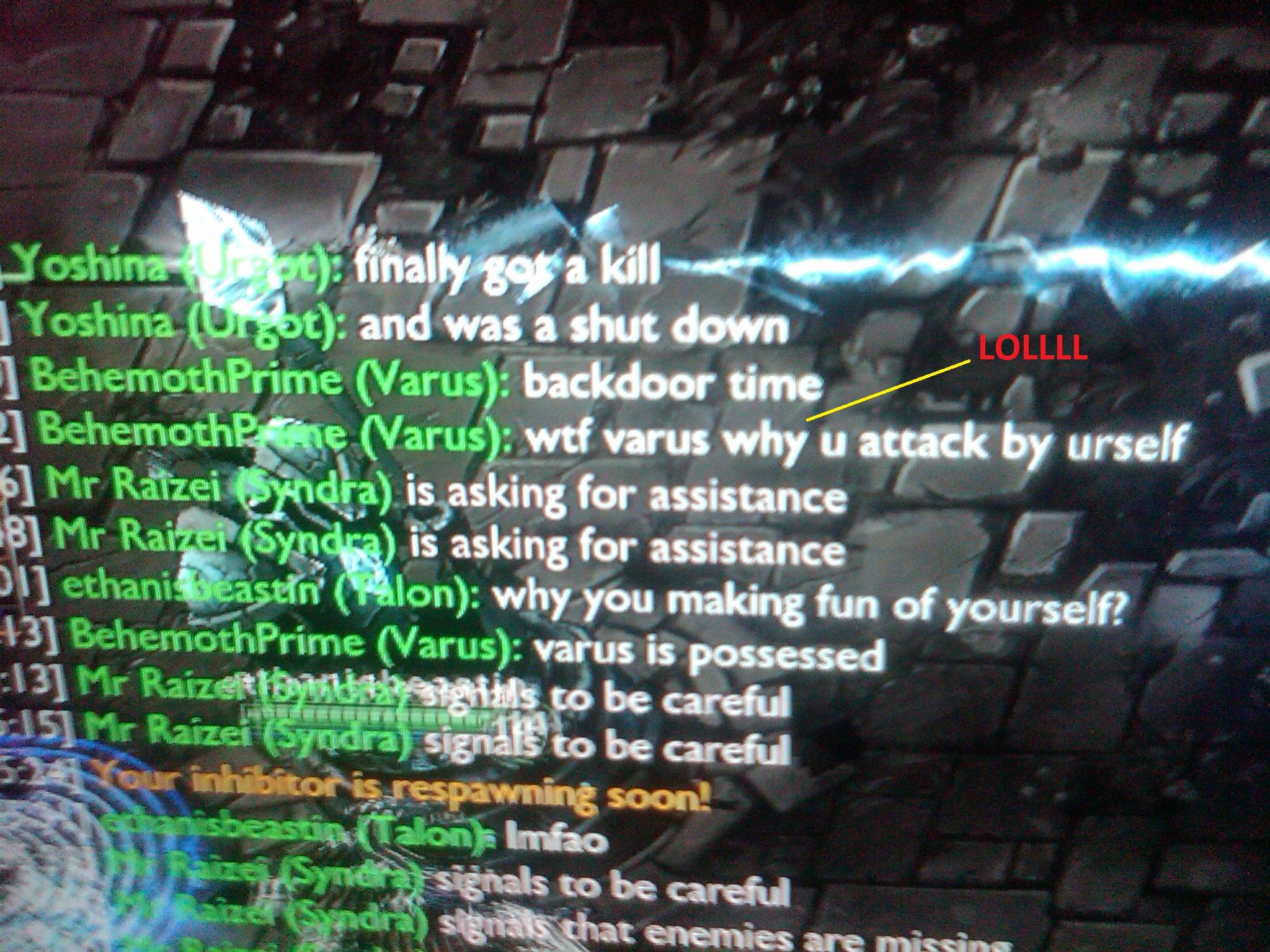
Maintenance Activities means any and all activities other than Decommissioning Activities that are necessary to ensure the adequate protection of public health and safety with respect to the Muskogee Property, including, but not limited to, securing licensed materials, water treatment and monitoring, airborne particulate and effluent monitoring, radon monitoring, personnel exposure monitoring, contamination monitoring, and the implementation and maintenance of engineered structures and controls to prevent the release of radiological and non- radiological hazardous materials from the Muskogee Property or the ponds which contain process waste exceeding regulatory release criteria.
