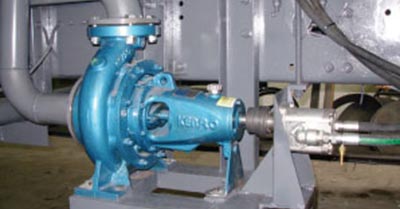
How much does a hydraulic pump cost?
The most basic hydraulic system will cost around $400. More high technology systems will be around $1000 or above. Mechanics will cost anywhere from $80 to $100 per hour. Pumps will cost around $500 each, and you’ll need 2-4 of these. You’ll also need multiple car batteries.
What is the function of hydraulic pump?
The purpose of a hydraulic pump is to flow hydraulic oil by a hydraulic system. It acts as a beating heart of the system. All hydraulic pumps have two major functions: These pumps supply hydraulic flow to other parts (such as hydraulic cylinder, rams, hydraulic motor, etc.) of the hydraulic system.
What are hydraulic power units and how do they work?
What are Hydraulic Power Units? Hydraulic power units (sometimes referred to as a hydraulic power pack) is a self-contained system that generally includes a motor, a fluid reservoir, and a pump.It works to apply the hydraulic pressure needed to drive motors, cylinders, and other complementary parts of a given hydraulic system.
How does a hydraulic pump work?
A hydraulic pump is a machine that uses the pressure of fluids to move things. It works by using a piston and cylinder assembly to push and pull fluid through a series of tubes. The force of the fluid moving through the tubes creates a mechanical force that can be used to do work. There are two main types of hydraulic pumps: reciprocating and ...

What are the 2 types of hydraulic pumps?
There are two types of hydraulic pumps to consider: gear pumps and piston pumps. Radial and axial piston pumps are types of piston pumps. Axial pumps produce linear motion, whereas radial pumps can produce rotary motion. The gear pump category is further subdivided into external gear pumps and internal gear pumps.
What does a hydraulic pump look like?
9:3013:18Hydraulic Pumps Types of and how are they work? - YouTubeYouTubeStart of suggested clipEnd of suggested clipEarlier in this course we looked at a simple piston pump with a single piston that produced aMoreEarlier in this course we looked at a simple piston pump with a single piston that produced a pulsating flow. In industry piston pumps have several Pistons. So they produce a relatively constant flow.
What are the 6 types of hydraulic pumps?
Types of Hydraulic PumpsGear Pumps.Piston Pumps.Vane Pumps.Clutch Pumps.Dump Pumps.Refuse Pumps.
What are hydraulic pumps and its types?
Three different types of hydraulic pumps exist: gear pumps, piston pumps and vane pumps.
What is a hydraulic pump usually used for?
Hydraulic pumps are used on excavators, cranes, loaders, tractors, vacuum trucks, forestry equipment, graders, dump trucks, mining machinery, etc. Mobile applications use hydraulic pumps more prolifically than do industrial machines, because electric actuators are generally not used for mobile machinery.
What is the most common hydraulic pump?
Rotary piston pumpsRotary piston pumps are the most common type of hydraulic pump. They use a rotating cylinder to move the fluid.
How do hydraulic pumps work?
Hydraulic pumps convert electrical energy into fluid pressure by using an electric motor to drive the pump. They are necessary for all hydraulic drives. The fluid pressure is then delivered by hydraulic fluid to cylinders and actuators and hydraulic motors at the required pressure level and volume.
What is the best type of hydraulic pump?
Rotary-vane pumps Advantages: They generally offer better volumetric efficiency than gear pumps. They produce less noise while maintaining high speeds (up to 3,000 rpm). There are available in variable and fixed displacement models.
Where is the hydraulic pump located?
The hydraulic system is located in the tractor's engine compartment. The pump turns on and off with the engine, providing pressure to drive the valves.
What is the difference between hydraulic motor and pump?
pumps convert mechanical energy into hydraulic energy; motors, on the other hand, transform hydraulic energy into mechanical energy.
Is a centrifugal pump a hydraulic pump?
Centrifugal pump is a hydraulic machine which converts mechanical energy into hydraulic energy by the use of centrifugal force acting on the fluid.
