
What causes discontinuity in welding?
Common causes are lack of shielding gas, excessive arc length, or dirty base material. Another no so common cause can be arc blow, where magnetic fields cause an erratic arc.
What is the difference between a discontinuity and a defect?
The Differences Between Discontinuities and Defects A discontinuity will survive a field test while a defect won't. A crack on a water pipe would be a defect since the water will leak while an unacceptable profile could pass as a discontinuity as long as the pipe doesn't leak.
What is discontinuity in metal?
Inherent discontinuities are created when metal is molten and malleable during the casting process. Inherent wrought discontinuities are associated with the melting and the solidification of the ingot before it is formed into salable quantities such as slabs, blooms, and billets.
What weld discontinuity is considered to be the most severe?
The most severe weld metal discontinuity is generally considered to be a crack. Cracks can propagate quickly and cause the weld joint to fail.
What are the 3 types of discontinuity?
There are three types of discontinuity.Jump Discontinuity.Infinite Discontinuity.Removable Discontinuity.
What is discontinuity?
lack of continuity or cohesionDefinition of discontinuity 1 : lack of continuity or cohesion. 2 : gap sense 5. 3a : the property of being not mathematically continuous a point of discontinuity. b : an instance of being not mathematically continuous especially : a value of an independent variable at which a function is not continuous.
What causes a discontinuity?
A point of discontinuity occurs when a number is both a zero of the numerator and denominator. Since is a zero for both the numerator and denominator, there is a point of discontinuity there. To find the value, plug in into the final simplified equation.
Do all welds have discontinuities?
The truth is that all welds have flaws, or discontinuities, but some have so many that they fail quality assurance tests and are ultimately considered. Welding discontinuities should be taken seriously because they can render all of the time, effort and energy you put into a weld completely pointless.
What are the 4 types of discontinuity?
There are four types of discontinuities you have to know: jump, point, essential, and removable.
How do you prevent welding discontinuities?
Here are the various ways to prevent welding defects;Use of Low Hydrogen Filler Metals. There are many manufactures out there who offer a wide variety of products. ... Proper Matching of Filler Metal and Base Material Strength. ... Pre- and Post-Weld Materials Correctly. ... Implementation of Proper Filler Storage. ... Proper Training.
What are the 3 groups of discontinuities in welding?
Globular, volumetric, 3-D discontinuities, porosity, or inclusions usually are found deep inside the weld. Porosity is a collective name describing cavities or pores caused by gas entrapment in molten metal during solidification.
What is the strongest form of weld?
TIG weldingTIG welding is often considered the strongest weld since it produces extreme heat, and the slow cooling rate results in high tensile strength and ductility. MIG is also an excellent candidate for the strongest type of weld because it can create a strong joint.
What does Foucault mean by discontinuity?
Discontinuity and continuity according to Michel Foucault reflect the flow of history and the fact that some "things are no longer perceived, described, expressed, characterised, classified, and known in the same way" from one era to the next.
What is the difference between discontinuity and continuity?
Continuity refers to the view that development is a gradual, continuous process. Discontinuity refers to the view that development occurs in a series of distinct stages. A similar debate exists concerning nature versus nurture.
What are some examples of discontinuity?
Some of the examples of a discontinuous function are: f(x) = 1/(x - 2) f(x) = tan x. f(x) = x2 - 1, for x < 1 and f(x) = x3 - 5 for 1 < x < 2.
What is another word for discontinuity?
What is another word for discontinuity?disconnectionbreakdiscontinuancediscontinuationendinghaltpausestaystopstoppage141 more rows
What is discontinuity in engineering?
Discontinuity is defined as an interruption of the typical structure of a material, such as a lack of homogeneity in its mechanical, metallurgical, or physical characteristics. A discontinuity could be the result of a defect, but isn't necessarily a defect.
What is a porosity weld?
Porosity is defined as a cavity-type discontinuity formed by gas entrapment during solidification. These trapped gases in the molten weld may form bubbles or pockets as the weld solidifies.
Why do welds crack?
