
What is flux cored arc welding?
This type of FCAW was developed primarily for welding structural steels. In fact, since it uses both a flux-cored electrode and an external shielding gas, one might say that it is a combination of gas metal ( GMAW) and flux-cored arc welding (FCAW). This particular style of FCAW is preferable for welding thicker and out-of-position metals.
What is a flux-cored wire electrode?
With this type of electrode, the weld pool is protected as gas is generated when the flux from the wire is burned. Because the self-shielding wire produces its own protective shield and doesn’t require an external gas tank, it is more easily carried about. Advantages of Flux-Cored Wire Electrodes
Why use self shielded flux cored wire for welding?
Because it’s the easiest and most convenient to use. Self shielded flux cored wire creates shielding gas needed for your hot weld pool from the flux inside the core of the wire. There’s no need for a tank of external shielding gas with self shielded flux cored wire.
What is the classification system for stainless steel flux cored electrodes?
The classification system for stainless steel flux-cored electrodes is based on the chemical composition of the weld metal and the type of shielding to be employed during welding. An example of a stainless steel electrode classification is E308T-1 where:

What is the function of the core of a flux-cored electrode?
The filler wire core contains slag forming fluxing agents and materials that produce shielding gases when burned by the heat of the welding arc. The shielding flux means that this process can be easily used outdoors even in windy conditions without the need of external shielding gas.
Is flux core and stick welding the same?
There are stick welding electrodes with cellulosic flux material, but flux-cored wires come only with rutile and basic flux. Cellulosic electrodes offer a stronger arc and deeper penetration and are more suitable to weld dirty metals.
What is the main difference between MIG wire and flux-cored wire?
First and foremost, both of these methods use a spool of wire to provide the filler metal to the weld, but the primary difference is in the type of wire. MIG welding uses a solid wire, whereas flux core welding wire is tubular and inside the tube is flux, hence the name.
What type of welder should a beginner use?
MIG WeldingMIG Welding (Beginner) MIG welders are among the best type for beginners, as they're designed with a wire welding electrode on a spool that is fed at a pre-selected speed through a welding gun. As a semi-automatic or automatic process, gas metal arc welding (GMAW or MIG), is the easiest to learn.
What is a good welder for a beginner?
The 7 Best Welders for BeginnersWeldpro 200 Multi-Process Welder – Best Overall. ... Lotos TIG200 Beginner TIG Welder. ... Forney Easy Weld 271 MIG Welder – Best Value. ... ESAB 120/230-Volt MIG/TIG/Stick Welder. ... Lotos MIG140 Flux Core Beginner Welder. ... Hobart Handler 210 MIG Welder for Beginners. ... Amico TIG160 ARC Stick Welder.
How do I know if my welding wire is flux core?
3:167:15FLUX CORE AND MIG WELDING WIRE COMPARISON ... - YouTubeYouTubeStart of suggested clipEnd of suggested clipThe weld and this has no flux in it this is just straight steel wire with a protective gasps now theMoreThe weld and this has no flux in it this is just straight steel wire with a protective gasps now the gases which shields the weld from oxygen nitrogen and gases coming out of the end of the hose.
Is flux core as strong as MIG welding?
Is flux core as strong as MIG? Both MIG and flux-cored wires make very similar strength welds, and if the joint is properly welded, there is not a significant difference in strength between the processes.
Can all MIG welders use flux core wire?
Yeah, that will work fine. Flux core is sometimes used in MIG welders even when gas is available. For example, flux core will work in windy conditions that would blow away shielding gas. Also, flux core often gives somewhat better penetration than gas shielded wire.
How Does Flux Core Arc Welding Work?
Flux cored arc welding uses heat generated by an electric arc to fuse metal in the weld joint area. This arc is struck between the metallic workpie...
Which Metals Can Be Welded with FCAW?
