left with minor imperfections—often but not always invisible to the naked eye.
Stainless Steel Finishes According to EN and ASTM Equivalents
Let’s start by comparing the EN and ASTM finishes in a table format. This gives you a great overview of the possibilities using both standards. We’ll get into the details of each finish later in the article.
Mill Finishes for Stainless Steel
Mill finish is the basic supply condition for stainless steels, no matter whether they are cold or hot rolled. However, most of these steels require further finishing processes to meet the requirements of certain applications.
Mechanically Polished & Brushed Stainless Steel Finishes
A few recommendations apply when selecting a stainless steel for your application. As a starting point, choose a mill finish that is the closest to the desired outcome. This way, the number of additional processes can be minimised.
Patterned Finishes for Stainless Steel
Producing patterned stainless steel finishes includes pressing or rolling with patterned rolls. These operations result in an effectively stiffened sheet. As a result, this allows for thinner gauge cladding, a subsequent possible cost saving and overall weight reduction.
Coloured Finishes for Stainless Steel
These finishes take advantage of the properties of the inert chromium layer at the surface of stainless steels. This layer provides the corrosion resistant properties to the material.
What is a No 3 finish?
No. 3 finishes are a 120-grit option. They obtain a 120-grit abrasive through a one-directional course. This type of finish is also known as grinding, roughing, or rough grinding given its coarse, preliminary finish. The intermediate polished finish ensures a peel-off protective covering on one side of the sheet. Using an initial 50- to 80-grit abrasive to achieve a final 120-grit abrasive, No. 3 finishes require mechanical or gradual finer polishing techniques via special coils or rolls. The resulting polishing lines indicate linear grain pattern with a roughness average (Ra) of less than or equal to 40 micro-inches and a moderate reflective finish. Operators must use short strokes in an elliptical motion to create these short grain patterns. No. 3 finishes are commonly used in food production and food service. This includes brewing equipment, food processing, kitchen equipment, and scientific apparatuses.
What is the grit number of a No. 4 finish?
No. 4 finishes show an Ra of 25 micro-inches or less with a highly reflective finish. Similar to No. 3 finishes, No. 4 finishes are used for general purposes.
What finish is Cloud Gate?
More so, the notable Cloud Gate in Chicago, Illinois uses a No. 8 stainless steel finish. Also known as “The Bean” amongst locals, this attraction draws hundreds of daily spectators who take pictures and observe their reflections in the steel finish.
What is a 2B stainless steel finish?
No. 2B is one of the most common stainless steel finishes used today. It’s a cold roll finish that’s non-reflective, smooth, and has good flatness. Often, the surface has a smooth, reflective grey matte finish, meaning it’s dull and unreflective in appearance. This makes it perfect for applications requiring a basic and unaesthetic finish. With that, 2B finishes are often the least expensive available option. In this case, the thickness can range based on skin passing capacity. To produce a No. 2B finish, stainless steel is cold rolled through a special roller. This produces a smooth, less pitted surface. Then, the surface is softened and descaled in an acid solution. Finally, it passes through polishing rolls for further smoothness. The most common applications for No. 2B finishes include chemical and pharmaceutical equipment, laundry and dry cleaning, refrigeration, and sewage.
Why do you need to choose a finish for aluminum?
Reason #2: Finishes can enhance the appearance of the aluminum. Depending on the look you are trying to achieve, you will need to select the appropriate finish. Maybe you want something that’s brightly colored. Maybe you’re trying to achieve a “mirror” finish. You need to choose a finish that will give you the look you want to achieve.
What is a bright dip?
An extrusion can be bright dipped, giving the aluminum a specular or “mirror” finish. To do this, technicians put the profile into a special dip solution (a combination of hot phosphoric and nitric acids). After bright dipping, profiles can also be anodized, thickening the metal’s corrosion-resistant oxide layer.
Why use aluminum extrusion?
There are many great reasons to choose aluminum extrusions for your project. Aluminum is versatile and relatively low-cost. It has a high strength-to-weight ratio and possesses non-corrosive properties. It is environmentally friendly and can accept high-performance coatings.
What is aluminum pretreatment?
The aluminum is either etched or cleaned with alkaline or acidic materials. Then a pretreatment coating is applied. This coating enhances powder or paint adhesion and provides resistance against corrosion.
What is liquid coating?
These coatings come in many colors and provide a uniform film thickness. Liquid coatings generally contain volatile organic compounds (VOCs). They are driven off during the curing or baking process. When the VOCs are gone the volume solids form a film on the extrusion.
Is aluminum extrusion environmentally friendly?
It is environmentally friendly and can accept high-performance coatings. Once you’ve decided to design your custom aluminum extrusions, there are some important choices you need to make. One such choice is which finishing option to choose.
Can you anodize aluminum?
Anodized aluminum will also accept vibrant colors. You can anodize any kind of aluminum alloy.