Cracking often is caused by stress concentration near discontinuities in welds and base metal and near mechanical notches in the weldment design. Hydrogen embrittlement, a condition that causes a loss of ductility and exists in weld metal because of hydrogen absorption, can contribute to crack formation in some materials.
How to control porosity?
The most practical methods for controlling or eliminating porosity are to use clean base materials, properly store uncontaminated welding consumables, adequately maintain welding equipment, use proven welding procedures, and weld in acceptable environmental conditions.
Why is welding inspection important?
Understanding these weld discontinuities will help welding inspectors identify them and, more important, prevent them from occurring in production. Using welding inspection as a preventive tool within the quality system is more efficient than using it only as an appraisal technique to sort bad welds from good welds.
What are the different types of cracks in welding?
Weld Metal Cracks. Weld metal cracks can be divided into three types: 1 Transverse, which are perpendicular to the direction of the weld. 2 Longitudinal, which travel in the same direction as the weld and often are confined to the center of the weld. This type of crack may be an extension of a crack that originally initiated at the end of a weld. 3 Crater, which can be formed by an abrupt weld termination if a crater is left unfilled with weld metal. These cracks usually are star-shaped and initially extend only to the edge of the crater. However, they can propagate into longitudinal weld cracks.
Why is there incomplete fusion?
Incomplete fusion often is found on one leg of a fillet weld and is caused by an incorrect welding angle, which distributes heat nonuniformly between both sides of the joint. It also may be caused by oxides or other foreign material on the surface of the base material.
How does discontinuity affect weld performance?
In some cases, a discontinuity can greatly affect the performance of the weld. Discontinuities like lack of fusion, laminar tearing, and most forms of cracks are one of them. No matter how hard you try to repair it, you’ll only waste your time and resources, making it not worth the fuss.
How to prevent welding?
Prevention : Use the electrode in good condition (dry) or the box of the electrode is not broken. Clean surface of the material from oil and another impurity. You must reduce arc length suitable at the welding procedure. Use gas flowrate suitable at welding procedure specification. 2.
What does it mean to sound weld?
As a welder, you really want to weld a sound weld. A sound weld means that there’s uniformity (with a very little variation tolerance) everywhere you see, either on weld surface or on sub-surface.
What is tungsten electrode?
The Tungsten electrode is in contact with the weld pool during the welding process. The hot tungsten electrode is in contact with filler metal. Occur crack in the tungsten electrode. The use of welding current exceeds the maximum temperature limit of tungsten electrodes.
What is slag inclusion?
Slag inclusion is also one of the classic discontinuity that occurs in welding. It’s a situation when the slag – a protective layer that supposed to resurface and protect the molten weld pool – is trapped under the geometry of the weld itself.
Why do carbides melt?
When the heat from welding highly increases the temperature, those carbides will melt and decrease the material’s strength. Combined with the stress applied to the material, it will break and propagate fast without even waiting for the material to cool down. Hence the name hot crack.
What is surface porosity?
1. Porosity. Example of surface porosity (right) and sub-surface porosity (left) Porosity is one of the classic discontinuities that happens in welding. It happens when there are just so many gas molecules trapped inside during welding.
What is welding discontinuity?
Technically, a welding discontinuity is the lack of a mechanical, physical or metallurgical harmony in the weld. This could be manifested in terms of
What would be a defect if the welder or the quality control department rejects it and blacklists?
Any weld would be a defect if the welder or the quality control department rejects it and blacklists the product.
Can a discontinuity survive a field test?
A discontinuity will survive a field test while a defect won’t. A crack on a water pipe would be a defect since the water will leak while an unacceptable profile could pass as a discontinuity as long as the pipe doesn’t leak.
Can discontinuities be ignored?
Discontinuities can be ignored since they are always well within the acceptable production error margins. Defects, on the other hand, must be repaired. If the defect is irreparable, the product should get a red reject tag and head to the junk bin.
Is a discontinuity a defect?
All welding defects are developed discontinuities. If a discontinuity renders a weld incompetent or lowers its quality, it would be classified as a defect. Defects make the product risky to use or substandard. It is up to the quality control to decide whether the discontinuity qualifies as a defect or not.