Flux cored arc welding works well with most carbon steels, cast iron, stainless steel and hard facing / surfacing alloys.However, nonferrous exotic...
What are the Advantages?
The flux core welding technique provides several advantages over other methods. FCAW is preferable to MAG welding for outdoor use as well as for jo...
What are the Disadvantages/Limitations?
There are few disadvantages of the process compared to other welding techniques, including production of noxious smoke that can make it difficult t...
What is FCAW Used For?
It is a flexible welding process suitable for all position welding, given the correct filler material and flux composition. Being highly productive...
Why is flux used in welding?
An externally supplied shielding gas is sometimes used, but often the flux itself is relied upon to generate the necessary protection from the atmosphere, producing both gaseous protection and liquid slag protecting the weld. The process is widely used in construction because of its high welding speed and portability.
What is irregular wire feed?
Irregular wire feed – typically a mechanical problem. Porosity – the gases (specifically those from the flux-core) don’t escape the welded area before the metal hardens, leaving holes in the welded metal. More costly filler material/wire as compared to GMAW.
What are the issues with FCAW welding?
Of course, all of the usual issues that occur in welding can occur in FCAW such as incomplete fusion between base metals, slag inclusion ( non-metallic inclusions ), and cracks in the welds. But there are a few concerns that come up with FCAW that are worth taking special note of: 1 Melted contact tip – when the contact tip actually contacts the base metal, fusing the two and melting the hole on the end. 2 Irregular wire feed – typically a mechanical problem. 3 Porosity – the gases (specifically those from the flux-core) don’t escape the welded area before the metal hardens, leaving holes in the welded metal. 4 More costly filler material/wire as compared to GMAW. 5 The amount of smoke generated can far exceed that of SMAW, GMAW, or GTAW. 6 Changing filler metals requires changing an entire spool. This can be slow and difficult as compared to changing filler metal for SMAW or GTAW. 7 Creates more fumes than SMAW.
What is dual shield welding?
This is known informally as "dual shield" welding. This type of FCAW was developed primarily for welding structural steels. In fact, since it uses both a flux-cored electrode and an external shielding gas, one might say that it is a combination of gas metal ( GMAW) and flux-cored arc welding (FCAW). The most often used shielding gases are either ...
What is a FCAW-S process?
These include self-shielded, flux-cored electrodes (FCAW-S process) and gas-shielded, flux-cored electrodes (FCAW-G process). They are all tubular electrodes with fluxing elements inside the electrode which, among other things, produce a slag covering of the weld.
Is a self shielded electrode a gas shield?
However, self-shielded electrodes completely produce their own shielding system (like Shielded Metal Arc Welding (SMAW) or stick electrodes), while gas-shielded electrodes also utilize an external shielding gas system (i.e., they are double shielded). These usability designators can be sub-divided into the two main categories ...
Can an electrode be tri-classified?
In other cases, electrodes may be tri-classified as a “T-1”, “T-9” and “T-12” electrode. A “12” designation classification also has the exact same electrode and operating characteristics as a “1” and “9” classification.
What is filler wire core?
The filler wire core contains slag forming fluxing agents and materials that produce shielding gases when burned by the heat of the welding arc.
Is FCAW good for joining metals?
Another disadvantage is the slag formation that needs to be removed prior depositing each subsequent layer. Finally, while FCAW is excellent for joining thicker metals, it is not recommended for use on materials thinner than 20 gauge.
Is flux cored arc welding a skill?
Flux cored arc welding can be an ‘all position’ process and also requires less skill among operators than MMA and MAG. It also requires less precleaning of metals than other processes. The chances of porosity are also very low if FCAW is applied correctly.
Can flux cored arc welding be used outdoors?
Since it can be used to for a range of alloys, plain carbon, stainless and duplex steels, flux cored arc welding is also frequently used for surfacing and hardfacing.
What is flux core wire?