Where is the hydraulic pump located?
The hydraulic system is located in the tractor's engine compartment. The pump turns on and off with the engine, providing pressure to drive the valves.
What is the symbol for a hydraulic pump?
0:324:3702 Hydraulic Pumps Symbols - YouTubeYouTubeStart of suggested clipEnd of suggested clipCircle represents a rotary device such as pump or motor denotes the devices capable of continuousMoreCircle represents a rotary device such as pump or motor denotes the devices capable of continuous rotation in one or both directions. Energy triangle shows direction of flow and type of fluid.
How do hydraulics pump work?
Hydraulic pumps convert electrical energy into fluid pressure by using an electric motor to drive the pump. They are necessary for all hydraulic drives. The fluid pressure is then delivered by hydraulic fluid to cylinders and actuators and hydraulic motors at the required pressure level and volume.
What is the difference between hydraulic motor and pump?
pumps convert mechanical energy into hydraulic energy; motors, on the other hand, transform hydraulic energy into mechanical energy.
What is a Hydraulic Pump?
A hydraulic pump is a mechanical source of power that converts mechanical power into hydraulic energy ( hydrostatic energy i.e. flow, pressure). When a hydraulic pump operates, it performs two functions. First, its mechanical action creates a vacuum at the pump inlet which allows atmospheric pressure to force liquid from the reservoir into the inlet line to the pump. Second, its mechanical action delivers this liquid to the pump outlet and forces it into the hydraulic system.
How does a hydraulic pump work?
As mentioned above, the hydraulic pump generates a flow with enough power that overcomes the pressure produced by the load at the outlet of the pump . A vacuum is created at the outlet of the pump when the pump is operated. The vacuum forces the liquid into the inlet of the pump and delivers it to the pump outlet with mechanical actions and finally forces the liquid into the hydraulic system.
What is vacuum in pump?
The vacuum created will push the fluid into the pump inlet. Electric, motor or a gas engine are used as the prime mover to rotate the shaft. The impeller blades are located on the shaft and the surrounding fluids will rotate with the movement of the shaft.
What is the check valve on a hydraulic pump?
The check valve located at the inlet will push the fluid from the tank/reservoir into the pump and the one located at the outlet will pump fluid to other parts of the system.
How does a vacuum pump work?
A vacuum is created inside the cylinder when the piston is pulled. The vacuum created will close the outlet check valve and open the inlet check valve. Then , fluid from the tank or reservoir enters the pump and partially fills the cylinder. When the piston is pushed, the fluid molecules will come closer and the inlet check valve will close. This will open the outlet check valve and fluid flows through it.
What is the role of impeller blades in a pump?
Also, they play an important role in lubricating and cooling the system .
What is the shaft used for in a pump?
Pump Shaft: The pump shaft is used to mount the impeller. Steel or stainless steel is used for constructing the shaft and the size will depend on the impeller.
What is hydraulic fluid?
Hydraulic fluid (sometimes referred to as hydraulic oil) can serve multiple purposes in a hydraulic system and its individual components — including pumps. These purposes include the following: Transmitting energy. Dissipating heat.
What happens if you use a hydraulic pump?
In fact, the use of a fluid that is poorly matched to the pump can lead to a catastrophic failure that can cause cascading issues throughout the system. Issues that can arise as a result of poor ...
Why is hydraulic fluid viscous?
It is closely related to temperature, with hydraulic fluids becoming more viscous as temperatures drop. If a hydraulic fluid has a viscosity that is too high, the system will not perform efficiently due to the losses involved in overcoming the resistance of the fluid to motion.
Why do hydraulic pumps fail?
Pumps may become inefficient or even catastrophically fail simply because the wrong type of hydraulic fluid is used. How do you know if you are using the right kind of fluid for your hydraulic pump? The answer to that question is dependent on several factors, including the type of pump, its maximum operating temperature, its maximum operating pressure, and even the type of material the pump’s seals are made from.
What is the viscosity of a vane pump?