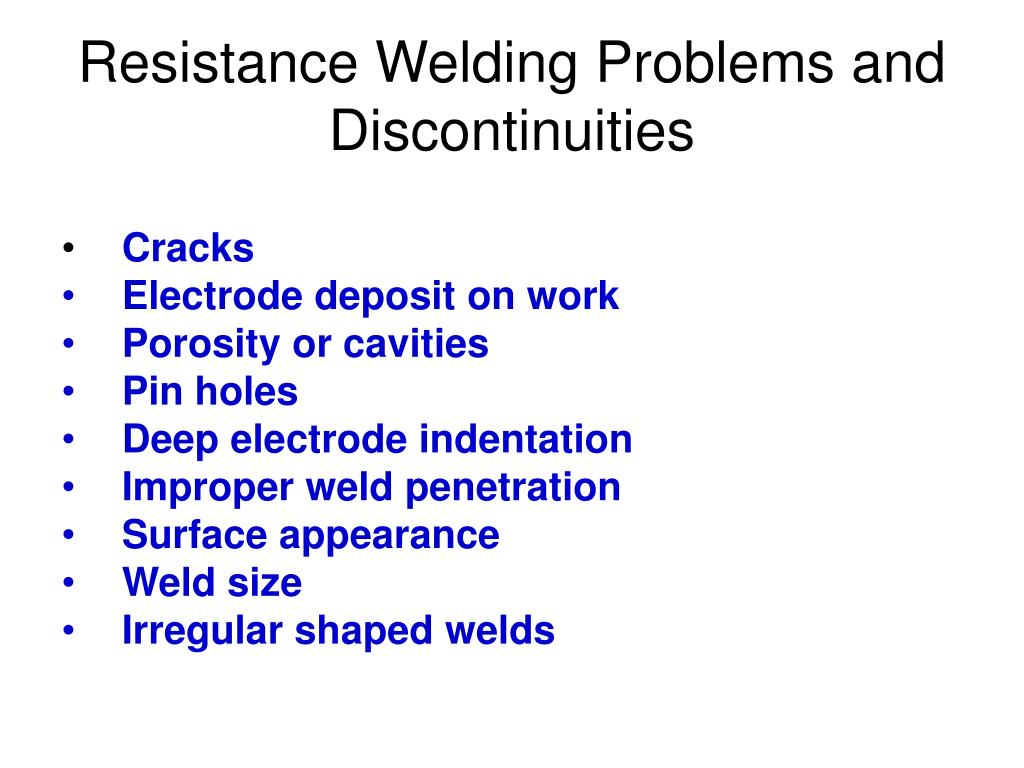
Porosity
Incomplete Fusion and Incomplete Joint Penetration
- Because these terms are sometimes misused, it's important to understand the difference between these two weld discontinuities. Incomplete fusionis a weld discontinuity in which fusion doesn't occur between the weld metal and fusion faces or adjoining weld beads. This absence of fusion can occur at any location within the weld joint and be present i...
Unacceptable Weld Profiles
- The profile of a completed weld may have a considerable effect on the performance of that weld in service. Welding inspectors must identify discontinuities through visual inspection and evaluate their acceptance or rejection according to the applicable welding code or standard acceptance criteria. Unacceptable weld profilescan cause a reduction in base material thickness, reduction i…
Cracking
- Cracks in a weldment are probably the most dreaded of all the weld discontinuities. Because so many materials and applications are used in welding, cracking is a complex subject. The base material's crack sensitivity may be associated with its chemistry and its susceptibility to the formation of elements that reduce its ductility. Excessive stresses in the weld joint, particularly i…
Detecting and Evaluating Discontinuities
- Weld discontinuities often are detected through visual inspection. Some are detected with inspection methods, such as radiography, ultrasonics, liquid penetrant, and magnetic particle inspection. The maximum acceptable limitations for these discontinuities depend on the performance requirements of the welded component and are specified in the appropriate weldin…