Made as a long tube, your flux cored wire has your weld metal around the outside. And inside this wire tube are compounds. And these compounds are the flux. Inside Flux Core Wire. These compounds when melted in your welder’s arc gives you a shielding gas around your hot metal. And that gas protects your weld from the air.
Why use self shielded flux cored wire?
Self shielded flux cored wire creates shielding gas needed for your hot weld pool from the flux inside the core of the wire . There’s no need for a tank of external shielding gas with self shielded flux cored wire. As the flux inside your wire melts.
What is flux in welding?
As the flux inside your wire melts. Your flux forms your shielding gas at the point of your weld. The gas from the flux protects your weld pool from the air around your weld. Plus the flux works to form something called slag over the top of your weld. And pulls contaminants out of your hot welded metal.
What is the base metal of a weld?
The base metal is the metal you’re welding. The metals flow together and at the same time compounds from your flux core wire form a gas. And that external gas protects your weld from the air around your weld. Picture of the MIG Process.
How much of the filler metal goes into the weld?
When you use Self shielding flux core wire. 65% of your filler metal makes it into your weld. With gas shielded flux core wire 75% to 85% goes into the weld. And so gas shielded flux core wire has higher deposition rates.
Where does the arc form in an electrical circuit?
It’s a key part of your electrical circuit. Your arc forms at the tip of your flux core wire. And the heat from your electrical arc melts the end of your flux cored wire. Your filler metal melts and your base metal melts. The base metal is the metal you’re welding.
Is gas shielded flux core better than flux core?
You’ll find gas shielded flux core wire’s slag easier to get off your weld. It’s also a better flux core wire for welding thicker metals. Because gas shielded flux core welding wire gives you better weld penetration. You can weld deeper into your metal.
What are the defects in welding?
Wormtracking and porosity are some of the most prevalent defects that can reduce the integrity of weld joints. Porosity develops when gas bubbles enter the weld pool and get trapped. The molten metal will solidify to form holes due to these bubbles. These holes can form at a point or along the entire length of the weld. To prevent such an occurrence, ensure that you remove all dirt, moisture, oil, coatings, paint, grease, and rust from the surface of the metal section before you begin welding.
What does it mean when a welding machine is in spray transfer mode?
When you switch your welding machine to spray transfer mode, then you will notice a distinct cracking sound. Welding is typically carried out with spray transfer. As the name suggests, tiny droplets of molten metal are passed along the arc towards the weld pool in spray transfer.
What is the purpose of setting up a FCAW welding machine?
Before setting up the device, you must ensure that the roller tension is adjusted correctly. There should be enough tension to feed the wire with no slip. If the rollers become too tight, then the wire may be crushed in which case you must feed the wire back again.
What is MIG welding?
MIG welding uses solid wires as electrodes for filler material. FCAW uses electrode wires with a hollow center that is filled with flux. This flux protects the hot weld joint from corrosion and contamination by shielding it from the environment.
How is globular transfer used in welding?
In globular transfer, the filler metal is transferred along the arc in the form of relatively big droplets. The size of these droplets is comparable to the electrode diameter. This transfer method is employed for carbon steel. Through globular transfer, welding is done in the horizontal or flat position owing to the large size of the droplets. The big droplet size makes this welding process more challenging in the overhead and vertical positions. Short circuit arc transfer is more natural in comparison. The large droplet size leads to high spattering.
How much wire can you deposit in an hour?
With MIG welding, you can deposit a maximum of about 8 pounds of wire within an hour. With the FCAW method, you can deposit up to 25 pounds of metal per hour. This method, therefore, has very high productivity and is a particularly good option for welding thick metal sections and workpieces.
Is FCAW welding like MIG welding?
FCAW process employs flux material just like stick welding. However, in FCAW electrodes, this flux is placed in the core rather than the exterior as in stick welding electrodes. Due to flux, the FCAW technique possesses several advantages over the MIG welding process. Here are the four significant benefits.