What are the maintenance activity types?
The maintenance activity types are used in the PM Information System as a grouping element for maintenance orders. So, first off you need to define what maintenance activity types are available. SAP gives you a group of types by default. So start with that list, and then determine if you need more. You’ll notice that it’s pretty straight forward.
What is maintenance?
Types of Maintenance | SafetyCulture What is Maintenance? Maintenance, otherwise known as technical maintenance, refers to a set of processes and practices which aim to ensure the continuous and efficient operation of machinery, equipment, and other types of assets typically used in business.
Where are the maintenance activity types stored in pm?
This can be from the point of view of task processing or of view of cost follow-up for the maintenance history. The maintenance activity types are stored in the header of each maintenance order. The maintenance activity types are used in the PM Information System as a grouping element for maintenance orders.
What is application maintenance and support in IT industry?
Application Maintenance and Support in IT industry includes many activities and functions. As a production support employee, you need to perform the following activities in a project environment. After moving the project from development to production it is under 24/7 surveillance by a team of members in rotational shifts.

What is an example of a maintenance activity?
Cleaning, visual inspection, functional tests, lubrication, measurement of operating quantities and oil tests are some of the examples of routine maintenance activities.
What are the types of maintenance activities?
Four general types of maintenance philosophies can be identified, namely corrective, preventive, risk-based and condition-based maintenance.
What are the three kinds of maintenance activities?
The Three Types of MaintenanceCorrective Maintenance.Preventative Maintenance.Predictive Maintenance.
What is maintenance example?
The definition of maintenance is providing support or upkeep to something. An example of maintenance is a janitor keeping a school clean.
What are 5 types of maintenance?
Five types of maintenance are in fact recurrent in the industry: corrective, preventive, condition-based, predictive and predetermined.
Which of the following is not part of maintenance activities?
Which of the following is not a type of maintenance? Explanation: Performative Maintenance is not a type of maintenance.
What are the 5 importance of maintenance?
Top five benefits of maintenance managementReduces equipment failure and unplanned downtime.Extends equipment's longevity.Helps with workplace safety.Helps keep costs under control.Improves equipment efficiency.
What is the main purpose of maintenance?
Purpose of Maintenance The main purpose of regular maintenance is to ensure that all equipment required for production is operating at 100% efficiency at all times.
What is the difference between service and maintenance?
Essentially, maintenance is what you get regularly done on your vehicle to make sure it stays in fighting form. Maintenance is something that's scheduled – like an oil change – whereas service is when you need something specific fixed or tuned up that's outside of your regular maintenance schedule.
What is simple maintenance?
For Organizational Management users, Simple Maintenance is best used to establish the basic framework in organizational plan development. Simple Maintenance uses a tree structure, which allows you to create a basic framework for organizational plans, using streamlined procedures.
What is the meaning of maintenance services?
A service provided to keep a product in good operating condition.
What are the two types of maintenance?
Most types of maintenance fall under two main categories: preventive and corrective.
What are the 4 types of preventive maintenance?
There are 4 major types of preventive maintenance. ... Usage-based preventive maintenance. ... Calendar/time-based preventive maintenance. ... Predictive maintenance. ... Prescriptive maintenance.
What are the 2 types of maintenance?
Most types of maintenance fall under two main categories: preventive and corrective.
What are the four types of system maintenance?
What are the 4 types of software maintenance?Corrective Software Maintenance. Corrective software maintenance is the typical, classic form of maintenance (for software and anything else for that matter). ... Preventative Software Maintenance. ... Perfective Software Maintenance. ... Adaptive Software Maintenance.
Which of the following are types of maintenance?
What are the Different Types of Maintenance?Condition-Based Maintenance. Condition-based maintenance is sometimes considered to be a more advanced alternative to preventive maintenance. ... Predictive Maintenance. ... Corrective Maintenance.
What is maintenance management?