For vane pumps with an operating pressure of 500 psi, the ISO VG viscosity can range from 15 to 22. When the maximum operating pressure is around 1000 psi, the viscosity is heavily dependent on the maximum operating temperature. For operating temperatures up to 104°F, the viscosity should be between 10 and 15; for temperatures between 104 and 140°F, the recommended viscosity is 15 to 32. When maximum operating temperatures are expected to reach 158°F, a higher viscosity fluid on the order of 22 to 46 is highly recommended.
What is the maximum pressure for a gear pump?
Most gear pumps need a fluid that can handle a maximum temperature and pressure of 158°F, 500 psi. Gear pumps work best with fluids that have an ISO VG viscosity of 15 to 32 for a max temperature of 140°F and 32 to 68 for a max temperature of 158°F.
Why is lubrication important in pumping?
In the majority of cases, the most important factor is the ability of the fluid to transmit energy, but that can be compromised if too much heat is trapped within the pump, internal components are allowed to corrode, or there is not enough lubrication to prevent surface damage of the internal components.
How does a hydraulic pump work?
They are driven by a prime mover (usually an electric motor, diesel engine, or gas engine) that rotates at several hundred revolutions per minute (rpm). Every rotation causes all of the pump’s pistons to extend and retract — drawing fluid in and pushing it out to the hydraulic circuit in the process. Hydraulic systems typically operate at fluid pressures of thousands of psi. So a system that can develop 2,000 psi can push with 10,000 lbs. of force from a cylinder about the same size as a can of soda pop.
What is a pumping device?
a pumping device — a hydraulic pump or air compressor to provide fluid power to the system
How to visualize hydraulic system?
To visualize a basic hydraulic system, think of two identical syringes connected together with tubing and filled with water (see Figure 1). Syringe A represents a pump, and Syringe B represents an actuator, in this case a cylinder. Pushing the plunger of Syringe A pressurizes the liquid inside. This fluid pressure acts equally in all directions (Pascal’s Law), and causes the water to flow out the bottom, into the tube, and into Syringe B. If you placed a 5 lb. object on top of the plunger of Syringe B, you would need to push on Syringe A’s plunger with at least 5 lbs. of force to move the weight upward. If the object weighed 10 lbs ., you would have to push with at least 10 lbs. of force to move the weight upward.
What is hydraulics used for?
Whether it’s construction, mining, agriculture, waste reduction, or utility equipment, hydraulics provides the power and control to tackle the task at hand and often to provide motive power to move equipment from place to place — especially when track drives are involved. Hydraulics is also widely used in heavy industrial equipment in factories, in marine and offshore equipment for lifting, bending, pressing, cutting, forming, and moving heavy work pieces. Following are case histories housed on websites of industry publications describing the use of hydraulics in a variety of applications:
Why are electronic sensors and switches used in fluid power systems?
Electronic sensors and switches are also incorporated into many of today’s fluid power systems to provide a means for electronic controls to monitor operation of components. Diagnostic instruments are also used for measuring pressure, temperature and flow in assessing the condition of the system and for troubleshooting.
What is an actuator?
actuators — cylinders, motors, rotary actuators, grippers, vacuum cups and other components that perform the end function of the fluid power system.
What is a pump?
WHAT IS A PUMP? – A device which converts mechanical energy into hydraulic. energy, either fixed or variable.
What is a filter in hydraulics?
WHAT IS A FILTER? – A device incorporated into a hydraulic system to remove contaminants from the oil.
What is an accumulator?
ACCUMULATOR: A container which stores fluid under pressure. Used as an energy source or to absorb hydraulic shock. Common types are piston, bladder and diaphragm. BLEEDER (BLEED VALVE): A device for removal of pressurized fluid. Used to bleed air from system. CAVITATION: A gaseous condition within a liquid stream caused when pressure is reduced ...
What is single cylinder?
WHAT IS A CYLINDER; SINGLE ACTING? – A cylinder which can apply force in one direction only.
What is a motor?
WHAT IS A MOTOR? – A device which converts hydraulic energy into rotary motion, either fixed or variable.
What is flow rate?
WHAT IS A FLOW RATE? – The volume of fluid passing through the system or component in gal. per min. (or 11m).