What is Flux-Cored Arc Welding (FCAW or FCA) ?
Flux-cored arc welding (FCAW or FCA) is a semi-automatic or automatic arc welding process. FCAW requires a continuously fed consumable tubular electrode containing a flux and a constant-voltage or, less commonly, a constant-current welding power supply.
How Does Flux Core Arc Welding Work?
Flux-cored arc welding uses heat generated by an electric arc to fuse base metal in the weld joint area. This arc is struck between the metallic workpiece and the continuously-fed tubular cored consumable filler wire, with both the wire and the metallic workpiece melting together to form a weld joint.
Disadvantages
Despite the great benefits of FCAW, some disadvantages still occur. Below are the limitations of flux cored arc welding in their various applications.
What is flux core wire?
Flux-Cored Wire Electrodes. There are two types of flux-cored wire electrodes: gas-shielded and self-shielded. As its name implies, the gas-shielded type of flux-cored wire requires an external shielding gas. The self-shielded variety does not.
What happens when you use flux core wire?
Additional problems that may arise when using flux-cored electrode wires include: A melted contact tip may occur if the electrode contacts the base metal and fuses the two together. If gases do not escape the welded area before the metal hardens, the weld may develop holes and become porous.
What are the concerns of welding?
Regardless of the process and type of electrode used, there is the possibility of creating an incomplete fusion between the base metals. Slag inclusion or cracks in the welds may also result.
Why is a solid wire electrode plated with copper?
Solid wire electrodes are often made of mild steel which is plated with copper to prevent oxidation and to aid in electrical conductivity. The copper plating also helps to increase the life of the welding contact tip.
How does FCAW work?
They work well outdoors and in windy conditions. With the right filler materials, these electrodes can make FCAW an “all-position” process. Typically, flux-cored wires create clean, strong welds.
Why is a weld pool protected?
With this type of electrode, the weld pool is protected as gas is generated when the flux from the wire is burned. Because the self-shielding wire produces its own protective shield and doesn’t require an external gas tank, it is more easily carried about.
Do flux cored wires need shielding?
They also work well for welding out-of-position applications. Slag removal is easy with this type of wire. Self-shielding flux-cored wires do not require an external shielding gas.
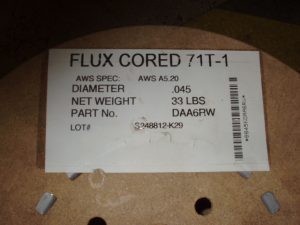
Overview
Flux-cored arc welding (FCAW or FCA) is a semi-automatic or automatic arc welding process. FCAW requires a continuously-fed consumable tubular electrode containing a flux and a constant-voltage or, less commonly, a constant-current welding power supply. An externally supplied shielding gas is sometimes used, but often the flux itself is relied upon to generate the necessary protection from the atmosphere, producing both gaseous protection and liquid slag protecting th…
Types
One type of FCAW requires no shielding gas. This is made possible by the flux core in the tubular consumable electrode. However, this core contains more than just flux. It also contains various ingredients that when exposed to the high temperatures of welding generate a shielding gas for protecting the arc. This type of FCAW is attractive because it is portable and generally has good penet…
Process variables
• Wire feed speed
• Arc voltage
• Electrode extension
• Travel speed and angle
• Electrode angles
Advantages and applications
• FCAW may be an "all-position" process with the right filler metals (the consumable electrode)
• No shielding gas needed with some wires making it suitable for outdoor welding and/or windy conditions
• A high-deposition rate process (speed at which the filler metal is applied) in the 1G/1F/2F
Disadvantages
Of course, all of the usual issues that occur in welding can occur in FCAW such as incomplete fusion between base metals, slag inclusion (non-metallic inclusions), and cracks in the welds. But there are a few concerns that come up with FCAW that are worth taking special note of:
• Melted contact tip – when the contact tip actually contacts the base metal, fusing the two and melting the hole on the end.