Maintenance management is an orderly process to control maintenance resources and activities required to preserve assets at, or repair them to, an...
Why is maintenance management important?
When done properly, maintenance management keeps assets in optimum operating condition.
What are the objectives of maintenance management?
Objectives of maintenance management minimizing asset failure and downtime, extending asset life, controlling maintenance costs, and more.
What are the components of maintenance management?
Maintenance management is made up of many key functions including work order management, asset management, MRO inventory management, and maintenanc...
What are maintenance management strategies?
Maintenance management generally employs two strategies: reactive maintenance and proactive maintenance.
Who is involved in maintenance management?
Maintenance management typically involves or is influenced by maintenance managers, maintenance technicians, corporate management, and other relate...
What is maintenance?
Maintenance, in general, can be defined as efforts taken to keep the condition and performance of a machine always like the condition and performance of the machine when it is still new.
What is planned maintenance?
Planned maintenance is maintenance that is organized and carried out with thought to the future, control and recording in accordance with the plans that have been determined previously. The type of maintenance cannot be equated for each equipment, which depends on the method, cost and critical level. The following types of maintenance methods are ...
What is predictive maintenance?
Predictive Maintenance: Predictive maintenance is a method for doing maintenance by replacing parts based on predictions using a tool. The point is if the preventive method is only based on the schedule, then the predictive method is based on the results of the measurement. This method can also use the five senses, ...
What is a maintenance inspection?
It is a method for preventing damage to equipment by periodically replacing parts based on time of use and carrying out minor maintenance and inspections to find out the current state of the equipment / machinery.
What are the objectives of TPM?
The objectives of the TPM are: 1 Develop operators that are able to detect damage signals as early as possible. Because it is the production operator that really knows the state of the equipment to even the most detailed part. 2 Creating a neat, clean workplace so that any irregularities can be detected as early as possible
Why develop operators that are able to detect damage signals as early as possible?
Because it is the production operator that really knows the state of the equipment to even the most detailed part.
What is Maintenance Management?
Maintenance management is an orderly process to control the maintenance resources and activities required to preserve assets at, or repair them to, an acceptable working order. While you may interpret this definition of maintenance management as simply meaning “fixing things,” that would be an oversimplification. There is a lot more to maintenance management than most people realize. Since much of an organization’s money is tied up in equipment and facilities, important decisions are made regarding time, people, and money.
How does maintenance affect an organization?
Assets that are poorly maintained experience frequent, unexpected downtime, and cause a ripple effect. Instability, inconsistent product quality, stopped production, and high operational costs jeopardize an organization’s profitability and longevity.
What is asset management?
In an industrial setting, asset management seeks to maximize the value of fixed assets throughout their lifecycle. Maintenance is only one aspect of asset management, which also includes planning, acquisition, operation, and decommissioning.
Why is maintenance management important?
Maintenance management reports inform the organization of different aspects of maintenance operations. Reports are used to collect key data about the maintenance department, track key performance indicators (KPIs), identify areas of improvement, and set goals. Reports also help the organization develop forecasts, guide budget planning, and make better decisions.
What is proactive maintenance?
While some organizations take a “fix it when it breaks,” approach, others take a more proactive approach. They look to prevent failure by looking for signs of wear and tear before a problem occurs. Proactive maintenance is performed in a number of ways.
How often is maintenance work performed?
Regularly occurring maintenance work, such as inspections and condition monitoring, is scheduled in advance at weekly, monthly, or even yearly intervals.
What is work order management?
Work Order Management. Work orders are the primary channel of communication for maintenance work. Work order management is the system that defines how work orders are processed and completed. It boils down to how the maintenance department makes sure that work gets done accurately and on time.
What are the types of maintenance?
Other than making sure we are talking about the same thing. If what I consider to be condition based maintenance you call predictive maintenance that doesn’t really matter. As long as we sensibly talk about the underlying principles.
What is preventative maintenance?
Preventive maintenance (or preventative maintenance) is basically a type of maintenance that is done at a regular interval while the equipment is still functioning with the objective of preventing failure or reducing the likelihood of failure.
How long should a CBM interval be?
A common rule of thumb is that the interval between CBM tasks should be one-half or one-third of the P-F interval. How much more effective CBM is above breakdown maintenance depends on how long the P-F interval is.
What is run to failure?
A Run to Failure or Corrective Maintenance strategy only restores the function of an item after it has been allowed to fail. It is based on the assumption that the failure is acceptable (i.e. no significant impact on safety or the environment) and preventing failure is either not economical or not possible.
What is the most expensive type of maintenance?
The most expensive type of maintenance is Emergency Maintenance because this is the type of maintenance that is so urgent that you drop everything to run off and fix the problem. That means that Emergency Maintenance is usually not well planned (prepared) and therefore is highly inefficiency and expensive (typically at least 3 – 5 times as expensive as well planned preventive maintenance).
What is condition based maintenance?
Condition Based Maintenance as a strategy therefore looks for physical evidence that a failure is occurring or is about to occur. Thinking of CBM in this way shows its broader applications outside condition monitoring techniques often only associated with rotating equipment.
What is failure finding maintenance?
Failure Finding Maintenance tasks are aimed at detecting hidden failures typically associated with protective functions. Think pressure safety valves, trip transmitters and the like.
What is MRO?
MRO is an acronym that stands for maintenance, repair, and operations. Broadly speaking, MRO refers to any activities and processes needed to run a business such as asset maintenance, accounting, customer service, and even administrative tasks like responding to emails and reception duties.
How to use a CMMS?
Using a CMMS to manage MRO inventory makes the maintenance team’s job easier. Within a CMMS, you reap many benefits: 1 Save time locating parts by viewing the item descriptions and stock room bin numbers in your CMMS system. 2 Avoid ordering surplus parts by viewing the on-hand counts and checking inventory levels at your other locations, if applicable. If they have the item or supply in stock, it can be transferred to your location. 3 See where all your parts are being used by generating reports that list parts and tools used for work orders or special projects. 4 Allocate parts more accurately by using an asset hierarchy and listing parts and supplies on preventive maintenance work orders. 5 Know the frequency, cost, and quantity of parts ordered by tracking purchase orders. 6 Improve workflow efficiency with barcode scanning. 7 Relate tools to work orders and assets through tools tracking.
Why is MRO used in inventory management?
MRO inventory management is used to support predictive, preventive, and corrective maintenance jobs.
What is CMMS in MRO?
FTMaintenance CMMS is an MRO inventory management system that makes it easy to keep track of spare parts and vendors while ensuring the items you need are always available. Request a demo today to learn more about FTMaintenance MRO inventory capabilities and other CMMS features.
What is poor MRO management?
Poor MRO management results in a number of hidden costs due to low productivity. Organizations that operate on reactive maintenance wait around for assets to fail – and when they do, it leads to excessive downtime that could have been reduced or avoided.
What is MRO in manufacturing?
In manufacturing environments, MRO is understood to describe the activities associated with the upkeep of the company’s assets. It includes physical maintenance performed on buildings (including any structures and grounds); electrical, lighting, HVAC, and plumbing systems; and equipment used in the production of finished goods or delivery of services.
How to improve maintenance tracking?
Improve maintenance tracking by keeping a record of all maintainable assets.
Application Maintenance and Support Activities in Production Environment
Moreover, candidates in IT production support should be responsible for Application Maintenance and Support Activities regularly. Usually, Clients will give more importance after moving the specific application to production (i.e., to live). Here the actual problem starts.
Application Maintenance and Support Activities in IT Industry
Below are the list of activities carried by the production support team members in 24/7 environment.

The Pros and Cons of Maintenance
- In general, businesses benefit from good maintenance practices. However, several factors need to be considered before you can determine if maintenance is helping, or hurting, your operation. Below are some of the pros and cons of maintenance.
Maintenance vs. Repair
- Maintenance and repair work have the same goals, and that is to keep your business running efficiently as designed. Knowing their fundamental differences, however, will help you determine when to utilize maintenance techniques over repairs and vice versa to keep your business productive and profitable without issue.
Maintenance Practices Across Industries
- Good maintenance programsbenefit virtually all businesses across different industries; the only difference is how they apply maintenance techniques to achieve their business goals. Below is a list of how different industries apply maintenance practices to maximize their operation.